Система автоматического управления процессом очистки метанола методом возгонки в агрегатах типа НДА
Содержание
- Введение
- 1. Цель и задачи разработки САУ
- 2. Анализ объекта управления
- 2.1. Описание и общая характеристика объекта управления
- 2.2. Установка очистки метанола как объект управления
- 3. Синтез системы автоматического управления
- 3.1. Выбор типа и разработка структурной схемы САУ
- 3.2. Математическая модель объекта управления
- 3.3. Моделирование системы управления и анализ показателей качества
- 4. Выбор комплекса технических средств
- 4.1. Требования к элементам САУ
- 4.2. Датчик температуры
- 4.3. Регулятор
- 4.4. Ключ выбора работ
- Выводы
- Список использованных источников
Введение
Совершенствование управления по отношению к рациональному планированию работы цехов является важной практической задачей деятельности метанолового завода. Решение, которое может быть достигнуто за счет создания типовых систем автоматического контроля и управления отдельными технологическими линиями с учетом постоянно возрастающих требований к качеству выпускаемой продукции.[1]
1. Цель и задачи разработки САУ
Цель работы – повышение выхода годной продукции за счет разработки системы автоматического управления установкой очистки метанола типа НДА-П. Для достижения поставленной цели необходимо решить следующие задачи:
- Проанализировать технологический процесс очистки метанола, выявить его особенности и определить переменные оказывающие влияние на процесс очистки метанола в аппарате.
- Провести обзор существующих систем автоматического управления и анализ процесса как объекта управления.
- Получить математическую модель и синтезировать регуляторы для рассматриваемого объекта управления. Провести моделирование разработанной системы.
- Разработать функциональную схему автоматизации и сформулировать требования к техническим средствам автоматизации.
2. Анализ объекта управления
2.1. Описание и общая характеристика объекта управления
Изобретение относится к области органической химии, а именно к технологии производства метанола прямым окислением метансодержащего газа (природного газа).
Основная проблема создания малотоннажных установок для получения метанола состоит в том, что все существующие на сегодня способы прямого окисления метана в метанол кислородом воздуха осуществляют при низкой концентрации кислорода в исходной газовой смеси и, следовательно, на выходе из реактора реакционная смесь будет обогащена метаном, азотом, окисью и двуокисью углерода и другими элементами.[2]
Рециркуляция метана требует его отделения от реакционной смеси, что является весьма затруднительным. Поэтому выход метанола, в расчете на весь пропущенный метан, остается крайне низким, а рециркуляция метана практически невозможной, как и окисление всего метана за один проход.[3]
Однако экспериментальным путем могут быть найдены соотношения параметров рабочего процесса и геометрических характеристик обогреваемого реактора, при которых данная задача становится разрешимой (весь поступающий на вход реактора метан окисляется за один проход с получением приемлемого выхода метанола и его содержанием в получаемом оксидате).
Технологический процесс, рассматриваемый в работе, представлен тремя взаимосвязанными объектами. В испарителе происходит испарение метанола. Метанол, содержащий 10-12% воды, непрерывно поступает в испаритель, туда же подается воздух, который барботирует через слой водного метанола и насыщается его парами. Затем паровоздушная смесь идет в реактор. Паровоздушная смесь попадает в реактор, температура в котором 500-600°С. Реакционные газы сразу же попадают в холодильник, где происходит охлаждение смеси и предотвращается распад продукта.
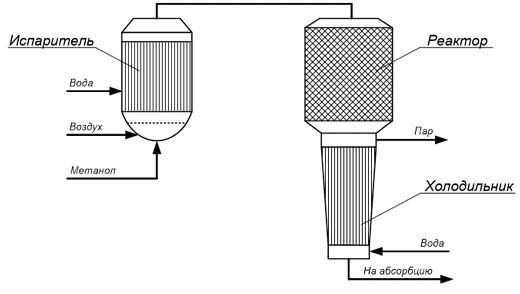
Рисунок 2.1 – Анализ объекта управления
Метанол содержит большое число разнообразных соединений, полное разделение которых обычными способами ректификации невозможно. Хорошо отделяются от метанола лишь легколетучие примеси: ацетальдегид, метилформиат, метилацетат, фуран, ацетон и др., имеющие высокий коэффициент ректификации. Соединения, входящие в состав метанола-сырца, образуют двойные, тройные и еще более сложные азеотропные смеси, что затрудняет отделение их от метанола. С учетом этих особенностей для получения товарного метанола в ЦНИЛХИ были разработаны непрерывно действующие аппараты НДА-I и НДА-П.
