Реферат за темою "Розробка технічних рішень для отримання вторинних пластиків з полімерних відходів побутового призначення"
Зміст
- Вступ
- 1.Пластмаси
- 2.Екструзія
- 2.1.Види екструдерів
- 2.2.Вихідна сировина для екструдера
- 3.Технологічні зони екструдера
- 4.Основні дослідження та результати
- Висновок
- Перелік посилань
Вступ
Промисловість пластмас розвивається сьогодні виключно високими темпами. Починаючи з 60-х років, виробництво полімерів, основну частку яких складають пластмаси, подвоюється через кожні 5 років, і ці темпи зростання у відповідності з прогнозом на період до 1990 р. збережуться.
Характерним є випереджальний розвиток в промисловості пластмас термопластичних матеріалів, що становлять у середньому близько 70 % від загальної кількості вироблених пластмас. Одним із супутніх ефектів бурхливого росту промисловості пластмас є одночасне збільшення кількості пластмасових відходів. Так, у ФРН вони склали в 1977 р. 1,2 млн. т, у США загальні відходи полімерів у 1980 р. — 6,4 млн. т, а в Японії за прогнозом до 1985 р. перевищать 4,4 млн. т/рік. В Англії утворюється в рік близько 800 тис. т пластмасових відходів, з яких приблизно 300 тис. т становлять промислові відходи термопластів. У Швеції кількість відходів від переробки пластмас перевищує 11 тис. т/рік. У 1975 р. в НДР відходи пластмас становили 30-40 тис. т, у Польщі — близько 20 тис. т, а в країнах-членах СЕВ — 200-250 тис. т[7].
Таким чином, відходи пластмас перетворилися на серйозне джерело забруднення навколишнього середовища і більшість країн різко інтенсифікували роботи по створенню ефективних процесів утилізації або знешкодження цих відходів. Багато в чому це пов'язано і з тим, що пластмасові відходи є все зростаючим за масштабами вторинною сировиною, яке може служити як для отримання виробів і композицій, так і в якості джерела паливних ресурсів. В умовах, коли сировинні нафтохімічні проблеми та енергетики дуже гостро стоять у багатьох країнах світу, певний внесок у вирішення цих питань може внести застосування раціональних способів утилізації та оброблення пластмасових відходів.
В даний час поряд з удосконаленням технології синтезу та переробки пластмас все більша увага приділяється розробці процесів і методів утилізації або знешкодження пластмасових відходів. При цьому можна виділити наступні основні напрями:
-повторна переробка відходів або використання їх у різних композиціях;
-термічне розкладання з отриманням цільових продуктів;
-термічне знешкодження з регенерацією виділеної теплоти;[6]
1.Пластмаси
Пластик – це органічні матеріали, основою яких є синтетичні або природні високомолекулярні сполуки (полімери).
Види пластмас та їх застосування базуються на тому, які полімери лежать в основі – природні або синтетичні. Їх піддають нагріванню, тиску, після чого виконують формування виробів різної складності. Головне, що при цих маніпуляціях зберігається форма готового виробу. Всі пластмаси бувають термопластичними, то є оборотними, і термореактивними (необоротними).
Оборотні стають пластичними під впливом нагрівання і подальшого тиску, при цьому корінні зміни в складі не відбуваються. Спресованого і вже стало твердим виріб завжди можна розм'якшити і надати йому певну форму. Відомі такі види пластмас (термопластичних), як поліетилен і полістирол. Перший відрізняється стійкістю до корозії і діелектричні властивості. На його основі виробляються труби, плівки, листи, він широко застосовується в якості ізоляційного матеріалу.
Види пластмас часто використовуються:
PET - поліетилентерефталат, застосовуваний у виробництві ПЕТ-пляшок, а також різної тари для їжі і медицини. Стійкий до активних середовищ, зносостійкий і стійкий до температурних коливань від -40 до 750С.
ABS-акрилонитрилбутадиенстирол,який використовується найчастіше з групи термопластиков. Однак не є найпоширенішим. Його відмінні властивості не можуть вплинути на труднощі, пов'язані з самою печаткою цим матеріалом.
PLA-Поліетилентерефталат, застосовуваний у виробництві ПЕТ-пляшок, а також різної тари для їжі і медицини. Стійкий до активних середовищ, зносостійкий і стійкий до температурних коливань від -40 до 750С.
На даний момент полімерні відходи є одним изважнейшим джерелом забруднення нашої планети. На сьогоднішній день велика кількість таких відходів вивозиться на звалища або на спеціальні полігони, де вони розкладаються 180 – 200 років. І лише мала їх частина переробляється вдруге.
2.Екструзія
Екструзія – метод формування в екструдері виробів або напівфабрикатів необмеженої довжини продавлюванням розплаву полімеру через формуючу голівку з каналами необхідного профілю. Для цього використовують шнекові або черв'ячні, екструдери.
