Реферат по теме "Разработка технических решений для получения вторичных пластиков из полимерных отходов бытового назначения"
Содержание
- Введение
- 1.Пластмассы
- 2.Экструзия
- 2.1 Обзор международных источников
- 2.2 Обзор национальных источников
- 3.Технологические зоны экструдера
- 4.Основные исследование и результаты
- Выводы
- Список источников
Введение
Промышленность пластмасс развивается сегодня исключительно высокими темпами. Начиная с 60-х годов, производство полимеров, основную долю которых составляют пластмассы, удваивается через каждые 5 лет, и эти темпы роста в соответствии с прогнозом на период до 1990 г. сохранятся.
Характерным является опережающее развитие в промышленности пластмасс термопластичных материалов, составляющих в среднем около 70 % от общего количества производимых пластмасс. Одним из сопутствующих эффектов бурного роста промышленности пластмасс является одновременное увеличение количества пластмассовых отходов. Так, в ФРГ они составили в 1977 г. 1,2 млн. т, в США общие отходы полимеров в 1980 г. — 6,4 млн. т, а в Японии по прогнозу к 1985 г. превысят 4,4 млн. т/год. В Англии образуется в год около 800 тыс. т пластмассовых отходов, из которых примерно 300 тыс. т составляют промышленные отходы термопластов. В Швеции количество отходов только от переработки пластмасс превышает 11 тыс. т/год. В 1975 г. в ГДР отходы пластмасс составили 30—40 тыс. т, в Польше — около 20 тыс. т, а всего в странах-членах СЭВ — 200—250 тыс. т .
Таким образом, отходы пластмасс превратились в серьезный источник загрязнения окружающей среды и большинство стран резко интенсифицировали работы по созданию эффективных процессов утилизации или обезвреживания этих отходов. Это во многом связано и с тем, что пластмассовые отходы являются все возрастающим по масштабам вторичным сырьем, которое может служить как для получения изделий и композиций, так и в качестве источника топливных ресурсов. В условиях, когда сырьевые нефтехимические проблемы и проблемы энергетики очень остро стоят во многих странах мира, определенный вклад в решение этих вопросов может внести применение рациональных способов утилизации и обработки пластмассовых отходов.
В настоящее время наряду с совершенствованием технологии синтеза и переработки пластмасс все большее внимание уделяется разработке процессов и методов утилизации или обезвреживания пластмассовых отходов. При этом можно выделить следующие основные направления:
-повторная переработка отходов или использование их в различных композициях;
-термическое разложение с получением целевых продуктов;
-термическое обезвреживание с регенерацией выделяемой теплоты;[6]
1.Пластмассы
Пластик – это органические материалы, основой которых являются синтетические или природные высокомолекулярные соединения (полимеры).
Виды пластмасс и их применение базируются на том, какие полимеры лежат в основе – природные или синтетические. Их подвергают нагреванию, давлению, после чего выполняют формовку изделий разной сложности. Главное, что при этих манипуляциях сохраняется форма готового изделия. Все пластмассы бывают термопластичными, то есть обратимыми, и термореактивными (необратимыми).
Обратимые становятся пластичными под воздействием нагревания и дальнейшего давления, при этом коренные изменения в составе не происходят. Спрессованное и уже ставшее твердым изделие всегда можно размягчить и придать ему определенную форму. Известны такие виды пластмасс (термопластичных), как полиэтилен и полистирол. Первый отличается стойкостью к коррозии и диэлектрическими свойствами. На его основе производятся трубы, пленки, листы, он широко применяется в качестве изоляционного материала.
Виды пластмасс часто используемые:
PET - полиэтилентерефталат, применяемый в производстве ПЭТ-бутылок, а также различной тары для пищи и медицины. Устойчив к активным средам, износоустойчив и стоек к температурным перепадам от -40 до 750С.
ABS - акрилонитрилбутадиенстирол, который используется чаще всего из группы термопластиков. Однако не является самым распространенным. Его отличные свойства не могут повлиять на трудности, связанные с самой печатью этим материалом.
PLA - Полиэтилентерефталат, применяемый в производстве ПЭТ-бутылок, а также различной тары для пищи и медицины. Устойчив к активным средам, износоустойчив и стоек к температурным перепадам от -40 до 750С.
На данный момент полимерные отходы являются одним изважнейшим источником загрязнения нашей планеты. На сегодняшний день большое количество таких отходов вывозиться на свалки либо на специальные полигоны, где они разлагаются 180 – 200 лет. И лишь малая их часть перерабатывается вторично.
