Реферат за темою випускної роботи
Зміст
- Вступ
- 1. Актуальність теми та постановка завдань
- 2. Розробка математичної моделі і моделювання системи управління
- 3. Технічна реалізація системи управління
- Висновки
- Перелік посилань
Вступ
Сучасні хіміко-технологічні процеси відрізняються складністю і великою швидкістю протікання, а також чутливістю до відхилення режимних параметрів від нормальних. Відхилення параметрів процесу від жорстко заданих норм може призвести не тільки до втрати якості готової продукції, псування сировини, допоміжних речовин (наприклад, каталізаторів), але і до аварійної ситуації, включаючи пожежі, вибухи, викиди великої кількості шкідливих речовин у навколишнє середовище. Одним із завдань, які стоять перед кожним виробництвом, є неухильне підвищення якості продукції, вдосконалення технології виробництва, а також підвищення надійності та безпеки обладнання і засобів управління.
1. Актуальність теми та постановка завдань
Аміак відноситься до числа важливих продуктів хімічної промисловості, щорічне його світове виробництво досягає 150 млн. тонн. В основному аміак використовується для виробництва азотних добрив (нітрат та сульфат амонію), вибухових речовин і полімерів, азотної кислоти, соди та інших продуктів хімічної промисловості.
Сучасний процес отримання аміаку заснований на його синтезі з азоту і водню при температурах 380–450 ℃ і тиску 320 атм, з використанням залізного каталізатора. Він являє собою складне виробництво в межах кількох блоків, тому у даній роботі буде розглядатися лише одна з його важливих частин – отримання аміаку в реакторі (колоні синтезу).
Технологічна схема синтезу аміаку представлена на рис 1.1.

Рисунок 1.1 – Технологічна схема синтезу аміаку в колоні.
На рис. 1.1 введені наступні позначення:
- Колона синтезу аміаку;
- Водяний холодильник;
- Теплообмінник;
- Повітряний холодильник;
- Сепаратор;
- Збірник холодильник;
- Циркуляційний компресор;
- Конденсаційна колона;
- Випарник.
Колони синтезу аміаку є основними і найбільш складними апаратами установок синтезу. Від правильного вибору конструкції, визначення розмірів і вибору режиму експлуатації колони залежить її продуктивність, стабільність роботи і тривалість експлуатації.[5]
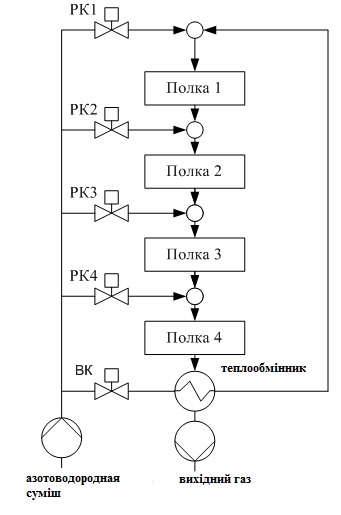
Рисунок 1.2 – Схематичне уявлення четырехполочной колони синтезу аміаку .
На рис. 1.2 введені наступні позначення: 1 – люк для вивантаження каталізатора; 2 – центральна труба; 3 – корпус катализаторной коробки; 4 – термопарный чохол; 5 – завантажувальний люк; 6 – теплообмінник; 7, 9, 11, 13 – введення байпасного газу; 8, 10, 12, 14 – катализаторные шари; 15 – корпус колони; РК1,..., РК4 – регулюючі клапани; ВК – впускний клапан.
У катализаторной зоні азотоводородная суміш послідовно проходить чотири шару каталізатора, на яких відбувається утворення аміаку. Реакція синтезу аміаку супроводжується зменшенням об’єму газової суміші і протікає з виділенням великої кількості теплоти, максимально допустима температура по шарах каталізатора повинні бути в межах 390–525 ℃. Після четвертого шару каталізатора газова суміш при температурі 500–515 ℃ піднімається центральної труби 2, проходить по трубках теплообмінника 6, охолоджуючись при цьому до 325–335 ℃, і виходить з колони. Температура після четвертого шару каталізатора не повинна перевищувати 535 ℃.
