Реферат по теме выпускной работы
Содержание
- Введение
- 1. Постановка задачи. Обзор механизмов
- 2. Структура промышленного робота
- 3. Система подъема/опускания
- 4. Вывод
- Список источников
Введение
В металлургической промышленности, в частности при производстве качественных сталей, широкое применение находят конверторы и печь – ковш. Полученная сталь на названных установках разливается в специальные ковши, которые в дальнейшем следуют к машинам непрерывного литья заготовок или к изложницам. Сталь из ковша поступает в промежуточный ковш, из промежуточного ковша через специальный стакан в кристаллизатор. Для стакана предполагается использование роботизированного комплекса. Этот комплекс в настоящее время проходит испытания на лабораторном макете кафедры механического оборудования заводов черной металлургии (МОЗЧМ) [1–3].
Лабораторная установка выполнена в масштабе 1:2 (по отношению к предполагаемому промышленному образцу) на данное устройство получен патент кафедры МОЗЧМ. Кафедра МОЗЧМ предложила разработать систему электропривода для двух механизмов роботизированного комплекса – механизма установки (уборки) стакана, механизма подъема/опускания платформы манипулятора.
В рассматриваемом проекте основное внимание уделено механизму подъема (опускания) платформы манипулятора. На первом этапе предполагается выполнить анализ режимов работы устройства, выбрать приводной двигатель и систему электропривода. На втором этапе после приобретения и установки элементов электропривода и системы управления предполагается произвести экспериментальные исследования и выявить основные достоинства и недостатки используемого привода.
1. Постановка задачи. Обзор механизмов
Современное высокомеханизированное и автоматизированное производство немыслимо без применения промышленных роботов (ПР), гибких автоматизированных производств (ГАП), обрабатывающих модулей или центров.
Первые промышленные роботы появились в США в 1959 году, когда были созданы роботы с программным управлением.
В 1962 нашли своё применение роботы Юнимейт
, Версатран
для обслуживания процессов литья, ковки, механической обработки,
точечной сварки, покраски. Стоимость первых роботов составляла 25–30 тысяч долларов за единицу. В автомобильной и
металлургической промышленности сроки окупаемости составляли 1,5–2,5 года, что было довольно высоким показателем для
того времени.
Интересно заметить, что в журнале Мэшинери Мегезин
была опубликована статья о появлении нового типа рабочего,
который не пьёт кофе, не курит, работает 24 часа в сутки и не является членом профсоюза. Слово robota
(барщина,
подневольный труд) было использовано чешским писателем К. Чапеком в пьесе RUR (Россумские универсальные роботы, январь 1921 г).
Оно быстро перекочевало в технику и стало применяться в качестве нарицательного для тех механизмов, которые выполняют тяжёлую, однообразную работу. Этот класс механизмов так и получил название «роботы». Передовые страны мира начинают активный выпуск ПР в борьбе за рынки сбыта. На первое место по проектированию, производству и внедрению выходит Япония. Динамику роста выпуска ПР можно проследить по следующим цифрам: в 1978 г. в мире было 16000 ПР, в 1980 г. – 25000, в 1983 г. – в капиталистических странах – 31000 штук [2].
По такому показателю как число роботов на 10000 рабочих на первом месте в мире Швеция – 40, в Японии – 13, в США и ФРГ – 3 – 4 шт.
По ориентировочным данным в СССР в 1983 г. действовало около 7000 ПР и к 1990 г. планировалось число ПР довести до 375 тыс. штук. Япония продолжает удерживать первенство по проектированию новых типов роботов. Большое внимание уделяется созданию так называемых гуманоидных роботов, повторяющих движения человека, разрабатываются и выпускаются специализированные роботы для помощи людям с дефектами зрения, слуха, опорно-двигательного аппарата [4].
2. Структура промышленного робота

Рисунок 1 – Структурная схема промышленного робота
Структурная схема промышленного робота (рис.1), основные элементы конструкции и виды движений рабочих органов: 1 – путепровод, 2 – основание, 3 – корпус, 4 – рука, 5 – захватное устройство, 6 – рабочая зона и её координат основных движений ПР, хх – направление движения руки вдоль продольной оси, уу – направление движения корпуса по путепроводу, zz – направление движения руки вверх–вниз, φxy – угол поворота корпуса вокруг вертикальной оси zz; φzx – угол поворота руки в вертикальной плоскости, φyz – угол поворота захвата относительно оси хх, δ – направление движения захвата детали, δ и yz – направление ориентирующих движений, xx, zz, φxy, φzx, – направления транспортирующих движений, уу – координатное движение.
