Исследование и разработка системы автоматического управления технологическим процессом сушки гранулированных смесей
Содержание
- Введение
- 1. Анализ состояния вопроса автоматизации
- 1.1. Анализ процесса сушки как объекта управления
- 1.2. Модель материальных потоков печи кипящего слоя
- 2. Анализ существующих САУ
- 3. Синтез САУ
- 3.1. Выбор типа САУ
- 3.2. Математическая модель объекта управления и элементов
- Выводы
- Список источников
Введение
Удаление влаги из твердых и пастообразных материалов позволяет удешевить транспортировку, придать им необходимые свойства, а также уменьшить коррозию аппаратуры и трубопроводов при хранении или последующей обработке этих материалов.
Влагу можно удалять из материалов механическими способами (отжимом, отстаиванием, фильтрованием, центрифугированием). Однако более полное обезвоживание достигается путем испарения влаги и отвода образующихся паров, т. е. с помощью тепловой сушки. [1]
Основным параметром, определяющим процесс сушки, является конечная влажность продукта. Однако в настоящее время промышленных влагомеров, работающих в потоке, мало, поэтому для правильного ведения процесса сушки в качестве регулируемых используются косвенные параметры: температура сушильного агента, выходящего из сушилки, температура высушенного продукта; регулирующим воздействием является количество подводимого тепла.
1. Анализ состояния вопроса автоматизации
1.1. Анализ процесса сушки как объекта управления
Cушилки широко распространены в химической и смежных отраслях промышленности, поскольку в аппаратах такого типа можно высушивать зернистые, пастообразные и жидкие материалы. Процесс протекает с большой скоростью, съем влаги с 1 м2 газораспределительной решетки в зависимости от размера частиц материала и температурного режима сушки составляет 500—2000 кг/(м2·ч). Возможность сушки слипающихся, пастообразных и жидких материалов объясняется тем, что кипящий (взвешенный, псевдоожиженный) слой является как бы ретуром
предварительно подсушенного продукта.
В установках со взвешенным слоем можно одновременно проводить несколько процессов, например сушку и обжиг, сушку и гранулирование, сушку и измельчение. [3]
Периодически действующие сушильные установки предназначены для сушки сыпучих и пастообразных материалов в малотоннажных производствах химической и химико-фармацевтической промышленности.
Сушилка имеет камеру, которая установлена на тележке, что позволяет производить загрузку влажного и выгрузку высушенного материала вне пределов установки. После загрузки камера вкатывается в нижнюю часть сушильной зоны, при помощи рычагов поднимается и соединяется с фильтром, расположенным в верхней части сушильной зоны. Фильтр представляет собой каркас из системы концентрических колец, на которые натянут конус из стеклоткани (площадь поверхности 20 м2). Фильтр периодически встряхивается с частотой вибраций 2800. Вибратор заключен в кожух с поддувом чистого воздуха или азота. К сушильной зоне примыкает зона со вспомогательным оборудованием – вентилятором, паровыми калориферами и калориферами для высокотемпературного теплоносителя.
Сушилка такого типа могут быть снабжены перемешивающими устройствами для пастообразных материалов, рассыпающихся в процессе сушки.
Примером сушилки полунепрерывного действия, обеспечивающей непрерывность процесса по транспорту твердой фазы при периодической сушке, может служить сушилка с вращающимися перегородками. В этих аппаратах достигается равномерная сушка, однако применять их можно только в малотоннажных производствах.
При сушке комкующихся материалов, а также термочувствительных продуктов гидродинамический режим в прирешеточной зоне должен быть достаточно активным, застойные зоны должны отсутствовать. Такой режим обеспечивается в аппаратах со слоем расширяющегося сечения – фонтанирующим. Эти аппараты легко масштабируются путем параллельного соединения соответствующего количества желобов. Отличие состоит в том, что в аппарате с вихревым слоем теплоноситель подводится в слой тангенциально, решетка беспровальная, а в аппарате с фонтанирующим слоем ввод теплоносителя осуществляется снизу.
Сушилки со взвешенным слоем успешно используются для сушки суспензий и растворов, причем высушенный продукт может быть получен либо в гранулированном виде, либо в виде порошка.
При получении высушенного материала в виде гранул процесс обычно проводят в слое высушиваемого материала с разгрузкой продукта из слоя, а при необходимости получения сравнительно тонкодисперсного материала и в тех случаях, когда высушиваются термочувствительные и вязкие материалы рекомендуется сушка с использованием инертных частиц (фторопластовых, фарфоровых и др.). Следует иметь в виду, что в последнем случае процесс более устойчив, поскольку масса слоя, состоящего практически только из инертных частиц, в процессе сушки не изменяется.