Процес синтезу аміаку являє собою многосвязный об’єкт управління за наявності збурень.[4]
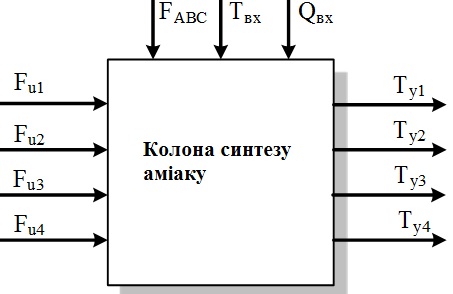
Рисунок 1.3 – Подання четир`йохполочной колони синтезу аміаку як об’єкта управління.
На рис. 1.3 прийняті наступні позначення: FABC, Qвх, Твх – витрата, концентрація і температура вхідний азотоводородной суміші відповідно; Fu1 – Fu4 - витрата холодного байпасного газу; Ty1 – Ty4 – температура в шарах каталізатора.
Оскільки хімічні реакції в шарах каталізатора протікає тривалий час, то об’єкт управління можна віднести до класу об’єктів з транспортним запізнюванням. Отже, при проектуванні системи управління необхідно враховувати цю особливість і застосувати відповідні методики синтезу регуляторів.
Існуючі системи управління володіють незадовільним якістю регулювання температури в шарах каталізатора, яке знижує продуктивність колони синтезу аміаку через відсутність компенсації зовнішнього збурення концентрації аміаку.
Таким чином сформулюємо мета роботи – збільшення виходу цільового продукту за рахунок модернізації системи автоматичного управління колоною синтезу аміаку, яка дозволить стабілізувати температуру в кожному шарі каталізатора четырехполочного реактора при нерівномірному навантаженні.
Для досягнення даної мети необхідно вирішити наступні завдання:
- Дослідити особливості технологічного процесу синтезу аміаку в колонах.
- Розробити функціональну системи автоматичного керування процесом синтезу аміаку в колоні. Зробити вибір технічних засобів.
- Отримати математичну модель основних елементів системи автоматичного управління синтезу аміаку. Розрахувати параметри регулюючих пристроїв і провести імітаційне моделювання.
2. Розробка математичної моделі і моделювання системи
Оскільки процес синтезу NH3, як і більшість процесів хімічного виробництва є процесом, який протікає тривалий час і характеризується плавно наростаючою кривою розгону з насиченням, то можна описати його у вигляді системи аперіодичних ланок першого порядку з запізненням.
Передатна функція по каналу керування має вигляд:[6,7]

Передатна функція по каналу збурення може бути представлена наступним чином:

де i = 1..4 – номер шару каталізатора на якому вимірюється температура на виході.
Розроблювана система управління колоною синтезу аміаку являє собою сукупність незалежних контурів управління для кожного шару каталізатора.
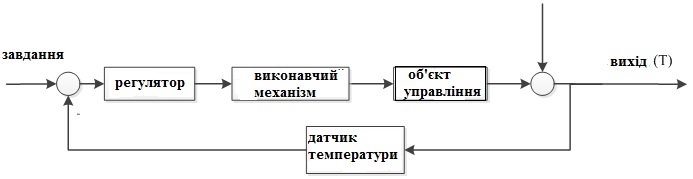
Рисунок 2.1 – Структурна схема управління температурою в i-му шарі каталізатора.[8]
На основі аналізу кривої розгону системи, можна зробити висновок про те, що розроблювана система відноситься до класу систем з транспортним запізнюванням. Відомо, що для таких систем хороших показників по управлінню вдається досягти при використанні спеціальних структур ПІД-регуляторів, що містять так звані «блоки передбачення», які ще називають предикторами Сміта. Таким чином, прийнято рішення використовувати модифікацію ППІ-регулятора (предиктивного ПІ-регулятора), що включає в себе І-регулятор і предиктор Сміта (рис. 2.2).