Практика эксплуатации подобных устройств на ряде зарубежных и отечественных металлургических предприятий показала, что эффективность их применения значительно повышается, если они работают в комплексе с манипуляторами, обеспечивающими механизированную подачу на приемные направляющие разливочного устройства промежуточного ковша предварительно разогретого до требуемой температуры резервного огнеупорного изделия, которое должно за доли секунды под действием силового цилиндра сменить вышедший из строя стакан.
Многообразие схем относительного расположения оборудования современных МНЛЗ и особенности его функционирования являются главными предпосылками для разработки систем быстрой замены погружных стаканов, которые в наибольшей мере соответствуют условиям непрерывной разливки металла конкретного сталеплавильного цеха. На кафедре «Механическое оборудование заводов черной металлургии» Донецкого национального технического университета за последние 5 лет запатентованы и спроектированы несколько типов систем, позволяющих практически без прерывания разливки осуществлять замену погружных стаканов, экранирующих струю стали на участке промежуточный ковш – кристаллизатор слябовой МНЛЗ.
Манипулятор, входящий в состав указанных систем, располагается на рабочей площадке со стороны торцевой части промежуточного ковша. Такая схема относительного размещения манипулятора в полной мере отвечает условиям разливки стали на одноручьевых МНЛЗ, промежуточные ковши которых переводятся в рабочую позицию с помощью подъемно-поворотных столов. На машинах с большим числом ручьев замену промежуточного ковша осуществляют, как известно, с использованием самоходной тележки, движущейся в направлении его продольной оси. В этом случае манипулятор является помехой перемещающейся тележке, что затрудняет его эксплуатацию.
В связи с этим была предложена новая конструктивная схема (рис. 2) стационарного манипулятора, позволяющая устранить отмеченный недостаток.
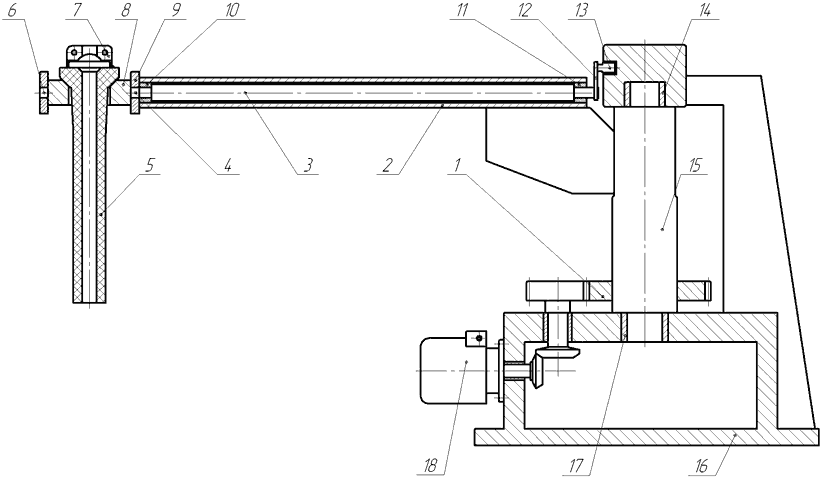
Рисунок 2 – Схема разработанной системы быстрой смены погружного стакана
Манипулятор включает основание 16, на котором смонтирована поворотная колонна 15, установленная в нижней 17 и верхней 14 неподвижных подшипниковых опорах и снабженная горизонтальной пустотелой консолью 2, жестко связанной с платформой 9. На этой платформе размещен силовой цилиндр 7 и на цапфах 4 и 6 закреплена скоба 8, несущая сменный погружной стакан 5. Скоба 8 имеет возможность поворота в вертикальной плоскости относительно пустотелой консоли с помощью механизма, включающего трансмиссионный вал 3, установленный внутри консоли в подшипниковых опорах 10 и 11 и удерживающий на конце, обращенном к поворотной колонне 15, рычаг 12, снабженный роликом 13, размещенным в профилированном направляющем пазу, выполненном на наружной цилиндрической поверхности корпуса верхней неподвижной подшипниковой опоры 14 поворотной колонны. Другой конец трансмиссионного вала жестко связан с цапфой 4 несущей скобы 8. Нижняя часть поворотной колонны 15 снабжена зубчатым венцом 1, посредством зубчатых передач связанным с электромеханическим приводом 18, закрепленным на основании 16 [5].
