Abstract
This article is not finished, approximate date of finishing June, 2018. You can ask for the final version of work by email-adress Pashons26@gmai.com.
Content
- Introduction
- 1. Theme urgency
- 2. Goal and tasks of the research
- 3. Physical and chemical basics of PET processing
- 4. Experimental part
- Conclusion
- References
Introduction
Hydrophobization is the process of giving water-repellent properties to some substances or surfaces. This quality allows you to protect the surface from contamination of liquid nature, increase their service life and protect against corrosion. Reducing moisture absorption eliminates the occurrence of cracks from freezing of moisture inside the building structure, as well as rotting and swelling of the wood.
From the point of view of bulk materials, the decrease in hygroscopicity of sand excludes their caking, the formation of solid lumps of fine particles. Sticking particles into pieces makes the bulk materials unsuitable for use. Hydrophobization increases the shelf life of mixtures.
The standard hydrophobizators for extinguishing powder formulations are Aerosil AM-1-300, white carbon black, silicone fluids, which occupy 3-5% of the total mass of the powder. However, in this paper, it is proposed to consider the possibility of using polyethylene terephthalate processing products as hydrophobizators.
1. Theme urgency
The relevance of this work has a dual justification. On the one hand, the processing of polyethylene terephthalate (PET), which is a huge part of solid domestic waste (SHW) [1], mainly plastic bottles and bags, is an important issue of our time because of its slow decomposition in the environment. Annually millions of animals die in the wild because they fall into "traps" from plastic bottles or eat plastic parts [2]. Huge land areas are allocated to garbage dumps, but they are already not enough. Thus, the issue of processing solid waste and the use of so-called secondary
plastics or products of its decomposition becomes acute.
The second side of the issue is hydrophobization. Technology of hydrophobization of materials is currently used extremely widely. Reducing hygroscopicity plays an important role in improving the properties of materials both in everyday life and at work.
For sale there are sprays for textiles and other surfaces that give the things water repellent properties, which helps protect them from contamination of various liquid nature. Most of the products of the paint and varnish industry also contain hydrophobizing agents, so that when they are coated with wood, they are excluded from rotting, ensure dimensional stability and evenness of the surface (due to the absence of swelling). Cements mixed with a hydrophobizing agent are also made more durable, they will not absorb moisture even though they are a porous material. Thus, buildings made of hydrophobic materials will remain reliable for longer, eliminating the risk of cracking during the winter period due to freezing of moisture inside the structures.
Also important is the reduction in the hygroscopicity of loose materials. The hydrophobic powder has a much lower hygroscopicity compared to the untreated analog, which allows it to reduce the moisture content and propensity to moisture immobilization, and eliminates the formation of lumps during storage. Their application can be extremely wide:
- In melioration a layer of hydrophobic sand is created under the fertile soil layer in order to reduce the water discharge for irrigation of fields and the washing out of minerals from the upper soil layer.
- In construction sand is used as a heat and waterproofing layer between floors, and this function it can perform only in dry form.
- Fine-dispersed materials can be stored without special conditions without sorption of moisture, caking and loss of fluidity, which allows to extend their shelf life, simplify the storage conditions without affecting further technological processes using the material.
In each case, it is necessary to pay attention to the different properties of the water repellents, since in addition to performing its basic function, it should not affect the rest of the process or deteriorate the properties of the material: for example, hydrophobic cement should not become less durable than the original one, evaporation of lacquers and paints should not become toxic, sand used in reclamation, should not contribute to the introduction of harmful substances into the culture, the spray used to protect against tissue contamination should not cause irritation on the human's skin. All water repellents must quickly and easily decompose into harmless components in environmental conditions.
From this point of view, the process of hydrophobization of fire extinguishing powders is of particular interest. The use of a special agent requires special consideration of its properties, namely, the absence of hazardous reactions to high temperature (combustion, explosivity) and the possibility of application to finely divided particles. The hydrophobic agent can improve the fire-extinguishing ability of the powder not only protecting it from caking, but also taking more heat in the combustion reaction if the hydrophobic agent decomposes on heating with absorption of a large amount of heat [3].
2. Goal and tasks of the research
The purpose of this work is to determine the feasibility of using thermal processing products of polyethylene terephthalate as a hydrophobic agent for bulk materials, in particular fire extinguishing powders, and to identify the optimal technology for using a hydrophobic agent.