1.2. Модель материальных потоков печи кипящего слоя
При разработке автоматизированной системы управления сушки в печи кипящего слоя, важнейшим этапом синтеза системы является анализ процесса, как объекта управления, то есть определение входных и выходных переменных, нахождение математических зависимостей между входными и выходными переменными описывающих поведение объекта регулирования.
При малых скоростях сыпучий слой, собой фильтрующий слой и его объем не изменяется, он остается неподвижным. С увеличением скорости потока воздуха, обогащенного кислородом, сопротивление слоя возрастает, вследствие трения газовой смеси о поверхность сырья и при прохождении газовых струй по каналам различного сечения, образующимися между частицами концентрата. При достижении определенной скорости газового потока, называемой минимально критической, качественно и объемно изменяется сыпучий слой концентрата и переходит в псевдоожиженное состояние, приобретает свойства жидкости выше перечисленные. [4]
Таким образом, для процесса сушки в печи КС, можно выделить входные материальные переменные, свойства которых изменяются в данном процессе.
Для данного процесса этими особенностями являются:
- давление теплоносителя перфорированным листом, кПа;
- температура теплоносителя, °С;
- температура на материале в СВК, °С;
- температура отходящих газов, °С;
- расход теплоносителя, м3/час;
- расход отходящих газов, м3/час.
Такое выделение входных переменных, характеризующих состояние входного потока по концентрату обусловлено следующими причинами – расход концентрата влияет на весь режим работы печи кипящего слоя, на ее производительность, на тепловой баланс и т.д.
Состояние входного материального потока по воздуху будет характеризоваться следующими входными переменными: расходом дутья, концентрации кислорода в газовой фазе, давлением в воздушной коробке.
Особенность управления процессом сушки заключается в том, что влажность получаемого продукта традиционно определяется не непосредственно, а косвенно, за температурой отходящих из печи газов. Это обусловлено отсутствием датчика, измеряющего содержание внутри кристаллической воды. Функциональная схема процесса сушки в печи, отражающий основные информационные переменные печи с точки зрения рассмотрения ее как объекта управления, приведена на анимации.
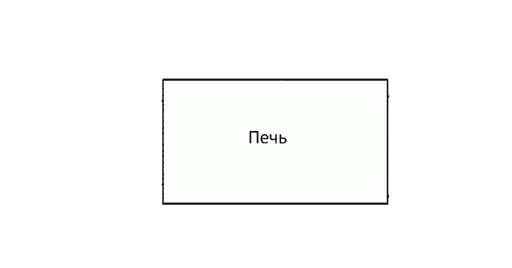
Анимация – Схема анализа процесса сушки в камере как объекта управления (анимация состоит из 5 кадров с промежутком в 1 с, количество циклов повторения - 7)
Из множества факторов, влияющих на температуру отходящих газов, можно выделить подачу газа в печь и скорость загрузки печи. Скорость загрузки концентрата в печь является возмущением, а подача газа – управляющим воздействием. Вариация влажности концентрата, подаваемого в печь, является неконтролируемым возмущением. Такой выбор входных воздействий для температуры продиктован тем, что предполагается неограниченное подача газа в печь в любое время суток, и газ может быть подан в количестве, достаточном для ее полной загрузки. Это позволит при оперативном управлении камерой подавать на нее столько концентрата, сколько производят предварительные стадии технологического процесса.
Анализ производительности печи требует учета ситуации, когда поставщик газа, в зависимости от времени суток, ограничивает его подачу некоторыми уровнями, меньше максимальной производительности печи или подача газа по некоторым причинам нестабильна. Таким образом, необходимо разработать систему автоматического управления печью, учитывающий взаимные перекрестные влияния локальных каналов управления температуры и производительности друг на друга с учетом технологических ограничений на производительность камеры сушки, а также конструктивные ограничения на исполнительные механизмы.
2. Анализ существующих САУ
На практике осуществляют два способа регулирования температуры слоя: изменением загрузки влажного материала и изменением расхода сушильного агента.
При использовании первого способа может автоматически увеличиться производительность сушилки (в случае уменьшения начальной влажности материала). Однако в этом случае между сушилкой и предыдущим технологическим аппаратом должен быть помещен промежуточный бункер, что нежелательно, а часто и просто недопустимо (из-за тенденции влажного материала к свободообразованию и зависанию в бункере). Схема автоматического управления работой такой сушилки включает в себя узлы регулирования соотношения расходов топлива и первичного воздуха, температуры сушильного агента на входе в сушилку, расхода сушильного агента, температуры кипящего слоя, уровня кипящего слоя и разрежения в сушилке.