2.Экструзия
Экструзия – метод формования в экструдере изделий или полуфабрикатов неограниченной длины продавливанием расплава полимера через формующую головку с каналами необходимого профиля. Для этого используют шнековые или червячные, экструдеры.
Экструдер, в котором полимер расплавляется и гомогенизируется, является основной машиной промышленных линий, на которых осуществляется ряд взаимосвязанных операций процесса переработки. Он выполняет функции пластикатора и насоса, непрерывно продавливающего расплав материала, полученного в винтовом канале, через головку (формующий канал). По устройству и принципу работы основного узла, продавливающего расплав в головку, экструдеры подразделяются на шнековые, без шнековые и комбинированные. Шнековые машины называют также червячными прессами. Высокая пластицирующая способность червячных экструдеров обусловлена тем, что пластикация происходит как в результате теплопередачи от обогреваемых стенок цилиндра (корпуса), так и выделения тепла при деформациях, которым материал подвергается в экструдере[1] .
2.1.Виды экструдеров
Экструдеры подразделяют на одночервячные и двухчервячные (в последних оба червяка расположены в одном цилиндре); известны также трехчервячные и четырехчервячные экструдеры; двухцилиндровые или многоцилиндровые (каждый червяк расположен в отдельном цилиндре); одно- и двухстадийные, в которых пластикация и выдавливание материала осуществляется соответственно в одну или в две стадии; универсальные и специализированные; с осциллирующими (вдоль оси) и одновременно вращающимся шнеком; с зоной дегазации и без нее с вращением шнеков в одну и в противоположные стороны[3] .
Экструдер представляет собой: бункер, в который поступает, гранулы пластмассы с помощью шнека перемещаются, по гильзе к нагревателю, который расплавляет данные пластиковые гранулы. В связи тем, что температура нагревателя 100°-180°C пластмасса не разлагается, и нет токсичных выделений, которые бывают при разложении. Продукт попадает на матрицу, где он равномерно распределяется и выходит через головку данного экструдера. После того как продукт вышел из экструдера он попадает на катушку для наматывания готовой нити. При этом толщина готовой нити зависит от диаметра сопла, установленного на экструдере. Для того чтобы нить остыла, после выхода ее из экструдера, устанавливается вентилятор, который обдувая воздухом, остужает нить[1] .Схема экструдера представлена на(рис. 1).
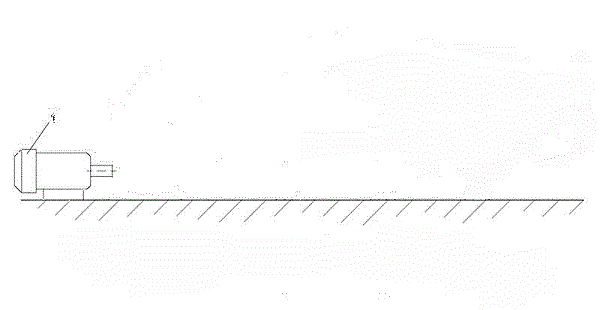
Рисунок
1.Схема экструдера
2.2.Исходное сырье для экструдера
Исходное сырье для экструзии, подаваемое в бункер, может быть в виде порошка, гранул, лент. Последний вид сырья характерен для переработки отходов промышленного производства пленок и осуществляется на специальных экструдерах, снабженных принудительными питателями-дозаторами, устанавливаемыми в бункерах. Равномерное дозирование материала из бункера обеспечивает хорошее качество экструдата.
Переработка полимера в виде гранул наилучший вариант питания экструдера. Это объясняется тем, что гранулы полимера меньше склонны к "зависанию", образованию пробок в бункере, чем порошок[2] .
Порошкообразный материал может слёживаться в процессе хранения и транспортировки, в том числе и при прохождении через бункер. Гранулированный материал в отличие от порошка имеет постоянную насыпную массу. Загрузка межвиткового пространства под воронкой бункера происходит на отрезке длины шнека, равном (1-1,5)ΔD. При переработке многокомпонентных материалов для загрузки их в бункер применяются индивидуальные дозаторы: шнековые (объемные), вибрационные, весовые. Если при применении порошкообразных материалов последние имеют непостоянную сыпучесть, то в бункерах образуются "своды", зависающие на стенках бункера. Питание шнека материалом прекращается. Для устранения этого необходимо в бункер помещать ворошители. Сыпучесть материала зависит в большой степени от влажности: чем больше влажность, тем меньше сыпучесть. Поэтому материалы должны быть вначале подсушены[2] .
