Automatic control system of the cleaning process by sublimation of methanol in units such as NDA
Content
- Introduction
- 1 The purpose and objectives of the ACS development
- 2 Analysis of the control object
- 2.1 Description and general characteristics of the control object
- 2.2 The methanol treatment as a control object
- 3 Synthesis of automatic control system
- 3.1 The type of development selection and the ACS structural scheme
- 3.2 Mathematical model of control object
- 3.3 Simulation of the control system and the quality of performance analysis
- 4. Selection of complex of technical facilities
- 4.1. Requirements to ACS elements
- 4.2. The temperature sensor
- 4.3. Regulator
- 4.4. Work selection key
- Conclusions
- List of references
Introduction
Improving governance in relation to the rational work planning workshop is an important practical task methanol plant operations. The solution, which can be achieved through the establishment of typical automatic control and management of separate processing lines, taking into account the ever increasing requirements for the quality of its products. [1]
1 The purpose and objectives of the ACS development
The purpose of the work – improving the yield of production due to the development of systems such as methanol NDA-P automatic cleaning installation management. To achieve this goal it is necessary to solve the following tasks:
- Analyze the process of methanol purification, to identify its characteristics and identify the variables influencing the methanol refining process in the machine.
- Review the existing automatic control systems and analysis of the process as a control object.
- Get a mathematical model and synthesize controllers for management reporting facility. Perform simulation of the developed system.
- Develop a functional diagram automation and formulate requirements for technical means of automation.
2 Analysis of the control object.
2.1 Description and general characteristics of the control object
The invention relates to the field of organic chemistry, in particular to technologies for producing methanol by direct oxidation of methane gas (natural gas).
The basic problem of creating a small-capacity plant for methanol production is that all existing today methods of direct oxidation of methane to methanol by atmospheric oxygen is carried out at a low oxygen concentration in the feed gas mixture and, therefore, at the outlet of the reactor, the reaction mixture will be enriched with methane, nitrogen, oxide and carbon dioxide, and other elements.[2]
Recirculation methane requires its separation from the reaction mixture, which is very difficult. Therefore, the methanol yield, based on the entire missed methane remains extremely low, and virtually impossible to recycle methane as the total oxidation of methane in a single pass.[3]
However, experimentation can be found the ratio of the working process parameters and geometric characteristics of the heated reactor, in which this problem becomes solvable (all arriving at the entrance of the reactor, methane is oxidized in a single pass to give a reasonable yield of methanol and its content in the resulting oxidate).
Workflow, reporting to work, is represented by three interrelated objects. In the evaporator there is evaporation of methanol. Methanol containing 10-12% of water is continuously fed to the evaporator, is supplied to the air which is bubbled through the aqueous methanol layer and its saturated vapor. Steam mixture then goes into the reactor. Steam mixture enters the reactor in which the temperature 500-600°C. The reaction gases immediately fall into a cooler where the mixture is cooled and prevents decomposition of the product.
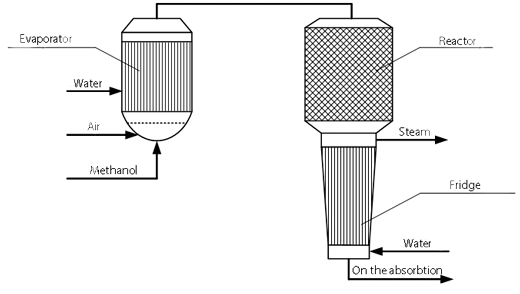
Figure 2.1 – Analysis of the control object
Methanol contains a large number of diverse compounds, where complete separation by conventional distillation techniques is not possible. Well separated from the methanol only volatile impurities: acetaldehyde, methyl formate, methyl acetate, furan, acetone, etc., having a high rectification ratio. Compounds included in the crude methanol to form double, triple and even more complicated azeotropic mixtures, which makes their separation from methanol. With these features for commercial methanol TsNILKhI been developed continuously operating apparatus NDA-I and NDA-P.
2.2 The methanol treatment as a control object
To study the installation as an object of regulation and construction of major technological dependency by monitoring and remote control of the system are determined by the connection between technological values.
One of the main requirements for the cleaning process is the stabilization of the temperature in the reactor.[5, 6]
The reactor temperature depends on the level of feed water and the level of methanol. Consumption of raw materials is controlled dosing or choice of control valve with electric drive.
Due to the fact that methanol is prepared in a roasting apparatus enters the reactor, it must have a controlled humidity. Excessive water content in the methanol fuel requires additional costs for evaporation in the reactor. The moisture content should be such as to provide the specified temperature conditions sufficient amount of driving of the product, as well as to do without pumping excess moisture level.
