Abstract
This master's work is not completed yet. Final completion: June 2018. The full text of the work and materials on the topic can be obtained from the author or his head after this date.
Содержание
- Introduction
- 1. Theme urgency
- 2. Goal and tasks of the research
- 3. The essence of the coal gasification
- 4. Underground coal gasification
- 4.1 Principle of underground gasification technology
- 4.2 Analysis of known methods for improving the quality of gas
- Conclusion
- References
Introduction
The need for energy increases with the development of society. To meet their needs, mankind uses the energy accumulated by nature for billions of years. One of such natural sources of energy is coal.
Coal is an organic fossil, an important and valuable energy carrier necessary for the development of many industries. Coals can be used as energy fuel and as raw materials for chemical processing.
Thermal processing of coal allows to obtain valuable products for many industries. The processes of solid fuel processing differ among themselves depending on the desired product. The process by which a combustible gas is obtained from a solid fuel as a target product is called gasification.
Gasification of coal is one of the oldest industrial technologies. The first report on the receipt of flammable gas from charcoal was made in 1609 by John Van Helmont from Brussels. The first patent for the method of coal gasification was issued in 1788 to Robert Gardner. And in 1792 engineer William Murdoch, who worked for the famous inventor of steam engine James Watt, produced the first gasifier and began using coal gas for lighting [1].
Until the 60s of the last century the technology of coal gasification on an industrial scale was actively used in many countries, since coal was the main source of energy. In the Federal Republic of Germany gasification was used to produce fuel gas and synthesis gas for the chemical industry. In the USA up to the 1940s the main consumer gas was the gasification product of coal. In 1925 in the United States about 12,000 units processed gas to 25 million tons of coal per year [2].
In the 1950s and 1960s supply increased and prices for petrochemical raw materials decreased, so the chemical industry and most of the municipal gas plants were forced to reorganize for the gasification of oil and gasoline. This made it possible to simplify the production of gas and made it more economical.
However, the first oil crisis in the early 1970s followed, which gave impetus to many countries to develop programs for energy independence. Since 1973, work on gasification of coal has intensified in Europe, especially in the FRG. Efforts were mainly focused on the development of such processes as the production of synthesis gas, a reducing gas for iron production, and also cheap clean fuel for industry and electric power. In the USA, a program was adopted with a multimillion budget for the development of new generation coal technologies.
1. Theme urgency
Gaseous fuel in comparison with solid fuel has a number of advantages: ecological compatibility, transportability and comfort of use. Therefore, it is more preferable for the energy sector.
In the gasification process, it is possible to obtain products such as:
- synthesis gas, through the processing of which valuable chemical products are obtained, including motor fuels;
- сombustible gas as a substitute for natural gas;
- generator gas used as fuel for power plants.
Energy crises and the prospect of exhaustible oil and gas resources lead to the need for alternative energy sources. Many consumers are starting to formulate energy supply programs focused on local energy sources in order to ease dependence on the world energy market. Therefore, to date, gasification of coal is of particular interest. Coal gasification as an alternative to oil and gas technologies has two major drawbacks: high capital intensity of main processes and significant costs for gas cleaning from harmful impurities.
Modern gasification processes are largely different technological and environmental indicators compared with 50-60 years. At that time, several basic methods of gasification were known. Now there are dozens of different options for organizing the process. However, the problem is that it is impossible to develop one universal process that will use different coals and produce products for individual industries, including traditional and hydrogen energy, metallurgy and chemical production. Each process has its own consumer niche, its shortcomings and advantages. Therefore, gasification technologies with combined production of several products have the greatest economic efficiency and flexibility. Along with the established term "cogeneration", the terms "trigeneration" and "quadrogenation" begin to be applied. This is a reflection of the current trend in the field of coal gasification.
As an integrated approach to fuel processing, an especially attractive process is the technology of underground coal gasification (UCG). Large-scale research and development of underground coal gasification began in the USSR since the 1930s. In the pre-war period, a lot of research and experiments were carried out at the experimental stations "Podzemgaz" in the Donbas and Moscow suburbs [3]. The "Podzemgaz" office developed the world's first UCG industrial scale project.
