Research and development of automatic control system of technological process of drying of granular mixtures
Content
- Introduction
- 1 Analysis of the issue of automation
- 1.1 Analysis of the drying process as a control object
- 1.2 Material flow model of BL furnace
- 2 Analysis of existing SAC
- 3 Synthesis of SAC
- 3.1 Selection of the type of SAC
- 3.2 Mathematical model of control object and elements
- Conclusions
- References
Introduction
The removal of moisture from solid and pasty materials allows cheaper transport, to give them desired properties, and also reduce corrosion of equipment and piping for storage or subsequent processing of these materials.
Moisture can be removed from the materials by mechanical means (squeezing, settling, filtration, centrifugation). However, a more complete dehydration is achieved by evaporation and removal of produced vapor, in example via thermal drying. [1]
The main parameter that determines the drying process is a final moisture content of the product. However, in the present, industrial hydrometers that work in a stream are few, so to properly conduct the drying process such indirect control parameters are used: temperature of the drying agent emerging from the dryer, the temperature of the dried product; regulating action is the amount of heat input.
1 Analysis of the issue of automation
1.1 Analysis of the drying process as a control object
Dryers are widely used in the chemical and allied industries, as in the devices of this type can be used to dry granular, paste-like and liquid materials. The process proceeds at high speed removal of moisture from a gas distribution grid 1 m2 depending on the particle size of the material and the temperature drying mode is 500-2000 kg/(m2·h). Possibility of drying sticky, pasty and liquid materials because the boiling (weighted, fluidised) layer is like a retour
pre the dried product.
In the systems with the slurry layer can be simultaneously performed several processes, such as drying and firing, drying and granulating, drying and grinding. [3]
Batch dryers are designed for drying loose and pasty materials in small-scale production of chemical and pharmaceutical industry.
Dryer has a camera, which is mounted on a trolley that allows loading and unloading wet the dried material outside the plant. After loading chamber rolled into the lower part of the drying zone, by means of levers rises and connects with a filter disposed in the upper part of the drying zone. A filter is a frame of a system of concentric rings, which are strung on the cone glass (surface area 20 m2). Filter periodically shaken at a frequency of vibration encased with blowing clean air or nitrogen. By the drying area adjacent area with auxiliary equipment – fans, heaters and steam heaters for high temperature heat carrier.
Dryers of this type can be equipped with a mixing device for pasty materials, crumbling in the drying process.
An example of a semi-continuous dryers, ensuring continuity of the transport of solids in intermittent drying, can serve as a dryer with rotating baffles. In these devices achieved even drying, but they can only be used in small-scale production.
When drying materials lumps, and heat-sensitive products in the hydrodynamic regime zone must be sufficiently active, should be no stagnant zones. This mode is provided in the apparatus with a layer of expandable section - spouting. These devices are easily scaled by parallel connection of a corresponding number of troughs. The difference is that in the device with the whirling bed of the coolant is fed to the bed tangentially unfailing grating, and spouted bed apparatus with coolant entering from below.
Slurry bed dryer with successfully used for drying slurries and solutions, the dried product may be obtained either in granular form or in powder form.
Upon receipt of the dried material in granular form process is generally carried out in a layer of material to be dried from the product discharge from the layer, and if necessary obtain relatively fine particulate material, and in cases where the dried heat-sensitive and viscous materials recommended drying with inert particles (PTFE, porcelain, etc.). It should be borne in mind that the latter process is more stable, because the mass layer composed almost exclusively of the inert particles is not changed in the drying process.
1.2 Material flow model of BL furnace
In the development of automated control system of drying in the fluidized bed furnace, a critical step in the synthesis of a system analysis of the process, as a control object, that is the definition of input and output variables, finding the mathematical relationships between the input and output variables describing the behavior of the controlled system.
At low speeds, bulk layer, a filter layer, and its volume is not changed, it remains motionless. With increasing air flow velocity, the oxygen-rich layer increases the resistance due to friction on the surface of the gas mixture feed and gas streams passing through the channels different cross-section, formed between particles of the concentrate. Upon reaching a certain gas flow rate, called the minimum critical quality and volume changes particulate layer and concentrate becomes fluidized, becomes fluid properties listed above. [4]
Thus, the drying process in the furnace of the COP, it is possible to allocate the input variables material whose properties vary in a given process.
These features for this process are:
- coolant pressure perforated sheet, kPa;
- coolant temperature, °С;
- the temperature of the material in the JMC, °С;
- flue gas temperature, °С;
- coolant flow rate, m3/h;
- flue gas flow rate, m3/h.
Such a selection of the input variables characterizing the state of the input stream for concentrate for the following reasons – concentrate flow rate affects the entire operation of the fluidized bed furnace, on its performance on the heat balance, etc.
Condition input material flow through the air will be characterized by the following input variables: the flow rate of blowing, the oxygen concentration in the gas phase, the pressure in the windbox.
Feature control the drying process is that the moisture content of the resulting product is traditionally defined not directly, but indirectly, the temperature of the exhaust gases of the furnace. This is due to the absence of the sensor, which measures the content in the crystal water. Functional diagram of the drying process in the furnace, which reflects basic information variables of the furnace from the viewpoint of its consideration as a control object is shown on animation.