2.2 Установка очистки метанола как объект управления
Для изучения установки как объекта регулирования и построения основных технологических зависимостей с помощью системы контроля и дистанционного управления определяются связи между технологическими величинами.
Одним из основных требований, предъявляемых к процессу очистки, является стабилизация температуры в реакторе.[5, 6s]]
Температура в реакторе зависит как от уровня подаваемой воды, так и от уровня метанола. Расход сырья контролируется дозаторами или выбором регулирующего вентиля с электроприводом.
В связи с тем, что приготавливаемый в аппарате метанол поступает на обжиг в реактор, он должен иметь контролируемую влажность. Избыточное содержание воды в метаноле требует дополнительных затрат топлива на ее испарение в реакторе. Содержание влаги должно быть таким, чтобы обеспечить установленный температурный режим достаточным количеством продукта перегона, а также обойтись без перекачивания лишнего уровня влаги.
Контролируемыми параметрами в испарителе являются: расход метанола, расход воздуха и давление пара. По технологическим требованиям расход метанола должен составлять Fм = 3 м3/ч, расход воздуха Fв = 30 нм3/ч.
Контролируемыми параметрами в реакторе являются давление пара, которое по технологическим требованиям должно составлять Рп = 0,5 МПа.
Регулируемым параметром в испарителе является соотношение расходов воздух-метанол, причем регулирование происходит с коррекцией по уровню метанола в испарителе. Уровень метанола в испарителе составляет L = 1м.
Регулируемым параметром в реакторе является температура. Температура в реакторе регулируется изменением подачи воды в холодильник. По технологическим требованиям температура в реакторе должна находиться в диапазоне 40-50°С.
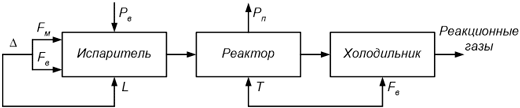
Рисунок 2.2 – Анализ процесса очистки метанола как объекта управления
Таким образом, системы автоматического управления процессом очистки метанола должны обеспечивать стабилизацию технологических параметров – чистоты перегона, влажности и максимальной производительности.
Управляющими переменными выступают: расход метанола, расход воздуха, уровень метанола, давление воздуха в испарителе, температура в реакторе и расход воды в холодильнике.
Возмущающими переменными выступают: температура реакционных газов и давление пара в холодильнике.
3. Синтез системы автоматического управления
3.1. Выбор типа и разработка структурной схемы САУ
Разрабатываемая систему автоматического управления установкой очистки метанола типа НДА-П должна поддерживать уровень в испарителе на заданном уровне (L = 1м) при автоматическом регулировании соотношения расходов (1:3) воздух-метанол при действии возмущающих воздействий, поэтому будем использовать структуру системы управления в которой реализован принцип управления по отклонению.
Задачу регулировки соотношений расхода воздуха и метанола можно решить применив структурную схему приведенную на рис. 3.1.
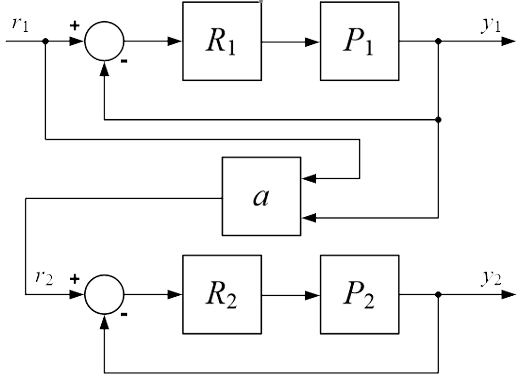
Рисунок 3.1 – Регулятор соотношений с увеличенным быстродействием
Первый регулятор (расхода метанола) поддерживает выходную величину y1 равной значению уставки r1. Величина y1(t)=Fметанол(t) всегда изменяется с некоторой задержкой относительно r1(t). Поэтому величина y2(t)=Fвоздух(t) будет отставать по времени от желаемого значения kсоотy1(t). Смягчить данную проблему позволяет блок a, который имеет два входа и описывается выражением:
r2(t)=kсоот[γr1(t)+(1-γ)y1(t)],
где γ – параметр, определяющий вклад r1(t) или y1(t) в величину r2(t).