Екструдер, в якому полімер розплавити і гомогенізований, є основною машиною промислових ліній, на яких здійснюється ряд взаємозалежних операцій процесу переробки. Він виконує функції пластикатора і насоса, безперервно продавливающего розплав матеріалу, отриманого в гвинтовому каналі, через головку (формується канал). По пристрою і принципу роботи основного вузла, продавливающего розплав в голівку, екструдери поділяються на шнекові, без шнекові та комбіновані. Шнекові машини називають також черв'ячними пресами. Висока пластицирующая здатність черв'ячних екструдерів обумовлена тим, що пластикация відбувається як у результаті теплопередачі від нагрітих стінок циліндра (корпусу), так і виділення тепла при деформаціях, яким матеріал піддається в екструдері[1] .
2.1.Види екструдерів
Екструдери підрозділяють на одночервячні і двухчервячні (в останніх обидва черв'яка розташовані в одному циліндрі); відомі також трехчервячні і четырехчервячні екструдери; двоциліндрові або багатоциліндрові (кожен черв'як розташований в окремому циліндрі); одно - і двостадійні, в яких пластикация і видавлювання матеріалу здійснюється відповідно в одну чи в дві стадії; універсальні та спеціалізовані; з осцилюючими (вздовж осі) і одночасно обертається шнек; з зоною дегазації і без неї з обертанням шнеків в одну і в протилежні сторони[3].
Екструдер являє собою: бункер, який надходить, гранули пластмаси з допомогою шнека переміщуються, по гільзі до нагрівача, який розплавляє дані пластикові гранули. У зв'язку з тим, що температура нагрівача 100°-180°C пластмаса не розкладається, і немає токсичних виділень, які бувають при розкладанні. Продукт потрапляє на матрицю, де він рівномірно розподіляється і виходить через головку даного екструдера. Після того як продукт вийшов з екструдера він потрапляє на котушку для намотування готової нитки. При цьому товщина готової нитки залежить від діаметра сопла, встановленого на екструдері. Для того щоб нитка охолола, після виходу її з екструдера, встановлюється вентилятор, який обдуваючи повітрям, остуджує нитка[1] .Схема екструдера представлена на(рис. 1).
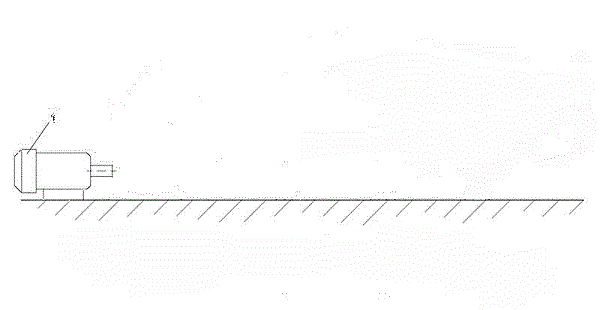
Рисунок
1.Схема экструдера
2.2.Вихідна сировина для екструдера
Вихідна сировина для екструзії, що подається в бункер, може бути у вигляді порошку, гранул, стрічок. Останній вид сировини характерний для переробки відходів промислового виробництва плівок і здійснюється на спеціальних екструдерах, забезпечених примусовими живильниками-дозаторами, встановлюваними в бункерах. Рівномірне дозування матеріалу з бункера забезпечує гарну якість екструдата.
Переробка полімеру у вигляді гранул найкращий варіант харчування екструдера. Це пояснюється тим, що гранули полімеру менше схильні до "зависання", утворенню пробок в бункері, ніж порошок[2].
Порошкоподібний матеріал може злежуватися в процесі зберігання і транспортування, в тому числі і при проходженні через бункер. Гранульований матеріал на відміну від порошку має постійну насипну масу. Завантаження межвіткового простору під воронкою бункера відбувається на відрізку довжини шнека, рівному (1-1,5) ΔD. При переробці багатокомпонентних матеріалів для завантаження їх в бункер застосовуються індивідуальні дозатори: шнекові (об'ємні), вібраційні, вагові. Якщо при застосуванні порошкоподібних матеріалів останні мають непостійну сипучість, то в бункерах утворюються "склепіння", зависати на стінках бункера. Харчування шнека матеріалом припиняється. Для усунення цього необхідно в бункер поміщати ворошителя. Сипучість матеріалу залежить у великій мірі від вологості: чим більша вологість, тим менше сипучість. Тому матеріали повинні бути спочатку підсушені[2] .