При использовании второго способа регулирования температуры слоя регулирующее воздействие вносится изменением расхода топлива, температура сушильного агента на входе в сушилку регулируется изменением расхода вторичного воздуха.
Эти способы имеют ряд существенных недостатков, а именно:
- недостаточно высокое качество готового продукта;
- длительность проведения процесса сушки;
- большая инерционность системы, т.е. низкая точность и надежность управления процессом сушки.
3. Синтез САУ
3.1. Выбор типа САУ
Управляемая величина определена технологией – это температура отходящих из печи газов. Из множества, влияющих на температуру факторов выбраны два самых значительных: подачу газа в печь и скорость загрузки печи. Скорость загрузки концентрата печи принята за возмущение, а подача газа за управляющую величину. Будем считать вариацию влажности подаваемого в печь концентрата неконтролируемым возмущающим фактором. Такой выбор продиктован тем, что подача газа осуществляется в количестве, достаточном для ее полной загрузки. Это позволит при оперативном управлении печью подавать на нее столько концентрата, сколько производят предыдущие стадии технологического процесса. [5]
Наряду со скоростью загрузки концентрата, в качестве возмущений следует рассматривать и ряд других, менее значимых, но ощутимых своим воздействием на процесс обжига факторов, прежде всего вариаций влажности исходного концентрата, а также метеоусловий. Но если построить САР стабилизации температуры по принципу замкнутой САР с управлением по отклонению, то, даже не контролируя эти величины, САР будет компенсировать их влияние. И ее в основном достаточно. Тем более что управляемую величину, т.е. температуру отходящих из печи газов, сравнительно не трудно измерять в процессе управления. Общая структурная схема САР с управлением по отклонению хорошо известна и широко применяется в промышленности.
В качестве исполнительного механизма в схеме выбран двигатель постоянного тока (ДПТ) с редуктором, тогда в установившемся режиме двигатель будет все время «подруливать» заслонкой подачу газа. Такая система управления непрерывная [2]. Исполнительный механизм такого рода сравнительно дорогой, но для такого серьезного объекта, как обжиговая печь он может быть применен, поскольку его стоимость не соизмерима со стоимостью печи. Этот механизм нелинейный, позволяет открывать заслонку только в допустимых пределах.
С целью экономии затрат на газ предлагается выбрать двухконтурную САУ, реализующую подчиненное регулирование. Окончательная структура САУ будет представлять два контура. Внешний – регулятор температуры отходящих газов, корректирующий задание на расход теплоносителя в соотношении расходов газ-воздух, так, что Fгаз=γ(Т)·Fвоз.
3.2. Математическая модель объекта управления и элементов
Для построения линейной динамической модели объекта управления достаточно иметь его репрезентативные разгонные характеристики, как по управляющей величине, так и по возмущающей. Эти характеристики снимаются по отдельности путем ступенчатого изменения на малые проценты от номинальных величин воздействий объекта, функционирующего в номинальном режиме и измерения изменений управляемой величины с течением времени.
Проанализируем имеющиеся технологические данные. Время прогрева пустой
печи, при увеличении подачи теплоносителя с 7000 куб.м/час до примерно 10000 куб.м/час, составляет 400 сек. А при изменении подачи теплоносителя с 8000 до 10000 куб.м/час при увеличивающейся подаче концентрата, составляющей вначале 1 т/час (что по технологии является минимальной величиной загрузки, когда температура отходящих газов составляет 60 °С), характерное время изменения температуры составляет примерно 100 сек.
Печь может быть приближенно промоделирована в динамике апериодическим звеном. И постоянная времени его должна составить третью часть характерного времени изменения температуры. Имеет смысл считать объект управления более инерционным. Действительно, если в реальности печь будет иметь меньшую инерционность, то это несколько ухудшит показатели качества установившегося режима, что можно исправить при наладочных работах, но САР будет застрахована от потери устойчивости и это для такого серьезного объекта важно. Итак, считаем печь по каналу управления (подача газа – температура отходящих газов) апериодическим звеном с постоянной времени, равной 90 сек.
Коэффициенты усиления динамических звеньев могут быть получены путем деления конечного приращения температуры отходящих газов на величину малого приращения подачи газа или скорости подачи концентрата, для коэффициентов усиления звена по управлению и по возмущению соответственно. А именно для номинального режима с параметрами по подаче теплоносителя 8000 куб.м/час и подаче концентрата 2 т/час:
T, C° = ΔFтепл·Kупр-ΔFтепл·Kвозм
или

Линеаризованная динамическая характеристика печи, работающей в номинальном режиме, по каналу управления, задается передаточной функцией:

Выражение для передаточной функции печи по возмущению можно записать в виде:

Схема моделирования объекта управления по температуре отходящих газов приведена на рис. 3.1.
