Abstract
Content
- Introduction
- 1 Topic relevance
- 2 Goals and tasks of the research
- 3 Analysis of the influence of the silicon content on the quality of coatings
- Conclusion
- References
Introduction
On the modern stage of society development the production of materials and volume of industrial wastes have increased considerably, the natural sources of raw materials are exhausted. As one of basic construction materials metals are used. At the same time metals are continuously exposed to corrosion.
Corrosion is a process of chemical or electrochemical destruction of metals under the impact of environment. It is set that annually from corrosion about 10 % producible metals are irretrievably lost, that corresponds to the annual products of large metallurgical plant.
Plenty of methods of steel constructions protection from corrosion are known. Wide-range of researches have shown, that zinc coverage is characterized by high enough firmness against corrosion and abrasion. Zinc protects the iron from damage by applying to its surface a protective oxide layer which protects the metal from further corrosion. Zinc coverage has good original appearance and allows to increase tenure of employment of metallic constructions in 2–3 times, reliably protecting them from atmospheric, marine and other types of corrosion.
However adhesion strength of this coverage can change from impact of different factors. In particular, it was considered how violation of coverage quality depends on content of silicon in steel.
1 Topic relevance
Hot dip galvanizing process, besides the fact that it protects construction against corrosion, it improves some of its characteristics. It improves the appearance and greater resistance to wear and tear, which increases its endurance limit in relation to chemical and mechanical influences.
The service life of the zinc coating of 100 microns thickness is 25–50 years, without the cost of funds for maintenance of examination and protective properties of the coating.
However, with poor quality the coating obtained, it is necessary to fix a defective coating. Sometimes the coating must be completely removed, with re-prepare of the surface and zinc. This leads to an overrun of zinc and other materials, drastically reduces performance and efficiency [1].
This master's work is devoted to an actual scientific problem of increasing the adhesive strength of protective coatings of steel, which produced by hot-dip galvanizing. It will improve the corrosion resistance of steel structures and extend their service life.
2 Goals and tasks of the research
The objective of the study is to examine the possibility of increasing the adhesive strength of coatings obtained by hot dip galvanizing, by achieving a certain silicon content of the steel.
Main tasks of the research:
- To assess the impact of production on the environment.
- To explore the process of protective coating by hot dip galvanizing.
- To conduct identification of factors affecting the adhesion of protective coatings.
- To determine the silicon content in the studied steels.
- To analyze the effect of the silicon content of the steel on the quality of the coatings obtained by hot dip galvanizing.
- To suggest the optimal values of the silicon content in the low-alloy structural steel.
Research object: The low-alloy structural steel.
The result this work will be recommendations for protective coatings of steel structures with high adhesion properties by hot dip galvanizing.
3 Analysis of the influence of the silicon content on the quality of coatings
Gradual diffusion of liquid zinc in the surface of metal structures occurs in the process of coating using hot dip galvanizing method. Diffusion zinc coating obtained while melting the zinc, consist iron-zinc of several phases, which are arranged on the base metal, and a layer of zinc [2].
As seen in Figure 1 the microstructure of the zinc coating consists of four layers of different hardness. Iron-layers of γ, δ and ζ are stronger than the original steel product, which gives the zinc coating a good ability to withstand mechanical damage.
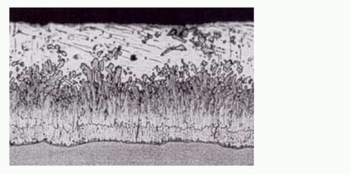
Figure 1 — Microstructure of the zinc coating
(animation: 6 frames, 5 cycles of repeating, 196 kilobytes)
Starting from the steel surface, the first layer located Gamma about 1 micron thick. It consists of steel and zinc alloy with a zinc content of about 25 %. The next layer is delta. It contains about 10 % iron. Then Zeta layer is located, which contains 7 % iron. A layer lying outside of it and referred Etta layer can be regarded as almost pure zinc as at ambient temperature maximum iron content thereof is 0.008 %.
Аlloying elements are introduced to improve the structural strength of conventional steel. Dissolved in the ferrite, they are able to harden it. Hardness of the ferrite most strongly increased silicon, manganese and nickel [3].
