Abstract
Сontents
- Introduction
- 1. Theme urgency
- 2. Goal and tasks of the research
- 3. Research of kinetics of exhaustion of powder mix for diffusive galvanizing
- Conclusion
- References
Introduction
Galvanizing is the most widespread sheeting on the stalyakh. It is explained by comparative low cost of material and technologies of drawing, and also satisfactory firmness of a covering.
The greatest application is found by technologies of hot and galvanic galvanizing. In the first way process, generally hire, elements of a metalwork: leaf, profiles. Galvanic zinc the wide nomenclature of hardware products, details of electric equipment and other small products.
Shortcomings of the listed technologies are high capital expenditure, existence of the harmful factors making noticeable impact on environment and worsening working conditions.
In this regard the technology of thermal diffusion galvanizing attracts attention. She has the following advantages: low capital expenditure; harmless initial substances and lack of toxic waste; high mechanical and corrosion properties.
The thermal diffusion covering is characterized by a high complex of properties. It is caused by the diffusive nature of a covering, lack of a time, high durability of coupling and hardness. These features in total with phase structure provide the increased corrosion resistance of a covering.
The most widespread is the technology of diffusive galvanizing in powder mixes. At the same time there are two approaches to formation of compositions of powder mixes. According to traditional approach, mix contains a certain amount of zinc powder and, in process of use, is updated fresh [2]. According to the technologies applied by some modern producers (see, for example, [2]) mix is applied once and contains such amount of zinc which is necessary for a covering of the set surface.
1. Theme urgency
An actual task is to achieve composition of powder mix which can be used for galvanizing, without noticeable deterioration of a zinc layer
2. Goal and tasks of the research
A research objective is studying of kinetics of impoverishment of powder mix for diffusive galvanizing.
3. Research of kinetics of exhaustion of powder mix for diffusive galvanizing
Processing of lamellar samples of steel of St 3 was made in the tight container. Used the mix consisting of 50% of zinc powder, 49% of sand and 1% of chloride ammonium. Temperature of processing made 450-470 °C. Duration – 3 hours.
In each experience processed identical quantity of samples with identical distance between them and walls of the container. After each experience mix was carefully mixed for averaging of structure.
The first samples had characteristic light gray color. Since the seventh experience, there is a darkening of a surface and sticking of the thin easily removed crust. Further observed emergence of spotty coloring of a surface decrease in a roughness of a surface was Visually noted.
Since the fifteenth experience, dark sites began to appear, heterogeneity of coloring of a surface has amplified. In process of increase in experiences quantity of dark sites and heterogeneity of coloring I increased. In the last two experiences observed emergence of flowers of a pobezhalost that speaks about the small thickness of a galvanized layer. When cooling air podsasyvatsya inevitably in the container. At the same time thin, with small contents of zinc, layers are painted in colors of a pobezhalost, characteristic of iron.
The diffusion zinc covering consists of usual phase layers: δ1-phases which often has a column structure and contains the cracks which have appeared at production of a shlif and the G-phase.
In process of increase in number of experiences occurs decrease in thickness of a galvanized layer (dr. 1). At the same time there is a change of relative thickness of phases. The microstructure of the first samples is presented mainly δ1 - a phase and a thin layer of the G-phase. In process of increase in frequency rate of use of mix in structure there was a new layer adjoining the G-phase which judging by his morphology is δ1к-фазой. Also, with increase in number of experiences G-phase layer thickness grows.
