Реферат по теме выпускной работы
Содержание
- Введение
- 1. Актуальность темы и постановка задач
- 2. Разработка математической модели и моделирование системы управления
- 3. Техническая реализация системы управления
- Выводы
- Список источников
Введение
Современные химико-технологические процессы отличаются сложностью и большой скоростью протекания, а также чувствительностью к отклонению режимных параметров от нормальных. Отклонение параметров процесса от жестко заданных норм может привести не только к потере качества готовой продукции, порче сырья, вспомогательных веществ (например, катализаторов), но и к аварийной ситуации, включая пожары, взрывы, выбросы большого количества вредных веществ в окружающую среду. Одним из заданий, которые стоят перед каждым производством, является неуклонное повышение качества продукции, совершенствования технологии производства, а также повышения надежности и безопасности оборудования и средств управления.[1,3]
1. Актуальность темы и постановка задач
Аммиак относится к числу важных продуктов химической промышленности, ежегодное его мировое производство достигает 150 млн. тонн. В основном аммиак используется для производства азотных удобрений (нитрат и сульфат аммония), взрывчатых веществ и полимеров, азотной кислоты, соды и других продуктов химической промышленности.
Современный процесс получения аммиака основан на его синтезе из азота и водорода при температурах 380–450 ℃ и давлении 320 атм, с использованием железного катализатора. Он представляет собой сложное производство в рамках нескольких блоков, поэтому в данной работе будет рассматриваться только лишь одна из его важных частей – получение аммиака в реакторе (колоне синтеза).
Технологическая схема синтеза аммиака представлена на рис 1.1.
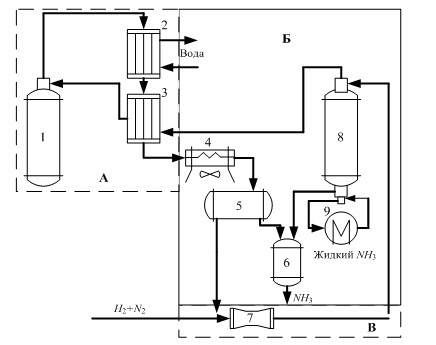
Рисунок 1.1 – Технологическая схема синтеза аммиака в колонне.
На рис. 1.1 введены следующие обозначения:
- Колонна синтеза аммиака;
- Водяной холодильник;
- Теплообменник;
- Воздушный холодильник;
- Сепаратор;
- Сборник холодильник;
- Циркуляционный компрессор;
- Конденсационная колонна;
- Испаритель.
Колонны синтеза аммиака являются основными и наиболее сложными аппаратами установок синтеза. От правильного выбора конструкции, определения размеров и выбора режима эксплуатации колонны зависит ее производительность, стабильность работы и длительность эксплуатации.[5]
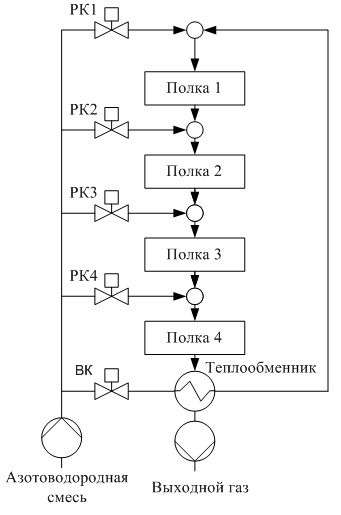
Рисунок 1.2 – Схематичное представление четырехполочной колонны синтеза аммиака.
На рис. 1.2 введены следующие обозначения: 1 – люк для выгрузки катализатора; 2 – центральная труба; 3 – корпус катализаторной коробки; 4 – термопарный чехол; 5 – загрузочный люк; 6 – теплообменник; 7, 9, 11, 13 – ввод байпасного газа; 8, 10, 12, 14 – катализаторные слои; 15 – корпус колонны; РК1,…, РК4 – регулирующие клапаны; ВК – впускной клапан.
В катализаторной зоне азотоводородная смесь последовательно проходит четыре слоя катализатора, на которых происходит образование аммиака. Реакция синтеза аммиака сопровождается уменьшением объему газовой смеси и протекает с выделением большого количества теплоты, максимально допустимая температура по слоям катализатора должны быть в пределах 390–525 ℃. После четвертого слоя катализатора газовая смесь при температуре 500-515℃ поднимается по центральной трубе 2, проходит по трубкам теплообменника 6, охлаждаясь при этом до 325–335 ℃, и выходит из колонны. Температура после четвертого слоя катализатора не должна превышать 535 ℃.
