Реферат по теме выпускной работы
Содержание
- Введение
- 1. Актуальность темы
- 2. Цель и задачи исследования, планируемые результаты
- 3. Обзор исследований и разработок
- 3.1 Анализ технологического процесса гидротранспорта как объекта автоматизации
- 3.2 Существующие способы регулирования углесосных установок
- 3.3 Критический анализ существующих решений по системе автоматического управления углесосной установкой
- 4. Основные результаты исследований и разработки
- Выводы
- Список источников
Введение
Для обеспечения эффективности работы предприятия нужно осуществлять своевременное внедрение комплексной системы автоматизации технологических процессов с использованием современных устройств автоматизации. Кроме того, автоматизация производства имеет не только технико–экономическое, но и большое социальное значение, т.к. существенно изменяет характер труда, создает условия для устранения различий между физическим и умственным трудом.
Увеличение производительности угледобычи предъявляет повышенные требования ко всем технологическим процессам горного предприятия. Одним из важных технологических процессов шахты с гидравлической выемкой угля является процесс напорного гидротранспорта с помощью углесосных установок.
По уровню автоматизации гидространспорт занимает одно из ведущих мест среди других отраслей шахтной автоматизации.
Технологический процесс гидротранспорта характеризуется непрерывностью протекающих в нём процессов. Эксплуатация углесосных установок должна обеспечивать надежный и эффективный транспорт требуемых параметров, а также безопасные условия труда персонала, работающего с этими установками.
1. Актуальность темы
Эксплуатация автоматизированных углесосных установок должна обеспечивать гидротранспорт угля или других полезных ископаемых с получением наибольшего экономического эффекта, что достигается именно обеспечением безопасного труда и непрерывностью технологического процесса.
Существующие средства автоматизации углесосных установок не в полной мере решают проблемы эксплуатации установок. Не решены вопросы регулирования углесоса по подаче, контроля уровня гидросмеси в пульпосборнике, расхода электроэнергии углесосной установкой и другие. Также существующая аппаратура автоматизации выполнена на технически устаревшей элементной базе, что не позволяет реализовывать такие функции, как связь с ЭВМ пульта диспетчера, сохранение данных, их анализ, автоматическое регулирование подачи углесосной установки. Поэтому разработка и исследование системы автоматического управления (САУ) углесосной установкой является актуальной темой.
2. Цель и задачи исследования, планируемые результаты
Целью магистерской работы является повышение эффективности технологического процесса гидротранспорта путем разработки и исследования системы автоматического управления углесосной установкой.
Исходя из анализа технологического процесса гидротранспорта как объекта автоматизации, к системе автоматического управления углесосной установкой предъявляются следующие требования:
- обеспечение автоматического пуска и остановки углесосной установки;
- автоматическое регулирование подачи углесосной установки;
- автоматический контроль следующих параметров: текущего уровня гидросмеси в пульпосборнике, подачи углесоса, давления гидросмеси в пульповоде, расхода электроэнергии углесосной установкой, температуры подшипниковых узлов углесоса, времени работы углесосной установки в режимах зарегулирования и разрегулирования;
- автоматическая защита углесосной установки: при развитии кавитации в углесосе, при снижении подачи углесоса, при закупорке всасывающего устройства;
- автоматическое регулирование: режим разрегулирования (номинальный режим работы по гидросмеси) и режим зарегулирования (минимальная подача);
- непрерывный сбор, обработка, хранение и представление информации о работе углесосной установки и системы автоматического управления углесосной установкой;
- обеспечение обмена информацией между смежными системами автоматизации с использованием высокоскоростной искробезопасной промышленной компьютерной сети;
- конструктивное исполнение и схемное решение технических средств системы автоматического управления должны соответствовать требованиям "Правил изготовления взрывозащищенного и рудничного электрооборудования" – иметь вид взрывозащиты " взрывонепроницаемая оболочка" и "искробезопасная электрическая цепь", а монтироваться и эксплуатироваться в соответствии с "Правилами технической эксплуатации угольных и сланцевых шахт"[1] .
Объект исследования: технологический процесс напорного гидротранспорта.
Предмет исследования: система автоматического управления углесосной установкой.
