Реферат
Зміст
- Вступ
- 1. Актуальність теми
- 2. Мета і задачі дослідження та заплановані результати
- 3. Опис конструкції
- 4. Огляд досліджень по темі
- 5. Основна частина
- Висновки
- Перелік посилань
Вступ
У сталеплавильному виробництві за останній час відбулися докорінні зміни в зв'язку з заміною мартенівського способу, виплавки сталі киснево-конверторним, створенням великих конвертерних агрегатів, потужних електросталеплавильних печей і нових установок спеціальної металургії, розробкою і широким впровадженням машин безперервного лиття заготовок. У зв'язку зі збільшенням обсягу виробництва і поліпшення якості сталі виключно важлива роль належить киснево-конвертерному виробництву, мающему високі техніко-економічні показники - високу продуктивність при менших капітальних витратах в порівнянні з мартенівським способом, більш сприятливі умови для автоматизації. Продуктивність одного 400 т конвертера перевищує продуктивність цілого мартенівського цеху з 8-10 печами місткістю 600 т кожна. Конвертерний спосіб виплавки сталі безперервно удосконалюється. Сучасна технологія виплавки сталі в конвертері передбачає відсічення шлаку при випуску сталі з конвертера. Існують кілька способів відсічення шлаку, для кожного з яких розроблено і експлуатується спеціальне обладнання. У цій роботі розглядається маніпулятор осьового типу для введення відсічних елементів в сталевипускний канал конвертера при випуску сталі.
1. Актуальність теми
У найбільш несприятливих умовах в момент введення в конвертер отсічного елемента знаходиться порожниста штанга, в тілі якої виникають значні температурні і механічні напруги. Деформації вигину штанги обумовлені дією сили тяжіння отсічного елемента. Багаторазове чергування нагрівання й охолодження (20 - 25 разів на добу), що сприяє появі, поряд з термічними, фазових напруг, в результаті чого штанга викривляється, а на її поверхні утворюється сітка розпалу і з'являються тріщини, поступово розвиваються в глибину і ослабляють перетин деталі. У підсумку термін служби штанги різко скорочується і її доводиться вибраковувати [1].
Для підвищення стійкості порожнистої штанги необхідні оптимізація її конструктивного виконання, правильний вибір матеріалу і методу зміцнення, які могли б сприяти підвищенню опірності виробу циклічним тепловим змінам і забезпечити необхідну жорсткість системи. Тому наявність інформації про характері і абсолютних значеннях змін температури по довжині, периметру та перетину цієї ланки маніпулятора в процесі його експлуатації дасть можливість при розрахунку і конструюванні не тільки аргументовано обгрунтувати вибір матеріалу для виготовлення, а й правильно призначити метод і режим зміцнення відповідальної деталі.
2. Мета і задачі дослідження та заплановані результати
Метою дослідження є удосконалення конструкції маніпулятора для підвищення безвідмовності, вивчення температурного поля діючого на штангу маніпулятора в кисневому конвертері. Основні завдання дослідження:
1. Вивчення конструкції маніпулятора і теплового поля конвертера.
2. Розробка математичної моделі.
3. Експериментальна частина.
4. Аналіз результатів експерименту.
5.Рекомендаціі щодо практичного застосування.
3. Опис конструкції
Конструкція маніпулятора осьового типу для введення відсічних елементів в сталевипускний канал конвертера при випуску сталі показана на малюнку 1. Цей маніпулятор включає вертикальну колону 1, встановлену з можливістю повороту в нижній 2 і верхній 3 нерухомих підшипникових опорах і оснащену консоллю 4, на якій змонтований підшипниковий вузел 5 з вертикальним валом 6. На нижньому кінці цього вала жорстко закріплено кронштейн 7, що має дві поздовжні напрямні, в яких розміщені ролики каретки 8, що має можливість переміщення відносно направляючих і несучої порожнисої штанги 9. На передньому кінці штанги за допомогою подпружиненного фіксатора закріплений відсічний елемент 10. Механізм повороту кронштейна щодо консолі включає конічну зубчату пару 11 передавальним числом, рівним 1, що зв'язує вертикальний вал із заднім кінцем горизонтального вала 12, на передньому кінці якого жорстко закріплено конічне зубчасте колесо 13, що має можливість обкатування по конічній зубчастій шестірні 14 [2].
Ця шестерня жорстко пов'язана з нерухомою верхньою опорою вертикальної колони. Причому ставлення чисел зубів нерухомої конічної шестірні і конічного зубчастого колеса становить 2: 1. Зазначені співвідношення конструктивних елементів конічних передач дозволяють автоматично забезпечити одночасно при повороті колони з консоллю на кут 90 град, з вихідного положення відносний поворот кронштейна на 180 град., В результаті чого консоль і кронштейн будуть зорієнтовані в лінію і займуть співвісние положення з кисневим конвертером, як показано на малюнку 1б. Подальшу доставку відсічного елемента в зону розташування сталевипускного каналу конвертера (рис. 1в) здійснюють переміщенням каретки з порожнистою штангою відносно кронштейна за допомогою ланцюгового приводу [3].