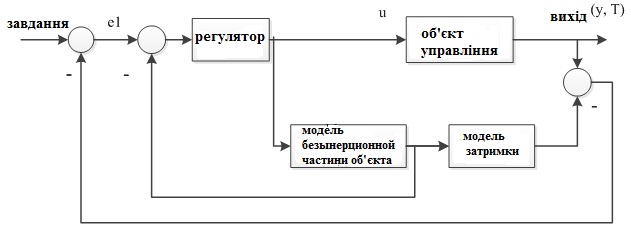
Рисунок 2.2 – Структура системи управління.
На основі структурної схеми та вирази (2.1-2.2) розроблена схема моделювання (рис.2.3).
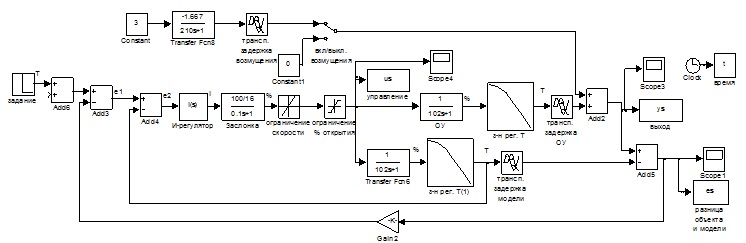
Рисунок 2.3 – Схема моделювання.
При моделюванні прийнято, що вхідним (задає) впливом є температура, яку необхідно підтримувати для протікання реакції і яка є оптимальною для максимального виходу аміаку, – 430 ℃. Результати моделювання наведені на рис. 2.4.
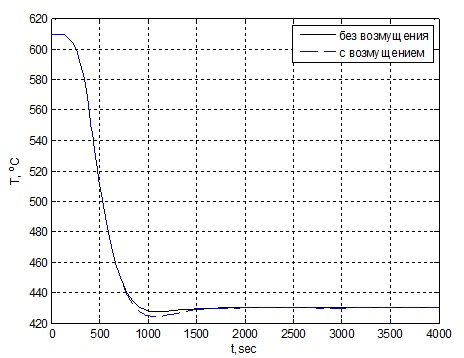
Рисунок 2.4 – Графік зміни температура в першому шарі каталізатора.
Виходячи з отриманих результатів, можна зробити висновок про те, що регулятор дозволяє компенсувати обурення і при цьому показники якості перехідного процесу не виходять за допустимі межі.
3. Технічна реалізація системи управління
Технічні засоби САУ колоною синтезу аміаку повинні розташовуються в приміщенні операторної та експлуатуються в наступних умовах:
• мінімальна температура навколишнього повітря – плюс 5 ℃;
• максимальна температура навколишнього повітря – плюс 40 ℃;
• відносна вологість від 40 до 80 %;
• атмосферний тиск 32 кПа.
Допустима температура по шарах каталізатора:
• температура на першому шарі каталізатора – 420–430 ℃;
• температура на другому шарі каталізатора – 460–465 ℃;
• температура на третьому шарі каталізатора – 480–490 ℃;
• температура на четвертому шарі каталізатора – 500–530 ℃;
Концентрація аміаку у вхідний АВС – не менше 3 % (про.) (це заданий некерований параметр, який можна вважати постійним і незмінним у часі). Концентрація аміаку на виході з колони має бути не менше 12 %.
Для реалізації керуючого пристрою доцільно використовувати промислові контролери. Функції, які повинні виконуватися контролером і засобами автоматичного управління процесом виробництва аміаку:
- Збір і первинна обробка інформації.