Таким образом, структурная схема системы автоматического управления уровнем паровоздушной смеси в испарителе установки типа НДА-П приведена на рис. 3.2–3.4.
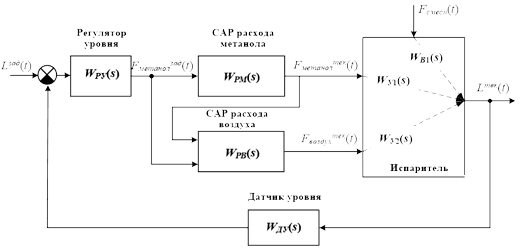
Рисунок 3.2 – Структурная схема САУ уровнем паровоздушной смеси в испарителе установки типа НДА-П
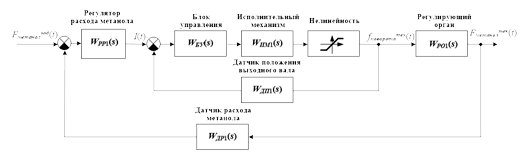
Рисунок 3.3 – Структурная схема САУ расхода метанола
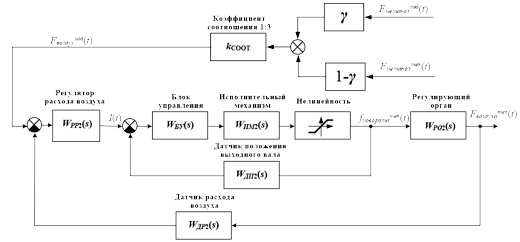
Рисунок 3.4 – Структурная схема САУ расхода воздуха
Алгоритм работы системы заключен в стремлении свести ошибку управления к нулю. Регулируемый параметр, уровень паровоздушной смеси Lтек сравнивается с заданным значением Lзад. На основании разности этих двух величин вырабатывается воздействие формируемое регулятором уровня поступающее на системы регулирования соотношений расхода метанол-воздух
. Исполнительные механизмы определяют угол поворота регулирующих органов, которые в свою очередь, изменяют количество веществ поступающих в испаритель.
Для сравнения фактического значения регулируемого параметра с его заданным значением этот параметр подается с выхода объекта регулирования (с помощью датчика уровня) на элемент сравнения, в результате чего образуется замкнутый контур передачи воздействий. Регулируемый параметр через главную обратную связь подается на вход регулятора со знаком обратным по отношению к входному воздействию, поэтому главная обратная связь считается отрицательной.
3.2. Математическая модель объекта управления
Получим математические модели элементов системы автоматического управления установкой очистки метанола типа НДА-П.[4]
Испаритель описывается математической моделью, вход которой – расходы метанола Fметанол(t), воздуха Fвоздуха(t) и смеси Fсмеси(t) выходящей из испарителя, а выход – уровень паровоздушной смеси L(t):

или

где V – объем испарителя, м3;
S – площадь поперечного сечения испарителя, м2.
Реализуем модель в пакете Simulink (рис. 3.5).
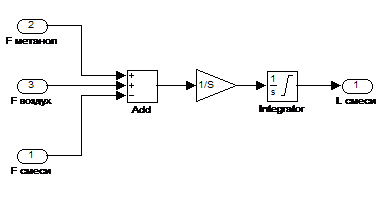
Рисунок 3.5 – Структурная схема испарителя в пакете Simulink
3.3. Моделирование системы управления и анализ показателей качества
В результате подачи на вход объекта управления фиксированных значений уровня паровоздушной смеси L, количества смеси Fсмеси выходящей из испарителя, получены графики переходных процессов, приведенные на анимации (1 и 2 кадр).
