Реферат
Содержание
- Введение
- 1. Актуальность темы
- 2. Цель и задачи исследования, планируемые результаты
- 3. Описание конструкции
- 4. Обзор исследований по теме
- 5. Основная часть
- Выводы
- Список источников
Введение
В сталеплавильном производстве за последнее время произошли коренные изменения в связи с заменой мартеновского способа, выплавки стали кислородно-конвертерным, созданием крупных конвертерных агрегатов, мощных электросталеплавильных печей и новых установок по специальной металлургии, разработкой и широким внедрением машин непрерывного литья заготовок. В связи с увеличением объёма производства и улучшении качества стали исключительно важная роль принадлежит кислородно-конвертерному производству, имеющему высокие технико-экономические показатели – высокую производительность при меньших капитальных затратах по сравнению с мартеновским способом, более благоприятные условия для автоматизации. Производительность одного 400 т конвертера превышает производительность целого мартеновского цеха с 8-10 печами вместимостью 600 т каждая. Конвертерный способ выплавки стали непрерывно совершенствуется. Современная технология выплавки стали в конвертере предусматривает отсечку шлака при выпуске стали из конвертера. Существуют несколько способов отсечки шлака, для каждого из которых разработано и эксплуатируется специальное оборудование. В этой работе рассматривается манипулятор осевого типа для ввода отсечных элементов в сталевыпускной канал конвертера при выпуске стали.
1. Актуальность темы
В наиболее неблагоприятных условиях в момент ввода в конвертер отсечного элемента находится полая штанга, в теле которой возникают значительные температурные и механические напряжения. Деформации изгиба штанги обусловлены действием силы тяжести отсечного элемента. Многократное чередование нагрева и охлаждения (20 - 25 раз в сутки), способствующее появлению, наряду с термическими, фазовых напряжений, в результате чего штанга искривляется, а на ее поверхности образуется сетка разгара и появляются трещины, постепенно развивающиеся в глубину и ослабляющие сечение детали. В итоге срок службы штанги резко сокращается и ее приходится отбраковывать [1].
Для повышения стойкости полой штанги необходимы оптимизация ее конструктивного исполнения, правильный выбор материала и метода упрочнения, которые могли бы способствовать повышению сопротивляемости изделия циклическим тепловым изменениям и обеспечить требуемую жесткость системы. Поэтому наличие информации о характере и абсолютных значениях изменений температуры по длине, периметру и сечению этого звена манипулятора в процессе его эксплуатации даст возможность при расчете и конструировании не только аргументировано обосновать выбор материала для изготовления, но и правильно назначить метод и режим упрочнения ответственной детали.
2.Цель и задачи исследования, планируемые результаты
Целью исследования является усовершенствование конструкции манипулятора для повышения безотказности, изучение температурного поля действующего на штангу манипулятора в кислородном конвертере. Основные задачи исследования:
1. Изучение конструкции манипулятора и теплового поля конвертера.
2. Разработка математической модели.
3. Экспериментальная часть.
4. Анализ результатов эксперимента.
5.Рекомендации по практическому применению.
2. Описание конструкции
Конструкция манипулятора осевого типа для ввода отсечных элементов в сталевыпускной канал конвертера при выпуске стали показана на рисунке 1. Этот манипулятор включает вертикальную колонну 1, установленную с возможностью поворота в нижней 2 и верхней 3 неподвижных подшипниковых опорах и оснащенную консолью 4, на которой смонтирован подшипниковый узел 5 с вертикальным валом 6. На нижнем конце этого вала жестко закреплен кронштейн 7, имеющий две продольные направляющие, в которых размещены ролики каретки 8, имеющей возможность перемещения относительно направляющих и несущей пустотелую штангу 9. На переднем конце штанги с помощью подпружиненного фиксатора закреплен отсечной элемент 10. Механизм поворота кронштейна относительно консоли включает коническую зубчатую пару 11 передаточным числом, равным 1, связывающую вертикальный вал с задним концом горизонтального вала 12, на переднем конце которого жестко закреплено коническое зубчатое колесо 13, имеющее возможность обкатывания по конической зубчатой шестерне 14 [2].
Эта шестерня жестко связана с неподвижной верхней опорой вертикальной колонны. Причем отношение чисел зубьев неподвижной конической шестерни и конического зубчатого колеса составляет 2:1. Указанные соотношения конструктивных элементов конических передач позволяют автоматически обеспечить одновременно при повороте колонны с консолью на угол 90 град, из исходного положения относительный поворот кронштейна на 180 град., в результате чего консоль и кронштейн будут сориентированы в линию и займут соосное положение с кислородным конвертером, кик показано на рисунке 1б. Последующую доставку отсечного элемента в зону расположения сталевыпускного канала конвертера (рис. 1в) осуществляют перемещением каретки с полой штангой относительно кронштейна с помощью цепного привода [3].
