Abstract
Contents
- Introduction
- 1. The relevance of the topic
- 2. The purpose and the objectives of the work and planned novelty
- 3. The main characteristics of the raw-stuff materials
- 4. Description of the practical part
- 4.1 Preparation solution
- 4.2 Preparation of the mixture
- 4.3 Pressing specimen
- 4.4 Steaming of finished samples
- 5. Investigation of samples on properties
- Conclusion
- References
Introduction
The conditions for the existence and development of life on earth are determined by environmental factors, that is, elements of the environment. Currently, the world community is fully aware of the scale of the threat of environmental pollution from man-made wastes. Output of ash and slag wastes and coal mining waste per year is about 1 billion tons. Accumulating in the areas of operation of enterprises, man-made materials. Danger to public health, loss of secondary resources is created [1].
Technological deposits are accumulations of mineral substances on the surface of the earth or in mine workings that are waste from mining, dressing, metallurgical and other industries and are suitable for quantity and quality for industrial use. it and changing economic conditions [2].
The total mass of accumulated industrial waste is about 30 billion tons. Dumps, slag ponds, and sludge accumulators are located on an area of 160-180 thousand hectares, which increases at a rate of 3 to 6 thousand hectares per year. Low volume of waste processing (10 - 15%) causes an increase in technogenic pollution of all components of OPS. The problem of waste has to do with it. One of the most promising and effective ways to solve it. Of the total amount of industrial waste generated, about 120-150 million tons are suitable for reuse. At present, only about 30% of this amount is used [3].
1. The relevance of the topic
The use of dolomitic dust as a component of the binder makes it possible to utilize slag accumulated in dumps, which are technogenic minerals, to save natural and energy resources, improve the ecological situation and significantly expand the raw material base for the production of building materials. The production of building materials from dolomitic dust will be cheaper than using traditional materials.
In this regard, the problem of implementing measures aimed at the integrated use of mineral resources is of urgent importance.
2. The purpose and the objectives of the work and planned novelty
The purpose of this work is the use of technogenic by-products of the industry as a raw material for the production of building materials.
To achieve the goal, solve the following tasks:
- Analysis of the possibilities of using dolomite dust, granulated blast furnace slag and other man-made wastes as a basis for the production of building materials.
- Development of technologies for the production of building materials from secondary man-made waste.
- Manufacturing of samples of building materials.
- Investigation of strength and other properties.
The planned scientific novelty:the developed technology for the use of dolomite dust and granulated blast furnace slag as raw material for the production of building materials, as well as a technique for investigating the properties of samples.
The use of technogenic raw materials makes it possible to obtain a practical effect:
- To produce cheap building materials.
- Training, putting into operation, renting and leasing.
- Release the occupied Land Sites, recultivate them and eliminate environmental sources, thereby improving the environmental situation around existing enterprises.
Methods of research: making samples and researching their properties on the real equipment of the department.
The results of the individual stages of the work were reported at a scientific conference and published in a collection.
3. The main characteristics of the raw-stuff materials
Dolomite is a unique mineral that belongs to the carbonate group. Dolomite in construction is pretty fast, so this material is strong enough. This mineral is used in construction instead of a lesser known one or together with limestone for the construction of low-rise buildings. This crystalline compound of white or yellow color was used earlier for the production of gypsum mixtures, cement, rubber and glass.
Dolomite dust is a waste of the metallurgical industry, obtained during the burning of dolomite in cupola furnaces. Fresh dolomite dust consists of CaO and MgO, which, during storage, gradually transform into CaCO3 and MgCO3. According to the neutralizing capacity of 1 ton of dolomite dust, 1.5 tons of CaCO3 corresponds [4].
The chemical and granulometric compositions of dolomite and dolomite dust are presented in Tables 1 and 2 [5].
Type of raw material | CaO | MgO | SiO2 | Al2O3 | Fe2O3 | L.O.I. |
---|---|---|---|---|---|---|
Dolomite dust | 12,14% | 24,66% | 12,00% | 10,00% | 12,00% | 29,17% |
Crude dolomite | 29,83% | 20,53% | 2,15% | 0,52% | 0,60% | 45,95% |
Sieve residue | 0,315 | 0,071 | -0,071 |
---|---|---|---|
Mass fraction,% | 3,15 | 31,5 | 65 |
Sieve size,mm | The rest on a sieve,% |
---|---|
10,0 | 2,2 |
5,0 | 40,0 |
3,0 | 45,0 |
1,0 | 66,0 |
0,63 | 67,0 |
less 0,63 | 33,0 |
In the process of grinding crude dolomite to the necessary fractions, about 250,000-260,000 tons were generated annually, and dolomite dust was 10,000-12,000 tons per year, the results were provided by OJSC Dokuchaevsky Fluxo-Dolomite Plant [5]. When calcining dolomite in rotary kilns, the main type of waste is dust. Part of the dust from the kiln in the form of a semi-rendered dolomite with a particle size of 0-1 mm is carried away with waste flue gases and products of decarbonization of dolomite and is captured by two-step purification of waste gases from precipitation chambers, cyclones and electrostatic precipitators. The dust taken by gas cleaning systems with a screw conveyor system and chamber pumps is transported to shipping hoppers or dumps. Dolomite screening has all the advantages of dolomite crushed stone, which distinguishes it from other mineral fillers, but it is much cheaper than crushed stone or chips.