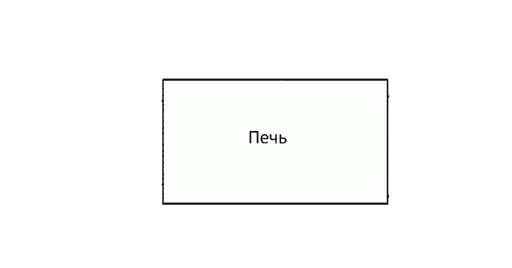
Animation – Analysis diagram of the drying process in the chamber (аnimation concist of 5 frames with delay in 1 s, cycles - 7)
Of the many factors affecting the exhaust gas temperature, gas flow can be identified in the oven and furnace loading speed. The download speed of the concentrate into the furnace is a perturbation, and the gas flow - control action. Variation of moisture concentrate fed into the furnace is uncontrolled disturbance. Such a selection input influences temperature dictated by the fact that an unlimited supply of gas to the furnace is assumed at any time, and gas may be supplied in sufficient amount for its complete download. This will allow the surgical management of the camera apply to it as much concentrate as produce the preliminary stage of the process.
Analysis of furnace productivity requires consideration of the situation where the supplier of gas, depending on the time of day, restricts its flow several levels below the maximum productivity of the furnace or gas is unstable for some reasons. Thus, it is necessary to develop an automatic furnace control, taking into account the mutual influence of cross each other at the local temperature and the control channel performance in view of technological limitations on the performance of drying chamber design as well as limitations on the actuators.
2 Analysis of existing SAC
In practice, carried out two ways to control the bed temperature: a change in load of the wet material and a change in the flow of the drying agent.
When using the first method can automatically increase the efficiency of the dryer (in the case of reducing the initial moisture content). However, in this case, the intermediate tank must be placed between the dryer unit and the previous process, which is undesirable, and often simply unacceptable (because of the tendency of the wet material to hang in a hopper). The scheme of automatic control operation of a dryer includes nodes controlling the ratio of fuel flow and the primary air temperature at the inlet of the drying agent in the dryer, the flow of the drying agent, the temperature of fluidized bed, the fluidized bed level and the vacuum in the dryer.
In the second method for adjusting the bed temperature regulating effect change introduced fuel flow, the temperature of the drying agent in the dryer inlet of secondary air is regulated by changing the flow rate.
These methods have a number of significant shortcomings:
- insufficient quality of the finished product;
- the duration of the drying process;
- a large inertia of the system, ie, low accuracy and reliability of the control of the drying process.
3 Synthesis of SAC
3.1 Selection of the type of SAC
Controlled value is determined by the technology - is the temperature of the exhaust gases from the furnace. Of the many influencing factors on the temperature selected two most significant: the gas supply to the furnace and the furnace load speed. Download speed furnace concentrate taken as a disturbance, and the gas supply for the control amount. We will consider the variation of moisture supplied to the furnace concentrate uncontrolled disturbing factor. This choice is dictated by the fact that the gas supply is in an amount sufficient for its complete download. This will allow the surgical management of the oven to submit to it as much concentrate as produced earlier stage of the process. [5]
In addition to the concentrate loading speed as disturbances should be considered and a number of other, less important, but their impact on the tangible factors roasting process, first of all variations of the original moisture content of the concentrate, as well as weather conditions. But if you build ATS temperature stabilization on the principle of closed ATS-controlled deflection, that even without controlling these values, the SAR will compensate for their effects. And it generally enough. Especially as the manipulated variable, ie, Flue gases from the furnace temperature, is comparatively difficult to measure in the management process. CAP overall structural diagram of a control on the deflection is well known and widely used in the industry.
As an actuator in the scheme chosen DC motor (DPT) with gear, then the steady-state engine will always be taxi
the gas supply valve. This continuous management system [2]. An actuator of this type is relatively expensive, but for such a serious object as kiln it can be applied because its cost is not commensurate with the cost of the furnace. This mechanism is non-linear, you can open the damper only within limits.
In order to save on gas costs prompted to select a two-circuit SAU realizing subordinate regulation. The final structure of the ACS will present two circuits. Appearance – exhaust gas temperature control, job correcting the coolant flow rate in the air-gas ratio of costs so that Fгаз=γ(Т)·Fвоз.
3.2 Mathematical model of control object and elements
To construct a linear dynamic model of the control object is enough to have its representative acceleration capabilities, both in the control magnitude and disturbing. These characteristics are taken separately by a step change in the small percentage of the face value effects facility operating at rated speed and measure changes the controlled quantity over time.
We analyze the available technology data. Warm-up time empty
the furnace, with an increase in supply of coolant to 7000 m3/h to about 10,000 cubic meters/hour, is 400 seconds. A change in the coolant flow from 8000 to 10000 m3/h with increasing feed concentrate first component 1 t/hour (which is the minimum value of the technology load when the exhaust gas temperature is 60 °C), the characteristic time of temperature change is about 100 sec.