- Регулювання температури в шарах каталізатора;
- Сигналізація стану параметрів.
- Виконання процедур автоматичного обміну інформацією між засобами автоматизації.
На підставі перерахованих вимог до складу системи автоматизації колоною синтезу аміаку складена функціональна схема, складу комплексу технічних засобів, наведена на рис. 3.1.
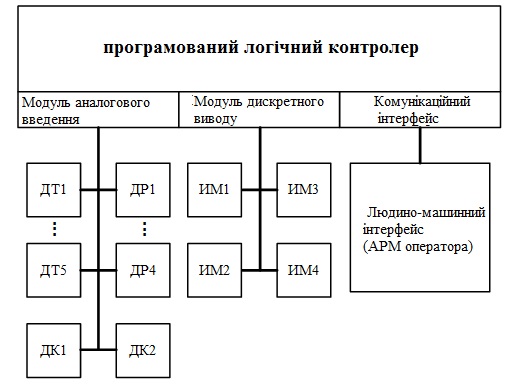
Рисунок 3.1 – Структурна схема процесу одержання аміаку.
На рис. 3.1 прийняті позначення: ДТ1,..., ДТ5 - датчики температури; ДР1,..., ДР4 - датчики витрати газової суміші; ДК1, ДК2 - датчики концентрації аміаку; ИМ1,..., ИМ4 – виконавчі механізми; АРМ – автоматизоване робоче місце.
На підставі ГОСТ 21.404-85 складена функціональна схема системи автоматичного управління колоною синтезу аміаку рис. 3.2.
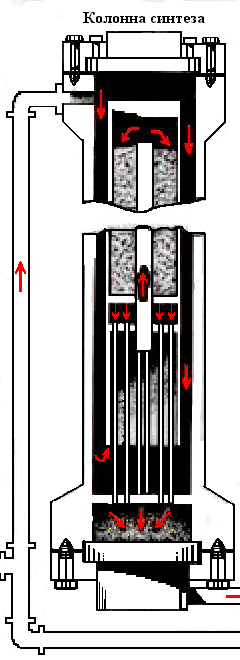
Анимация – Колонна синтеза
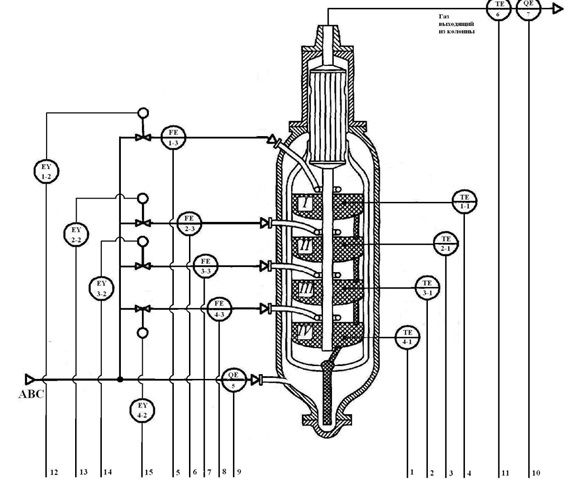
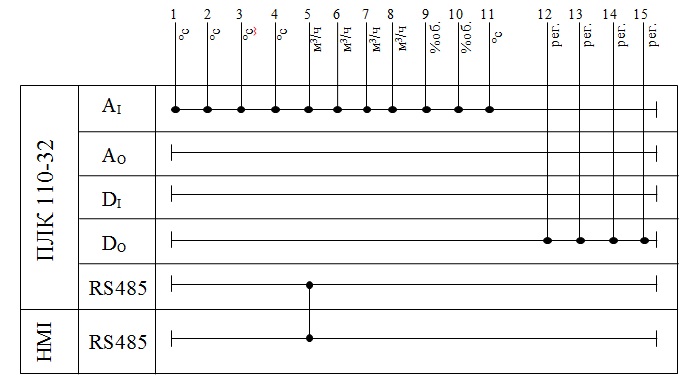
Рисунок 3.2 – Функціональна схема системи управління колоною синтезу.