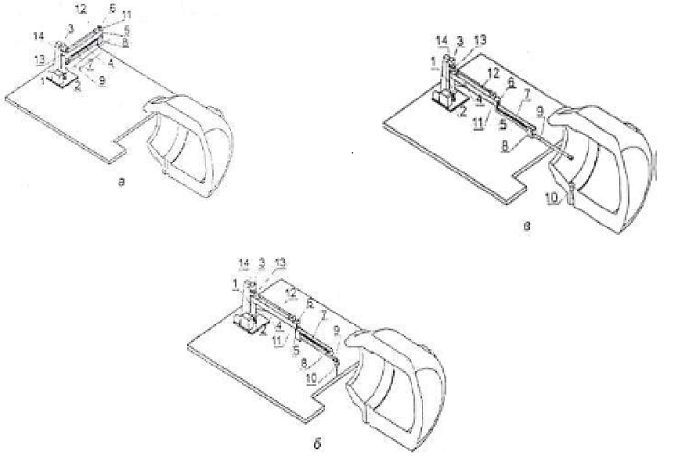
Рисунок 1 - Устройство манипулятора осевого типа и расположение его элементов в исходном (а), промежуточном (б), и конечном (в) положениях
4. Обзор исследований по теме
Сотрудниками кафедры МОЗЧМ [4] была разработана математическая модель температурного поля для исследования напряженно-деформированного состояния звеньев манипулятора с учетом реальных нагрузок, действующих на элементы во время работы. Определяющим фактором напряженно-деформированного состояния штанги манипулятора является ее температура, поэтому правильность выполненных расчетов возможно оценить с помощью проверки адекватности математической модели температурного поля.
Так как в производственных условиях конвертерного цеха провести измерения температур в штанге манипулятора для ввода отсечных элементов не представлялось возможным, то проверку адекватности математической модели температурного поля выполняли в лаборатории на физической модели. В качестве физической модели штанги была выбрана труба из нержавеющей стали со следующими геометрическими параметрами: наружный диаметр 32 мм, толщина стенки 6 мм, длина 250 мм.
Эксперимент проводился в следующем порядке. Труба с заделанными термопарами устанавливалась на штативе с помощью держателя. Выполнялся разогрев электропечи до температуры 900 °С и печь переводилась в режим выдержки. Участок трубы длиною 180 мм через загрузочное отверстие печи заводился в нагревательную камеру, где выдерживался в течении 10 с. При этом каждые 2 с. выполнялась регистрация температуры с помощью измерительных приборов.
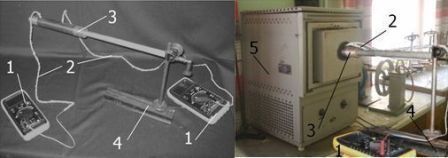
Рисунок 2 – Фотографии штанги с заделанными термопарами, установленной на штативе, (а) и лабораторного комплекса (б): 1 – измерительный прибор; 2 – термопары; 3 – труба, имитирующая штангу манипулятора; 4 – штатив; 5 – электропечь
Далее труба выводилась из нагревательной камеры, и происходило ее остывание на открытом воздухе в течение 10 мин. Регистрация температуры в контрольных точках выполнялась каждую минуту.
Такая схема термического воздействия повторялась до тех пор, пока относительное отклонение температур в контрольных точках для соседних циклов стало менее 5%, что соответствовало установлению квазистационарного состояния. На рис.5 приведены графики изменения температур в трех контрольных точках №1 (рис.5 а), №2 (рис.5 б), №3 (рис.5 в). Видно, что квазистационарный режим наступил после 10 цикла нагружения. При этом максимальная температура на поверхности трубы для периода нагрева составила 163 °С, а для периода охлаждения температура снизилась до 132 °С.
После проведения лабораторных исследований были проведены расчеты температурного поля трубы с помощью разработанной математической модели [4]. При этом данные о теплофизических свойствах материала трубы приняли по [5]. В результате моделирования получено распределение температуры по поперечному сечению трубы. Для трех контрольных точек №1 (рис.6 а, б), №2 (рис.6 в, г) и №3 (рис.6 д, е) показано сравнение рассчитанных и измеренных значений температуры при квазистационарном режиме (10 цикл нагружения в физическом эксперименте). Относительное отклонение измеренных и расчетных значений для периода нагрева и периода охлаждения составило 3,6 - 6,4 %.