Качество переходного процесса по уровню при постоянных входных воздействиях соответствует требованиям:
- время регулирования – 280 с;
- статическая ошибка – 0 %;
- перерегулирование – 1 %.
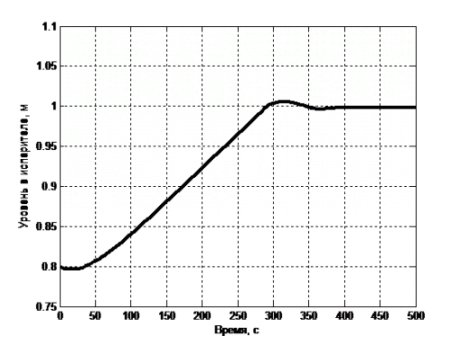
Анимация – Переходные процессы (анимация состоит из 5 кадров с задержкой в 5 с между ними, количество циклов повторения – 7)
Качество переходного процесса по уровню при переменном расходе смеси из испарителя соответствует требованиям – отклонение от заданного значения при увеличении расхода смеси на 3·10-4 м3/с составляет 1 см, а при уменьшении на 6·10-4 м3/с – 10 см.
4. Выбор комплекса технических средств
4.1. Требования к элементам САУ
Сформулируем требования к основным элементам системы автоматического управления установкой очистки метанола типа НДА-П.[7, 9]
4.2. Датчик температуры
Термодатчик ZET 7021 TermoTR-485 и его разновидности имеют следующие выходные устройства: термопреобразователь сопротивления измерение температуры сразу после подачи питания и не требует специального технического обслуживания. Все необходимые настройки устанавливаются при первичной и периодической поверках и сохраняются в памяти измерительного модуля.
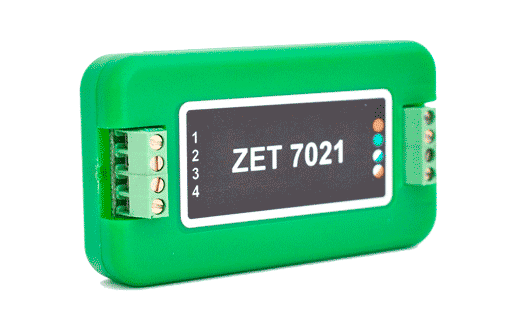
Рисунок 4.1 – Внешний вид датчика температуры
Установки предназначены для работы в закрытых помещениях без агрессивных сред при температуре окружающего воздуха от 5 до 50°С и верхнем значении относительной влажности 80% при 35°С и более низких температурах без конденсации влаги. Они являются восстанавливаемыми изделиями и не создают индустриальных радиопомех. С учетом вышесказанного интеллектуальный термодатчик ZET 7021 TermoTR-485 оптимальный вариант. В пользу этого говорит и то, что он обладает унифицированным выходным сигналом возможностью подключения к ЭВМ. Датчик имеет малые размеры, в отличие от КСП, КСД или КСМ, которые безнадежно устарели, следовательно, на их место смело можно ставить интеллектуальный термодатчик ZET 7021 TermoTR-485.
4.3. Регулятор
В качестве регулятора, реализующего ПИД-закон регулирования, возьмем Ремиконт
Р-130, который входит в состав всех трёх АСР. Ремиконт
Р-130 – регулирующий микропроцессорный контроллер.
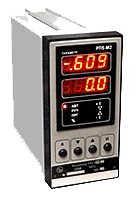
Рисунок 4.2 – Внешний вид регулятора
Выбор этого контроллера обусловлен тем, что Ремиконт
Р-130 представляет собой компактный микропроцессорный контроллер, имеющий 28 каналов ввода/вывода и оснащенный интерфейсным каналом цифровой последовательной связи. На лицевой панели контроллера расположены органы оперативного управления, с помощью которых реализуют большое число оперативных команд. Ремиконт
Р-130 реализует функции одноконтурного, каскадного, программного, супервизорного и многосвязного регулирования, а также логико-программное управление с последующим использованием команд и алгебры логики, что обеспечивает высокий уровень регулирования.