У колоні синтезу на кожній полиці каталізатора розташовані датчики температури (1-1, 2-1, 3-1, 4-1). На кожному трубопроводі, подаючому холодний байпасний газ в колону синтезу, розташований датчик расходасмеси (1-3, 2-3, 3-3, 4-3). На трубопроводі, подаючому свіжу азотоводородную суміш (АВС), розташований датчик концентрації аміаку (5). На трубопроводі газу, що виходить з колони синтезу, розташовані датчик температури виходить з колони суміші (6) і датчик концентрації аміаку (7). Сигнали з датчиків температури, витрати суміші і датчиків концентрації надходять на аналогові входи програмованого логічного контролера (ПЛК). Відхилення параметрів від норми сигналізується на екрані комп’ютера оператора КИПиА.
З цифрових виходів ПЛК подаються сигнали на електромеханічні перетворювачі (1-2, 2-2, 3-2, 4-2), які розташовані на кожному виконавчому механізмі (заслінці) трубопроводу подачі холодного байпасного газу.
Зробимо вибір комплексу технічних засобів:
- Датчики температури.
В якості датчиків температури масових потоків в колоні застосуємо датчик компанії ОВЕН ДТПL015-0110.250 – термопара
хромель-копель
, матеріал захисної арматури – сталь 12Х18Н10Т з діапазоном вимірювання температури від −200 до +600 ℃, з ізольованим робочим спаем, діаметром термоелектроду 0,7 мм, з металевою комутаційної голівкою, довжина монтажної частини 250 мм, в корпусі 015.Рисунок 3.3 – Конструктивне виконання термопари 015.
Оскільки потрібно забезпечити вихідний сигнал від датчиків температури в уніфікованій формі (сигнала постоянного тока 4…20 мА) (сигналу постійного струму 4...20 мА) застосуємо перетворювач ОВЕН НПТ-2.14.1.2 з діапазоном перетворення
0…+600 ℃
і типом номінальної статичної характеристики ТПL(ГК) хромель-крапель. - Датчики витрати.
В якості датчиків витрати масових витрат у колоні застосуємо витратомір Метран-150RFA (метод вимірювання витрати – перепад тиску з використанням осредняющей напірної трубки Annubar 485). Вихідний сигнал 4-20 мА відповідає поточним значенням перепаду тиску або значенням пропорційного витрати (корінь квадратний з перепаду тиску).
Рисунок 3.4 – Схема зовнішніх електричних з’єднань і габаритні розміри витратоміра Метран-150RFA
- Датчики концентрації.
Виберемо стаціонарний газоаналитический датчик OLCT 100 XP HT – високотемпературне пристрій у вибухозахищеному виконанні, призначена для контролю вибухонебезпечних газів (у тому числі аміаку) температурою не більше 300 ℃.
Рисунок 3.5 – Вигляд датчика OLCT 100 XP HT.
- Виконавчі механізми.
В якості виконавчих механізмів, керуючих витратою газу в полки каталізатора застосуємо однооборотні електричні фланцеві (МЕОФ) виконавчі механізми, що забезпечують передачу крутного моменту на робочий орган арматури неполноповоротного принципу дії.
При цьому виготовлення та постачання підлягає МЕОФ-100/10-0,25 У-Б – механізм электроисполнительный однооборотный фланцевий з номінальним значенням моменту на вихідному валу 100 Нм, з номінальним значенням часу повного ходу 10 з номінальним значенням повного ходу 0,25 про., з струмовим блоком сигналізації положення вихідного органу, з струмовим датчиком і вбудованим блоком живлення.
Рисунок 3.6 – Ввигляд МЕОФ.
- Промисловий контролер.
Застосовується промисловий контролер ОВЕН ПЛК110-220.30.Р-М.