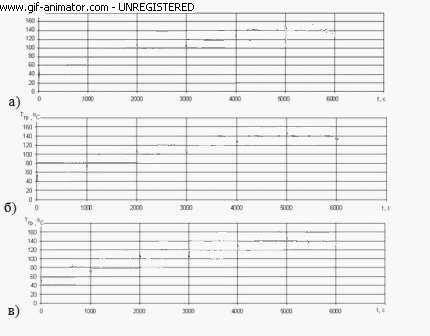
Рисунок 3 - Графики изменения температур в контрольных точках
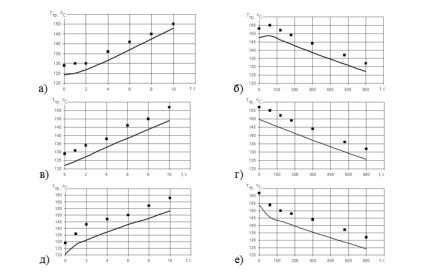
Рисунок 4 – Сравнение рассчитанных (–) и измеренных (•) значений температуры для периодов нагрева и охлаждения в контрольных точках
Таким образом, проведенные исследования подтверждают адекватность математической модели температурных полей, и позволяет использовать ее для расчетов при проектировании манипуляторов для ввода отсечных элементов в ванну кислородного конвертера во время выпуска стали. Разработанный лабораторный комплекс и методы исследования позволяют изучать влияние температур на элементы металлургических машин подверженных тепловому воздействию.
3. Основная часть
Возрастающая потребность на высококачественные марки стали являются первостепенной задачей как для металлургов, так и для проектировщиков металлургических установок. Одной из важных проблем которая требует решения в условиях нынешнего конвертерного изготовления металла, является такая задача как уменьшение попадания конечного шлака, попадающего в разливочный ковш за период, выпуска стали из кислородного конвертера. Эффективность нынешних способов, предотвращающих процесс попадания расплава шлака в ковш на конечном этапе выпуска жидкого металла во многом определяется техническими ресурсами механических установок, разработанных для отсечки конечного шлака [6].
Один из новейших манипуляторов для отсечки конечного шлака с использованием элементов поплавкового типа фирмы «Monocon» показан на рисунке 5. При вводе поплавка в кислородный конвертер все звенья манипулятора испытывают значительные тепловые нагрузки, в наиболее неблагоприятных условиях находится полая штанга манипулятора. Большая температура может привести к деформации конструкции и повлечет за собой ухудшение точности позиционирования, что есть не маловажным критерием при сбросе поплавка в сталевыпускное отверстие.
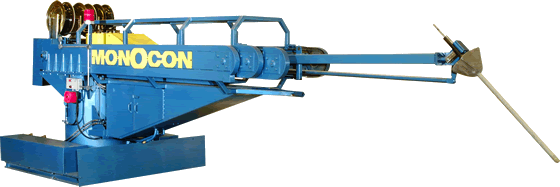
Рисунок 5 - Манипулятора для ввода отсечных элементов в ванну кислородного конвертера
Одним из самых нагруженных мест в манипуляторе для ввода отсечного элемента является его штанга над которой и проводился эксперемент. Штанга манипулятора, на которой закреплен отсечной элемент, конструктивно представляет собой трубу. В процессе ввода элемента в ванну конвертера штанга подвергается воздействию тепловых потоков, что приводит к возникновению в ней температурных напряжений. Особенность работы манипулятора заключается в циклическом повторении действий, при этом длительность нагрева штанги составляет 40 с, длительность охлаждения 40 мин. Поэтому при конструировании штанги по критериям прочности (выбор материала, размеров поперечного сечения) следует учитывать цикличность теплового воздействия. В работе [7] представлена математическая модель и результаты расчета распределения температуры по поперечному сечению штанги. Не менее важным является знание распределения температуры по длине штанги, которое предположительно имеет неравномерный характер, что вызвано неодинаковым тепловым потоком в полости конвертера и за его пределами. Для подтверждения выдвинутой гипотезы о характере распределения температуры по длине штанги были проведены эксперименты в условиях лаборатории на физической модели. В качестве физической модели штанги была выбрана труба из нержавеющей стали со следующими геометрическими параметрами: наружный диаметр 24 мм, толщина стенки 2 мм, длина 450 мм. В течение 40 с в электропечи, обеспечивающей температуру внутренней печной среды 250 °С, выполнялся нагрев участка трубы длиною 200 мм. Охлаждение трубы происходило на открытом воздухе при комнатной температуре в течение 5 мин. На поверхности трубы было нанесено 9 контрольных точек. Измерение температуры выполнялось тепловизором. Погрешность измерения составляла ±1 °С. Эксперимент включал 5 циклов термического нагружения. На рисунке 3 приведены термограммы для 1-го и 5-го циклов нагрева трубы, а на рисунке 4 представлены графики изменения температуры по длине трубы после каждого цикла нагрева.