Принцип работы предлагаемой системы быстрой смены погружных стаканов поясняет (рис. 3) Во время серийной разливки стали манипулятор расположен в исходной позиции на рабочей площадке 19 перед промежуточным ковшом 20, оборудованным разливочным устройством 21, снабженным защитным стаканом 22, нижняя часть которого погружена в расплав, находящийся в кристаллизаторе 23. В этой позиции поворотная колонна 15, горизонтальная консоль 2 и несущая скоба 8 с установленным в ней сменным погружным стаканом 5 занимают относительное положение, показанное на (рис. 3а). При этом сменный стакан 5 расположен горизонтально и удерживается зажимами несущей скобы 8, развернутой в вырезе платформы 9. Фиксация скобы со стаканом относительно платформы обеспечена трансмиссионным валом 3, рычаг 12 которого своим роликом 13, находящимся в профилированном направляющем пазу, удерживает указанные элементы механизма в заданном положении [5].

Рисунок 3 – Последовательность выполнения операции быстрой смены погружных стаканов
Для замены погружного стакана необходимо включить привод 18, который через зубчатые передачи и венец 1 осуществляет поворот колонны 15 в нижней 17 и верхней 14 неподвижных подшипниковых опорах. Вместе с колонной будет поворачиваться горизонтально пустотелая консоль 2 и установленный внутри неё в подшипниковых опорах 10 и 11 трансмиссионный вал 3 с прикрепленным рычагом 12. Ролик 13, перекатываясь по одной из поверхностей профилированного направляющего паза, выполненного на наружной цилиндрической поверхности верхней неподвижной опоры 14, воздействует на конец рычага 12, поворачивающего трансмиссионный вал в опорах 10 и 11 относительно горизонтальной консоли 2. Вращение вала 3 через цапфу 4 передается скобе 8, которая осуществляет поворот относительно платформы 9 сменного погружного стакана 5 (рис. 3б) до полного его перевода в вертикальное положение. Этот перевод завершится при подходе стакана к торцу разливочного устройства 21 и расположении его соосно с направляющими. После этого силовым цилиндром 7, расположенным на платформе 9, резервный стакан 5 перемещают по направляющим разливочного устройства 21 до тех пор, пока он не займет место вышедшего из строя погружного стакана 22, экранирующего струю стали, истекающей из промежуточного ковша 20 в кристаллизатор 23 (рис. 3в). Скорость перемещения стаканов такова, что процесс их смены длится 0,2–0,3 с, т.е. практически без прерывания струи жидкой стали. Заменённый погружной стакан удаляют из направляющих пазов разливочного устройства с помощью специального приспособления, а консоль манипулятора возвращают в исходную позицию, поворачивая колонну в обратном направлении. В исходной позиции элементы конструкции манипулятора не препятствуют перемещению тележки с промежуточным ковшом при аварийном съезде или в случае передачи ковша на ремонтную площадку для замены его футеровки.
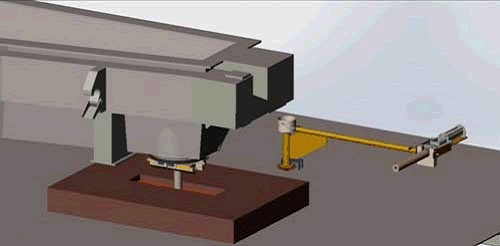
Рисунок 4 – Анимированное отображение работы манипулятора (5 кадров, 6 циклов повторения, размер 157кб)
При проектировании промышленного образца предложенной системы быстрой замены погружных стаканов, предварительно разработали методику расчета энергосиловых параметров приводов механизмов, входящих в ее состав: комбинированного электромеханического, обеспечивающего одновременный поворот колонны с консолью в горизонтальной и сменного стакана в вертикальной плоскостях, а также гидравлического, осуществляющего ускоренное перемещение заменяемого и нового стаканов по опорным направляющим разливочного устройства.