The oven can be approximately modeled in the dynamics of the aperiodic links. And the constant time it should reach a third of the typical temperature change time. It makes sense to assume control over the object inertia. Indeed, if the reality of the oven will have a lower inertia, it will worsen the quality of some indicators of steady state, that can be corrected by adjusting work, but the CAP is insured against loss of stability, and it is for such a serious matter object. Now, consider the control channel furnace (feed gas – exhaust gas temperature) aperiodic element with a time constant of 90 seconds.
The gains of dynamic links can be obtained by dividing the final increment of the exhaust gases by an amount small increments of temperature or feed gas flow rate of the concentrate, for gains and link by the perturbation control, respectively. Namely, for the nominal mode, with parameters for heating medium flow 8000 m3/h and concentrate supply 2 tons/hour:
T, C° = ΔFheat·Ktask-ΔFheat·Kdist
or

The linearized dynamic characteristics of the furnace operated at rated speed, the control channel, the transfer function is given by:

The expression for the transfer function of the furnace in the perturbation can be written as:

Driving simulation of the control object on the exhaust gas temperature is shown in Fig. 3.1.
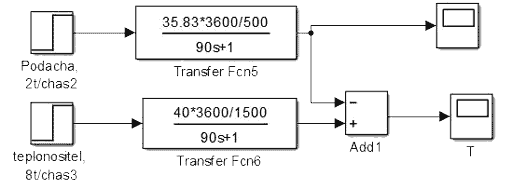
Figure 3.1 - Block diagram of the linear model of furnacep>
We model the given scheme. Transient Response of OC, flue gas temperature is shown in Figure 3.2.
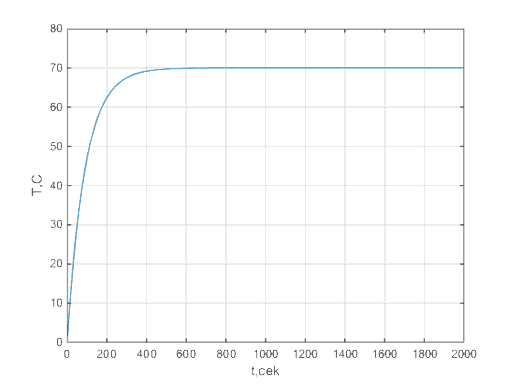
Figure 3.2 - Transitional flue gas temperature characteristic of the output of the BL furnace
Fig. 3.3 shows the transition characteristics when temperature decreases from the concentrate feed 2 t/h and 1.5 t/h at time 750s. The graph shows that that the exhaust gas temperature increased to 90°C. At time 1400 feed control action – the coolant flow rate is reduced by 800m3/hour to compensate for the reduction of concentrate feed, thereby restoring the temperature to the desired level of 70 °C.

Thus, the graph showing the behavior of OC in the dynamics proves the consistency of the model, which will be used in the ACS.
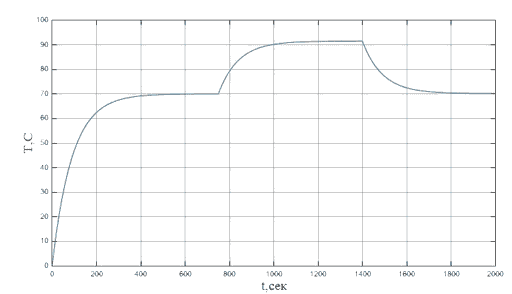
Figure 3.3 - Transition flue gas temperature characteristic of the output of the BL furnace
Also not unimportant system response to disturbance and compensation. As the impact of acts of raw feed into the BL furnace. The system should be qualitatively react to this outrage, and also prevent the quality of the output of the system set parameters. [6]
Conclusions
A linear dynamic model of the drying process in the BL furnace, which is the inertial object and the mathematical model of the actuator, which takes into account the real technological constraints on the control channel and the disturbance in the input and output signals.
The simulation results prove the efficiency of the SAR and the possibility of use of the systems developed under the conditions of drying in the BL furnace. Key regulatory quality indicators correspond to the TT:
- aperiodic transient with acceptable overshoot of 15%;
- settling time (control) for 15 minutes;
- the time of processing of the external perturbation 8 minutes.
- Беспалов А. В., Харитонов Н. И. Системы управления химико-технологическими процессами. Учебное пособие для вузов. – М.:Академкнига, 2007 – C. 690.
- Беспалов А. В., Харитонов Н. И. Задачник по системам управления химико-технологическими процессами. Учебное пособие для вузов. – М.:Академкнига, 2007 – C. 690.
- Дорф Р., Бишоп Р. Современные системы управления. – М.: Лаборатория Базовых Знаний. – 2002 – C. 832.
- Лукас В. А. Теория управления техническими системами. Учебный курс для вузов. Екатеринбург: Издательство УГГГА, 2002. – C. 675.
- Филлипс Ч., Харбор Р. Системы управления с обратной связью. – М.: Лаборатория Базовых Знаний, 2001 – C. 616.
- Денисенко В. ПИД – регуляторы: принципы построения и модификации. Статья, C. 8