Research object : finely dispersed compounds.
Research subject : hydrophobic properties of finely dispersed systems.
Within the framework of the master's work, it is planned to receive the current scientific results on the moisture resistance of various finely dispersed mixtures, depending on their treatment with hydrophobisers in different percentages.
3. Physical and chemical basics of PET processing
Polyethylene terephthalate is a polymer whose monomer contains an aromatic nucleus and a carbonyl group (Figure 1). When heated, depolymerization occurs. According to the results of laboratory studies, it can be said that as a result of the destruction processes, gas, terephthalic and benzoic acid synthesis and holonuclear compounds are formed. There are discontinuities of aliphatic C—C bonds, C—O bonds with the liberation of CO and H2, and due to the presence of hydrogen in the pyrolysis medium, a C=O bond breaks down to form a hydroxyl group.
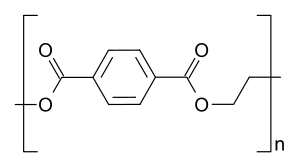
Figure 1 – Structural formula of polyethylene terephthalate
Thus, depolymerization of PET with separation of two para-substituents leads to the formation of pitch, gonuclear aromatic and polyaromatic compounds, depolymerization and separation of one of the substituents of the benzene ring with hydrogen saturation with C=O bonds leads to the formation of benzoic acid (Figure 2), and hydrogen saturation two para-substituents on the C=O bond – to the formation of terephthalic acid (Figure 3).
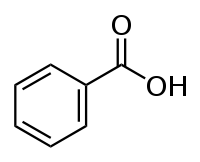
Figure 2 – Structural formula of benzoic acid
Laboratory studies have shown that the yield of solid and liquid pyrolysis products to gaseous substances is 1:1. A pyrolysis process with rapid heating was carried out, which gives an increased yield of gaseous products, in the steady-state gas regime much less is released. The heating was carried to 600°C.
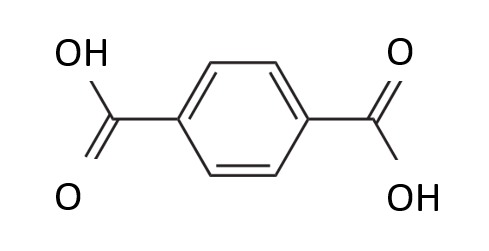
Figure 3 – Structural formula of terephthalic acid
4. Experimental part
To study the process of thermal destruction of PET, we assembled the apparatus shown in Fig. 4. Thermal degradation of polyethylene terephthalate was carried out at a temperature of 400°C with trapping the decomposition products.
