Реферат по теме выпускной работы
Содержание
- Введение
- 1. Актуальность темы
- 2. Цель и задачи исследования
- 3. Обзор исследований и разработок
- 4. Основные результаты исследований и разработки
- Выводы
- Список источников
Введение
На крупных угольных шахтах доставка угля от очистных забоев до скипового подъема осуществляется по многопоточной линии конвейерного транспорта, состоящей из участковых конвейерных линий и сборных конвейеров – магистральных конвейерных линий. Участковая ленточная конвейерная линия обеспечивает транспортирование угля от очистного забоя до места перегрузки на магистральную конвейерную линию. Как правило перегрузка осуществляется через промежуточный бункер.
Основным видом управления конвейерным транспортом шахты является автоматизированное управление, техническая сущность которого заключается в централизации управления процессами пуска-останова конвейеров в линии, при обеспечении автоматической защиты от развития аварии в случае возникновении аварийных ситуаций.
1. Актуальность темы
Современные подземные конвейерные линии характеризуются значительной протяженностью (десятки километров) и разветвленность транспортных магистралей, изменяющих со временем свои параметры: длину, топологию и т.п. В условиях шахт конвейерная линия может быть не разветвленной и разветвлённой. Под неразветвленной конвейерной линией понимают однопоточную линию, в которой груз на каждый конвейер поступает только с одного предыдущего конвейера, а под разветвленной - многопоточную линию, состоящую из ответвлений и сборной части. Для разветвленных конвейерных линий требуется согласование режимов работы основных – магистральных конвейеров с участковыми.
Характерна многозвенность конвейерного транспорта, которая определяется большой протяженностью, а также наличием горизонтальных и наклонных выработок, сопрягаемых между собой. Это приводит к необходимости в некоторых случаях иметь каскады последовательно установленных ленточных конвейеров, число которых может составлять до 10 и более. Ленточные конвейеры могут быть проложены по горизонтальным выработкам, уклонным и бремсберговым. Иногда в многозвенных транспортных цепях применяют различные виды транспорта, например, локомотивный по горизонтальной и конвейерный по наклонной выработкам. Требуется согласование режимов работы различных видов транспорта.
Ленточные конвейеры могут быть оборудованы одним приводным электродвигателем или несколькими мощными электродвигателями. Например, конвейер 1Л80 оборудованный одним асинхронным электродвигателем с короткозамкнутым ротором типа ВАО2-280L10 мощностью 45 кВт, а магистральный конвейер 2ЛУ120В оборудованный двумя асинхронным электродвигателем с фазным ротором типа АК312 49-6 мощностью 250 кВт каждый и т.д. Суммарная мощность электродвигателей участковых конвейеров составляет 300-500 кВт, а магистральных – несколько тысяч киловатт, поэтому подземная транспортная система современной угольной шахты наравне с подъёмными, водоотливными и вентиляторными установками является основным потребителем электроэнергии. Доля энергопотребления конвейерного транспорта шахты составляет порядка 20% общешахтного потребления электроэнергии. Требуется обеспечение работы конвейерных установок в энергосберегающих режимах.
Высокая неравномерность грузопотоков, поступающих на транспортные установки, так как конвейерная линия по своему технологическому назначению является транспортным объектом, обслуживающим очистной забой. Технологические паузы в работе выемочных комбайнов, в том числе при аварийной остановке лавы, и периодическое изменение их скорости перемещения вдоль линии очистного забоя являются причиной неравномерности или отсутствия грузопотоков, которые также отражаются на загрузке конвейера. При этом характерна значительная недогрузка магистральных конвейеров; продолжительная работа в режиме холостого хода. Это отрицательно сказывается на технико-экономических показателях использования средств транспорта, т.к. они большую часть времени своей работы имеют существенную (в 2...4 раза) недозагрузку, приводят к повышению удельных расходов электроэнергии.