4.4. Ключ выбора работ
В качестве ключа выбора рода работ мы выбираем БРУ-32. Блок типа БРУ-32 выполняет следующие функции: дистанционное переключение с автоматического режима управления на ручной и обратно, кнопочное управление исполнительными устройствами больше-меньше
, световая индикация выходного сигнала регулирующего устройства больше-меньше
с импульсным входным сигналом, определение положения регулирующего органа.
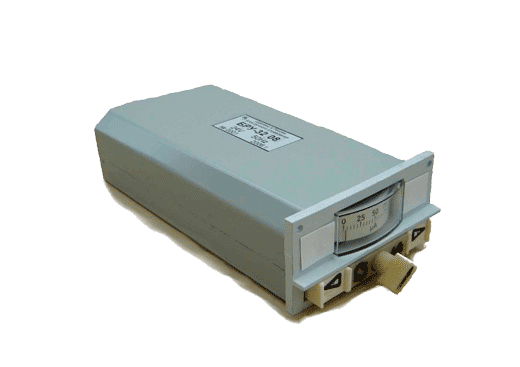
Рисунок 4.3 – Блок ручного управления
Выводы
Для достижения поставленной цели решены следующие задачи:
- Проанализировать технологический процесс очистки метанола, выявить его особенности и определить переменные, оказывающие влияние на процесс очистки метанола в аппарате.
- Провести обзор существующих систем автоматического управления и анализ процесса как объекта управления.
- Получить математическую модель и синтезировать регуляторы для рассматриваемого объекта управления. Провести моделирование разработанной системы.
- Разработать функциональную схему автоматизации и сформулировать требования к техническим средствам автоматизации.
Составлена структурная схема системы управления установкой очистки метанола типа НДА-П. Получены математические модели элементов САУ на основании данных каталогов и технических паспортов средств автоматизации, которые входят в состав системы. Используя приведенную структурную схему и математические модели, разработанная имитационная модель системы управления в пакете MATLAB&SIMULINK.
Проанализировав полученные графики можно сделать вывод, что разработанная система является устойчивой и показатели качества переходных процессов удовлетворяют требованиям заказчика.
Разработана функциональная схема с учетом состава и структуры функциональных узлов системы. Проведен выбор необходимых средств автоматизации.
При написании данного реферата магистерская работа еще не завершена. Окончательное завершение: май 2016 года. Полный текст работы и материалы по теме могут быть получены у автора или его руководителя после указанной даты.
Список использованных источников
- Голубятников В. А., Шувалов В. В. Автоматизация производственных процессов в химической промышленности. М., 1985.
- Емельянов А. И., Капник О. В. Проектирование систем автоматизации технологических процессов: Справочное пособие по содержанию и оформлению проектов. – 3-е изд., перераб. и доп. – М.: Энергоатомиздат, 1983. – С. 400.
- Клюев А. С. и др. Проектирование систем автоматизации технологических процесссов: Справочное пособие /Клюев А. С., Глазов Б. В., Дубровский А. Х.; Под. Ред. А. С. Клюева. – М.: Энергия, 1980. – C. 512.
- Олссон Г. Цифровые системы автоматизации и управления / Г. Олссон, Д. Пиани. – СПб: Невский Диалект, 2001. – C. 557.
- Проектирование систем контроля и автоматического регулирования металлургических процессов. Учеб. Пособие для вузов/Глинков Г. М., Маковский В. А., Лотман С. Л., Шапировский М. Р. 2-е изд., перераб. и доп.: – М.: Металлургия, 1986. – C. 352.
- Проектирование систем автоматизации технологических процессов/ Сост.: Т. В. Лопатина, И. И. Лапаев; КИЦМ. – Красноярск, 1988. – C. 36.
- Промышленные приборы и средства автоматизации: Справочник / В. Я. Баранов, Т. Х. Безновская, В. А. Бек и др.; Под общ. ред. В. В. Черенкова. Л.: Машиностроение. Ленингр. отд-ние. 1987. – C. 847.
- СТП ГАЦМиЗ 7-99 Текстовые документы в учебном процессе. Общие требования к оформлению.
- Филлипс Ч. Системы управления с обратной связью / Ч. Филлипс, Р. Харбор. – М.: Лаборатория базовых знаний, 2001. – C. 616.