Parameters are controlled in the evaporator: methanol flow rate, airflow rate and steam pressure. According to the technological requirements of methanol consumption should be Fm = 3 m3/h, the airflow FB = 30 Nm3/h.
Controllable parameters in the reactor are steam pressure at which the process requirements must be P = 0.5 MPa.
Evaporator adjustable parameter is the ratio of the air-methanol costs and regulation occurs with the correction of the level of methanol in the evaporator. The level of methanol in the evaporator is L = 1 m.
Adjustable parameters of the reactor is temperature. The reactor temperature is controlled by changing the water supply to the refrigerator. According to the technological requirements of the temperature in the reactor should be in the range of 40-50°C.
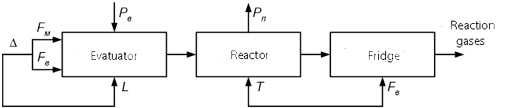
Figure 2.2 – Analysis of methanol refining process as a control object
Thus, the system of automatic control of the methanol purification process should ensure stabilization of process parameters – purity haul, humidity and maximum performance.
Control variables are: methanol, flow rate, air flow rate of methanol, the air pressure in the evaporator, reactor temperature and the flow rate of water in the refrigerator.
Perturbs variables are: the reaction gas temperature and vapor pressure in the refrigerator.
3 Synthesis of automatic control
3.1 The type of development selection and the ACS structural scheme
The developed system of automatic installation of NDA-P type methanol cleaning management should maintain the level in the evaporator at a predetermined level (L = 1 m) with automatic regulation of flow ratio (1:3) air-to-methanol under the influence of disturbances, so we will use a control structure in which it implemented the principle of management by the deviation.
Air flow regulation task relations and methanol can be solved by applying the block diagram shown in Fig. 3.1.
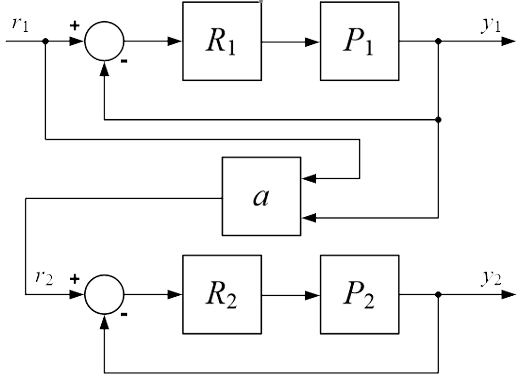
Figure 3.1 – Control of relationships with increased speed
The first regulator (methanol consumption) supports output value y1 equal to the value r1 set point. The quantity y1(t) = Fmethanol(t) always varies with respect to some delay r1(t). Therefore, the value y2(t) = Fair(t) will lag in time from the desired value ksooty1(t). Alleviate this problem allows to block a, which has two inputs and is described by the expression:
r2(t)=ksoot[γr1(t)+(1-γ)y1(t)],
where γ – parameter determining the contribution r1(t) and y1(t) to the value r2(t).
Thus a block diagram of the automatic control system the level of vapor in the evaporator installation type NDA-P is shown in Fig. 3.2–3.4.
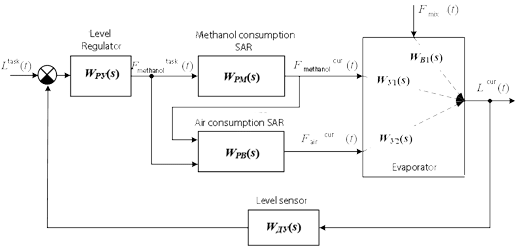
Figure 3.2 – Block diagram of the ACS level of vapor in the evaporator installation type NDA-P
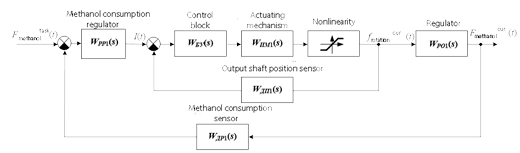
Figure 3.3 – Block diagram of the SAR methanol consumption
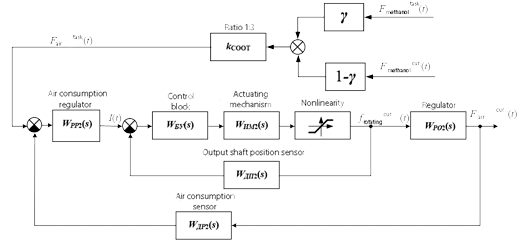
Figure 3.4 – Block diagram of the ACS airflow
The algorithm system is enclosed in an effort to reduce the control error to zero. An adjustable parameter, the level of vapor Lcur compared with a predetermined value Ltask. Based on the difference of these two values is generated impact level regulator formed supplied to the methanol-air
flow ratio control system. Actuator mechanisms determine the angle of rotation of the regulatory authorities, which, in turn, alter the amount of substances entering the evaporator.