Процесс синтеза аммиака представляет собой многосвязный объект управления при наличии возмущений.[4]
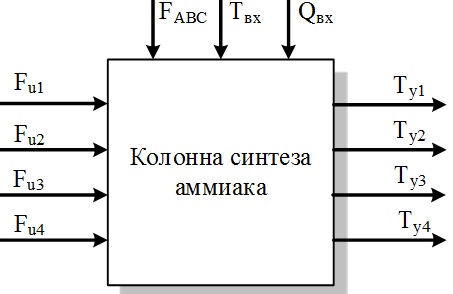
Рисунок 1.3 – Представление четырехполочной колонны синтеза аммиака как объекта управления.
На рис. 1.3 приняты следующие обозначения: FABC, Qвх, Tвх – расход, концентрация аммиака и температура входной азотоводородной смеси соответственно; Fu1 – Fu4 – расход холодного байпасного газа; Ty1 – Ty4 – температура в слоях катализатора.
Поскольку химические реакции в слоях катализатора протекают длительное время, то объект управления можно отнести к классу объектов с транспортным запаздыванием. Следовательно, при проектировании системы управления необходимо учитывать эту особенность и применить соответствующие методики синтеза регуляторов.
Существующие системы управления обладают неудовлетворительным качеством регулирования температуры в слоях катализатора, которое снижает производительность колонны синтеза аммиака из-за отсутствия компенсации внешнего возмущения по концентрации аммиака.
Таким образом сформулируем цель работы – увеличение выхода целевого продукта за счет модернизации системы автоматического управления колонной синтеза аммиака, которая позволит стабилизировать температуру в каждом слое катализатора четырехполочного реактора при неравномерной нагрузке.
Для достижения данной цели необходимо решить следующие задачи:
- Исследовать особенности технологического процесса синтеза аммиака в колоннах.
- Разработать функциональную системы автоматического управления процессом синтеза аммиака в колонне. Произвести выбор технических средств.
- Получить математическую модель основных элементов системы автоматического управления синтеза аммиака. Рассчитать параметры регулирующих устройств и провести имитационное моделирование.
2. Разработка математической модели и моделирование системы управления
Поскольку процесс синтеза NH3, как и большинство процессов химического производства, является процессом, который протекает длительное время и характеризуется плавно нарастающей кривой разгона с насыщением, то можно описать его в виде системы апериодических звеньев первого порядка с опозданием.
Передаточная функция по каналу управления имеет вид:[6,7]

Передаточная функция по каналу возмущения может быть представлена следующим образом:

где i = 1..4 – номер слоя катализатора на котором измеряется температура на выходе.
Разрабатываемая система управления колонной синтеза аммиака представляет собой совокупность независимых контуров управления для каждого слоя катализатора.
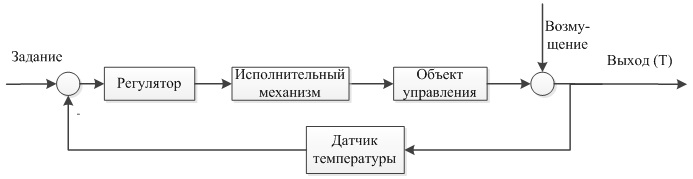
Рисунок 2.1 – Структурная схема управления температурой в i-м слое катализатора.[8]
На основе анализа кривой разгона системы, можно сделать вывод о том, что разрабатываемая система относится к классу систем с транспортным запаздыванием.
Известно, что для таких систем хороших показателей по управлению удается достичь при использовании специальных структур ПИД-регуляторов, содержащих так называемые
блоки предсказания
, которые еще называют предикторами Смита. Таким образом, принято решение использовать модификацию ППИ-регулятора (предиктивного ПИ-регулятора),
включающую в себя И-регулятор и предиктор Смита (рис. 2.2).
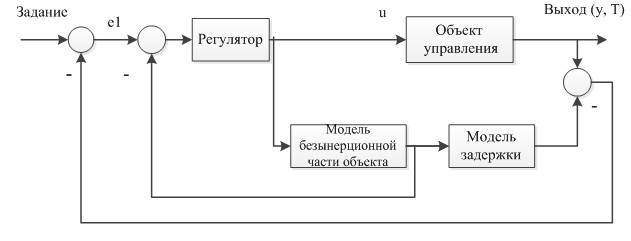
Рисунок 2.2 – Структура системы управления.
На основе структурной схемы и выражений (2.1-2.2) разработанная схема моделирования (рис.2.3).