Рисунок 3.7 – Зовнішній вигляд контролера ОВЕН ПЛК110-220.30.Р-М.
Контролер ПЛК110 призначений для створення систем автоматизованого управління технологічними процесами в різних галузях промисловості.
Можливий варіант структури сполук контролера при його роботі в автоматичній системі керування технологічними процесами показаний на рисунку 3.8.
Рисунок 3.8 – Приклад структури сполук при використання ПЛК в системі управління.
Оскільки необхідно підключення до контролера 11-ти аналогових датчиків необхідно вибрати аналоговий модуль вводу. В якості такого застосуємо 2 модуля швидкісного введення (8-ми канальний) аналогових сигналів ОВЕН МВ110-220.8 АС, з напругою живлення 220 В змінного струму частотою від 47 до 63 Гц.
- Людино-машинний інтерфейс.
Для організації людино-машинного інтерфейсу застосуємо панель оператора з сенсорним екраном ОВЕН СП107. Вона дозволяє відображати на екрані хід виконання технологічного процесу і редагувати значення параметрів, що відповідають за функціонування системи. Володіє розвиненими інтерфейсами зв’язку.
Рисунок 3.9 – Зовнішній вигляд і схема зовнішніх електричних з’єднань панелі ОВЕН СП107.
Висновки
Технологічний процес виробництва аміаку в колонах проаналізований з точки зору об’єкту управління, виявлено вхідні, вихідні та збурюючи параметри.
На основі аналізу існуючих структур систем управління і контролю спорідненими об’єктами, обрана багаторівнева децентралізована структура побудови системи управління колоною синтезу аміаку, що дозволяє забезпечити ефективність роботи, знизити відносну вартість системи управління, підвищити її надійність і ремонтопридатність.
Розроблена модель системи управління процесом синтезу аміаку на прикладі першої полиці каталізатора четырехполочной колони синтезу аміаку. Отримані в результаті моделювання перехідні процеси підтверджують відповідність розрахункових і експериментальних даних і, отже, адекватність моделі.
Зроблений вибір технічних засобів САУ колоною синтезу аміаку обумовлений перспективою розвитку обраних технічних засобів, можливістю зв’язку з існуючою обчислювальною технікою, забезпеченням необхідних метрологічних вимог.
Перелік посилань
- Автоматические приборы, регуляторы и вычислительные системы. Под ред. Б. Д. Кошарского. – Л.: Машинобудування, 1976 – 488 С.
- Бесекерский В. А. Теория систем автоматического регулирования / В. А. Бесекерский, Е. П. Попов – К.: Наука, 1975. – 766 С.
- Дорф Р., Бишоп Р. Современные системы управления: Пер. с англ. Б. И. Копылова. – М.: Лаборатория Базовых Знаний, 2004. – 832 С.
- Клюев А. С. Проектирование систем автоматизации технологических процессов / А. С. Клюев, Б. В. Глазов, А. Х. Дубровский. – М.: Энергия, 1980. – 345 С.
- Сердюк Ю. А. Сетевые технологии как составная часть интегрированных систем управления промышленных предприятий / Ю. А. Сердюк, А. В. Ловейкин // Промышленные измерения, контроль, автоматизация, диагностика. – 2003. – №3-4. – С. 10–13.
- Теоретические основы и технология синтеза аммиака. – под редакцией А. М. Николаева – Киев: Вища школа, 1969 – 256 С.
- Филлипс Ч. Системы управления с обратной связью / Ч. Филлипс, Р. Харбор. – М.: Лаборатория базовых знаний, 2001. – 616 С.
- Штейнберг Ш. Е. Адаптация стандартных регуляторов к условиям эксплуатации в промышленных системах регулирования / Ш. Е. Штейнберг, И. Е. Залуцкий // Промышленные АСУ и контроллеры. – 2003. – №4. – С. 11–14.