Abstract
Contents
- Introduction
- 1.The relevance of the topic
- 2.The purpose and research tasks, planned results
- 3.Review of existing development
- 4.The method of solving the problem and current results
- 5.Development of the algorithm of ACS
- Conclusions
- References
Introduction
Blast furnace production is a complex multistage process, consisting of a set of specialized operations for processing of various materials. Due to continuity, the high degree of mechanization, large saturation test and measurement equipment blast furnace process is well prepared for automatic control.
The main objective in the management domain process is the stabilization of the thermal state of the furnace, resulting in the constancy of the productivity of the furnace, composition and temperature product of melting.
Because of the research of this process, as well as centuries of experience, currently achieved good quality understanding of the whole process.
However, existing knowledge is not used fully, therefore it needs to development of better information-measuring systems, as well as means of real-time calculation of optimum modes of melting and loading on the basis of its mathematical models.
1.The relevance of the topic
A characteristic feature of blast furnace production is to maintain practically constant the productivity of the furnace and the composition of cast iron. This constancy requires the stabilization of blast parameters and download parameters.
As the control object has a large inertia and time delay, it greatly complicates management, especially on top
and requires the using of all possible information on the progress of the blast furnace process to predict changes in the thermal state and other parameters.
For smooth descent of the charge in the furnace, uniform distribution of gas flow over the cross section of the mine and the stabilization of this charge mode is necessary to provide the desired distribution of material around the perimeter of the furnace top, as well as the necessary level of the surface of the grain bill batch.
Since the rate of download is a mismatch between the specified and the actual level of the grain bill, then the maintenance level of the grain bill of the charge – the distance from the edge of the large cone down to the surface of charge materials in the furnace is to regulate the system.
As this property has great transport delay on the control channel and indignation, as well as a large inertia, it is necessary to choose such control, which will be compensated by a time delay in the system to ensure that the information on progress was received on time and without delay. This task – compensation of the time delay is relevant.
Consider the process of the download rate from the point of view of material flow and information variables (Fig.1).
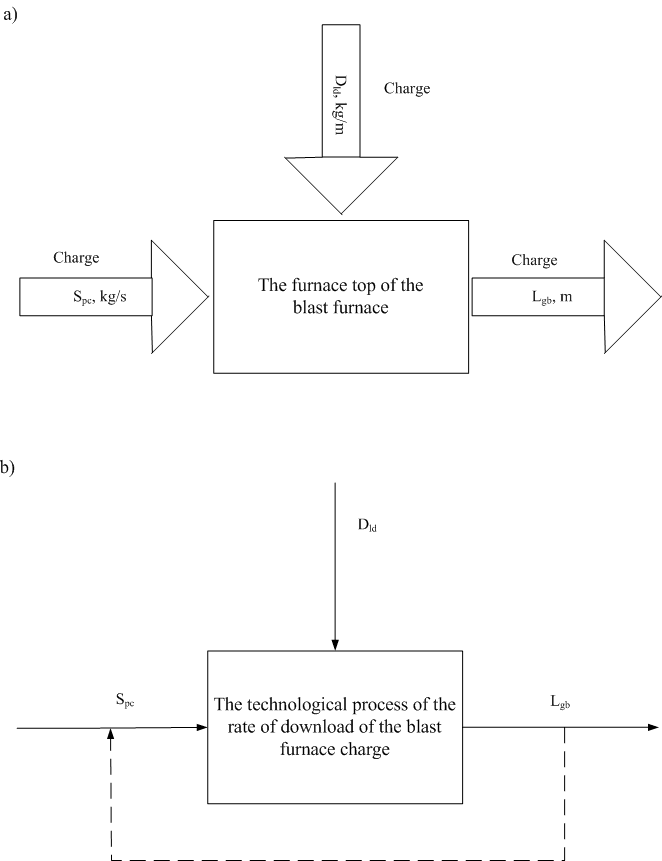
Figure 1 – Scheme of the analysis of the process rate of download of management:
a) scheme of material flow and information variables;
b) the block diagram of ACS
From the diagram analysis of the process rate of download, as object of management follows that the main information variables are:
- Spc – the performance of the conveyor (kg/s);
- Dld – linear density of material (kg/m), which is the perturbation to maintain the level of the grain bill on the furnace top.
Manipulated variable output is:
- Lgb – the level of the grain bill of the charge on the furnace top (m).