In the 50-60's several UCG industrial stations were operated. With the advent of Siberian natural gas and the advent of the era of cheap oil, the UCG process ceased to be economically attractive, and it was also characterized by a number of serious technical difficulties. On the territory of the modern Russian Federation, the last station "Podzemgaz" in the Kuzbas worked until the 90s and was closed due to physical wear and tear of equipment.
In China in the 2000s a number of UCG enterprises were exploited. The development was carried out in a combined way using mine preparation and drilling of technological wells for blasting and gas removal [4]. Experimental work on UCG, some of them on an industrial scale, in the last decade were conducted in China, Australia, Canada, the European Union, the United States and others.
2. Goal and tasks of the research
Goal of the research is the determination of intensification ways for the coal gasification process to ensure high productivity of gas generator and quality of output products.
:Tasks of the research
- Study of the theoretical foundations of coal gasification.
- Study of existing technological schemes for coal gasification.
- Comparative analysis of gasification methods in gas generators and underground gas generators.
- Development of a mathematical model describing the process of the gasification.
- Analysis of prospects for the use of generator gas.
Research object: coal gasification technology.
Research subject: improvement of coal gasification technology.
Scientific novelty of the work lies in finding opportunities to improve the technique of coal gasification.
Practical significance of the work is to apply the results obtained to intensify the gasification process, increase the productivity of gasifiers and improve the quality of the products.
3. The essence of the coal gasification
Gasification is a thermochemical process of processing solid fuel in flammable gases in the presence of gasifying agents. During gasification, the fuel is converted into combustible gases by incomplete oxidation with oxygen or steam at high temperatures. The gasification product is a combustible gas containing mainly CO and H2. By-products are ash, slag and resin.
In a gasifier with a direct gasification process (figure 3.1), a layer of coal with a thickness of 0.6 m and more is supported by a grate, under which blast is fed. Slag and ash fall down through the grate holes. In the combustion (oxidation) zone, carbon dioxide forms, which rises and interacts with hot carbon, resulting in a reduction zone where carbon dioxide is reduced to carbon oxy. Both zones form a gasification zone. Above the height of the layer, hot gas distills volatile substances from the coal (the coking zone). At the uppermost part of the apparatus, the moisture of the coal evaporates (the drying zone). The gas produced in this process contains resin.
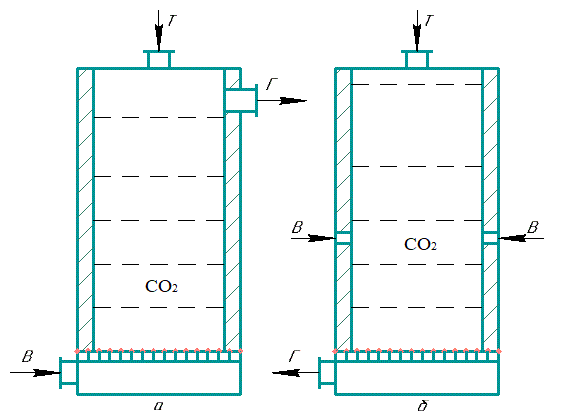
Figure 3.1 – Arrangement of zones in the gas generator
(animation: 13 frames, 138 kilobytes)
(а – direct process, б – reverse process, Т - fuel, В - air, Г - gas)
4. Underground coal gasification
4.1 Principle of underground gasification technology
Of special interest is the technology of underground coal gasification, which consists in converting fuel into combustible gas directly at the site of its occurrence.
The essence of UCG technology (figure 4.1) consists in drilling from the ground surface of vertical 2, 3 and inclined wells 1 to coal seam 8. Wells are joined in the formation creating a fire drift 6. Inclined workings and a fire drift limit the area of the coal seam called the panel 4. Air is supplied to the blowing (injection) well 2. When applying the blast, the coal seam is ignited and conditions are provided for the conversion of coal directly into the bowels into combustible gas. The produced gas is discharged through the gas-discharging wells 3 to the ground surface.