Для збільшення продуктивності машини гранули можна попередньо підігріти. Застосовуючи пристосування для примусової подачі матеріалу з бункера на шнек, також вдається істотно підвищити продуктивність машини (в 3-4 рази). При ущільненні матеріалу в межвитковом просторі шнека витіснений повітря виходить назад через бункер. Якщо видалення повітря буде неповним, то він залишиться в розплаві і після формування утворює у виробі порожнини.
При невеликому коливанні ΔP (рис. 2), яке може виникнути при практичній роботі, останнє позначається на величині коливання Δ Q1 або ΔQ2. Чим більше ΔQ, тим більше пульсація розплаву, тобто більше нерівномірність у часі швидкості і виходу розплаву. Це позначається в першу чергу на різнотовщинності одержуваних виробів. Різнотовщинність тим більше, чим вище ΔQ.
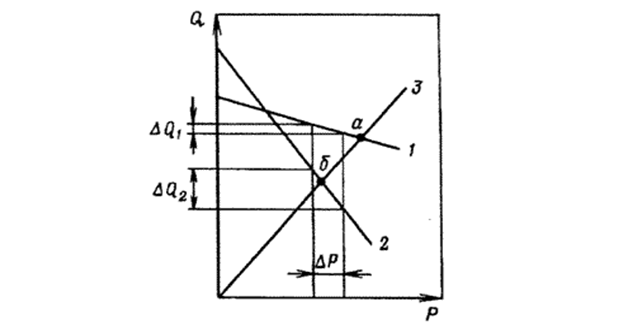
Рисунок
2. Зависимость производительности Q от
давления Р расплава на выходе из экструдера: 1, 2- характеристики
шнека;3- характеристика головки; а и б - рабочие точки
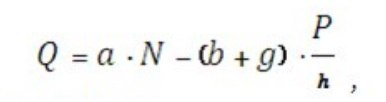
де N– частота обертання шнека;
P – тиск на виході із шнека (у кінці зони III);
h – середня в'язкість розплаву;
a, b, g – постійні коефіцієнти, що залежать від геометричних параметрів шнека.
З рівняння легко показати, що при інших рівних умовах у екструдерів з великим L/D коливання Q, тобто пульсація, менше, ніж у екструдерів з меншим L/D.
При рівності D перший тип екструдера називається длинношнековым, другий-короткошнековым. Крім того, збільшення L сприяє отриманню гомогенного розплаву, так як час впливу на нього шнека більше, ніж у короткошнековых екструдерах. Вироби, одержувані з гомогенного розплаву, що володіють кращими властивостями. Короткошнековые екструдери мають L/D = 12-18, длинношнековые L/D > 30. Найбільш поширені екструдери з L/D = 20 - 25.
Розплав обертовим шнеком продавлюється через решітку, до якої притиснуті металеві сітки. Сітки фільтрують, гомогенізують і створюють опір руху розплаву, на них втрачається частина тиску. Проходячи через систему фільтруючих сіток, порції полімерного розплаву з більшою в'язкістю затримуються на сітках. Цього часу має вистачити для того, щоб порція розплаву досягла потрібної температури. Сверхвысокомолекулярные фракції полімеру і різні домішки затримуються сітками і через деякий час вони разом з сіткою видаляються з циліндра екструдера[2] .
3.Технологічні зони екструдера
Зона харчування. Полімер у вигляді гранул, порошку або безперервної стрічки (екструзія гумових сумішей) поступає через завантажувальну воронку в гвинтовий канал черв'яка і захоплюється ним за рахунок різниці сил тертя між полімером і стінкою циліндра і полімером і стінками гвинтового каналу. Дуже грубої аналогією руху полімеру на цій стадії є взаємодія гвинта і гайки. Уявімо, що маса надходить через бункер полімеру — це гайка, а черв'як — гвинт. При обертанні гвинта «гайка» починає переміщатися уздовж гвинта. Слід лише мати на увазі, що ця «гайка» має можливість прослизати щодо стінок циліндра, що перешкоджають її обертання. Тому відстань, на яке переміщається така гайка-полімер за один оборот черв'яка, не дорівнює кроку нарізки; за рахунок прослизання полімеру щодо стінок воно у багато разів менше.[1].
По мірі руху полімеру по черв'яку в ньому розвивається високий гідростатичний тиск. Сили тертя, що виникають па контактних поверхнях при русі полімеру, створюють роботу тертя. Виділяється при цьому тепло йде на нагрівання полімеру. Деяка частина тепла підводиться також і за рахунок теплопровідності від стінок циліндра.[4]
Верхню межу, до якої нагрівають стінку на цій ділянці екструдера, визначається коефіцієнтом тертя і його температурної залежністю. При занадто високій температурі стінки інтенсивні тепловиділення за рахунок роботи зовнішнього тертя при недостатньому тепловідвід призводять до передчасного плавленню пристінного шару полімеру. При цьому сила тертя різко зменшується, полімер починає повністю прослизати щодо стінки циліндра, і його рух уздовж черв'яка припиняється. При нормальному температурному режимі спочатку утворюється досить довга пробка полімеру, яка проштовхується силами тертя по гвинтовому каналі. Довжина пробки повинна бути досить велика для того, щоб розвивається внаслідок відносного руху поздовжня сила штовхає могла проштовхнути полімер через зону плавлення.