Dolomite dust does not require grinding, however, when sowing seed, it is necessary to screen large and solid particles. The volume of its production is enough today to fully meet the needs of the state. [6].
Slag is a by-product or a waste from the production of metal, after purification from the remains of valuable components sent to the dump. However, in some cases, the main product of the smelting containing the most valuable component of the raw materials is slag (titanium slag obtained by melting ilmenite concentrates, vanadium slag formed during the conversion of vanadium-containing cast iron). The chemical composition of blast furnace slags depends on the composition of the ore, the melting fluids, the fuel used, and the cooling conditions of the slag melt [7].
CaO | MgO | SiO2 | Al2O3 | Fe2O3 | MnO | SO3 | L.O.I. |
---|---|---|---|---|---|---|---|
38,0% | 7,2% | 36,4% | 15,0% | 1,8% | 0,7% | 1,0% | 0,12% |
The high content of MnO in the slag is non-noble, because in this case, partial replacement of CaO occurs in active minerals and the formation of less active minerals. If the MnO content in the slag is more than 3-4%, its hydraulic activity decreases, the properties and structure of the slag glass deteriorate.
The microstructure of the slag affects the most important properties, of which the building material is mechanical strength, chemical resistance and durability.
The porosity of the slag has an inhomogeneous value for its mass. Thus, the porosity of the various fractions of the rapidly cooled slag does not coincide and varies between 15 and 80% [8].
One of the features of the slag filler is an increase in the porosity of the grains as their size increases. The high porosity of blast furnace slags is primarily due to their degassing during cooling of the slag melt. Because The gassing process is not adjustable, it is possible to influence the degree of porosity of the granulated slag by such quantities as the slag viscosity, temperature, and also the cooling rate of the slag melt.
The water consumption of granulated blast furnace slag, due to its high porosity and voidness, is higher than the water demand of natural sand and can reach 30%. It is also possible to reduce the water consumption of blast-furnace slag by partially or completely grinding it [9].
Slag is a granular material with particles of less than 10 mm in size, from dark brown to light yellow, predominantly a glassy structure. After its fine grinding, get the astringent, which possesses hydraulic activity, i.e. property of hardening in water. Granulated main blast furnace slag can be used to produce an activated binder, on the basis of which activated concrete is made [10].
The most profitable direction now is the use of slag as a component for various building materials. It also has great prospects, and still leads to the saving of resources, since slag is a waste of production. And using waste to deal, will bring great benefits.
4. Description of the practical part
4.1 Preparation solution
4.1 Preparation solution
The technology of producing compressed bricks on the basis of technogenic products in laboratory conditions begins with the writing of the formulation. Then weigh and mix components. For a qualitative and reliable verification of the properties, we used 3 samples, different in percentage. To obtain a plastic mass, all components must be strictly dosed according to the recipe. 0.5%. In Table 5, the formulations of the three samples.
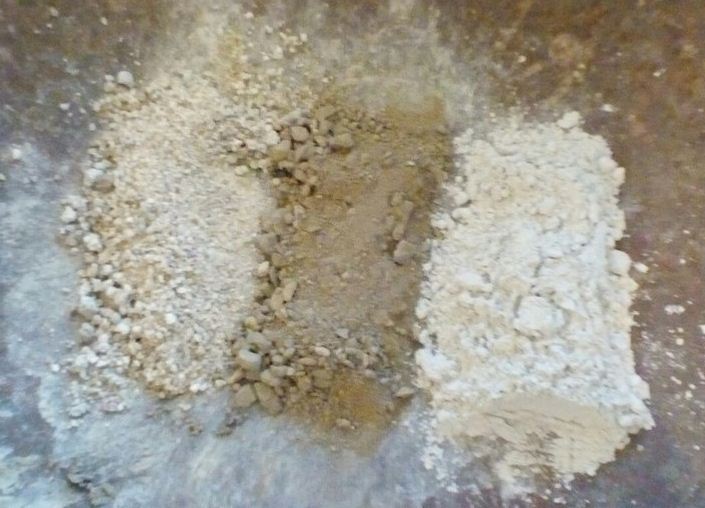
Picture 1 — Raw materials
Sample | Ground grind slag | Granulated slag | Dolomite screenings | Water + LST |
---|---|---|---|---|
1 | 30% | 30% | 40% | 5 мл |
2 | 40% | 20% | 40% | 5 мл |
3 | 50% | 10% | 40% | 5 мл |
4.2 Preparation solution
The dosed mixture was crushed, using a grinder with grinding bodies, where there was also a thorough mixing of all components for their activation. The amount of water strictly prescribed by the recipe was added (if the amount of water does not match the prescription, then at this technological stage the solution will not meet certain standards, the finished products will not obtain the required properties). To obtain a homogeneous mass, it is necessary to continuously mix the mixture.