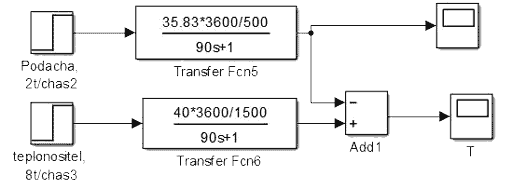
Рисунок 3.1 - Структурная схема линейной модели обжиговой печи
Промоделируем данную схему. Переходная характеристика ОУ, т.е. температуры отходящих газов представлена на рис. 3.2.
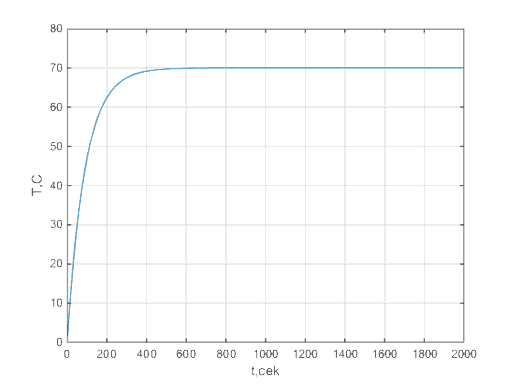
Рисунок 3.2 - Переходная характеристика температуры отходящих газов на выходе из печи КС
На рис. 3.3 приведена переходная характеристика температуры при уменьшении подачи концентрата с 2 т/час до 1,5 т/час в момент времени 750 с. На графике видно, что что температура отходящих газов увеличилась до 90 °С. В момент времени 1400 с подача управляющего воздействия – расхода теплоносителя уменьшена на 800м3/час, чтобы компенсировать уменьшение подачи концентрата, вернув тем самым температуру на требуемый уровень в 70 °С. Т.е.

Таким образом, данный график, отражающий поведение в динамике ОУ, доказывает состоятельность модели, которая будет использована в САУ.
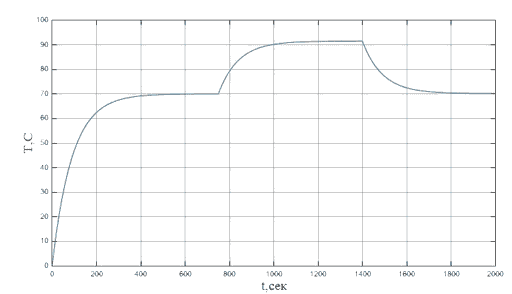
Рисунок 3.3 - Переходная характеристика температуры отходящих газов на выходе из печи КС
Также не маловажна реакция системы на возмущения и его компенсация. В качестве воздействия выступает подача сырья в печь КС. Система должна качественно реагировать на это возмущение и также качественно предотвращать выход системы из заданных параметров. [6]
Выводы
Получена линейная динамическая модель процесса сушки в печи КС, являющаяся инерционным объектом, а также математическая модель исполнительного механизма, учитывающая технологические реальные ограничения по каналу управления и возмущения на входные и выходные сигналы.
Результаты моделирования доказывают работоспособность САР и возможность применения разработанных систем в условиях сушки в печах КС. Основные показатели качества регулирования соответствуют ТЗ:
- апериодический характер переходного процесса с допустимым перерегулированием 15%;
- время установления (регулирования) 15 мин;
- время отработки внешнего возмущения 8 мин.
- Беспалов А. В., Харитонов Н. И. Системы управления химико-технологическими процессами. Учебное пособие для вузов. – М.:Академкнига, 2007 – C. 690.
- Беспалов А. В., Харитонов Н. И. Задачник по системам управления химико-технологическими процессами. Учебное пособие для вузов. – М.:Академкнига, 2007 – C. 690.
- Дорф Р., Бишоп Р. Современные системы управления. – М.: Лаборатория Базовых Знаний. – 2002 – C. 832.
- Лукас В. А. Теория управления техническими системами. Учебный курс для вузов. Екатеринбург: Издательство УГГГА, 2002. – C. 675.
- Филлипс Ч., Харбор Р. Системы управления с обратной связью. – М.: Лаборатория Базовых Знаний, 2001 – C. 616.
- Денисенко В. ПИД – регуляторы: принципы построения и модификации. Статья, C. 8