Silicon as an incidental element in steel plays a role in the hot-dip galvanizing of steel products, as it is part of the main types of conventional structural steel. Silicon is a necessary element in the production of steel. It removes oxygen from a metal, and slightly increases its strength and corrosion resistance. Furthermore, silicon, along with manganese and aluminum are the primary deoxidizer of steel. It removes from the molten metal dissolved oxygen, which is harmful impurity affects the mechanical properties of the metal. Silicon improves significantly the strength of steel, but if its content is more than 1 % it may reduce the viscosity, plasticity and may increase brittleness threshold. Silicon in the steel is not detected as fully soluble in the ferrite, except that part which in the form of silica did not have time to float in the slag and remained in the metal in the form of silicate inclusions.
On the practice of PJSC Donetsk Power Transmission Tower Plant
in the process of applying zinc coatings to the main low-alloy structural steels 09G2S brand, C345 and S355 it was observed that at the same conditions of galvanizing obtained adhesive strength is different. In some cases, there was a violation of the quality of coatings, they become loose, diminished luster, even peeling occurred.
In the literature similar defects in steel structures with high silicon content attributed to the formation of loose iron-zinc alloy layer instead of tight. The velocity of the reaction in the steel can be so large that a layer of pure zinc is completely transformed into the iron-zinc alloy. Then it can spread to the coating surface. As a result, this coating has a too low adhesion. Then peel and failure occurs at any minimal deformations [4].
For further study, we developed a method for determination of silicon content in low alloyed silicon-manganese steels.
Laboratory analysis showed the following results:
- in the studied steel 09G2S mass fraction of silicon amounted to 0.79 %.
- the sample of steel C345 contains 2.58 % silicon.
- the content of silicon in the euro-steel sample grade S355 is at a level of 1.55 %.
The resulting increased silicon content in the euro-steel C345 and S355 corresponds to those samples in which the violation of the zinc coating and decrease the adhesion strength were observed.
Appearance control is produced for 100 % of the products. The surface of the zinc coating must be smooth, the coating must be continuous. Color coating must be from the silver-shiny to matt dark gray. An example of a quality coating is shown in Figure 2. The thickness of the coating should be 40–200 microns. The thickness of the zinc coating is measured by a magnetic method, as well as metallographic and gravimetric methods.
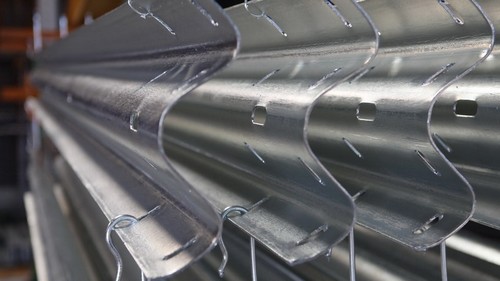
Figure 2 — An example of a quality coating
Conclusion
The work allows us to formulate the following conclusions:
- In the work the factors of production were discussed and analyzed, which affect the quality of the coating by hot dip galvanizing.
- Effect of various factors on the adhesion can not be fully identified or excluded, so researchers have different opinions.
- According to the study, it was determined that the silicon content of the steel has a great influence on the quality of the coatings produced by hot dip galvanizing. Moreover, with increase in the mass fraction of silicon is a decrease of adhesion strength of protective coating. The best performance of coating adhesion strength were determined at the silicon content is less than 1 %.
At the time when this essay was written, master's work has not been completed yet. The term of completion: May 2017. The full text of work and materials on the topic can be obtained from the author after that date.
References
- Алексеев А. А. Организация эффективного технологического процесса горячего цинкования на судостроительных предприятиях путем внедрения ресурсосберегающих технологий: дис. на соиск. учен. степ. канд. техн. наук: 05.08.04: защищена 24.05.07 / Алексеев Александр Алексеевич. — Санкт-Петербург, 2007. — 127 с.
- Рекомендации пользователям услуг цинкования ООО «Агрисовгаз».
- Хансен М., Андерко К. Структуры двойных сплавов. Т. II. — М.: Металлургиздат, 1962 (1992). — 607 с.
- Дефекты на горячеоцинкованных изделиях: Справочник. / Под ред. Хорстмана Д. Пер. с нем. Проскуркина Е. В., Коршмана И. Л. — М.: Металлургия, 1983. — 31 с.