В настоящее время на угольных предприятиях для повышение эффективности конвейерного транспорта применяются угольные аккумулирующие бункеры и предлагается регулирование скорости движения конвейерной ленты с использованием частотно-регулируемого привода (ЧРП). На рисунке 1 представлена технологическая схема конвейерной линии с накопительным бункером. В современных ленточных конвейерах применяют нерегулируемый асинхронный электропривод.
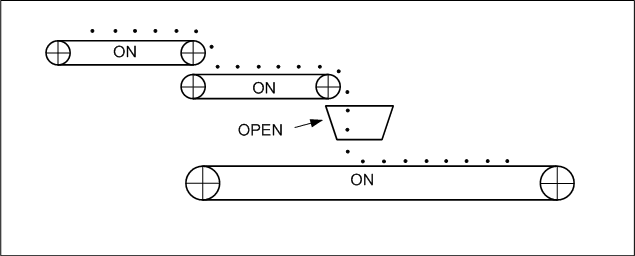
Рисунок – 1 Технологическая схема конвейерной линии с накопительным бункером
(анимация: 8 кадров, бесконечный цикл повторения, 42 килобайт)
Однако целесообразность использования ЧРП имеет ряд спорных моментов. Во-первых, диапазон регулирования частоты в установившемся режиме для таких механизмов, особенно в наклонных выработках, ограничен, чтобы говорить о существенном изменении производительности. Увеличению скорости движения ленты будет препятствовать характеристика транспортируемого груза, который будет просто падать с конвейера. При уменьшении частоты вращения необходимо обеспечить рабочий момент на валу двигателя, к тому же использовать высокопроизводительный конвейер для транспортирования малого объема груза просто нецелесообразно. Во-вторых, длительная работа преобразователя в режиме пониженных частот приведет к необходимости дополнительного принудительного охлаждения как двигателя, так и самого преобразователя.
С точки зрения повышения энергоэффективности конвейерного транспорта целесообразнее регулировать не производительность конвейера, а поступающий на него грузопоток, приближая его к номинальному значению. Наиболее эффективным мероприятием для предотвращения режима холостого хода и сокращения времени работы конвейеров путем обеспечения их полной загрузки является применение усредняющих и аккумулирующих бункеров, объем и производительность разгрузки которых будут выравнивать и определять грузопоток на забункерной конвейерной линии. К примеру, по самым скромным подсчетам, исключение холостого хода и полная загрузка (через бункер) одного мощного магистрального конвейера позволит снизить суточное электропотребление до 1 МВт/ч при транспортировании того же объема горной массы, что существенно отразится на значении удельного расхода электроэнергии. К тому же, применение аккумулирующих бункеров позволит на время их заполнения остановить магистральные конвейеры большой мощности и перенести время их работы на периоды с меньшей оплатой за электроэнергию (например, на ночной провал
) при расчете по дифференцированному по зонам суток тарифу.
Пуск конвейерной линии должен осуществляется в направлении, обратному грузопотоку, причем каждый следующий конвейер должен включаться после установления нормальной рабочей скорости движения тягового органа предыдущего конвейера. При пуске приложенное пусковое усилия вызывает возникновение упругой волны на участке ленты, связанной с приводным барабаном. Эта упругая волна распространяется вдоль ленты, причем скорость ее распространения зависит от многих факторов, в том числе и от изменения силы трения и ускорение. Принимая во внимание эти особенности при пусковом режиме необходимо обеспечить: плавный пуск (для обеспечения безударного выбора люфтов в зубчатых передачах в начальный период трогания, предотвращение пробуксовки ленты на приводном барабане) и обеспечение минимальной продолжительности процесса пуска (с целью сокращения пусковых потерь в электроприводе с короткозамкнутым электродвигателем).
Основные функциональные требования к системе автоматизации конвейерными установками.
Система автоматизации должна обеспечивать управление разветвленными и неразветвленными конвейерными линиями, отдельными конвейерами и механизмами в линии, а также режимы пуска и останова, защитное отключение механизма, блокировки и сигнализацию.