3. Обзор исследований и разработок
3.1 Анализ технологического процесса гидротранспорта как объекта автоматизации
При гидромеханизации транспортирование гидросмеси (смесь горной массы и воды в пропорции Т:Ж) осуществляется по лоткам (безнапорный гидротранспорт) или по трубам (напорный гидротранспорт).
В данной работе рассматривается как объект автоматизации и исследования технологический процесс гидротранспорта.
На рисунке 1 приведена технологическая схема гидротранспорта. Перекачивание гидросмеси напорным гидротранспортом осуществляется углесосными установками.
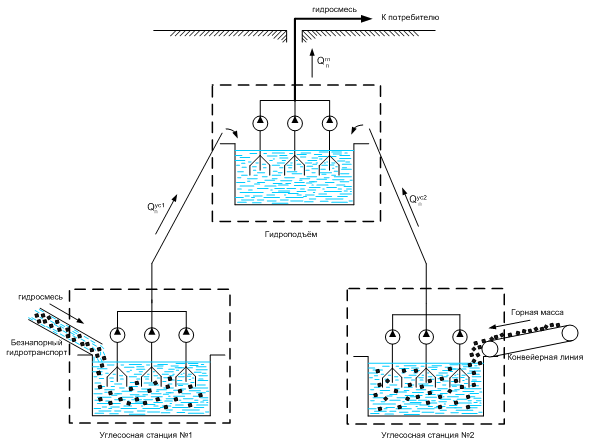
Рисунок 1 – Технологическая схема гидротранспорта шахты
Углесосные установки по назначению делятся на гидроподъёмные углесосные установки с положительной геометрической высотой нагнетания (вертикальный и наклонный гидротранспорт) и без геометрической высоты нагнетания (горизонтальный гидротранспорт).
Углесосные установки по месту расположения в подземных горных выработках делятся на главные гидроподъёмные углесосные установки (вертикальный гидротранспорт), вспомогательные углесосные установки (наклонный гидротранспорт с положительными углами прокладки пульповодов) и участковые углесосные установки (горизонтальные и слабонаклонные с отрицательными углами прокладки пульповодов в сторону околоствольного двора). Первый вид транспорта осуществляет выдачу гидросмеси или воды из пульпосборников центральной гидрокамеры на поверхность шахты. Второй вид транспорта осуществляет передачу гидросмеси из нижележащих горизонтов на вышележащий. Третий вид осуществляет передачу гидросмеси от добычных гидроучастков до пульпосборников либо промежуточных станций, либо до центральной гидрокамеры.
Углесосные установки в шахте располагаются в углесосных станциях.[3]
Углесосная станция – это технологический комплекс, который обеспечивает транспортировку гидросмеси, или воды по трубопроводам. Количество углесосных станций различное и зависит от мощности шахты, производственной необходимости, системы вскрытия и разработки шахтного поля и т.д. Углесосная станция содержит три углесосных установки (одна рабочая, вторая резервная, третья в ремонте).
3.2 Существующие способы регулирования углесосных установок
Все известные в настоящее время способы регулирования подачи углесосных установок по технической сущности делятся на две группы:
- регулирование без предварительного перевода углесоса на воду;
- регулирование с предварительным таким переводом.
К первой группе относятся следующие способы. Регулирование путем: изменения частоты вращения рабочего колеса углесоса; впуска воздуха во всасывающую линию углесоса; изменения консистенции гидросмеси; дросселирования пульповода напорного трубопровода.
Все перечисленные способы данной группы обладают общим существенным недостатком: все они для обеспечения заданной глубины регулирования требуют увеличения на такую же величину начальной скорости потока, что ведет к резкому увеличению потерь на трение и существенному сокращению длины транспортирования. Поэтому отмеченные способы не отвечают современным требованиям, предъявляемым к ним условием эффективной эксплуатации углесосных установок.