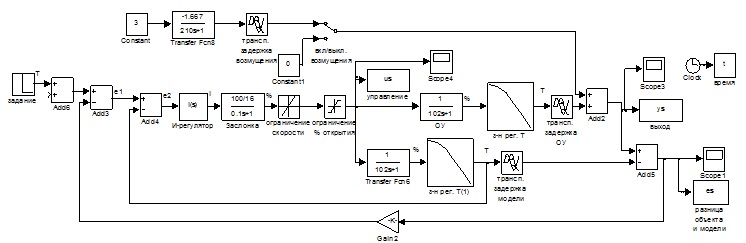
Рисунок 2.3 – Схема моделирования.
При моделировании принято, что входным (задающим) воздействием является температура, которую необходимо поддерживать для протекания реакции и которая является оптимальной для максимального выхода аммиака, −430 ℃. Результаты моделирования приведены на рис. 2.4.
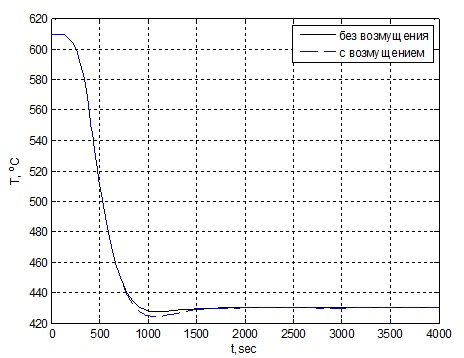
Рисунок 2.4 – График изменения температура в первом слое катализатора.
Исходя из полученных результатов, можно сделать вывод о том, что регулятор позволяет компенсировать возмущение и при этом показатели качества переходного процесса не выходят за допустимые пределы.
3. Техническая реализация системы управления
Технические средства САУ колонной синтеза аммиака должны располагаются в помещении операторной и эксплуатируются в следующих условиях:
• минимальная температура окружающего воздуха – плюс 5 ℃;
• максимальная температура окружающего воздуха – плюс 40 ℃;
• относительная влажность от 40 до 80 %;
• атмосферное давление 32 кПа.
Допустимая температура по слоям катализатора:
• температура на первом слое катализатора – 420–430 ℃;
• температура на втором слое катализатора – 460–465 ℃;
• температура на третьем слое катализатора – 480–490 ℃;
• температура на четвертом слое катализатора – 500–530 ℃;
Концентрация аммиака во входной АВС – не меньше 3 % (об.) (это заданный неуправляемый параметр, который можно считать постоянным и неизменным во времени). Концентрация аммиака на выходе из колонны должна быть не менее 12 %.
Для реализации управляющего устройства целесообразно использовать промышленные контроллеры. Функции, которые должны выполняться контролером и средствами автоматического управления процессом производства аммиака:
- Сбор и первичная обработка информации.
- Регулирование температуры в слоях катализатора;
- Сигнализация состояния параметров.
- Выполнение процедур автоматического обмена информацией между средствами автоматизации.
На основании перечисленных требований к составу системы автоматизации колонной синтеза аммиака составлена функциональная схема, состава комплекса технических средств, приведенная на рис. 3.1.
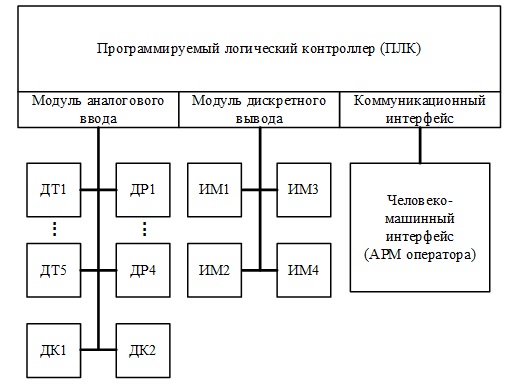
Рисунок 3.1 – Структурная схема процесса получения аммиака.
На рис. 3.1 принятые обозначения: ДТ1,…, ДТ5 – датчики температуры; ДР1,…,ДР4 - датчики расхода газовой смеси; ДК1, ДК2 – датчики концентрации аммиака; ИМ1,…, ИМ4 – исполнительные механизмы; АРМ – автоматизированное рабочее место.
На основании ГОСТ 21.404-85 составлена функциональная схема системы автоматического управления колонной синтеза аммиака рис. 3.2.