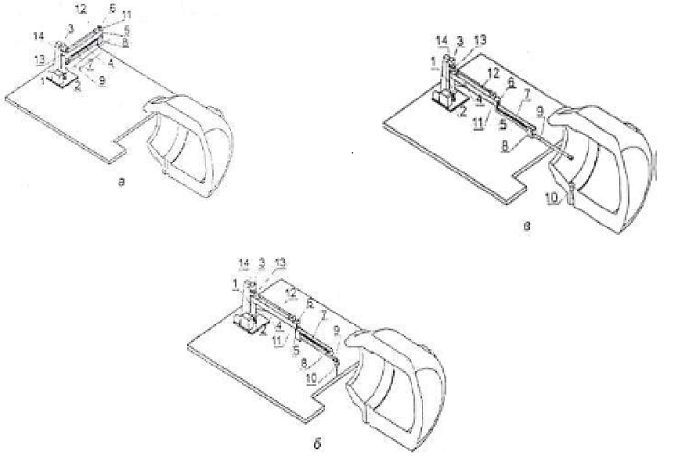
Малюнок 1 - Пристрій маніпулятора осьового типу і розташування його елементів у вихідному (а), проміжному (б), і кінцевому (в) положеннях
4. Огляд досліджень по темі
Співробітниками кафедри МОЗЧМ [4] була розроблена математична модель температурного поля для дослідження напружено-деформованого стану ланок маніпулятора з урахуванням реальних навантажень, що діють на елементи під час роботи. Визначальним фактором напружено-деформованого стану штанги маніпулятора є її температура, тому правильність виконаних розрахунків можливо оцінити за допомогою перевірки адекватності математичної моделі температурного поля.
Так як в виробничих умовах конвертерного цеху провести вимірювання температур в штанзі маніпулятора для введення відсічних елементів не представлялося можливим, то перевірку адекватності математичної моделі температурного поля виконували в лабораторії на фізичній моделі. Як фізична модель штанги була обрана труба з нержавіючої сталі з наступними геометричними параметрами: зовнішній діаметр 32 мм, товщина стінки 6 мм, довжина 250 мм.
Експеримент проводився в наступному порядку. Труба з забитими термопарами встановлювалася на штативі за допомогою утримувача. Виконувався розігрів електропечі до температури 900 ° С і піч переводилася в режим витримки. Ділянка труби завдовжки 180 мм через завантажувальний отвір печі заводився в нагрівальну камеру, де витримувався протягом 10 с. При цьому кожні 2 з. виконувалася реєстрація температури за допомогою вимірювальних приладів.
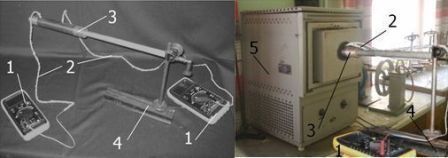
Малюнок 2 – Фотографії штанги з забитими термопарами, встановленої на штативі, (а)
і лабораторного комплексу (б):
1 - вимірювальний прилад; 2 - термопари; 3 - труба, що імітує штангу маніпулятора; 4 - штатив; 5 - електропіч
Далі труба виводилася з нагрівальної камери, і відбувалося її охолодження на відкритому повітрі протягом 10 хв. Реєстрація температури в контрольних точках виконувалася кожну хвилину.
Така схема термічного впливу повторювалася до тих пір, поки відносне відхилення температур в контрольних точках для сусідніх циклів стало менше 5%, що відповідало встановлення квазістаціонарного стану. На рис.5 наведені графіки зміни температур в трьох контрольних точках №1 (рис.5 а), №2 (рис.5 б), №3 (рис.5 в). Видно, що квазістаціонарний режим настав після 10 циклу навантаження. При цьому максимальна температура на поверхні труби для періоду нагріву склала 163 °С, а для періоду охолодження температура знизилася до 132 °С.
Після проведення лабораторних досліджень були проведені розрахунки температурного поля труби за допомогою розробленої математичної моделі [4]. При цьому дані про теплофізичних властивостях матеріалу труби взяли по [5]. В результаті моделювання отримано розподіл температури по поперечному перерізі труби. Для трьох контрольних точок №1 (рис.6 а, б), №2 (рис.6 в, г) і №3 (рис.6 д, е) показано порівняння розрахованих і виміряних значень температури при квазістаціонарному режимі (10 цикл навантаження в фізичному експерименті). Відносне відхилення виміряних і розрахункових значень для періоду нагріву і періоду охолодження склало 3,6 - 6,4%.