Для увеличения производительности машины гранулы можно предварительно подогреть. Применяя приспособления для принудительной подачи материала из бункера на шнек, также удается существенно повысить производительность машины (в 3-4 раза). При уплотнении материала в межвитковом пространстве шнека вытесненный воздух выходит обратно через бункер. Если удаление воздуха будет неполным, то он останется в расплаве и после формования образует в изделии полости.
При небольшом колебании ΔP (рис. 2), которое может возникнуть при практической работе, последнее сказывается на величине колебания Δ Q1 или ΔQ2. Чем больше ΔQ , тем больше пульсация расплава, то есть больше неравномерность во времени скорости и выхода расплава. Это сказывается в первую очередь на разнотолщинности получаемых изделий. Разнотолщинность тем больше, чем выше ΔQ.
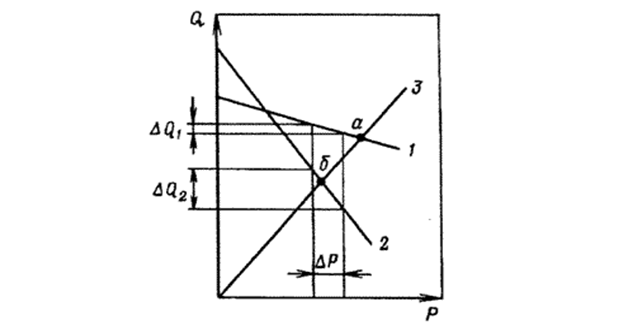
Рисунок
2. Зависимость производительности Q от
давления Р расплава на выходе из экструдера: 1, 2- характеристики
шнека;3- характеристика головки; а и б - рабочие точки
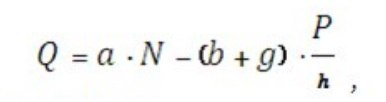
где N– частота вращения шнека;
P – давление на выходе из шнека (в конце зоны III);
h – средняя вязкость расплава;
a, b, g – постоянные коэффициенты, зависящие от геометрических параметров шнека.
Из уравнения легко показать, что при прочих равных, условиях у экструдеров с большим L/D колебания ΔQ, то есть пульсация, меньше, чем у экструдеров с меньшим L/D.
При равенстве D первый тип экструдера называется длинношнековым, второй-короткошнековым. Кроме того, увеличение L способствует получению гомогенного расплава, так как время воздействия на него шнека больше, чем в короткошнековых экструдерах. Изделия, получаемые из гомогенного расплава, обладают лучшими свойствами. Короткошнековые экструдеры имеют L/D = 12-18, длинношнековые L/D > 30. Наиболее распространены экструдеры с L/D = 20- 25.
Расплав вращающимся шнеком продавливается через решетку, к которой прижаты металлические сетки. Сетки фильтруют, гомогенизируют и создают сопротивление движению расплава, на них теряется часть давления. Проходя через систему фильтрующих сеток, порции полимерного расплава с большей вязкостью задерживаются на сетках. Этого времени должно хватить для того, чтобы порция расплава достигла нужной температуры. Сверхвысокомолекулярные фракции полимера и различные примеси задерживаются сетками и через некоторое время они вместе с сеткой удаляются из цилиндра экструдера[2] .
3.Технологические зоны экструдера
Зона питания. Полимер в виде гранул, порошка или непрерывной ленты (экструзия резиновых смесей) поступает через загрузочную воронку в винтовой канал червяка и увлекается им за счет разницы сил трения между полимером и стенкой цилиндра и полимером и стенками винтового канала. Очень грубой аналогией движения полимера на этой стадии является взаимодействие винта и гайки. Представим, что масса поступающего через бункер полимера — это гайка, а червяк — винт. При вращении винта «гайка» начинает перемещаться вдоль винта. Следует лишь иметь в виду, что эта «гайка» имеет возможность проскальзывать относительно стенок цилиндра, препятствующих ее вращению. Поэтому расстояние, на которое перемещается такая гайка-полимер за один оборот червяка, не равно шагу нарезки; за счет проскальзывания полимера относительно стенок оно во много раз меньше.
По мере движения полимера по червяку в нем развивается высокое гидростатическое давление. Силы трения, возникающие па контактных поверхностях при движении полимера, создают работу трения. Выделяющееся при этом тепло идет на нагревание полимера. Некоторая часть тепла подводится также и за счет теплопроводности от стенок цилиндра.[4]
Верхний предел, до которого нагревают стенку на этом участке экструдера, определяется коэффициентом трения и его температурной зависимостью. При слишком высокой температуре стенки интенсивные тепловыделения за счет работы внешнего трения при недостаточном теплоотводе приводят к преждевременному плавлению пристенного слоя полимера. При этом сила трения резко уменьшается, полимер начинает полностью проскальзывать относительно стенки цилиндра, и его движение вдоль червяка прекращается. При нормальном температурном режиме вначале образуется достаточно длинная пробка полимера, которая проталкивается силами трения по винтовому каналу. Длина пробки должна быть достаточно велика для того, чтобы развивающаяся вследствие относительного движения продольная толкающая сила могла протолкнуть полимер через зону плавления.