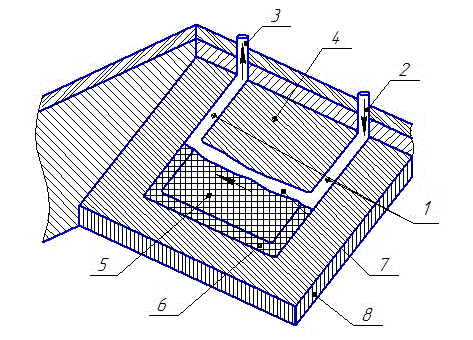
Figure 4.1 – Scheme of the UCG panel
4.2 Analysis of known methods for improving the quality of gas
The composition and heating value of the product gas depends on the technological modes of the gasification process. The technological regime implies different amounts and composition of the blast. Let us consider the experimental data of the experimental stations "Podzemgaz" on the investigation of the dependence of the gas composition on the blast conditions.
When using air blast, the main combustible part of the produced gas was carbon monoxide, but most of the gas was occupied by non-flammable nitrogen. Consequently, the gas with air blast has a relatively low calorific value [7].
With the artificial enrichment of the air with oxygen, the calorific value of the gas increased, since the content of carbon monoxide and hydrogen increased, and the nitrogen content decreased. Thus, the change in the oxygen content in the blast is a regulator of the heat of combustion of the gas.
Conclusion
The processing of coal by gasification is an actual topic for today. There is a trend of interest and transition to the technology of coal gasification in most countries and regions that have large reserves of this natural fossil. The transition is conditioned by the desire of consumers to be independent of fluctuations in the global energy market and to use local energy resources.
Gasification of coal allows us to obtain a valuable gas that can be used not only as an energy source, but also as a technological raw material for the production of methanol, dimethyl ether, for the extraction of hydrogen, for use as a reducing agent in metallurgical processes.
The intensification of the process in gas-generator plants depends on the design decisions and a number of technological factors, one of which are: the temperature regime of the reaction volume, the change in the reaction surface of the reacting particles, the gas flow rate, and the process under pressure.
The method of underground gasification is a promising area for complex processing of coal seams. A comparative analysis of the two methods shows that gasification in underground gas generators excludes mine work, eliminates the need to design land-based gas generators, allows processing seams with complex geological and geological conditions, and also processes low-grade fuels. Gasification in terrestrial gas generators is a big plus in that this process can be controlled, which is extremely difficult for underground gasification. Underground gasification has significant technical drawbacks. These include the complexity of drilling operations, difficulties in drainage, leakage of blast and gas. The future of gasification of fuel depends on the solution of the above problems.
References
- Исламов С. Р. Газификация угля: прошлое и будущее / С. Р. Исламов, В. Н. Кочетков, С. Г. Степанов // Уголь. – 2006. - № 8. – С. 69-71
- Шиллинг Г.-Д., Бони Б, Краус У. Газификация угля: Горное дело – сырье – энергия/Пер. с нем. – М.: Недра, 1986. 175 с.
- Чумарина А. В., Голубев А. В. Перспективы развития подземной газификации горючих ископаемых// Материалы VII Региональной конференции «Комплексное использование природных ресурсов» - Донецк, ДонНТУ – 2015.
- Кондырев Б. И. Опыт подземной газификация в Китайской Народной Республике / Кондырев Б. И., Белов А. В. // Горный информационно-аналитический бюллетень (научно-технический журнал). - № 10. – 2005. – С. 286-289.
- Химия и переработка угля/В. Г. Липович, Г. А. Калабин, И. В. Калечиц и др. – М.: Химия, 1988. – 336 с.: ил.
- Каталымов А. В., Кобяков А. И. Переработка твердого топлива:Учебное пособие для вузов. – Калуга: Издательство Н. Бочкаревой. 2003. – 248 с.
- Чумарина А. В., Веретельник С. П., Голубев А. В. Направления конструктивного и технологического совершенствования подземной газификации горючих ископаемых// Материалы Х Международной научной конференции аспирантов и студентов «Охрана окружающей среды и рациональное использование природных ресурсов» - Донецк, ДонНТУ – 2016.
- Нусинов Г. О. Подземная газификация углей/Нусинов Г. О. – Москва: ГОНТИ НКТП СССР, 1938. – 128 с.