В большей мере поставленным требованиям отвечают способы второй группы. К ним относится способ, разработанный в Донецком национальном техническом университете. Этот способ основан на применении всасывающего устройства УВ–5 и заключается в предварительном переводе углесоса на воду, полной промывке транспортного трубопровода стандартной задвижкой. Данный способ в течении нескольких лет успешно применялся на гидрошахтах, и показал достаточную эффективность, по сравнению с ранее применявшимся способом включения-отключения углесосов по уровню гидросмеси в зумпфе. Однако, как показал опыт эксплуатации, эффективность применения этого способа уменьшается с увеличением длины транспортирования из–за наличия операции полной промывки транспортного трубопровода, потребляющей около 50 процентов всех непроизводительных затрат воды на транспорте. Причем время полной промывки пульповода, в ряде случаев, оказывается соизмеримо с временем включения подачи воды в забои, вследствие чего по гидросистеме может непрерывно перекачиваться максимальный расход воды, который в одном случае необходим для гидротранспорта твердого материала, а в другом – для промывки трубопроводов[5] .
В магистерской работе применён способ регулирования подачи углесосной установки изменением частоты вращения рабочего колеса углесоса, с предварительным переводом работы углесоса с гидросмеси на воду. Применение данного способа регулирования требует использования преобразователя частоты вращения высоковольтного электропривода в специальном рудничном исполнении.
3.3 Критический анализ существующих решений по системе автоматического управления углесосной установкой
В настоящее время известны ряд схем автоматизации, обеспечивающих автоматическое выполнение различных операций по управлению гидротранспортом. Схемы автоматизации углесосных установок предусматривают, в основном, автоматизированный пуск и остановку электроприводов агрегатов, дистанционное управление запорной арматурой, дистанционный контроль состояния агрегатов и аппаратуры, ввода резерва.
В Донецком национальном техническом университете разработано несколько модификаций аппаратуры автоматизации углесосных станций типа АСУ. Аппаратура модификации АСУ–1 выполняет следующие функции:
- заполнение водой напорного транспортного трубопровода одновременно с подачей воды в забой;
- заливку с помощью гидроэлеватора одного из углесосных агрегатов при поступлении гидросмеси в зумпф и достижении в нем верхнего уровня;
- включение углесоса по окончании заливки;
- остановки углесоса при отсутствии притока и по достижении нижнего уровня в зумпфе;
- промывку всей гидросистемы перед остановкой углесоса;
- обеспечения продолжительного режима работы углесосов за счет регулирующей емкости;
- регулирования концентрации гидросмеси применением всасывающего устройства УВ–1.
Аппаратура АСУ–1 предусматривает следующие виды защит: гидравлический защиту углесосов от выхода из зоны рабочих режимов и от прекращения подачи воды, осуществляемую по производительности применением дифференциальных манометров, подключенных к коллектору всасывающих трубопроводов; электрическая защита электрооборудования; тепловая защита подшипников. В аппаратуре АСУ–1 импульс на включение углесосных агрегатов подается при совокупности двух факторов: наличия приплыва гидросмеси в пульпосборнике и достижения верхнего уровня в нем. Импульс на остановку подается при достижении нижнего уровня в пульпосборнике. Дальнейшим совершенствованием аппаратуры АСУ–1 стало разработка аппаратуры АСУ–4.[6]
Аппаратура выполняет следующие функции:
- автоматический пуск в работу двух последовательно включенных углесосов предварительной заливкой при верхнем уровне гидросмеси в пульпосборнике;
- остановку углесосов при нижнем уровне гидросмеси в пульпосборнике с предварительной промывкой всей гидротранспортрной системы;
- последовательную работу последовательно включенных групп углесосов, автоматическое выключение всей группы при неисправности хотя бы одного из работающих углесосов;
- включение резервной группы углесосов; выведение любой из углесосных групп из режима автоматического управления в ручной.