The source of information for the subsystem, the value of the specified level of the grain bill Lgb on the basis of which determines the speed of descent of the charge into the furnace at the furnace top Sft and the magnitude of the error is valid and the specified levels of the grain bill. Control is charge material enters the horizontal conveyor, that is, the performance of the conveyor Spc in accordance with the change of speed of descent of the charge in the blast furnaceSft [4]. Perturbation is the linear density of the charge Dld, which prevents maintaining the specified level of the grain bill on the furnace top. Based on the foregoing information and analysis of the structural scheme of the process (Fig 1 b), the implementation of ACS expedient to apply the principle of control by deviation from NF with compensation of delay in the system.
2.The purpose and research tasks, planned results
The goal is the safety of the production process, decrease the cost of smelting the pot and rational flow of materials to maintain the required level of the grain bill of the charge on the furnace top by regulating the flow of charge materials on the horizontal conveyor.
The basic functions performed by ACS:
- To maintain the necessary level of the grain bill batch.
- Automatic regulation of the flow of material in accordance with the level of the grain bill of the charge on the furnace top.
- Providing the communication between the architectural levels of the hierarchy system.
Object of study:rate of batch charging to the blast furnace.
3.Review of existing development
Automatic level control of the surface of the grain bill of the charge is an important factor for the development of systems of stabilization of this charge regime.
As this property has great transport delay, it can lead to the fact that information on progress is supplied to the regulator later than required which may lead to inadequacy of the closed-loop system. It is known that the complexity of the control objects with time delays characterized by the ratio of the amount of delay to constant time of the object: what it is – the harder it is to achieve the required quality of regulation.
To improve the quality of management of such objects possible in two ways:[5]
- reduce transport delay in the object by making design changes;
- use more complex control structures to reduce the negative impact of delay.
In practice, most often used the first way to improve quality control. First, replace the mechanical gauges, radiometric, or radar, as the radiometric sensor is not immersed in the charge, and taking gama-radiation absorbed by the charge. Second, try to replace the transportation of materials to the furnace top with the machines of periodic action machines with continuous action. Third, replace the cone the boot device bell-less tray-loading device, as cone constantly wear out, and they regularly need to fix. Basically all the disadvantages of the system pace download come from obsolete equipment and structures that are in need of modernization. With regard to the use of more complex structures management system allowing to reduce the negative impact of delay, it is known several methods of synthesis of control systems by objects with delay.
Most often used in practice:
- the method using the controller Risvic;
- the method of using the Smith predictor.
Controller Risvic and its modifications, despite pretty good results, has the drawback of the system is stable only when the exact equality of the delay element and a delay, modeled in the object, and the slightest violation of equality leads to a loss of stability [6]. It is therefore advisable to use the Smith predictor, because its implementation using standard PID-controller. Also, among the many solutions obtained for the prediction of controlled variable time delay, the Smith predictor (including modifications) received the most widespread [7], and due to the Smith predictor, we can predict the appearance of the signal at the output of the object before it will actually. Which implies that this method should ensure maintaining a specified level of the grain bill on the furnace top and timely testing of the regulator.
4.The method of solving the problem and current results
To manage objects with a large transport delay, usually by:
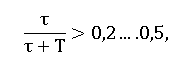
where τ is the time delay;
T – the transition process without delay;
proposed the solution method by using the Smith predictor. The aim of the Smith predictor is to predict which signal should appear at the output of the object before it will actually be [13].
Due to the fact that on the basis of the projected speed of descent of the charge it is possible to determine the required capacity of the conveyor with a significant precession and thereby to compensate for a large transport delay in the load system, appears the opportunity to predict the behavior of the object until a signal at its output [9].
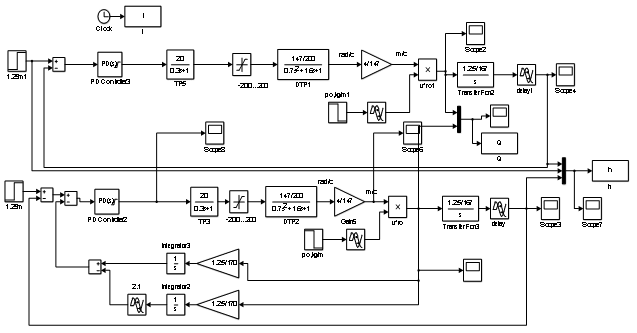
Figure 2 – scheme of the modeling of the ACS of the grain bill level on the furnace top with Smith predictor and without it
As a method of setting parameters of the regulator will choose the automatic setting method of PID-controller in the Matlab simulation package.
Compare the simulation results of two structures of ACS: with Smith predictor and without it (fig.3).