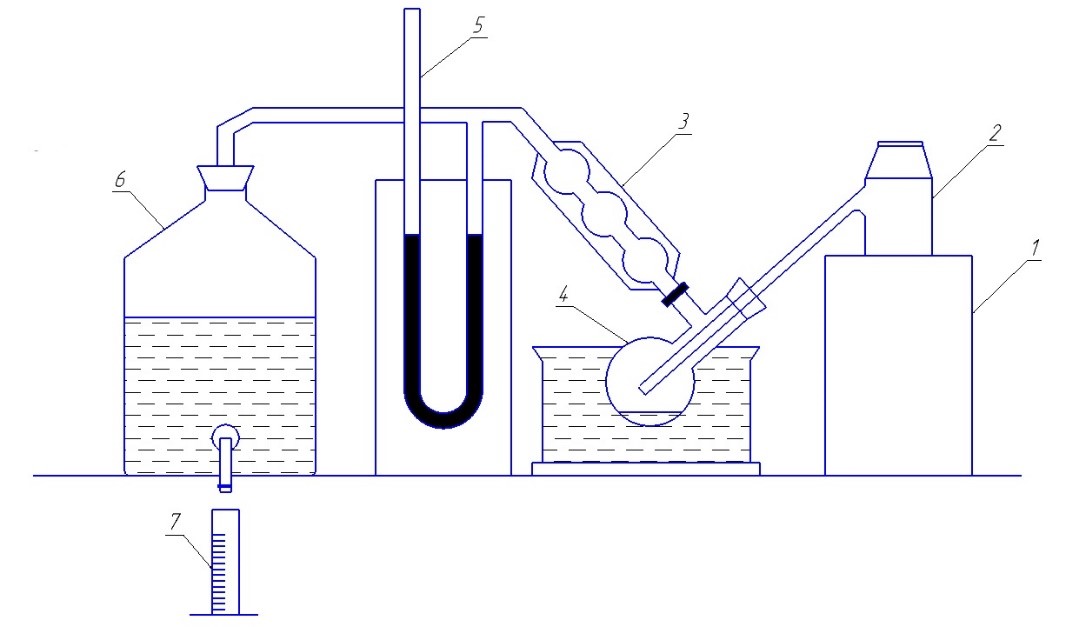
1 – electric furnace; 2 – retort; 3 – refrigerator; 4 – Wurtz flask; 5 – manometer; 6 – gas collector; 7 – dimensional cylinder
Figure 4 – Laboratory installation of semi-coking PET
To obtain raw materials for the hydrophobization of extinguishing powders, the method of low-temperature alkaline hydrolysis of PET was used. It took 24 g of 5 mm to 5 mm plastic shredded from pre-cleaned PET bottles and in a stoichiometric ratio with an excess to increase the product yield of 38 g of NaOH. Water was added to better mix the reaction mixture. The plant consists of a flat bottom flask, a reaction mixture preheater, a reverse water cooler. The reaction initiation is the boiling point of the reaction mixture. After 15 minutes from the beginning of the boiling, a foam appears in the flask. A white precipitate is the desired product. The reaction is limited by the formation of a PET product on solid particles, which makes it difficult to diffuse the alkali to the surface of the plastic.
By solubility in liquids of different nature, density, and flame shape during combustion, it was determined that the products contain benzoic and terephthalic acids. Both these acids are surface-active substances of cationic type, which means they can impart hydrophobic properties to materials.
To conduct research as a bench for evaluating the hydrophobic properties of powdered materials, the device represented in GOST 14839.13-2013 (Figure 5) was used as a prototype [5].
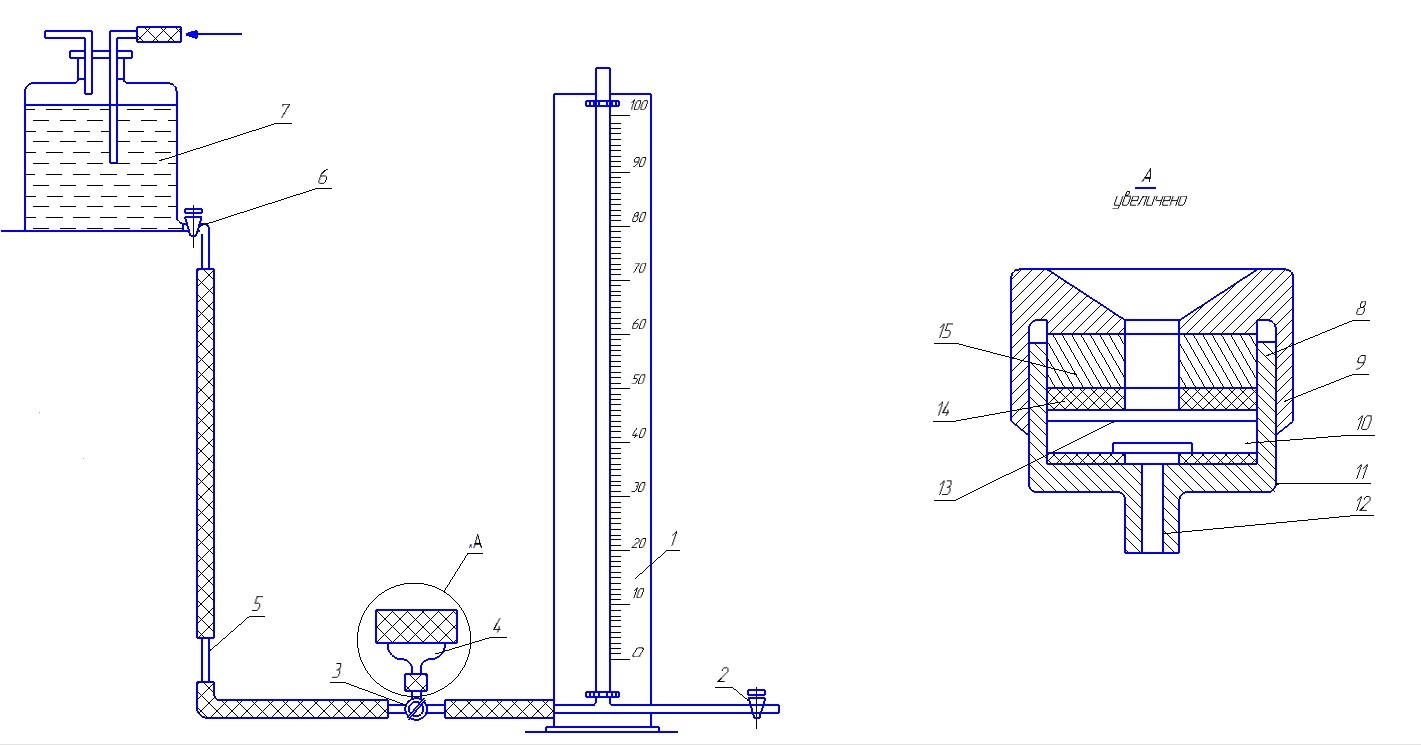
1 – barometric tube; 2 – the trigger cock; 3 – a three-way crane; 4 – assembly; 5 – capillary tube; 6 – the adjusting crane; 7 – pressure vessel; 8 – housing; 9 – cover-nut; 10 – the substance to be tested; 11 – the limiter; 12 – a branch pipe; 13 – circles of filter paper; 14 – rubber sealing rings; 15 – metal clamping ring
Figure 5 – Diagram of the device for determining the wettability of powders
For a more vivid presentation of the results of experiments, it was suggested to use the time necessary for complete filling of the pores in the powder material as the wettability criterion. The test material, dried at room temperature until air-dry, was sieved through a sieve with a non-ferrous metal mesh with a nominal mesh size of 1.0 mm to 0.08 mm.