Виды управления: местное автоматизированное управление транспортным механизмом; централизованное автоматизированное управление конвейерной линией; автоматическое управление конвейерной линией.
Режимы пуска: пуск конвейерной линии или её части по командам от оператора или технологических датчиков в последовательности, исключающей завал мест перегрузок;
Режимы останова: оперативный, аварийный и экстренный остановы конвейера.
2. Цель и задачи исследования
В настоящее время почти все конвейерные линии на шахтах автоматизированы. Однако потенциальные возможности автоматизированного управления исчерпаны не полностью. Продолжают оставаться актуальными следующие задачи: снижение трудоемкости обслуживания автоматизированных конвейерных линий, вероятности отказов в работе линии и времени простоев линии в результате отказа за счет улучшения параметров надежности и ремонтопригодности аппаратуры и технических средств автоматизации, а также развития информационных свойств аппаратуры автоматизации позволяющих сократить время поиска причины и места отказа; повышение безопасности эксплуатации за счет совершенствования существующих технических средств и создания средств автоматизации нового функционального назначения (например, устройство контроля критической температуры в конвейерной выработке, устройство контроля залипання
силовых контактов пускателя привода конвейера и др.).
Для шахтных конвейерных линий характерны возмущения на входе объекта управления (дискретный характер забойных грузопотоков и их переменная интенсивность в периоды непрерывных поступлений), внутренние возмущения объекта управления (экстренные и аварийные остановы конвейеров линии), возмущения на выходе объекта управления, связанные с ограниченной пропускной способностью сопряженных транспортных звеньев (приемного бункера, рельсового транспорта, грузового подъема) либо с нарушением нормального режима их работы.
Задача оптимального автоматического управления сводится к автоматическому поиску и автоматической реализации такого варианта реакции системы на возмущение, при котором достигается наиболее выгодный по выбранному критерию режим работы объекта. Таким образом, система управления является замкнутой по отношению к основному технологическому параметру.
Следует иметь в виду, что автоматическое оптимальное управление является более высокой качественной ступенью развития общей проблемы управления конвейерным транспортом. Однако наличие более высокой качественной ступени не может само по себе служить гарантией целесообразности применения автоматического оптимального управлении на всех' шахтных конвейерных линиях и не предопределяет необходимости повсеместного перехода от автоматизированного управления к оптимальному автоматическому. В данном случае необходим дифференцированный подход, учитывающий параметры конкретного технологического объекта (конвейерной линии).
Критерии и задачи оптимального автоматического управления
В настоящее время довольно широко распространена точка зрения, согласно которой основная задача системы оптимального автоматического управления конвейерной линией заключается в повышении фактической производительности этой линии или даже в достижении максимально возможной производительности линии, но такую постановку задачи нельзя считать приемлемой. Известно, что конвейерная линия по своему технологическому назначению является транспортным объектом, обслуживающим очистной забой и, следовательно, вопрос о величине фактической производительности данного объекта имеет реальный смысл только в сопоставлении с интенсивностью забойного грузопотока. Без связи с забойным грузопотоком задача максимальной производительности конвейерной линии недостаточно конкретна. В частности, из такой постановки задачи вытекает необходимость постоянной работы всех конвейеров линии на номинальной или даже максимально возможной скорости.
Более правильной является постановка задачи об обеспечении необходимой фактической производительности конвейерной линии в соответствии с интенсивностью забойного грузопотока. Однако и этот вариант постановки задачи не может считаться достаточно конкретным. На основании такой постановки задачи можно сделать вывод лишь о том, что линия должна работать по принципу переменной скорости транспортирования груза в ритме забойного грузопотока.
Главная задача системы оптимального автоматического управления заключается в том, чтобы предельно снизить ограничивающее влияние режимов работы конвейерной линии на производительность очистного забоя, т.е. главная задача системы вытекает из той вспомогательной обслуживающей технологической роли, которую играет конвейерная линия по отношению к забою.
