Abstract
Thr content
- Introduction
- 1.Plastic
- 2.Extrusion
- 2.1.Types of extruders
- 2.2.The feedstock for the extruder
- 3.The processing zone of the extruder
- 4.Basic research and results
- Conclusion
- References
Introduction
The plastics industry is developing extremely rapid. Since the 60-ies, production of polymers, mainly plastics, is doubling every 5 years, and the growth rates in accordance with the forecast for the period up to 1990 will continue.
Characteristic is the rapid development in the plastics industry thermoplastic materials, comprising on average about 70 % of the total number of produced plastics. One of the spillover effects of rapid growth of the plastics industry is a simultaneous increase in the amount of plastic waste. So, in Germany they made in 1977 to 1.2 million tons in the US total wastes of polymers in 1980 to 6.4 million t, and in Japan according to the forecast by 1985 will exceed 4.4 million tonnes/year. Formed in England annually about 800 tons of plastic waste, of which about 300 thousand t amount of industrial waste thermoplastics. In Sweden, the only amount of waste from plastics processing more than 11 thousand tons/year. In 1975 in the GDR plastic waste amounted to 30-40 thousand tons, Poland — about 20 thousand t, and in the countries of the CMEA — 200-250 thousand tons[7].
Thus, waste plastics has become a serious source of environmental pollution and most countries strongly intensified work on the creation of efficient processes of recycling or disposal of these wastes. This is largely due to the fact that plastic wastes are increasing the scale of secondary raw materials, which can serve both to produce articles and compositions and as a source of fuel resources. In conditions when the raw material of the petrochemical problems and energy problems are very acute in many countries, a contribution to the solution of these issues may make the use of rational methods of utilization and processing of plastic waste.
Currently, along with the improvement of technology of synthesis and processing of plastics more and more attention is paid to the development of processes and methods of recycling or disposal of plastic waste. It is possible to distinguish the following main directions:
-recycling wastes or using them in various compositions;
-thermal decomposition with receiving of desired products;
-thermal decontamination with regeneration of heat generated of;[6]
1.Plastic
Plastic is an organic material, which are based on synthetic or natural macromolecular compounds (polymers).
Types of plastics and their application are based on what polymers are the basis of natural or synthetic. They are subjected to heat, pressure, and then perform the forming of products of varying complexity. Importantly, these manipulations retained the form of the finished product. All plastics are thermoplastic, that is reversible, and thermosetting (irreversible).
Reversible become plastic under the influence of heat and pressure further, with the dramatic changes in the composition do not occur. Pressed and has become a solid product you can always soften it and give it some form. Such known types of plastics (thermoplastic), such as polyethylene and polystyrene. The first is corrosion resistance and dielectric properties. Based on it to manufacture pipes, films, sheets, it is widely used as insulating material.
Types of plastics commonly used are:
PET - polyethylene terephthalate used in the manufacture of PET bottles and various containers for food and medicine. Resistant to active media, wear-resistant and resistant to temperature extremes from -40 to 750С.
ABS - Acrylonitrile butadiene styrene, which is used most often from the group of thermoplastics. However, it is not the most common. Its excellent properties can not affect the difficulties associated with the printing of this material.
PLA - polyethylene Terephthalate used in the manufacture of PET bottles and various containers for food and medicine. Resistant to active media, wear-resistant and resistant to temperature extremes from -40 to 750С.
At the moment, polymer waste is ivanychem source of pollution of our planet. To date, a large number of such waste be disposed of in landfills or in special landfills, where they decompose 180 – 200 years. And only a small part of them is processed a second time.
2.Extrusion
Extrusion – a method of molding during extrusion of semifinished or finished products of unlimited length forcing the polymer melt through the forming head with the channels of the profile. For this purpose, a screw or worm gear, extruder.
The extruder in which the polymer is melted and homogenized, is the main industrial lines, where a number of interrelated operations of the recycling process. It performs the functions of the kneader and pump continuously pushes the molten material obtained in the helical channel through the head (forming the channel). The device and principle of operation of the primary node, pushes the melt in the head, extruders are divided into the screw, without a screw and combined. The screw machine is also called worm presses. High plastichouse the ability of the worm extruders due to the fact that plasticization occurs as a result of heat transfer from the heated walls of the cylinder (the housing) and heat under deformations which the material is subjected in the extruder[1] .