По мере продвижения твердой пробки по каналу червяка давление в ней возрастает, пробка уплотняется, поверхность пробки, соприкасающаяся с внутренней стенкой цилиндра, нагревается, и на ней образуется тонкий слой расплава. Постепенно толщина этого слоя увеличивается, и в тот момент, когда она станет равна толщине радиального зазора между стенкой корпуса и гребнем нарезки червяка, последний начинает соскребать слой расплава со стенки, собирая его перед своей толкающей гранью. Это сечение червяка является фактически концом зоны питания и началом зоны плавления.
Зона плавления. В пределах зоны плавления полимерная пробка расплавляется под действием тепла, подводимого от стенки корпуса, и тепла, выделяющегося в тонком слое расплава за счет работы сил вязкого трения. Суммарный эффект поступательного движения полимерной пробки и вращения червяка проявляется в относительном движении между стенкой корпуса и пробкой. Под действием этого движения в тонком слое расплава, образовавшемся на наружной поверхности пробки, возникает течение, направленное к толкающей стенке канала. Этот поток расплава натыкается на толкающую стенку и направляется вдоль нее, оттесняя материал пробки к передней стенке. В результате этого высота пробки остается примерно постоянной, а ширина по мере продвижения по червяку постепенно уменьшается.
Зона дозирования. Течение расплава в зоне дозирования происходит под действием сил вязкого трения, развивающихся вследствие относительного движения червяка и стенок цилиндра, подобно течению жидкости в винтовых насосах — по винтовой траектории. Принято представлять это течение как сумму двух независимых движений: поступательного движения расплава вдоль оси винтового канала и циркуляционного (кругового) движения в плоскости, нормальной к оси винтового канала.
Объемный расход поступательного течения определяет производительность экструдера и, следовательно, лимитирует скорость движения пробки гранул в пределах зон питания и плавления. Циркуляционное течение возникает вследствие существования составляющей скорости относительного движения в направлении, перпендикулярном оси винтового канала, увлекающей расплав в этом направлении. Двигаясь поперек канала, поток встречает толкающую стенку и направляется вдоль нее ко дну канала, а затем в обратную сторону. Циркуляционное течение обеспечивает гомогенизацию расплава, выравнивает распределение температур и позволяет использовать экструзию для смешения.
В начале зоны дозирования температура расплава равна температуре плавления. Продвигаясь в зоне дозирования, полимер продолжает разогреваться как за счет подвода тепла извне, так и за счет тепла, выделяющегося вследствие интенсивной деформации сдвига. Одновременно идет процесс гомогенизации расплава. Происходит окончательное расплавление мелких включений и выравнивание температурного поля. Для нормальной работы экструдера необходимо, чтобы расплав, поступающий к головке, имел заданную, однородную по сечению температуру. Поэтому время пребывания расплава в зоне дозирования должно быть достаточно для его прогрева и гомогенизации[5] .
4.Основные исследование и результаты
Был произведен расчет шнека, по методике, приведенной в [1] : нахождение геометрии шнека, а также частоты его вращения, расчет производительности одношнековых экструдеров.
При производительности Q = 1216 мм3/с шнек имеет диаметр D = 20 мм и длиной L = 250 мм. Он систематически разделяют на три зоны: зона питание L1 = 50 мм, зона пластикации L2 = 70 мм, зона дозирование L3 = 80 мм. Резьба с шагом t = 18 мм, и глубиной h = 3 мм, ширина гребня винта e = 2 мм, угол наклона резьбы μ = 180. Также был получен зазор между шнеком и корпусом экструдера δ = 0,4 мм.
Выводы
Полученные результаты позволили определить, что наилучшим сырьем экструдера для повышения его эффективности может стать полимер в виде гранул, так как гранулы меньше склонны к «зависанию», образованию пробок в бункере, чем порошок. В отличие от порошка гранулы имеют постоянную насыпную массу, что не позволит им слёживаться во время транспортировки.
При написании данного реферата магистерская работа еще не завершена. Окончательное завершение: 2018 год. Полный текст работы и материалы по теме могут быть получены у автора или его руководителя после указанной даты.