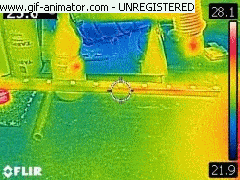
Рисунок 6 – Термограммы трубы после 1-го (а) и 5-го (б) цикла нагружения
(анимация: 7 кадров, 5 циклов повторения, 142 килобайт)
Анализ результатов измерения показал, что после первого ввода трубы в печь максимальный нагрев происходит на участке 150 мм. Здесь температура возросла на 8…24% относительно исходного состояния. Температура на участке трубы, расположенном за пределами печи (300…400 мм), осталась практически неизменной. Центральный участок – переходной от зоны с высокой температурой к зоне с более низкой температурой, поэтому здесь возможно образование концентраторов напряжений, вызванных перепадом температуры. После 2-го цикла нагрева трубы отмечается равномерное приращение температуры по всей длине трубы на 5,4…6,8% относительно значений, достигнутых при первом вводе в печь. Третий цикл нагрева трубы привел к повышению температуры на 2,3…4,4% на участке, вводимом в печь. Температура участка трубы, находящегося на открытом воздухе, практически не изменилась.
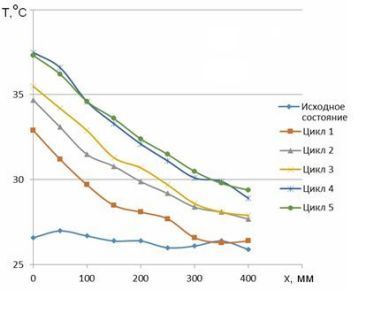
Рисунок 7 – График изменения температуры (Т) по длине (х) штанги после каждого цикла нагрева
После 4-го ввода в печь произошло одинаковое изменение температуры по всей длине трубы, температура возросла в среднем на 5,4%. Пятый цикл нагрева практически не привел к росту температуры. В целом, максимальное изменение температуры трубы происходит после первого цикла нагрева, хотя после 5-го нагрева температура возрастает еще в 1,3…1,6 раза.
Выводы
Полученные экспериментальные данные будут использованы при проверке адекватности разрабатываемой автором математической модели распределения температуры в штанге манипулятора для ввода отсечных элементов в кислородный конвертер при её циклическом нагреве. Данная модель позволит уточнить представления о напряженно-деформированном состоянии штанги и разработать рекомендации по выбору оптимальных геометрических параметров штанги и марок стали для её изготовления. При написании данного реферата магистерская работа еще не завершена. Окончательное завершение: июнь 2018 года. Полный текст работы и материалы по теме могут быть получены у автора или его руководителя после указанной даты.
Список источников
- Опыт разработки систем отсечки шлака для сталеплавильных агрегатов / С.П. Еронько, А.Ю. Цупрун, С.А. Бедарев, С.В. Мечик // «Черметинформация». Бюллетень «Черная металлургия», 2007. – вып. 9, – С. 81 – 87.
- Еронько С. П., Смирнов А.Н., Кукуй Д.П. Разработка эффективных схем отсечки шлака при сливе металла из конвертера // Металлургическая и горнорудная промышленность. - 2003. - №8. - С. 33 – 37.
- Опыт разработки систем отсечки шлака для сталеплавильных агрегатов / С.П. Еронько, А.Ю. Цупрун, С.А. Бедарев и др. // ОАО «Черметинформация». Бюлл. «Черная металлургия» - 2007 - № 9 - С. 81 – 87.
- Исследование напряженно-деформированного состояния звеньев манипулятора для ввода отсечных элементов в выпускной канал конвертера / Еронько С.П., Ошовская Е.В., Бедарев С.А., Мечик С.В. // Металлургическая и горнорудная промышленность. – 2007.– №5. – С. 107 – 111.
- Теплофизические свойства веществ. Справочник / Под ред. Н.Б. Варгафтика. – Л.: Гос.энергетическое изд-во, 1956. – C. 367.
- Использование математического моделирования и САПР при разработке устройства устройства для отсечки конвертерного шлака / С.П. Еронько, Е.В. Ошовская, В.В. Киселев и др. // Прогрессивные технологии и системы машиностроения: Сборник научных трудов - Донецк: ДонГТУ, 2002 - № 23 - С. 52 – 56.
- Исследование напряженно-деформированного состояния звеньев манипулятора для ввода отсечных элементов в выпускной канал конвертера / Еронько С.П., Ошовская Е.В., Бедарев С.А., Мечик С.В. // Металлургическая и горнорудная промышленность. – 2007.– №5. – С. 107 – 111.