2.1.Types of extruders
Extruders are divided into one-screw and a twin-screw (the last screw both located in the same cylinder); also known three-screw and four-screw extruders; twin-cylinder or multi-cylinder (each worm is located in a separate cylinder); single - and two-stage, in which the mastication and extrusion material, respectively, is carried out in one or in two stages; universal and specialized; with oscillating (along the axis) and simultaneously rotating a screw; degassing zone and without it, with the rotation of the screws in one and in opposite directions[3].
The extruder consists of a hopper, which receives the granules of the plastic through the screw moves the casing to the heater, which melts data plastic granules. Due to the fact that the temperature of the heater 100°-180°C plastic does not decompose, and no toxic emissions, which come from the decomposition. The product is placed on the matrix where it is evenly distributed and goes through the head of the extruder. After the product exited the extruder it goes on coil winding the finished yarn. The thickness of the finished yarn depends on the diameter of the nozzle installed on the extruder. In order that the thread has cooled down after its exit from the extruder, set the fan to blowing air cools the filament[1] .The scheme of the extruder are presented in(Fig. 1).
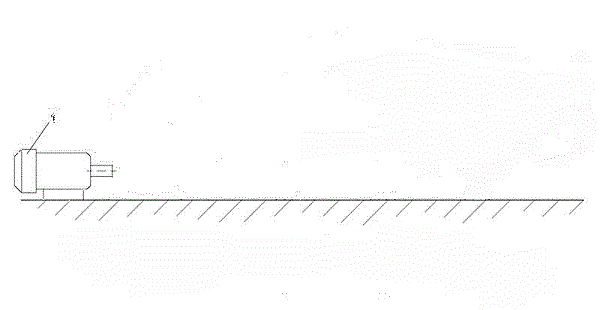
Figure
1. 1- electromotor, 2-
reduction gear, 3- bearing unit, 4- boot device, 5- casing, 6- heating
element, 7- auger, 8- extrusion head.
2.2.The feedstock for the extruder
The feedstock for extrusion, is fed to the hopper may be in the form of powder, granules, strips. The latter type of materials is typical for processing industrial waste films and is on a special extruder, equipped with forced feeders-dispensers installed in the bunkers. Uniform dosing of the material from the hopper ensures a good quality of extrudate.
Processing of the polymer in the form of pellets best option of food extruder. This is because granules of the polymer is less prone to freeze, the formation of traffic jams in the hopper than the powder[2].
The powdered material may cake during storage and transportation, including the passage through the hopper. Granular material in contrast to the bulk powder has a constant mass. Download of the interturn space under the funnel of the hopper occurs on the segment length of the screw, equal to (1-1,5)ΔD. In the processing of multicomponent materials to load them into the hopper use individual dispensers: screw (body), vibration, weight. If the application of powdered material the latter have irregular flowability in the hoppers are formed of "arches" hangs on the walls of the bunker. The power auger the material ceases. To address this need in the hopper to put the agitators. The flowability of the material depends to a large extent against humidity: the more humidity, the less the flowability. Therefore, the materials must first be dried[2] .
To increase the productivity of the pellets can be preheated. Using fit to force feed material from the hopper to the auger, also can significantly improve the performance of the machine (in 3-4 times). When compacting material in the interturn space of the screw displaced air escapes back through the hopper. If air removal will be incomplete, it will remain in the melt and after molding forms in the product cavity.