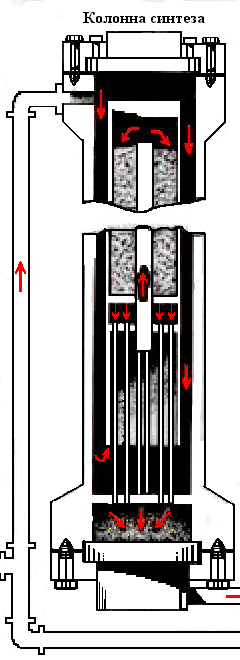
Анимация – Колонна синтеза
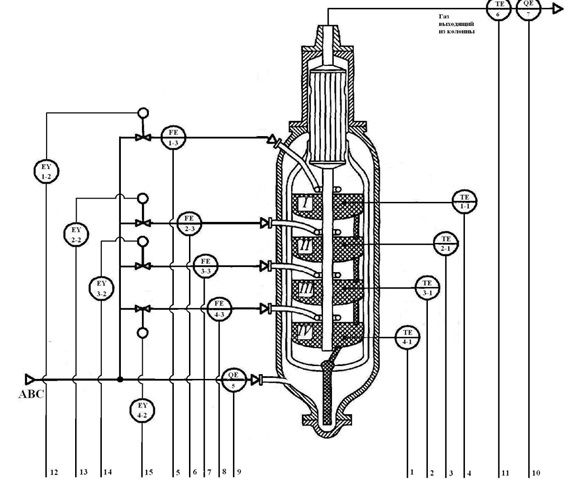
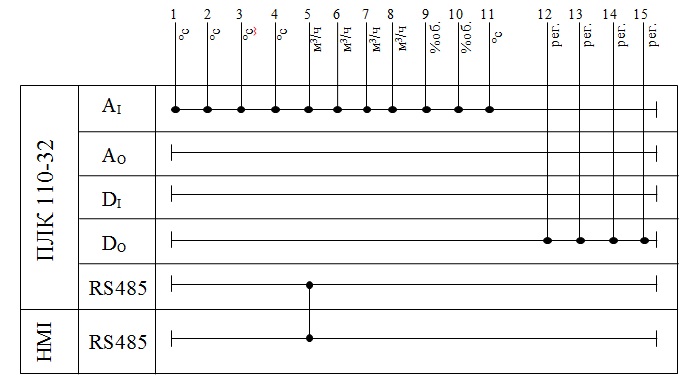
Рисунок 3.2 – Функциональная схема системы управления колонной синтеза.
В колонне синтеза на каждой полке катализатора расположенные датчики температуры (1-1, 2-1, 3-1, 4-1). На каждом трубопроводе, подающем холодный байпасный газ в колонну синтеза, расположен датчик расходасмеси (1-3, 2-3, 3-3, 4-3). На трубопроводе, подающем свежую азотоводородную смесь (АВС), расположен датчик концентрации аммиака (5). На трубопроводе газа, выходящего из колонны синтеза, расположены датчик температуры выходящей из колонны смеси (6) и датчик концентрации аммиака (7). Сигналы с датчиков температуры, расхода смеси и датчиков концентрации поступают на аналоговые входы программируемого логического контролера (ПЛК). Отклонение параметров от нормы сигнализируется на экране компьютера оператора КИПиА.
С цифровых выходов ПЛК подаются сигналы на электромеханические преобразователи (1-2, 2-2, 3-2, 4-2), которые расположены на каждом исполнительном механизме (заслонке) трубопровода подачи холодного байпасного газа.
Произведем выбор комплекса технических средств:
- Датчики температуры.
В качестве датчиков температуры массовых потоков в колонне применим датчик компании ОВЕН ДТПL015-0110.250 – термопара
хромель-копель
, материал защитной арматуры – сталь 12Х18Н10Т с диапазоном измерения температуры от -200 до +600 ℃, с изолированным рабочим спаем, диаметром термоэлектрода 0,7 мм, с металлической коммутационной головкой, длиной монтажной части 250 мм, в корпусе 015.Рисунок 3.3 – Конструктивное исполнение термопары 015.
Поскольку нужно обеспечить выходной сигнал от датчиков температуры в унифицированной форме (сигнала постоянного тока 4…20 мА) применим преобразователь ОВЕН НПТ-2.14.1.2 с диапазоном преобразования
0…+600 ℃
и типом номинальной статической характеристики ТПL(ХK) хромель-капель. - Датчики расхода.
В качестве датчиков расхода массовых расходов в колонне применим расходомер Метран-150RFA (метод измерения расхода – перепад давления с использованием осредняющей напорной трубки Annubar 485). Выходной сигнал 4-20 мА соответствует текущему значению перепада давления или значению пропорциональному расходу (корень квадратный из перепада давления).
Рисунок 3.4 – Схема внешних электрических соединений и габаритные размеры расходомера Метран-150RFA.
- Датчики концентрации.
Выберем стационарный газоаналитический датчик OLCT 100 XP HT – высокотемпературное устройство во взрывозащищённом исполнении, предназначенное для контроля взрывоопасных газов (в том числе аммиака) температурой не более 300 ℃.