Предусмотрены следующие виды защит: гидравлическая – по минимально допустимой производительности; электрическая – от перегрузок, коротких замыканий и нулевой, а также тепловую защиту подшипников. Предусмотрена световая и звуковая сигнализация. Схема аппаратуры АСУ–4 построена на контактных элементах. Пуск и остановка углесосных агрегатов осуществляются по заданной программе. Программное реле включается при достижении гидросмеси верхнего уровня в зумпфе пульпосборника. Импульс для промывки гидротранспортной системы перед остановкой углесосов поступает от датчика нижнего уровня. Время промывки определяется по заранее заданной программе. Углесосы должны быть оборудованы впитывающими устройствами типа УВ–2М.[7]
Аппаратура автоматического управления углесосных установкой типа АУУГ осуществляет запуск и остановку углесосы зависимости от верхнего и отключающего уровней гидросмеси в зумпфе гидротранспортной установки. Кроме того, в полукомплект управления предусмотрена отработка специальной программы повторных запусков углесосных агрегата в случае неудачных предыдущих запусков по причине некачественной заливки, или сброс подачи углесосы, (возникших к заключительному моменту запуска) и исключают дальнейшую нормальную эксплуатацию агрегата и всей установки в целом.
На рисунке 2 приведена структурная схема аппаратуры АУУГ.
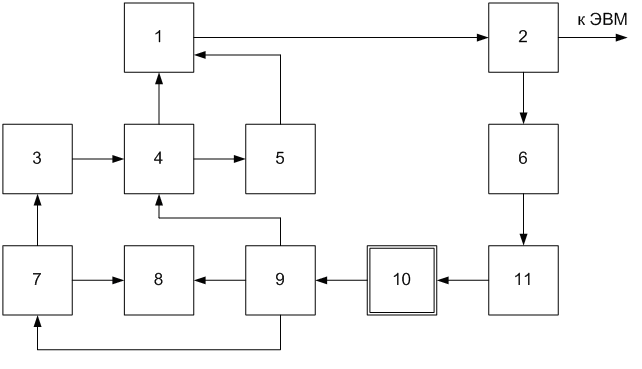
Рисунок 2 – Структурная схема аппаратуры АУУГ
На рисунке 2 обозначено:
- датчики (манометры, вакуумметры, дифманометры)
- блок нормирующих преобразователей;
- пульт управления;
- углесосный агрегат;
- зумпф углесосной станции;
- блок формирователей;
- исполнительные механизмы;
- блок индикации;
- блок исполнительных реле;
- блок программ управления (программы пуска–остановки, контроля и защиты, регулирования углесоса)
- дешифратор.
Принцип действия аппаратуры АУУГ основан на использовании информации о текущих уровнях гидросмеси в зумпфе, гидравлических параметров узла дозирования и других элементов всасывающего устройства, основных рабочих параметров установки (расход, давление, вакуум). Исходным состоянием для функционирования аппаратуры АУУГ является наличие верхнего уровня в зумпфе, закрытое состояние шибера нагнетания и открытое состояние шибера подпитки. Информация от первичных датчиков о технологических параметрах углесосной установки сосредотачивается в блоке 2, и поступает в блок формирователей 6, где заданными уставками формируются дискретные сигналы. В дешифраторе 11, в зависимости от технологической ситуации, производятся сигналы для выбора соответствующей программы управления в блоке 10. Например, программа нормального запуска, предусматривает заполнение пульповодов и заливку углесосы с последующим его выключением. Если при этом углесос работает нормально, то задвижка гидроэлеватора закрывается и на этом запуск заканчивается, а углесос переводится на гидросмесь и работает нормальном транспортном режиме (задвижка на пульповодов открыта, шибер подпитки закрыт). Если после включения углесос не развил необходимых параметров (вакуум и давление), то включается программа повторного запуска, которая при необходимости повторяется еще 2 раза в том же порядке, что и при нормальном запуске и если после этого углесосы не развивает подачи - срабатывает счетчик повторных запусков (при числе пусков равном трём), включая неисправную установку и выдается команда перехода на резервную с одновременной сигнализацией на световое табло блока сигнализации.
4. Основные результаты исследований и разработки
Структурная схема системы автоматического управления углесосной установкой с использованием промышленной сети
Обмен информацией между устройствами, входящими в состав системы автоматического управления происходит с помощью промышленной сети, которая является основой проектирования любой автоматизированной системы технологического процесса.
Коммуникационная технология построения единой информационной сети, объединяющей интеллектуальные контроллеры, датчики и исполнительные механизмы, определяется одним термином fieldbus (полевая шина, или промышленная сеть).
Промышленная сеть – это, во–первых, физический способ объединения устройств (например, RS 485) и, во–вторых, программно–логический протокол их взаимодействия.