At small oscillation ΔP (Fig. 2), which can occur in practical work, the latter affects the magnitude of fluctuations ΔQ1 or ΔQ2. The more ΔQ, the more the pulsation of the melt, there is more irregularity in the time of the speed and output of the melt. This has an impact primarily on the thickness variation of the obtained products. The increase of the thickness depends on ΔQ
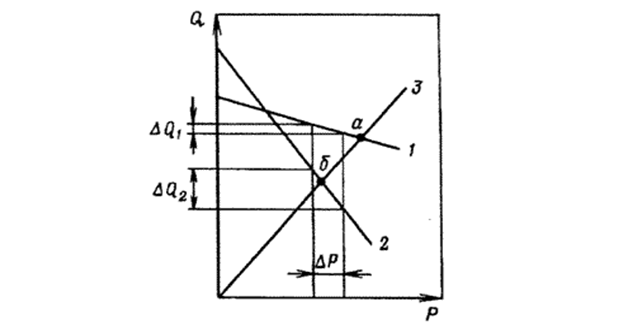
Figure
2. The dependence of the performance Q of
the pressure P of the melt at the exit of the extruder: 1, 2 -
characteristics of the screw;3 - head feature; a and b - operating point
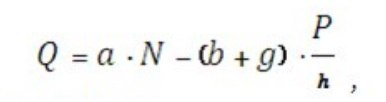
Where: N– frequency of rotation of the auger;
P – pressure at the outlet of the screw (in the end zone III);
h is the average viscosity of the melt;
a, b, g are constant coefficients that depend on geometric parameters of the screw.
From the equation it is easy to show that other things being equal, conditions, extruders with a large L/D fluctuations ΔQ, i.e., ripple is less than in extruders with a smaller L/D.
In case of equality D the first type of extruder is called long- auger, the second- Briefly-auger. In addition, the increase of L contributes to obtaining a homogeneous melt, as the time of exposure to auger more than Briefly-auger extruders. The products, manufactured from a homogeneous melt, possess the best properties. Briefly-auger extruders have L/D = 12-18, long- auger L/D > 30. The most common extruders with L/D = 20 - 25.
The melt spinning auger is pressed through the lattice, which is pressed against the metal mesh. Mesh filter, homogenizer and create resistance to the movement of the melt, they lost some of the pressure. Passing through the filter mesh, the portions of polymer melt with a higher viscosity to stay on the grids. This time should be enough for that portion of the melt has reached the desired temperature. Ultra-high molecular weight fractions of the polymer and various impurities trapped by the nets and after a while they, along with the mesh removed from the barrel[2] .
3.The processing zone of the extruder
The area of nutrition. The polymer in the form of granules, powder or a continuous tape (extrusion of rubber compounds) enters through the feed hopper to the screw channel of a worm and enjoys them due to the difference of friction forces between polymer and cylinder wall and the polymer and the walls of the screw channel. A very rough analogy of the movement of the polymer at this stage is the interaction of the screw and the nut. Imagine that weight coming through the hopper of the polymer is a nut and worm screw. The rotation of the propeller "nut" begins to move along the screw. It is only necessary to bear in mind that this "nut" has the ability to slip relative to the wall of the cylinder, preventing its rotation. Therefore, the distance by which to move such nut-polymer per one revolution of the worm, is not equal to the step cuts; due to the slipping of the polymer on the walls it is many times less.
As the movement of the polymer by the worm develop a high hydrostatic pressure. The resulting friction PA contact surfaces during movement of the polymer, creating a work of friction. Released during this heat is used for the heating of the polymer. Some part of heat is supplied also by conduction from the cylinder walls.[4]
The upper limit to which heated wall on this section of the extruder is determined by the friction coefficient and its temperature dependence. At too high a wall temperature of intensive heat dissipation through the work of external friction of insufficient heat removal leads to premature melting wall layer of the polymer. The friction force sharply decreases, the polymer begins to completely slip relative to the wall of the cylinder and its movement along the screw stops. Under normal temperature conditions initially formed a long tube of polymer, which is pushed by the friction forces on the screw channel. Tube length needs to be large enough in order to developing due to relative motion of the longitudinal pushing force could push the polymer through zone melting.
As you move the solid tube through the channel of the screw the pressure increases, the tube is sealed, the tube surface is in contact with the inner wall of the cylinder heats up, and it formed a thin layer of the melt. Gradually the thickness of this layer increases, and in that moment, when it becomes equal to the thickness of the radial gap between the enclosure wall and the crest of the cut worm, the latter starts to scrape the layer of the melt from the wall, gathering it in front of his pushing face. This section of the worm is actually the end of the feed zone and the beginning of the melting zone.