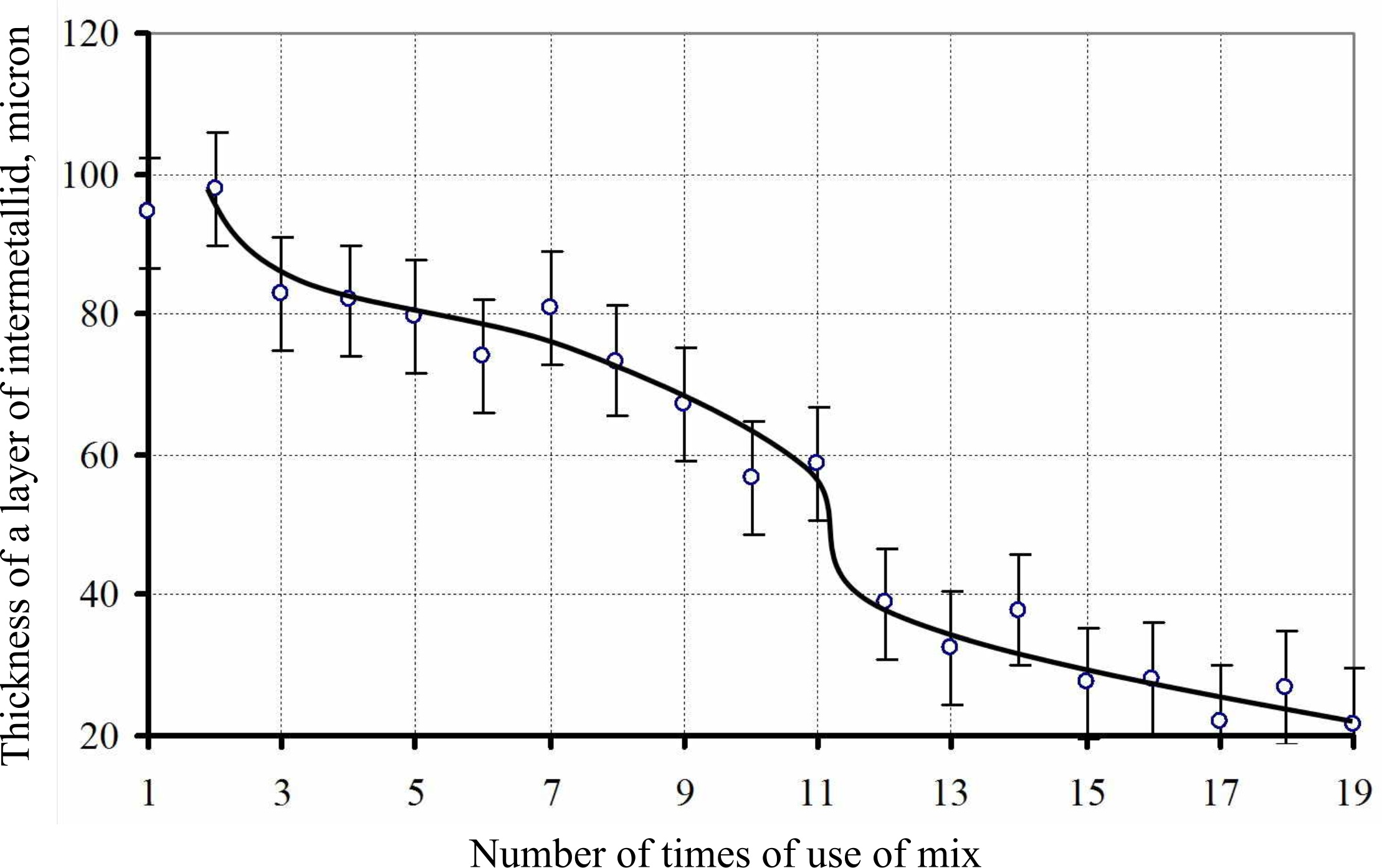
Drawing 1 – The dependence of the intermetallic layer thickness by the use of the powder mixture
In the last two experiences structure of a layer the two-phase and presented by light and dark crystals which alternate, dark crystals form either inclusions, or the dark crystals growing from a substrate to a surface. Perhaps, the dark structural component is the G-phase.
Influence of frequency rate of use of mix on the content of zinc in the intermetallidakh was estimated on the microhardness which measured in the top and lower part of a layer, at distance 1/3 and 2/3 thickness (dr. 2). At the same time microhardness separately δ1к-phases didn't manage to be measured. Microhardness δ1-phases with increase in number of experiences decreases.
