The contents
- Introduction
- 1. Actuality of the problem
- 2. The purpose and research problems, the planned results
- 3. Main part
- Conclusion
- References
Introduction
The ceramics is the first artificial material received by the person. It was known from an extreme antiquity and was used generally for production of ware, decorative and household products. Later, in the 20th century, with development of technology the era of plastic and ceramics
came. So there was its technical version used in instrument making, electrical equipment, transport, power, mechanical engineering, medicine and other fields [1].
Diamond grinding is most efficiently allowance material removal in ceramic preparations owing to their high hardness. Big requirements for maintenance of sharpness of the cutting edges and preservation of a required form of a profile of a wheel are imposed to a grinding wheel as to the cutting tool,. If durability of fixing of abrasive grains in the tool is lower than durability of grains, then wear happens due to chipping of grains, and the wheel works in the self-sharpening mode. Self-sharpening call property of a wheel to keep cutting capacity owing to formation of the new cutting edges in processing. If durability of abrasive grains appears lower than durability of their fixing in a grinding wheel, then wear happens partially due to brittle destruction and pin together of grains, and partially — as a result of their abrasion by the processed material. Such wear names blunting of a wheel and consists in formation of platforms of wear on the surface of abrasive grains and reduction of cutting capacity of the tool that is shown in increase of cutting force up to two times. Besides, the uneven wear of a wheel leads to change of its profile. The instability of performance rates of a grinding wheel, it's change during processing of preparations leads them to change of quality of a surface layer of a workpiece. Therefore there is need for dressing of a grinding wheel [2].
1. Actuality of the problem
Dressing – the process of restoring the cutting capacity of the grinding wheel (GW) and the correction of geometric shape of the tool. The tools newly installed on the machine tool and blunt in machining are subjected to the dressing. The correction is spent from 45% to 80% of the useful volume of the GW. Expenses for dressing can reach up to 40% of the unit's processing time and more. At this time, the following basic methods of dressing are most well known [3]:
Physical and chemical methods of straightening have a number of disadvantages[4]:
Numerous mechanical ways of dressing act as an alternative to physical and chemical ways of dressing. Mechanical
Dressing by a free abrasive has a number of advantages in comparison with other mechanical ways of impact on a working surface of a wheel:
The insufficient amount of information about process of interaction of a free abrasive and working surface of a diamond grinding wheel at its dressing doesn't allow to choose rational conditions for its carrying out.
2. The purpose and research problems, the planned results
Research objective is increase of process productivity of dressing by a free abrasive due to determination of rational parameters of process of influence of a free abrasive on wheel working surface.
Main objectives of a research:
- Development of design of the device for dressing by a free abrasive.
- To experimentally investigate of influence probability of charging of a free abrasive in a surface of a hone on productivity of process of dressing and influence of kinematic parameters of process of dressing on probability of use of an abrasive.
- Choice of the rational dressing conditions for dressing of diamond wheels.
Research object: process of dressing of a diamond grinding wheel free abrasive.
Object of research: process of interaction of a free abrasive with hone and a working surface of a diamond grinding wheel at its dressing.
3. Main part
Dressing by a free abrasive is quite difficult technological process which is directed to recovery of cutting capacity of a wheel. Process of work of GW can be separated into 2 stages:
- A stage of grinding of workpiece preparation with loss of cutting capacity of a wheel.
- Process of recovery of cutting capacity of a wheel (dressing of a wheel).
Both stages of work of a wheel can be presented in the form of the scheme provided on the figure 1.
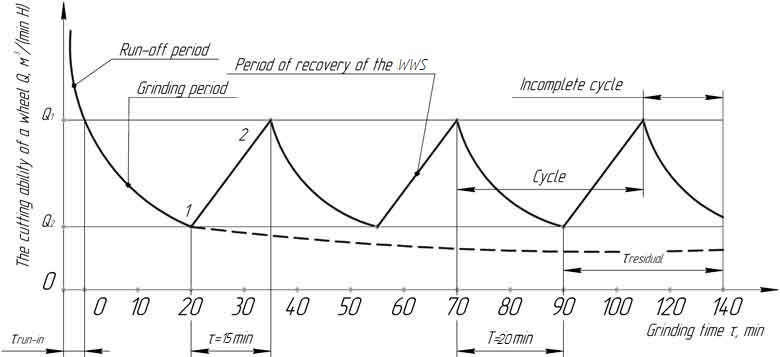
Figure 1 – Change in time of the current cutting capacity of a wheel using electroerosive action (EEA) [11]
The period 0 – τ1 corresponds to a stage work wheel surface (WWS) extra earnings. The stage extra earnings is characterized by the greatest value of cutting capacity of WWS and intensive wear of a working layer of a wheel. The stage extra earnings is considered finished when the current cutting capacity of a wheel reaches a certain Q1 value.
The stage τ1 – τ2 describes change of the current limited cutting capacity of a wheel in grinding. The value of time τ2 corresponds to value of cutting capacity of a wheel Q2, at which recovery of cutting capacity of a wheel begins.