For comparison of the actual value of the controlled parameter with its setpoint, this parameter is fed to the controlled object output (by means of the level sensor) of the comparison element, whereby a closed loop transmission effects. Adjustable parameter through the main feedback is input to the controller with the sign of the inverse of the input impact, so the main feedback is considered negative.
3.2 Mathematical model of control object
The mathematical model of the system elements such as methanol NDA-P automatic cleaning installation management.[4]
The evaporator is described by a mathematical model, which the input - Fmethanol(t), Fair(t) and Fmix(t) coming from the evaporator, and the output – level steam mix L(t):

or

where V – volume of the evaporator, m3;
S – evaporator cross-sectional area, m2.
Realizing the model in Simulink package (Fig. 3.5).
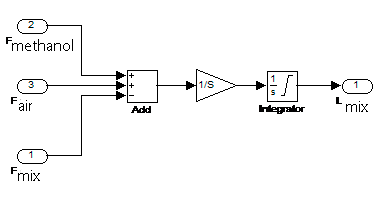
Figure 3.5 – Block diagram of the evaporator in Simulink package
3.3 Simulation of the control system and the quality of performance analysis
In the result of inputting object management of fixed values of L level-steam mix, the amount of mix Fmix leaving the evaporator, the resulting chart transients shown on animation (1 and 2 frames).
The quality of the transition process on the level meets the requirements for constant input actions:
- regulation time – 280 s;
- static error – 0 %;
- overshoot – 1 %.
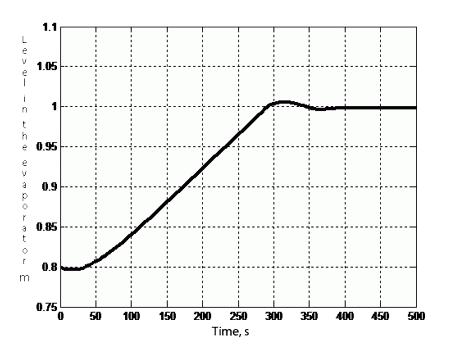
Animation – Transients (animation consists of 5 frames with a delay in 5 s between them, the number of repetition cycles – 7)
The quality of the transition process on a level with a variable flow rate of the mixture from the evaporator meets the requirements – a deviation from the target value by increasing the flowrate of the mixture into 3·10-4 m3/s is 1 sm, and a decrease of 6·10-4 m3/s – 10 sm.
4 Choice of complex of technical facilities
4.1 Requirements to ACS elements
We formulate the requirements for the basic elements of the system such as methanol NDA-P automatic cleaning installation management. [7, 9]
4.2 The temperature sensor
Temperature sensor ZET 7021 TermoTR-485 and its variants have the following output devices: RTD temperature measurement immediately after the power supply and does not require special maintenance. All necessary settings are set during the initial and periodic calibration and stored in the memory of the measuring module.
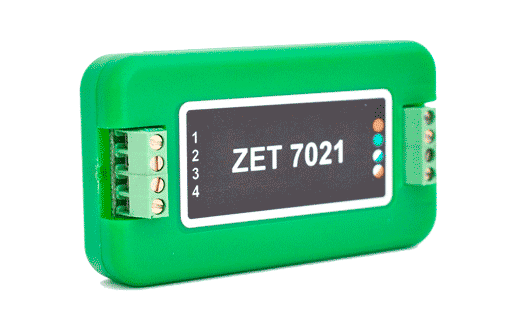
Figure 4.1 – Exterior of temperature sensor
The units are intended for use in enclosed areas without aggressive media at an ambient temperature of 5 to 50°C and the upper limit of 80% relative humidity at 35°C and lower temperatures without condensation. They are resilient and do not create products of industrial interference. With this in mind intelligent sensor ZET 7021 TermoTR-485 the best option. This is supported by the fact that it has a unified output signal can be connected to a computer. The sensor has a small size, as opposed to the PCB, the RACs or KSM, which is hopelessly outdated, therefore, in their place can be safely put intelligent sensor ZET 7021 TermoTR-485.