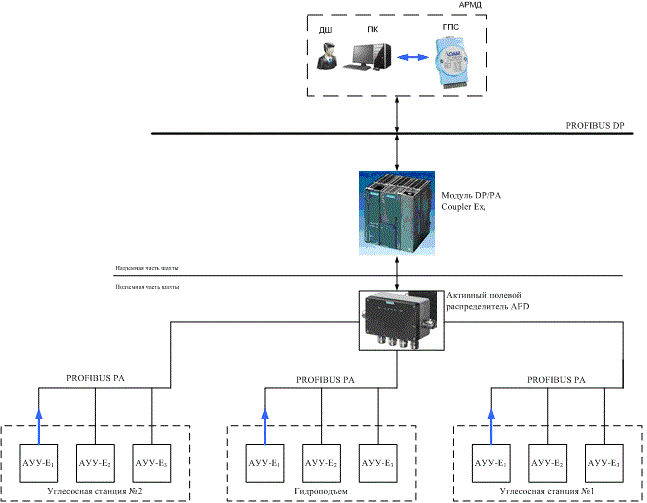
Рисунок 3 – Структурная схема системы автоматического управления углесосной установкой с использованием промышленной сети
(анимация: 8 кадров, бесконечный цикл повторения, 97 килобайт)
(AУУ-Еi – устройства автоматического управления углесосной установкой, расположенные на каждой углесосной установке)
На рисунке 3 обозначено:
- АУУ–Е – устройство автоматического управления углесосной установкой;
- ДШ – диспетчер шахты;
- АРМД – автоматизированное рабочее место диспетчера;
- ПК – промышленный компьютер;
- ГПС – гальваноизолированный преобразователь сигналов RS–232 в сигнал RS–485;
Программно–логический протокол при построении промышленной сети технологическом процессе напорного гидротранспорта шахты можно реализовать, с помощью интерфейсных модулей RS485, которые предусмотрены конструкцией устройства автоматического управления углесосной установкой типа АУУ-Е.[11]
В устройствах АУУ–Е используются микросхемы типа MAX489CPD. Микросхема MAX489CPD представляет собой полнодуплексный приёмо-передатчик стандартов RS–485/RS–422 с низким энергопотреблением и ограничением скорости. Каждая микросхема содержит один передатчик и один приёмник.[8]
Унифицированный протокол PROFIBUS–DP и PROFIBUS–PA обеспечивает связь обоих сетей и тем самым комбинацию временных характеристик и искробезопасной техники передачи.
На нижнем уровне автоматизации функционирует протокол PROFIBUS–PA. Протокол PROFIBUS–PA – это сеть полевого уровня, ориентированная на использование в системах автоматизации непрерывных и периодических процессов. Нормированные коммуникационные службы гарантируют организацию надежного обмена данными между системами автоматизации и интеллектуальными приборами полевого уровня различных производителей.
В сети PROFIBUS–PA используются электрические каналы связи, выполненные экранированными витыми парами. Допускается применение магистральных, древовидных и звездообразных топологий протяженностью до 1.9 км. На концах каждого сегмента PROFIBUS–PA устанавливаются пассивные терминальные элементы (SplitConnect Terminator). Подключение PROFIBUS–PA к сети PROFIBUS–DP выполняется через блоки или модули DP/PA–связи.
Преимущества распределенной системы автоматизации использующей сеть PROFIBUS–PA являются: меньшее количество оборудования, эффективное проектирование, высокая надежность функционирования системы, легкость обслуживания.
Структурная схема устройства автоматического управления углесосной установкой типа АУУ–Е
Структурная схема устройства автоматического управления углесосной установкой типа АУУ–Е приведена на рисунке 4.