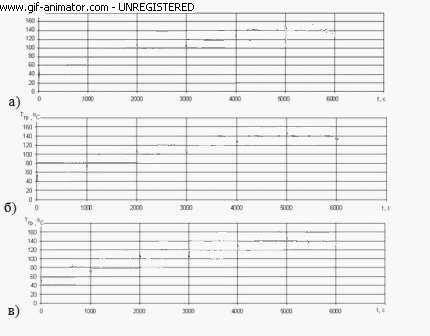
Малюнок 3 - Графіки зміни температур в контрольних точках
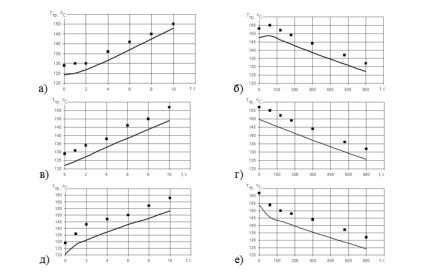
Малюнок 4 - Порівняння розрахованих (-) і виміряних (& bull;) значень температури для періодів нагріву і охолодження в контрольних точках
Таким чином, проведені дослідження підтверджують адекватність математичної моделі температурних полів, і дозволяє використовувати її для розрахунків при проектуванні маніпуляторів для введення відсічних елементів в ванну кисневого конвертера під час випуску сталі. Розроблений лабораторний комплекс і методи дослідження дозволяють вивчати вплив температур на елементи металургійних машин схильних до теплового впливу.
5. Основна частина
Зростання попиту на високоякісні марки сталі є головною проблемою, як для металургів, так і для проектувальників металургійного обладнання. Однією з найважливіших завдань, що вимагають рішення в умовах сучасного конвертерного виробництва сталі, є зменшення кількості кінцевого технологічного шлаку, що потрапляє в розливний ківш за час випуску рідкого металу з кисневого конвертера. Ефективність застосовуваних способів, що запобігають процессу потрапляння шлакового розплаву в ківш на кінцевій стадії випуску плавки багато в чому визначається технічними можливостями механічних систем, призначених для відсічення кінцевого шлаку [6].
Один з новітніх маніпуляторів для відсічення кінцевого шлаку з використанням елементів поплавкового типу фірми «Monocon» показаний на малюнку 5. При введенні поплавка в кисневий конвертер всі ланки маніпулятора відчувають значні теплові навантаження, в найбільш несприятливих умовах знаходиться порожниста штанга маніпулятора. Велика температура може привести до деформації конструкції і спричинить за собою погіршення точності позиціювання, що є важливим критерієм при скиданні поплавка в сталевипускний отвір.
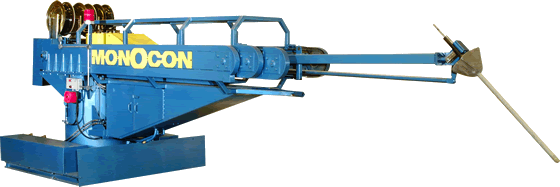
Малюнок 5 - Маніпулятора для введення відсічних елементів в ванну кисневого конвертера
Одним з найбільш навантажених місць в маніпуляторі для введення відсічного елемента є його штанга над якою і проводився експеремент. Штанга маніпулятора, на якій закріплений відсічний елемент, конструктивно являє собою трубу. У процесі введення елемента в ванну конвертера штанга піддається впливу теплових потоків, що призводить до виникнення в ній температурних напружень. Особливість роботи маніпулятора полягає в циклічному повторенні дій, при цьому тривалість нагріву штанги становить 40 с, тривалість охолодження 40 хв. Тому при конструюванні штанги за критеріями міцності (вибір матеріалу, розмірів поперечного перерізу) слід враховувати циклічність теплового впливу. В роботі [7] представлена математична модель і результати розрахунку розподілу температури по поперечному перерізі штанги. Не менш важливим є знання розподілу температури по довжині штанги, що можливо має нерівномірний характер, що викликано неоднаковим тепловим потоком в порожнині конвертера і за його межами. Для підтвердження висунутої гіпотези про характер розподілу температури по довжині штанги були проведені експерименти в умовах лабораторії на фізичної моделі. Як фізичне моделі штанги була обрана труба з нержавіючої сталі з наступними геометричними параметрами: зовнішній діаметр 24 мм, товщина стінки 2 мм, довжина 450 мм. Протягом 40 з в електропечі, що забезпечує температуру внутрішньої пічної середовища 250 °С, виконувався нагрів ділянки труби завдовжки 200 мм. Охолодження труби відбувалося на відкритому повітрі при кімнатній температурі протягом 5 хв. На поверхні труби було нанесено 9 контрольних точок. Вимірювання температури виконувалося тепловізором. Похибка вимірювання становила ± 1 °С. Експеримент включав 5 циклів термічного навантаження. На малюнку 6 наведені термограмми для 1-го і 6-го циклів нагрівання труби, а на малюнку 4 представлені графіки зміни температури по довжині труби після кожного циклу нагріву.