The stage τ2 – τ3 describes the change in the current cutting ability of the wheel when the EEA is introduced into the cutting zone simultaneously with the machining process. In this case, the cutting ability of the wheel is restored from the value Q2 to Q1. This period is characterized by an intensive increase of cutting capacity due to the removal of products of greasing the wheel and particles of bond, which also leads to an intensification of the working layer of the wheel.
In timepoint τ3, when the current cutting capacity reaches a reference preset value of Q1, continue work in the mode of normal grinding before the next falling of cutting capacity to the Q2, level then the cycle is repeated [11].
When processing preparations change the current cutting capacity of wheels of Q(τ) when grinding can be described are described by exponential dependences of a look [11]:
where Q(τ), Qin, Qest– respectively the current, initial and established value of cutting capacity of a wheel; ΔQ = Qin–Qest – amplitude of decrease in cutting capacity, mm3/min; βQ – empirical coefficient, 1/min; τ – duration of grinding, min.
At recovery of cutting capacity of WWS at the expense of EEA, increase in cutting capacity of WWS and growth of the current drain of diamonds is described by linear dependences of such kind [11]:
Duration of the period of work of a wheel to a state at which it is necessary to dress the diamond grinding wheel depends on physical and mechanical properties of material being machined, on the characteristics of the wheel and on dressing conditions.
For reduction of time of recovery of cutting capacity of WWS it is recommended to carry out impact of a free abrasive on the working surface of a wheel at the dressing conditions to be rational for these machining process (speeds of a hone and abrasive). Impact of a free abrasive on WWS needs to be stopped when cutting capacity of a wheel reaches the determined, set level that will allow to exclude an excessive drain of diamonds and an irrational expense of a dressing abrasive.
Apparently from schedules (fig. 1), the period of recovery of WWS quite big therefore there is a need for modeling of process of dressing and determination of parameters which influence on reductions of process time.
Conclusion:
The master's thesis is devoted to a research of increase in productivity of dressing due to the choice of rational parameters of process of impact of a free abrasive on wheel working surface. When writing this paper the master's thesis isn't completed yet. Final end: June, 2018. The full text of work and materials on a subject can be received from the author or his scientific supervisor after the specified date.
References
- Библиотека Машиностроителя. Керамика. Ее свойства и применение // [Электронный ресурс] – Режим доступа: https://lib-bkm.ru/publ/26-1-0-1719.
- Попов, С. А. Шлифовальные работы / С. А. Попов. – М.: Высшая школа,1987.383 с.
- Полтавец, В.В. Повышение степени управляемости технологической системой шлифования кругами из сверхтвердых материалов за счет воздействий на характеристики инструмента / В. В. Полтавец // Наукові праці ДонНТУ. Серія Машинобудування і машинознавство. Випуск 6 (154). Донецьк: ДонНТУ, 2009. – С.79–86.
- Матюха, П. Г. Устройство для электроэрозионной правки кругов на металлической связке / П. Г. Матюха, В. П. Цокур // Науч.-техн. реферативный сб. «Электрические и электрохимические методы обработки». – М.НИИМАШ. – 1981. – Вып.8. – С.2 –3.
- А.с. 1839393 СССР. Способ правки абразивного инструмента / Бурмистров В. В., Байков А. В., Емельянов А. Н., Калафатова Л. П., Хроменко А. Д. // Бюл. – 1993. – № 47–48. – 2 с.
- Пат. 97700Укр. Способ правки шлифовальных кругов свободным абразивом / Гусев В. В., Вяльцев М. В., Молчанов А.Д., Медведев А. Л., Семенюк Д. Ю. // Бюл. – 2012. – №5.
- Пат. 96351Укр. Способ правки шлифовальных кругов свободным абразивом / Гусев В. В., Вяльцев М. В., Молчанов А. Д., Медведев А. Л., Семенюк Д. Ю., Калафатова Л. П. // Бюл. – 2011. – №20.
- А.с.1668121 СССР. Способ правки абразивного интсрумента/ В.В. Бурмистров, А.Д. Хроменко, В.В. Мащенко, Е.М. Сировский // Бюл.– 1991. – № 29. – 3 с.
- Пат. 99526 Укр. Способ правки шлифовального круга/ Гусев В. В., Вяльцев М.В., Молчанов А. Д., Медведев А. Л., Тупик А. Л., Калафатова Л. П. // Бюл. – 2012. – №26.
- Пат. 3838 Укр. Способ правки шлифовального инструмента / Калафатова Л. П., Шевченко В. А., Поезд С. А. // Бюл. – 2004. – №12.
- Матюха П.Г., Шлифование труднообрабатываемых материалов кругами из алмазов и эльбора. Монография / П.Г. Матюха, В.В. Полтавец, А.В. Бурдин, В.В. Габитов. – Черкаси.: Вертикаль, 2015. – 251 с.