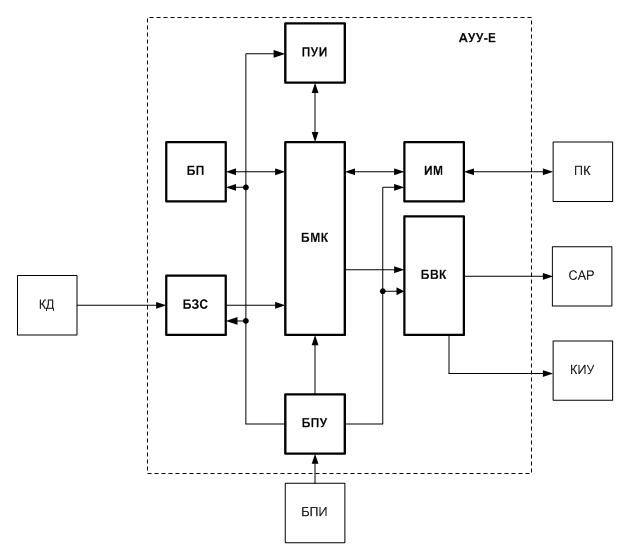
Рисунок 4 – Структурная схема устройства автоматического управления углесосной установкой типа АУУ–Е
На рисунке 3 изображено: БЗС – блок согласования и защиты, БМК – блок микроконтроллера, ИМ – интерфейсный модуль, БВК – блок вывода команд, БП – блок памяти, ПУИ – пульт управления и индикации оператора углесосной установки.
Блок БЗС предназначен для:
- согласования уровня напряжения, коммутируемого дискретными датчиками, с рабочим напряжением микроконтроллера устройства;
- согласования входных сигналов от датчиков и защиты микроконтроллера от возможных повреждений линий связи.
Блок БЗС состоит из 2–х субблоков: субблок ввода дискретных сигналов СбД, и субблока ввода аналоговых сигналов СбА.
Субблок СбД предназначен для согласования входных сигналов от дискретных датчиков с блоком микроконтроллера БМК, а также для предотвращения возникновения воспламенения внутри устройства управления АУУ–Е. Субблок СбА предназначен для согласования входных сигналов от аналоговых датчиков с блоком микроконтроллера БМК.
Блок микроконтроллера БМК представляет собой два работающих с одной и той же частотой микроконтроллера серии AVR типа ATmega64 и ATmega16 , основной функцией которого является обработка входных сигналов от датчиков, тумблеров и кнопок , а также вывод согласно алгоритму управления соответствующие управляющие команды.
Интерфейсный модуль ИМ предназначен для обеспечения промышленной сети между устройством управления и промышленным компьютером. Блок ИМ представляет собой универсальный модуль RS–485/RS–232, который реализует последовательный интерфейс приёма–передачи данных по линиям интерфейса RS–485 или RS–232 с автоматическим управлением направлением потока передачи данных, с гальванической развязкой, рассчитан для организации связи на расстояния не более 1,2 км.
Блок БВК предназначен для:
- согласования уровня напряжения, коммутируемого дискретными или аналоговыми датчиками, с рабочим напряжением исполнительных устройств системы автоматизации;
- согласования выходных сигналов микроконтроллера и защиты микроконтроллера от возможных повреждений линий связи.
Блок ПУИ предназначен для:
- визуализации на ЖКИ текущих параметров углесосной установки: текущей подачи углесосной установки, величины активной мощности потребляемой углесосом, текущего уровня гидросмеси в пульпосборнике;
- индикация технологических событий с помощью светодиодов: перегрев подшипниковых стаканов приводного электродвигателя, кавитация углесоса, закупорка всасывающего устройства, режим работы углесосной установки (САР).
Встроенный блок питания устройства управления БПУ предназначен для питания искробезопастным постоянный стабилизированным напряжением микроконтроллер, интегральных микросхем и оптопар.
Выводы
В магистерской работе рассматривается вопрос разработки и исследования системы автоматического управления углесосной установкой с целью обеспечения непрерывности работы, меньшего энергопотребления технологического процесса напорного гидротранспорта.
Выполнен анализ работы углесосной установки технологического процесса гидротранспорта, как объекта автоматизации, затем были сформулированы требования к исследованию системы автоматического управления углесосной установкой.
Во время разработки системы автоматического управления было учтены условия среды для данной системы. К примеру, устройство автоматического управления углесосной установкой АУУ–Е выполнено по всем нормам искробезопастности, что обеспечивает безопасное протекание тока в момент переходных процессов, замыкании контактов. Устройство рассчитано для работы в шахтах, в том числе опасных по газу или пыли, в условиях умеренного, холодного климата при температуре окружающего воздуха от минус 10 до 35°С и относительной влажности до 100% при температуре 35°С.