Area melting. Within the melting zone of the polymer tube is melted by heat supplied from the wall of the housing, and the heat released in a thin layer of the melt due to the work of forces of viscous friction. The total effect of the translational motion of the polymer tube and the rotation of the worm is manifested in the relative motion between the body wall and tube. Under the influence of this movement in a thin layer of melt is formed on the outer surface of the tube, there is a course directed toward the clamping wall of the channel. The melt flow stumbles upon pushing the wall and directed along it, pushing the material of the tube to the front wall. As a result, the height of the tube remains approximately constant, and the width as you move the worm gradually decreases.
Area the dosing. The melt flow in the zone of the dispensing occurs under the action of forces of viscous friction developing due to relative motion of the worm and the cylinder walls, similar to fluid flow in a screw pump through a spiral trajectory. It is customary to represent it as a sum of two independent movements: the translational movement of the melt along the axis of the spiral channel, and circulation (circular) motion in the plane normal to the axis of the screw channel.
Volumetric flow translational flow determines the performance of the extruder and, consequently, limits the rate of movement of the cork granules within the food zone and melting. The circulating current arises because of the existence of a velocity component of the relative motion in the direction perpendicular to the axis of the screw channel, overwhelming the melt in this direction. Moving across the channel, the flow meets the wall pushing and goes along it to the bottom of the channel and then in the opposite direction. The circulation provides for homogenization of the melt, and to even temperature distribution and allows the use of extrusion blending.
At the beginning of the metering zone the melt temperature equal to the melting temperature. Moving in the area of weighing, the polymer continues to heat up as due to the supply of heat from outside and due to heat released due to the intense shear strain. Simultaneously, the process of homogenization of the melt. The final melting of small inclusions and alignment of the temperature field. For normal operation of the extruder it is necessary that the melt flowing to the head, have a defined, uniform in cross-section the temperature. Therefore, the residence time of the melt in the batching area must be sufficient for its heating and homogenization[5] .
4.Basic research and results
Calculations were made of the screw, according to methodology described in [1]: the presence of the screw geometry, and the frequency of its rotation, the calculation of the performance of single screw extruders.
The productivity Q = 1216 mm3/s auger has a diameter of D = 20 mm and length L = 250 mm. It is systematically divided into three zones: the zone food L1 = 50 mm, the plasticizing zone L2 = 70 mm, zone metering L3 = 80 mm. Thread with a pitch of t = 18 mm, and depth h = 3 mm, the width of the crest of the screw e = 2 mm, the angle of the thread µ = 180. Also was obtained the clearance between the auger and the housing of the extruder δ = 0.4 mm.
Conclusion
The results obtained allowed to determine what is the best raw material of the extruder to improve its efficiency may be a polymer in the form of granules, because the granules are less likely to freeze, the formation of traffic jams in the hopper than the powder. Unlike the powder granules have a constant bulk mass that will not allow them to cake during transport.
When writing this abstract master's work is not yet complete. Final completion: 2018. Full text works and materials on the subject can be obtained from author or his supervisor after the specified date.
References
1.Литвинец Ю.И. Технологические и энергетические расчеты при переработке полимеров экструзией. – Екатеринбург 2010г.
2.Лущейкин Г.А. Полимерные электреты / Г.А. Лущейкин – М.: Химия, 1984. – 184 с.
3.Шварц О. Переработка пластмасс /Шварц О, Эбелинг Ф.-В., Фурт Б. – Профессия, 2005. – 320с.
4.В.В. Кафаров. Принципы создания безотходных технологий химических производств, М.: Химия, 1982. С. 285.
5.Д.А. Арашкевич. Вторичная переработка отходов пластмасс и специальные роторные дробилки / Пластические массы, 2003, № 5, с. 13
6.А.П. Цыганков, В.Н. Сенин. Циклические процессы в химической технологии. Основы безотходных производств. М.: Химия, 1988. С. 120 – 131.
7.Свободная энциклопедия Википедия. Статья «Полимеры»http://ru.wikipedia.org/