Ограничивающее влияние режимов работы конвейерной линии на производительность добычного участка проявляется исключительно в виде простоев лавы из-за неисправности конвейерного транспорта. Поэтому главный критерий для систем оптимального автоматического управления конвейерными линиями целесообразно формулировать в следующем виде: минимальное время простоя добычных участков по причине отказов конвейерной линии или отказов на выходе конвейерной линии(минимальное время простоя
).
Помимо указанной задачи, существует другая задача системы оптимального автоматического управления конвейерными линиями шахт, которая формулируется как: предельное снижение эксплуатационных затрат на единицу веса транспортируемого груза.
Критерии для указанной задачи формулируются следующим образом:
минимальный расход электроэнергии на транспортирование единицы веса груза
(минимальные удельные энергозатраты
);минимальный износ материальной части конвейера на транспортирование единицы веса груза
(минимальный удельный износ
).
3. Обзор исследований и разработок
Оптимальное управление по критерию минимальное время простоев добычных участков
достигается за счет предельного использования аккумулирующей способности линии, находящейся в зоне отказа. Предельное использование аккумулирующей способности линии, находящейся в зоне отказа, достигается путем применения следующих способов:
- Регулирование скорости ленты, обеспечивающее использование ее аккумулирующей способности за счет стабилизации погонной нагрузки на уровне номинального значения. Способ позволяет использовать аккумулирующую способность участков конвейерной ленты, не полностью загруженных в периоды непрерывных реализации забойного грузопотока при работе конвейеров в нормальном режиме на номинальной скорости. Параметры регулирования каждого принимающего груз конвейера определяются системой автоматического слежения за состоянием грузопотока на основании информации, формируемой в пределах измерительного интервала смежного подающего конвейера.
- Синхронизация моментов пуска (останова) конвейера с моментами поступления (прекращения поступления) груза на его ленту. Способ позволяет уменьшить среднюю скорость продвижения груза к точке отказа за счет отключения линии в интервалах отсутствия забойного грузопотока, частично или полностью использовать аккумулирующую способность свободных участков конвейерной ленты, не загруженных в периоды отсутствия забойного грузопотока при работе конвейеров в нормальном режиме на номинальной скорости. Степень использования аккумулирующей способности ленты зависит от фактического состояния загрузки части линии, находящейся между забоем и точкой отказа, т. е. в зоне отказа. Принципиально использование аккумулирующей способности ленты возможно, если на линии, находящейся в зоне отказа, имеется (в данный момент) свободный участок ленты в головной части хотя бы одного конвейера. Следует отметить, что данный способ автоматического определения последовательности н начальных моментов времени пуска (останова) конвейеров является наиболее общим и охватывает все другие известные способы, которые можно рассматривать как частные (ограниченные) варианты этого способа. Для реализации данного способа управления необходима информация о фактическом расположении груза по длине каждого конвейера линии. Если система управления располагает ограниченной информацией, например,
конвейерная линия загружена — конвейерная линия не загружена
, то в этом случае возможна реализация только частных вариантов данного способа:- при загруженной конвейерной линии — пуск против грузопотока (классический вариант), ускоренный пуск, одновременный регулируемый пуск;
- при незагруженной линии — пуск каждого конвейера в момент поступления груза на его ленту.
Современные системы автоматического управления конвейерными линиями шахт
К современным системам автоматического управления конвейерными линиями шахт относятся следующие системы:
- система автоматизированного управления разветвленными конвейерными линиями САУКЛ.