Для выполнения силового расчета рычажного механизма использован принцип Даламбера, согласно с которым подвижная система тел находится в каждый момент времени в равновесии под действием внешних сил, включая и силы инерции. При этом разделим механизм на две структурные группы (рис. 4) и расчет начнем с последней из них. В ее состав (рис. 4а) входят установленная на цапфах в подшипниковых опорах D и Е скоба, несущая сменный погружной стакан.

Рисунок 5 – Расчетная схема механического привода системы быстрой смены погружных стаканов
В период пуска привода манипулятора на звенья рассматриваемой структурной группы действуют силы тяжести стакана Gст и скобы Gск; сопротивление трения в подшипниковых опорах D и E, вызванное силами реакций; силы инерции; момент, приложенный к цапфе скобы и необходимый для преодоления указанных сил.
3. Система подъема/опускания
Зачем нужна система подъема/опускания манипулятора? В современной системе технологий промежуточный ковш МНЛЗ рассматривается как один из важнейших элементов, который самым непосредственным образом влияет на качество непрерывнолитой заготовки.
В цепи технологических переливов промежуточный ковш является буферной емкостью, так как с его помощью согласовывается поступление металла из сталеразливочного ковша в кристаллизатор. При этом обеспечивается усреднение поступающей порции металла и предотвращение попадания шлака в кристаллизатор. Предполагается, что конструкция промежуточного ковша должна обеспечивать минимальные потери тепла металлом.
Промежуточный ковш обеспечивает поступление металла в кристаллизатор с определенным расходом и, обеспечивая хорошо организованную струю, позволяет разливать сталь в несколько кристаллизаторов одновременно и осуществлять серийную разливку методом плавка на плавку при смене сталеразливочных ковшей без прекращения и снижения скорости разливки. Конструкция и вместимость промежуточного ковша в значительной степени определяют стабильность процесса разливки стали и качество заготовки.
Причины смены положения по вертикали: 1. Переход на разливку другого сечения слитка. Происходит перенастройка сечения кристаллизатора и изменение положения промковша. 2. При переходе на разливку других марок стали (другой хим. состав стали). Изменение положения промковша из-за необходимости формирования соответствующих новым маркам стали гидродинамических потоков в кристаллизаторе МНЛЗ. Изменение положения промковша осуществляется при помощи электропривода.
Система подъема/опускания манипулятора позволяет настроить, с помощью асинхронного двигателя, конструкцию за минимальное время, а так же установить промежуточный стакан в паз с минимальными потерями в производстве.
4. Вывод
Данный проект уже получил множество положительных отзывов от ведущих преподавателей Донецкого национального технического университета, а так же уникальность манипулятора была отмечена множеством стран (Китай, Россия, Польша и др.).
Для автоматизации системы подъема/опускания платформы манипулятора был выбран асинхронный двигатель с короткозамкнутым ротором . Для полной автоматизации была закреплена система управления приводом по схеме ПЧ-АД (преобразователь частоты – асинхронный двигатель). В дальнейшем будет реализована следящая система электропривода, обеспечивающая слежение за положением промежуточного ковша во время разливки стали.
На момент написания данного реферата магистерская работа еще не завершена.Ориентировочная дата завершения магистерской работы: июнь 2017 года. Полный текст работы и материалы по теме могут быть получены у автора или его руководителя после указанной даты.
Список источников
- Дюдкин Д. А., Кисиленко В. В. Производство стали, Том 1. Процессы выплавки, внепечной обработки и непрерывной разливки, М.: Теплотехник, 2008. – 528 с.
- Введение в специальность. В. Ф. Борисенко, - Донецк, ДонНТУ, 2014. – 357с.
- Еронько С. П., Быковских С. В. Разливка стали: Оборудование. Технология. – К.:Техника. 2003. – 216с.
- Материал из Википедии – свободной энциклопедии https://ru.wikipedia.org/wiki/....
- Патент 96891 Україна, В22D41/56, В22D11/106. Маніпулятор для заміни занурювального стакана на слябовій машині безперервного лиття заготовок / С. П. Єронько, М. Ю. Ткачов, К. В. Дубойський; Донец. нац. техн. ун-т. – №2010155511; заявлено 23.12.2010; опубл. 12.12.2011, бюл. №23. – 5 с.Патент 96891