4.3 Regulator
As a regulator that implements the PID control law, take Remicont
P-130, which is part of all three ACP. Remicont
P-130 – regulating microprocessor controller.
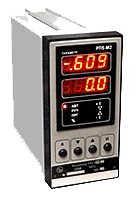
Figure 4.2 – Exterior of regulator
Selection of the controller due to the fact that Remicont
P-130 is a compact microprocessor controller with 28 I/O channels and equipped with a digital interface channel serial communication. On the controller front panel are operational controls, with which realize a large number of operational teams. Remicont
P-130 implements the functions of single-loop, cascade, software, supervisory and multivariable control, and logic-control software and then use commands and the algebra of logic, which provides a high level of regulation.
4.4 Work selection key
As we choose to BRU-32 works as a kind of selection key. BRU-32 unit provides the following functions: remote switching from automatic control to manual and back, push-button actuator control more-less
or less-more
regulating the output device with a pulse input, the determination of the regulatory body position.
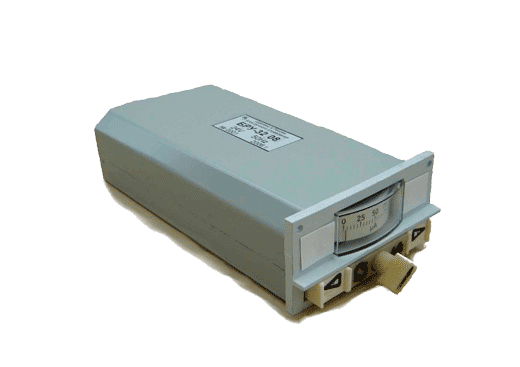
Figure 4.3 – Manual control unit
Conclusions
To achieve our goal following tasks were completed:
- Analyze the process of methanol purification, to identify its characteristics and identify the variables that influence the methanol refining process in the machine.
- Review the existing automatic control systems and analysis of the process as a control object.
- Get a mathematical model and synthesize controllers for management reporting facility. Perform simulation of the developed system.
- Develop a functional diagram automation and formulate requirements for technical means of automation.
Compiled a block diagram of the system control such as methanol cleaning NDA-P. The mathematical models of components of ACS based on data catalogs and data sheets of automation, which are part of the system. Using the above block diagram and mathematical models developed simulation model of the control system in MATLAB & SIMULINK package.
After analyzing the graphs can be concluded that the developed system is stable and transient quality indicators meet the requirements of the customer.
The functional circuit based on the composition and structure of the system functional units. Spend a selection of the necessary automation tools.
In writing this essay master's work is not yet complete. Final completion: May 2016. The full text of work and materials on the topic can be obtained from the author or his manager after that date.
List of references
- Голубятников В. А., Шувалов В. В. Автоматизация производственных процессов в химической промышленности. М., 1985.
- Емельянов А. И., Капник О. В. Проектирование систем автоматизации технологических процессов: Справочное пособие по содержанию и оформлению проектов. – 3-е изд., перераб. и доп. – М.: Энергоатомиздат, 1983. – С. 400.
- Клюев А. С. и др. Проектирование систем автоматизации технологических процесссов: Справочное пособие /Клюев А. С., Глазов Б. В., Дубровский А. Х.; Под. Ред. А. С. Клюева. – М.: Энергия, 1980. – C. 512.
- Олссон Г. Цифровые системы автоматизации и управления / Г. Олссон, Д. Пиани. – СПб: Невский Диалект, 2001. – C. 557.
- Проектирование систем контроля и автоматического регулирования металлургических процессов. Учеб. Пособие для вузов/Глинков Г. М., Маковский В. А., Лотман С. Л., Шапировский М. Р. 2-е изд., перераб. и доп.: – М.: Металлургия, 1986. – C. 352.
- Проектирование систем автоматизации технологических процессов/ Сост.: Т. В. Лопатина, И. И. Лапаев; КИЦМ. – Красноярск, 1988. – C. 36.
- Промышленные приборы и средства автоматизации: Справочник / В. Я. Баранов, Т. Х. Безновская, В. А. Бек и др.; Под общ. ред. В. В. Черенкова. Л.: Машиностроение. Ленингр. отд-ние. 1987. – C. 847.
- СТП ГАЦМиЗ 7-99 Текстовые документы в учебном процессе. Общие требования к оформлению.
- Филлипс Ч. Системы управления с обратной связью / Ч. Филлипс, Р. Харбор. – М.: Лаборатория базовых знаний, 2001. – C. 616.