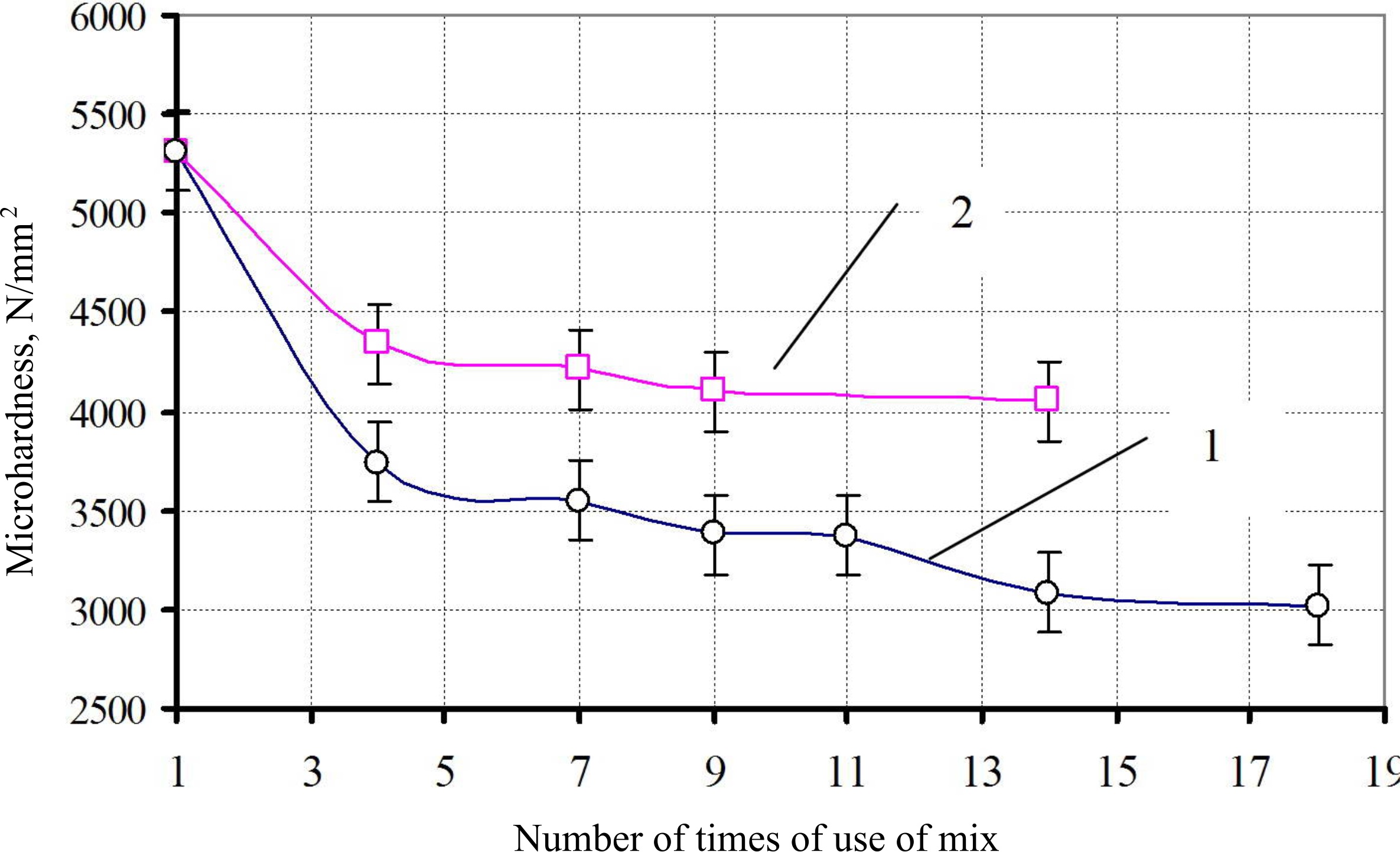
Drawing 2 – Microhardness intermetallic layer of the multiplicity of the mixture
1 – at a distance of 1/3 thickness
2 – at a distance of 2/3 thickness
In the direction from a surface to a core layer microhardness δ1-phases decreases approximately by 20%. It can be connected with the fact that δ1-the phase has variable structure and on a surface the maintenance of Zn above.
Conclusions
Thus, mix with the initial content of zinc of 50% it is possible to use up to 15 times without noticeable deterioration of a layer. These results, in general, confirm the data published in references which also speak about a possibility of use of the same mix during 10-15 experiences [1].
References
- Проскуркин Е.В. Цинкование / Е.В. Проскуркин, В.А. Попович, А.Т. Мороз. – М.: Металлургия, 1988. – 528 с
- Описание технологии ДИСТЕК / DISTeK thermal diffusion technology & equipment. – Режим доступа: http://www.distekgroup.com/distek-ru/htm/process.htm/. – Дата доступа: 12.04.2016. - DiSTeK Technology.