To apply a water-repellent film to the powder particles, 35 ml of a solution of the hydrophobizer in benzene were added to the material of the determined fraction in a quantity of 100 g, and the solution was left to stand for 30 minutes. The test material was then spread out in a thin layer on a substrate and dried at room temperature for a day to an air-dry state. Before the test, the test material was thoroughly mixed.
For the analysis, a sample of a certain fraction was taken in an amount of 30 g. The sample was placed in a prepared assembly. The constant rate of water rise (constant of the hydrodynamic device) was maintained at 20 cm / min. The wetting time was determined from the moment the water was fed into the assembly from the pressure vessel until the wet spot appeared on the surface of the filter paper cup covering the layer of the test material [6]. For each sample, three parallel determinations were made, the results of which computed the arithmetic mean, rounded to 1 s.
To conduct further research, we selected the most significant factors affecting the rate of filling of pores in the powder material:
To study the dependence of the hydrophobic properties of the material on its dispersion (see Fig. 6), silicon dioxide was used for fractions of 1.0-0.5 mm, 0.315-0.250 mm, less than 0.250 mm.
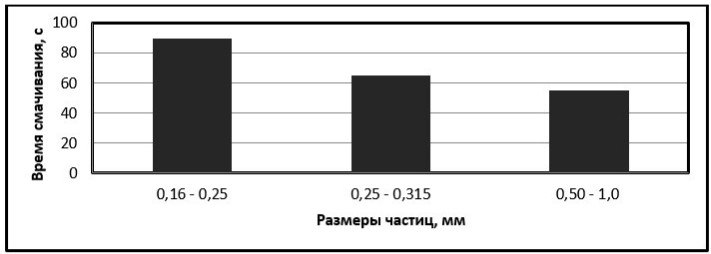
Figure 6 – Dependence of wetting time of sand on dispersion
As can be seen from the diagram, the wettability depends on the particle size of the material being studied. The larger the particle, the easier the water penetrates into the pores of the material.
Further studies were carried out to determine the effect of hydrophobic additives on the wettability of powder materials. As it was said before, as hydrophobic additives we used benzene and terephthalic acids obtained as a result of pyrolysis of polyethylene terephthalate.
To apply a water repellent to the particles of the dispersed material, the latter was dissolved in benzene and the resulting solution was treated with a particulate material, followed by air drying (in a fume hood) at room temperature.