Рисунок 3.5 – Внешний вид датчика OLCT 100 XP HT.
- Исполнительные механизмы.
В качестве исполнительных механизмов, управляющих расходом газа в полки катализатора применим однооборотные электрические фланцевые (МЭОФ) исполнительные механизмы, обеспечивающие передачу крутящего момента на рабочий орган арматуры неполноповоротного принципа действия.
При этом изготовлению и поставке подлежит МЭОФ-100/10-0,25У-Б – механизм электроисполнительный однооборотный фланцевый с номинальным значением момента на выходном валу 100 Нм, с номинальным значением времени полного хода 10 с, номинальным значением полного хода 0,25 об., с токовым блоком сигнализации положения выходного органа, с токовым датчиком и встроенным блоком питания.
Рисунок 3.6 – Внешний вид МЭОФ.
- Промышленный контроллер.
Применим промышленный контроллер ОВЕН ПЛК110-220.30.Р-М.
Рисунок 3.7 – Внешний вид контроллера ОВЕН ПЛК110-220.30.Р-М.
Контроллер ПЛК110 предназначен для создания систем автоматизированного управления технологическими процессами в различных областях промышленности.
Возможный вариант структуры соединений контроллера при его работе в автоматической системе управления технологическими процессами показан на рисунке 3.8.
Рисунок 3.8 – Пример структуры соединений при использования ПЛК в системе управления.
Поскольку необходимо подключение к контроллеру 11-ти аналоговых датчиков необходимо выбрать аналоговый модуль ввода. В качестве такового применим 2 модуля скоростного ввода (8-ми канальный) аналоговых сигналов ОВЕН МВ110-220.8АС, с напряжением питания 220 В переменного тока частотой от 47 до 63 Гц.
- Человеко-машинный интерфейс.
Для организации человеко-машинного интерфейса применим панель оператора с сенсорным экраном ОВЕН СП107. Она позволяет отображать на экране ход выполнения технологического процесса и редактировать значения параметров, отвечающих за функционирование системы. Обладает развитыми интерфейсами связи.
Рисунок 3.9 – Внешний вид и схема внешних электрических соединений панели ОВЕН СП107.
Выводы
Технологический процесс производства аммиака в колоннах проанализирован с точки зрения объекта управления, выявлены входные, выходные и возмущающие параметры.
На основе анализа существующих структур систем управления и контроля родственными объектами, выбрана многоуровневая децентрализованная структура построения системы управления колонной синтеза аммиака, позволяющая обеспечить эффективность работы, снизить относительную стоимость системы управления, повысить ее надежность и ремонтопригодность.
Разработанная модель системы управления процессом синтеза аммиака на примере первой полки катализатора четырехполочной колонны синтеза аммиака. Полученные в результате моделирования переходные процессы подтверждают соответствие расчетных и экспериментальных данных и, следовательно, адекватность модели.
Произведен выбор технических средств САУ колонной синтеза аммиака обусловлен перспективой развития выбранных технических средств, возможностью связи с существующей вычислительной техникой, обеспечением необходимых метрологических требований.
Список источников
- Автоматические приборы, регуляторы и вычислительные системы. Под ред. Б. Д. Кошарского. – Л.: Машинобудування, 1976 – 488 С.
- Бесекерский В. А. Теория систем автоматического регулирования / В. А. Бесекерский, Е. П. Попов – К.: Наука, 1975. – 766 С.
- Дорф Р., Бишоп Р. Современные системы управления: Пер. с англ. Б. И. Копылова. – М.: Лаборатория Базовых Знаний, 2004. – 832 С.
- Клюев А. С. Проектирование систем автоматизации технологических процессов / А. С. Клюев, Б. В. Глазов, А. Х. Дубровский. – М.: Энергия, 1980. – 345 С.
- Сердюк Ю. А. Сетевые технологии как составная часть интегрированных систем управления промышленных предприятий / Ю. А. Сердюк, А. В. Ловейкин // Промышленные измерения, контроль, автоматизация, диагностика. – 2003. – №3-4. – С. 10–13.
- Теоретические основы и технология синтеза аммиака. – под редакцией А. М. Николаева – Киев: Вища школа, 1969 – 256 С.
- Филлипс Ч. Системы управления с обратной связью / Ч. Филлипс, Р. Харбор. – М.: Лаборатория базовых знаний, 2001. – 616 С.
- Штейнберг Ш. Е. Адаптация стандартных регуляторов к условиям эксплуатации в промышленных системах регулирования / Ш. Е. Штейнберг, И. Е. Залуцкий // Промышленные АСУ и контроллеры. – 2003. – №4. – С. 11–14.