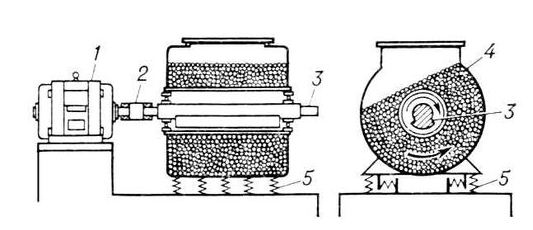
Picture 2 — Mill (1 - electric motor, 2 - coupling, 3 - shaft, 4 - drum, 5 - spring)
4.3 Pressing specimen
At modern enterprises, automated presses, and in the laboratory, a manual press was used. For the workability of the mixture, the mold was lubricated by the LST. The finished mixture with the required consistency was filled with a mold and the pressing process was started. Manipulation was repeated for three different samples. After the samples were pressed they were left for 24 hours on the shelter.
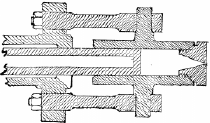
Figure 3 – Press
(animation: 8 frames, 11 cycles of repeating, 136 kilobytes)
4.4 Steaming of finished samples
The manufacture of bricks is then carried out by steaming the raw material obtained after pressing. In the process of steaming, finished products gain up to 70% of their branded strength. At this stage, a special steam chamber was used, where molded samples were sent on pallets. We chose different time intervals: 2, 4 and 6 hours. Steady at a temperature of 70 - 75 °С. After the steamed products were sent to the doppelk for a gradual decrease in temperature, for 1 hour at a temperature of 45 °С. At the end of the steaming phase, the products were allowed to stand at room temperature for 3 days.
5. Investigation of samples on properties
The practical part has not yet been completed, a sufficient number of samples have been made for the experiments. At this stage of the master's work, the strength properties of the samples are investigated. The samples will then be subjected to tests for compression, abrasion, frost resistance and water absorption.
It can be noted that, depending on the percentage of the original components with improved compressibility, the samples are more durable, with sharper ribs and a smooth surface.
Conclusion
When writing this essay, the master's work is not yet complete. The full text of the work and materials on the topic can be obtained from the author or his supervisor after the specified date.
References
- Техногенные отходы в производстве строительных материалов [Электронный ресурс]. — Режим доступа: http://www.concrete-union.ru/articles/index.php?ELEMENT_ID=5206.
- Трубецкой К.Н., Уманец В.Н., Никитин Н.Б. // Комплексное использование минерального сырья. – Екатеринбург. 1987. №12. 18-23 с.
- Касимов А.М. Промышленные отходы. Проблемы и решения. Технологии и оборудование: учебное пособие / А.М. Касимов, В.Т. Семёнов, А.А. Романовский; под ред. А.М. Касимова. – Харьков: ХНАМГ, 2007. – 411 с.
- Известковые отходы промышленности [Электронный ресурс]. — Режим доступа: http://agro-portal24.ru/agrohimiya/686-belitovaya-muka.html.
- Инвентаризация отходов производства «Докучаевского флюсо-доломитного комбината». Форма ОТ – 4 от 06.09.95 г. № 208.
- Доломиты [Электронный ресурс]. — Режим доступа: https://ru-ecology.info/term/42993/.
- Строительные материалы: Справочник / Болдырев А.С., Золотов П.П., Люсов А.Н. и др.; Под ред. А.С. Болдырева, П.П. Золотова. - М.: Стройиздат, 1989. - 567 с.
- Попов Л.Н. Строительные материалы и детали. – М.: Стройиздат, 1986. - 335 с.
- Паращенко О.Д., Шульга А.С., Валешко К.А. Контроль качества строительных материалов. - К.: Будівельник, 1985. - 96 с.
- Пальгунов П.П., Сумарохов М.В. Утилизация отходов / П.П. Пальгунов. - М.: Стройиздат, 1990. - 352 с.