Главные преимущества системы автоматического управления углесосной установкой заключаются в решении ряда технических задач, которые не возможно решить без автоматизированного управления: сокращение рабочего персонала и увеличение производительности его труда, мониторинг работы углесосной установки с помощью технических средств автоматизации, системы визуализации и аппаратуры АУУ–Е, уменьшение энергопотребления углесосной установки и снижение затрат, которые идут на предотвращение или устранение различных аварийных ситуаций.
При написании данного реферата магистерская работа еще не завершена. Окончательное завершение: июнь 2018 года. Полный текст работы и материалы по теме могут быть получены у автора или его руководителя после указанной даты.
Список источников
- НПАОП 10.0-1.01-10. Правила безпеки у вугільних шахтах. Наказ Державного комітету України з промислової безпеки, охорони праці та гірничого нагляду №62 від 23.03.2010. – 150с.
- Маренич К.Н. Электрооборудования технологических установок горных предприятий: [учеб. для студентов высших учеб. заведений] / Маренич К.М., Калинин В.В., Товстик Ю.В., Лизан И.Я., Коломиец В.В. - Донецк: ДонНТУ, Харьков: УИПА, 2009. – 372с.
- Коденцов А.Я. Гидротехнология на шахтаx/ А. Коденцов. – М.: Недра, 1984. – 320 с.
- Технические средства автоматизации в горной промышленности: Учебное пособие / В.И. Груба, Э.К. Никулин, А.С.Оголобченко. – К.:ИСМО, 1998. – 373 с.
- Основы управления гидроэнерготранспортными системами угольных шахт / В.И. Груба, Э.К. Никулин, А.С. Оголобченко; Под ред. В.И. Грубы, – Донецк: Донбасс, 1993. – 225 с.
- Методология расчётов гидродинамических параметров шахтных автоматизированных стационарных установок с центробежными нагнетателями: монография / Э.К. Никулин, И.В. Ковалёва, К.Н. Маренич. – Донецк: ООО "Технопарк ДонГТУ "Унитех", 2015. – 134 с.
- Центробежные насосы и трубопроводные сети в горной промышленности : справочное пособие / Ф.А. Папаяни, Н.Б. Трейнер, В.И. Никитин и др. ; под общ. ред. Ф.А. Папаяни, Н.Б. Трейнера. – Донецк : Восточный издательский дом, 2011. – 334 с.
- Рюмик С.М. 1000 и одна микроконтроллерная схема. Вып. 1. – М.: Додэка – XXI, 2010. – 356 с.
- Единая система конструкторской документации: Справочное пособие / С.С. Борушек, А.А. Волков, М.М. Ефимова и др.–2–е изд., перераб. И доп.– М. : Издательство стандартов, 1989. – 352 с.
- Груба В. И. Технические средства автоматизации в горной промышленности. – В. И. Груба, Э. К. Никулин, А. С. Оголобченко – К.: ИСМО, 1998. – 373 с.
- Ермолинский А.А., Оголобченко А. С. Автоматизированная система управления комплексом углесосных установок гидрошахты / Автоматизация технологических объектов и процессов. Поиск молодых. Сборник научных работ ХVII международной научно – технической конференции аспирантов и студентов в г. Донецке 24 – 25 мая 2017. – c.101 – 107.
- Ермолинский А.А., Оголобченко А. С. Компьютеризированная система автоматического управления шахтной гидротранспортной установкой / Автоматизация технологических объектов и процессов. Поиск молодых. Сборник научных работ ХVI международной научно – технической конференции аспирантов и студентов в г. Донецке 24 – 26 мая 2016. – c.111 – 115.
- Овсянников Ю.А., Кораблев А.А., Топорков А.А., Автоматизация подземного оборудования: Справочник рабочего. – М.: Недра, 1990.– 287 с.
- Баранов В.Н. Применение микроконтроллеров AVR: схемы, алгоритмы, программы. – М.: Издательский дом «Додэка–XXI», 2004. – 288 с.