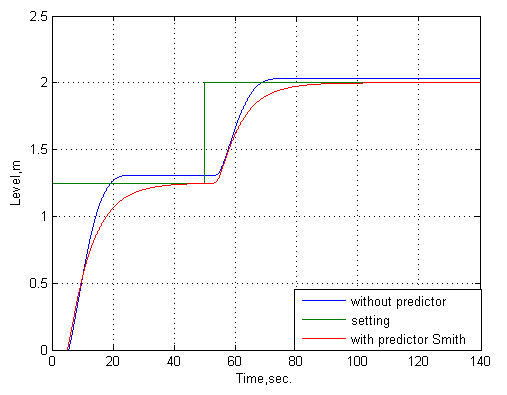
Figure 3 – Transient response of the grain bill level on the furnace top when you change the setpoint from 1.25 m to 2 m
Analyzing figure 3 it can be seen that the level of the corresponding grain bill 1.25 m supports ACS with the Smith predictor, disappeared a static error, which was present in the system without Smith predictor. Overshoot in both systems is not observed, the transient time in the system with Smith predictor T≈40 sec, without it 22 seconds. On the basis of the ratio of the transport delay to the time of full transient process in the system with Smith predictor is equal to 0,1; 0,3 – without him.
5.Development of the algorithm of ACS
Implement the algorithm of the main program control the rate of batch charging. When running ACS, you must perform the initialization: to start the control program on a PC of the operator to reset all program variables to verify the operation of all sensors, the executive mechanisms of the system and the whole system. Computer communication with the controller is provided via Ethernet Protocol, and controller with sensors and actuators by means of the Modbus Protocol. They can be used to monitor and control the process. Next is running the programme on computer and introduction to settings: speed of the conveyor belt, the level of the grain bill batch and dose of the material to get started. Further work programme is carried out cyclically. Conducted a survey of all sensors, processing of the values obtained from them, the information output to the monitor.
Next, the program will compare the data received from the sensors with the settings that were set previously, and if some parameter has gone beyond setpoint, the controller takes control action to the corresponding actuator, thus compensating the mismatch between setpoint and current value.
After the control action over a period of time required for testing, to verify its efficiency has reached the parameters for the specified values. If the parameters have reached the required values, the program returns to the beginning of the cycle.
Submit all above in the form of a block diagram (fig.4).
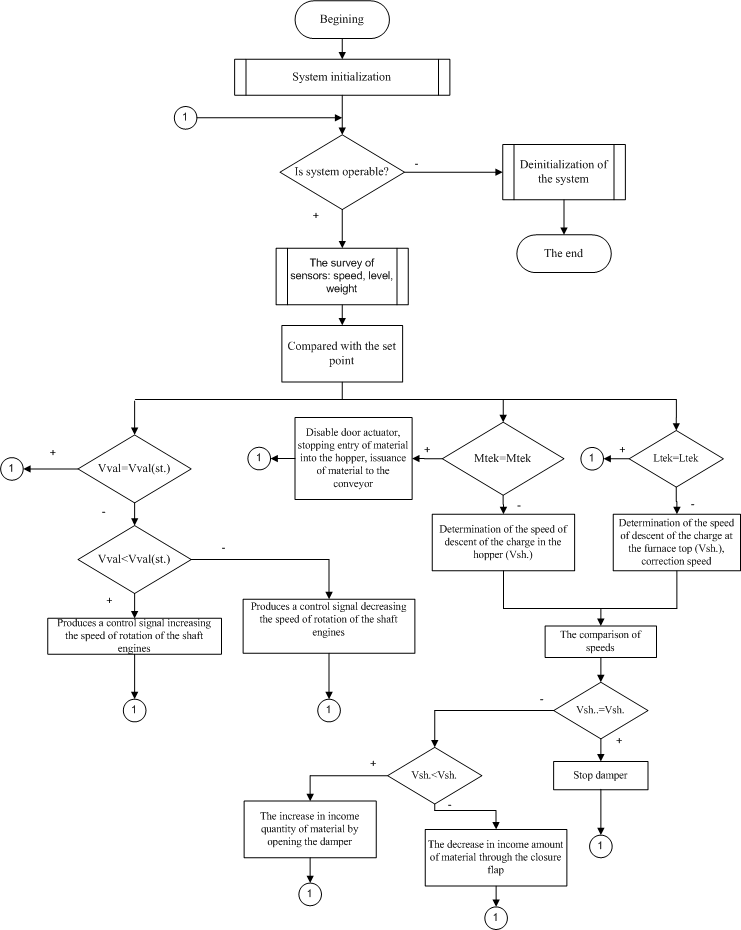
Figure 4 – The block algorithm diagram of the ACS work
6.Conclusions
- The analysis of TP rate of batch charging to the blast furnace as a control object. Found that this property has great transport delay.