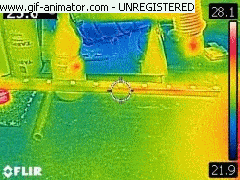
Малюнок 6 - Термограмми труби після 1-го (а) і 6-го (б) циклу навантаження
(анімація: 7 кадрів, 5 циклів повторення, 142 кілобайт)
Аналіз результатів вимірювання показав, що після першого введення труби в піч максимальний нагрів відбувається на ділянці 150 мм. Тут температура зросла на 8 ... 24% щодо вихідного стану. Температура на ділянці труби, розташованому за межами печі (300 ... 400 мм), залишилася практично незмінною. Центральну ділянку - перехідну від зони з високою температурою до зони з більш низькою температурою, тому тут можливе утворення концентраторів напружень, викликаних перепадом температури. Після 2-го циклу нагріву труби відзначається рівномірне збільшення температури по всій довжині труби на 5,4 ... 6,8% щодо значень, досягнутих при першому введенні в піч. Третій цикл нагріву труби привів до підвищення температури на 2,3 ... 4,4% на ділянці, що вводиться в піч. Температура ділянки труби, що знаходиться на відкритому повітрі, практично не змінилася.
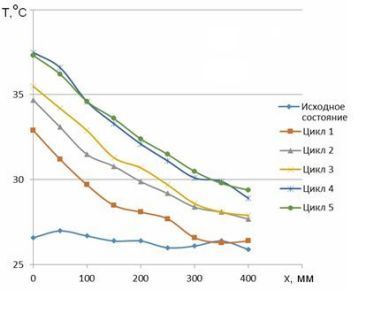
Малюнок 7 - Графік зміни температури (Т) по довжині (х) штанги після кожного циклу нагріву
Після 4-го введення в піч відбулася однакова зміна температури по всій довжині труби, температура зросла в середньому на 5,4%. П'ятий цикл нагріву практично не привів до зростання температури. В цілому, максимальна зміна температури труби відбувається після першого циклу нагріву, хоча після 5-го нагрівання температура зростає ще в 1,3 ... 1,6 рази.
Висновки
Отримані експериментальні дані будуть використані при перевірці адекватності розробляємої автором математичної моделі розподілу температури в штанзі маніпулятора для введення відсічних елементів в кисневий конвертер при її циклічному нагріванні. Дана модель дозволить уточнити уявлення про напружено-деформований стан штанги і розробити рекомендації щодо вибору оптимальних геометричних параметрів штанги і марок сталі для її виготовлення. При написанні даного реферату магістерська робота ще не завершена. Остаточне завершення: червень 2018 року. Повний текст роботи та матеріали по темі можуть бути отримані у автора або його керівника після зазначеної дати.
Перелік посилань
- Опыт разработки систем отсечки шлака для сталеплавильных агрегатов / С.П. Еронько, А.Ю. Цупрун, С.А. Бедарев, С.В. Мечик // «Черметинформация». Бюллетень «Черная металлургия», 2007. – вып. 9, – С. 81 – 87.
- Еронько С. П., Смирнов А.Н., Кукуй Д.П. Разработка эффективных схем отсечки шлака при сливе металла из конвертера // Металлургическая и горнорудная промышленность. - 2003. - №8. - С. 33 – 37.
- Опыт разработки систем отсечки шлака для сталеплавильных агрегатов / С.П. Еронько, А.Ю. Цупрун, С.А. Бедарев и др. // ОАО «Черметинформация». Бюлл. «Черная металлургия» - 2007 - № 9 - С. 81 – 87.
- Исследование напряженно-деформированного состояния звеньев манипулятора для ввода отсечных элементов в выпускной канал конвертера / Еронько С.П., Ошовская Е.В., Бедарев С.А., Мечик С.В. // Металлургическая и горнорудная промышленность. – 2007.– №5. – С. 107 – 111.
- Теплофизические свойства веществ. Справочник / Под ред. Н.Б. Варгафтика. – Л.: Гос.энергетическое изд-во, 1956. – C. 367.
- Использование математического моделирования и САПР при разработке устройства устройства для отсечки конвертерного шлака / С.П. Еронько, Е.В. Ошовская, В.В. Киселев и др. // Прогрессивные технологии и системы машиностроения: Сборник научных трудов - Донецк: ДонГТУ, 2002 - № 23 - С. 52 – 56.
- Исследование напряженно-деформированного состояния звеньев манипулятора для ввода отсечных элементов в выпускной канал конвертера / Еронько С.П., Ошовская Е.В., Бедарев С.А., Мечик С.В. // Металлургическая и горнорудная промышленность. – 2007.– №5. – С. 107 – 111.