По мірі просування твердої пробки по каналу черв'яка тиск в ній зростає, пробка ущільнюється, поверхню пробки, стикається з внутрішньою стінкою циліндра, що нагрівається, і на ній утворюється тонкий шар розплаву. Поступово товщина цього шару збільшується, і в той момент, коли вона стане дорівнює товщині радіального зазору між стінкою корпусу і гребенем нарізки черв'яка, останній починає відскрібати шар розплаву зі стінки, збираючи його перед своєю штовхає гранню. Це переріз черв'яка є фактично кінцем зони харчування і початком зони плавлення.
Зона плавлення. У межах зони плавлення полімерна пробка розплавляється під дією тепла, що підводиться від стінки корпусу, і тепла, що виділяється в тонкому шарі розплаву за рахунок роботи сил в'язкого тертя. Сумарний ефект поступального руху полімерної пробки і обертання черв'яка проявляється у відносному русі між стінкою корпусу і пробкою. Під дією цього руху в тонкому шарі розплаву, що утворився на зовнішній поверхні пробки, виникає течія, спрямоване до штовхає стінці каналу. Цей потік розплаву натикається на штовхає стінку і прямує уздовж неї, відтісняючи матеріал пробки до передньої стінки. Внаслідок цього висота пробки залишається приблизно постійною, а ширина по мірі просування по черв'яку поступово зменшується.
Зона дозування. Протягом розплаву в зоні дозування відбувається під дією сил в'язкого тертя, що розвиваються внаслідок відносного руху черв'яка і стінок циліндра, подібно до течії рідини в гвинтових насосах — по гвинтовій траєкторії. Прийнято представляти це протягом як суму двох незалежних рухів: поступального руху розплаву вздовж осі гвинтового каналу і циркуляційного (кругового) руху в площині, нормальній до осі гвинтового каналу.
Об'ємний витрата течії поступального визначає продуктивність екструдера і, отже, лімітує швидкість руху пробки гранул в межах зон живлення і плавлення. Циркуляційний протягом виникає внаслідок існування складової швидкості відносного руху в напрямку, перпендикулярному до осі гвинтового каналу, що зваблює розплав в цьому напрямку. Рухаючись поперек каналу, потік зустрічає штовхає стінку і прямує уздовж неї до дна каналу, а потім у зворотний бік. Циркуляційний протягом забезпечує гомогенізацію розплаву, вирівнює розподіл температур і дозволяє використовувати екструзію для змішування.
На початку зони дозування температура розплаву дорівнює температурі плавлення. Просуваючись в зоні дозування, полімер продовжує розігріватися як за рахунок підведення тепла ззовні, так і за рахунок тепла, що виділяється внаслідок інтенсивної деформації зсуву. Одночасно йде процес гомогенізації розплаву. Відбувається остаточне розплавлення дрібних включень і вирівнювання температурного поля. Для нормальної роботи екструдера необхідно, щоб розплав, що надходить до голівці, мав задану, однорідну по перетину температуру. Тому час перебування розплаву в зоні дозування повинно бути достатньо для його прогріву і гомогенізації[5] .
4.Основні дослідження та результати
Був проведений розрахунок шнека, за методикою, наведеною в [1]: знаходження геометрії шнека, а також частоти його обертання, розрахунок продуктивності одношнекових екструдерів.
При продуктивності Q = 1216 мм3/с шнек має діаметр D = 20 мм і довжиною L = 250 мм. Він систематично поділяють на три зони: зона харчування L1 = 50 мм, зона пластикации L2 = 70 мм, зона дозування L3 = 80 мм. Різьблення з кроком t = 18 мм і глибиною h = 3 мм, ширина гребеня гвинта e = 2 мм, кут нахилу різьблення μ = 180. Також було отримано зазор між шнеком і корпусом екструдера δ = 0,4 мм.
Висновок
Отримані результати дозволили визначити, що найкращим сировиною екструдера для підвищення його ефективності може стати полімер у вигляді гранул, так як гранули менше схильні до «зависання», утворенню пробок в бункері, ніж порошок. На відміну від порошку гранули мають постійну насипну масу, що не дозволить їм злежуватися під час транспортування.
При написанні даного реферату магістерська робота ще не завершена. Остаточне завершення: 2018 рік. Повний текст роботи і матеріали по темі можуть бути отримані у автора або його керівника після зазначеної дати.