- Established that to improve the quality of management of such objects possible in two ways: reducing the transport delay in the object by structural modifications or by using more complex control structures to reduce the negative impact of delay. Proposed the method of Smith predictor.
- By the methods simulation in Matlab-Simulink proved the efficiency of the ACS with the Smith predictor.
- The algorithm of work of the ACS rate of batch charging is represented.
- In the future we plan to investigate the effect of noise on model to consider optimization techniques to reduce the performance burden materials will also be produced by economic calculations the possibility of introducing this system into operation.
Writing this abstract master's work has not complete yet. Final completion: june 2018. Full text works and materials on the subject can be obtained from author or his supervisor after the specified date.
References
- Свинолобов Н.П. Печи черной металлургии: Учебное пособие для вузов / Н.П. Свинолобов, В.Л. Бровкин. – Днепропетровск: Пороги, 2004. – 154 с.
- Автоматическое управление металлургическими процессами: Учебник для вузов / А.М. Беленький, В.Ф. Бердышев, О.М. Блинов, В.Ю.Каганов. – М.: Металлургия, 1989. – 384 с.
- Левин М.З. Механическое оборудование доменных цехов / М.З. Левин, В.Я. Седуш. – Киев-Донецк: издательское объединение
Вища школа
, Головное изд-во, 1978. – 176 с. - Глинков Г.М. АСУ Технологическими процессами в агломерационных и сталеплавильных цехах: учебник для вузов / Г.М. Глинков, В.А. Маковский. – М.:
Металлургия
, 1981. – 360 с. - Ермолович Д.А. Управление объектами с большим запаздыванием / Д.А. Ермолович, А.П. Мовчан //
Автоматизація теплоенергетичних процесів
/6 – Міжнародна науково-практична конференція. /КПИ
. – Киев. - Кочетыгов И.С. Применение регуляторов в системах транспортного запаздывания / И.С. Кочетыгов, Д.Е. Макаров // Научный вестник. / НГТУ. – 1995. – № 1. – C. 92-94.
- Фуртат И.Б. Адаптивное управление объектом с запаздыванием по управлению без использования прогнозирующих устройств / И.Б. Фуртат // Управления большими системами. – 2012. – №40. – С. 144-163.
- Поляков К.Ю. Теория автоматического управления / К.Ю. Поляков. – СПб.: Питер, 2008.
- Глинков Г.М. АСУ Технологическими процессами в агломерационных и сталеплавильных цехах: учебник для вузов / Г.М. Глинков, В.А. Маковский. – М.:
Металлургия
, 1981. – 360 с. - Волков Р.А. Конвейеры Справочник / Р.А. Волков, А.Н. Гнутов, В.К. Дьячков. – Л: Машиностроение, Ленингр. отд-ние, 1984. – 367 с.
- Филлипс Ч. Системы управления с обратной связью / Ч. Филлипс, Р. Харбор. – М.: Лаборатория Базовых Знаний, 2001 – 616 с.
- Денисенко В.В. ПИД-регуляторы вопросы реализации часть 2 / В.В. Денисенко // СТА. – 2008. – № 1. – С. 86-99.
- Денисенко В.В. ПИД-регуляторы: принципы построения и модификации / В.В. Денисенко // СТА. – 2007. – № 1. – С. 77-88.
- Большаков В.И. Применение радиолокационных систем измерения поверхности засыпи шихты для контроля и управления доменной плавкой / В.И. Большаков, И.Г. Муравьева, Ю.С.Семенов. – Днепропетровск: Пороги, 2013. – 364 с.
- Осипова В.А. Автоматизация металлургических производств / В.А. Осипова, Т.В. Астахова, А.А. Дружинина. – Красноярск: ИПК СФУ, 2008.
- Лукас В.А. Теория автоматического управления: Учеб. для вузов – 2-е издание., перераб. и доп. / В.А.Лукас. – М: Недра, 1990. – 416 с.
- Поляков А.К. Языки VHDL и VERILOG в проектировании цифровой аппаратуры / А.К. Поляков. – М.: СОЛОН-Пресс, 2003. – 320 с.
- Гурецкий Х. Анализ и синтез систем управления с запаздыванием / Х. Гурецкий. – М.:
Машиностроение
, 1974. – 328 с. - Клименко В.А. Основы физики доменного процесса / В.А. Клименко, Л.С Токарев. – Челябенск: Металлургия. Челябенское отделение, 1991. – 288 с.
- Готлиб А.Д. Доменный процесс / А.Д. Готлиб. – М.:
Металлургия
, 1966. - Банных А.М. Доменное производство. Справочник / А. М. Банных, П.Л. Грузин, А.П. Гора. – М.:
Металлургиздата
, 1963.