Two series of experiments with silica of fraction less than 0.250 mm were carried out. In the first experiment, silicon dioxide was treated with pure benzene (control sample), and in the second - with a solution of a hydrophobizer in benzene. The results of the experiment are shown in the diagrams (Figures 7-8).

Figure – 7 Dependence of the wetting time of sand on the nature of the hydrophobic agent
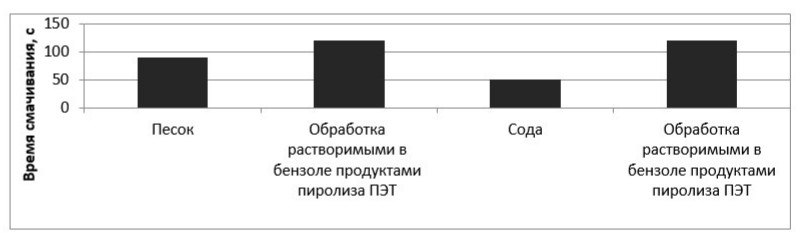
Figure 8 – Dependence of the wetting time on the nature of the material
As can be seen from the results presented in the figures, the application of a hydrophobic agent increases the time required for complete blotting of the powder material in accordance with GOST 14839.13-2013 almost twice. A slight decrease in the time for complete blotting of the powder material after treatment with pure benzene can be explained by washing away fats from the surface of this material.
Conclusion
The results of these studies allow us to draw the following conclusions. Wetability depends on the particle size of the test material. The larger the particle, the easier the water penetrates into the pores of the material. The application of a hydrophobizer to the surface of particles of particulate material significantly increases the time required for complete sweeping of the powder material. The possibility of using pyrolysis products of polyethylene terephthalate (benzoic acid and terephthalic acid) as a hydrophobizer is shown.
Further research is planned to be carried out using existing extinguishing powder compositions for hydrophobization, also promising new ones.
References
- Маракулина А.Н. Рентабельность переработки ПЭТ бутылок / А.Н. Маракулина // Уральская горная школа – регионам, сборник докладов Международной научно-практической конференции. – Екатеринбург: Изд-во УГГУ, 2017. – с.626.
- Лунёва О.В. Основной источник загрязнения окружающей природной среды – отходы / О.В. Лунёва // Вести Автомобильно-дорожного института, 2011. – №1(12). – с. 181-187.
- Бобрышева С.Н., Боднарук В.Б., Кашлач Л.О., Горовых О.Г. Технологические особенности обеспечения гидрофобности огнетушащих порошков. // Чрезвычайные ситуации: образование и наука, 2008. – №2(3). – С.24-33.
- Дмитрук А. Ф. Исследование термодеструкции отходов растительного и синтетического происхождения / А. Ф. Дмитрук, Т. В. Крюк, Л. Ф. Пикула, В. Ю. Портнянский // [Электронный архив ДонНТУ]. – Режим доступа: http://ea.donntu.ru:8080/jspui/handle/123456789/3287
- Суркова А.О., Грачев И.О., Чернова О.А. Разработка технологии переработки отходов полиэтилентерефталата / А. О. Суркова, И. О. Грачев, О. А. Чернова // Охрана окружающей среды и рациональное использование природных ресурсов. Материалы X Международной научной конференции аспирантов и студентов. – Донецк, ДонНТУ – 2016.
- ГОСТ 14839.13-2013 Вещества взрывчатые промышленные. Методы определения водоустойчивости. – М. Стандартинформ. 2014. – 13 с.
- ГОСТ 26952-2009 Порошки огнетушащие. Общие технические требования и методы испытаний. – М. Стандартинформ, 2009. – 14 с.
- ГОСТ 4.107-83 Система показателей качества продукции. Порошки огнетушащие. Номенклатура показателей. – 7 с.
- Баратов, А. Н. Огнетушащие порошковые составы / А.Н. Баратов, Л.П. Вогман // – М.: Стройиздат, 1982. – 72 с.
- Абдурагимов, И. М. Физико-химические основы развития и тушения пожаров / И. М. Абдурагимов, В. Ю. Говоров, В. Е. Макаров – М.: Высшая инженерная пожарно-техническая школа МВД СССР, 1980. – 255 с.