- комплекс автоматизированного управления конвейерными линиями типа АУК-3;
Система автоматизированного управления конвейерными линиями САУКЛ
Система автоматизированного управления разветвленными конвейерными линиями САУКЛ предназначена для:
- централизованного автоматизированного управления и контроля работы разветвленными и неразветвленными конвейерными линиями, состоящие из ленточных конвейеров, предназначенных для транспортирования груза и перевозки людей, с числом конвейеров, управляемых через один комплект АПУ и АЛС до 60 единиц, и неограниченным числом маршрутов;
- централизованного или местного автоматизированного управления и контроля работы отдельными конвейерами, входящими или не входящими в состав конвейерной линии;
- телеуправления и контроля состояния сопутствующим вспомогательным оборудованием (типа
шибер
,перегружатель
,питатель
); - автоматической регистрации и сохранения информации о работе конвейеров и сопутствующего оборудования, командах управления и настройках, защитных отключениях и блокировках.
Система САУКЛ рассчитана на применение в подземных выработках шахт, опасных по газу и пыли, но может также применяться на рудниках, обогатительных фабриках и других предприятиях.
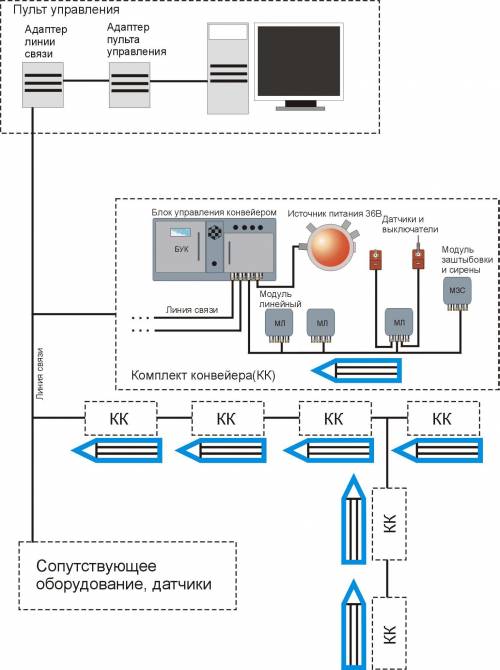
Рисунок – 2 Структурная схема системы САУКЛ
Комплекс автоматизированного управления конвейерами АУК.3 — аппаратура нового поколения на базе микропроцессоров.
Комплекс автоматизированного управления конвейерами АУК.3 предназначен для автоматизированного управления неразветвлёнными конвейерными линиями, состоящими из ленточных и скребковых конвейеров с общим числом конвейеров в линии до 10 включительно, исполнительными органами накопительных бункеров, монорельсовыми канатными дорогами (грузовыми), рельсовыми канатными напочвенными дорогами (грузовыми) и моноканатными дорогами кресельного типа. Комплекс является комплектующим изделием ленточного конвейера (линии конвейеров). Комплекс АУК.3 совместим с комплексом АУК.1М в части линии управления и связи. Комплекс рассчитан для эксплуатации в шахтах, в том числе опасных по газу и/или пыли в климатических районах с умеренным и холодным климатом.
Комплекс управления АУК.3 обеспечивает следующие виды управления:
- местное автоматизированное управление конвейером;
- централизованное автоматизированное управление конвейерной линией;
- автоматическое управление конвейерной линией, осуществляемое по командам технологических датчиков с соблюдением требуемых защитных отключений и блокировок;
- автоматический последовательный запуск конвейеров, включенных в линию в порядке, обратном направлению движения грузопотока;
- запуск части конвейерной линии;
- пуск конвейеров конвейерной линии без остановки уже работающих конвейеров;
- отключение части конвейерной линии;
- управление одиночным конвейером без применения пульта управления.
В режиме управления бункером:
- местное автоматизированное управление исполнительным органом бункера;
- автоматическое управление исполнительным органом бункера, осуществляемое по командам технологических датчиков или линии управления, с соблюдением требуемых защитных отключений и блокировок.
В режиме управления канатной дорогой: местное автоматизированное управление канатной дорогой.
В режиме работы ретранслятором: ретрансляция данных о состоянии составных частей комплекса.
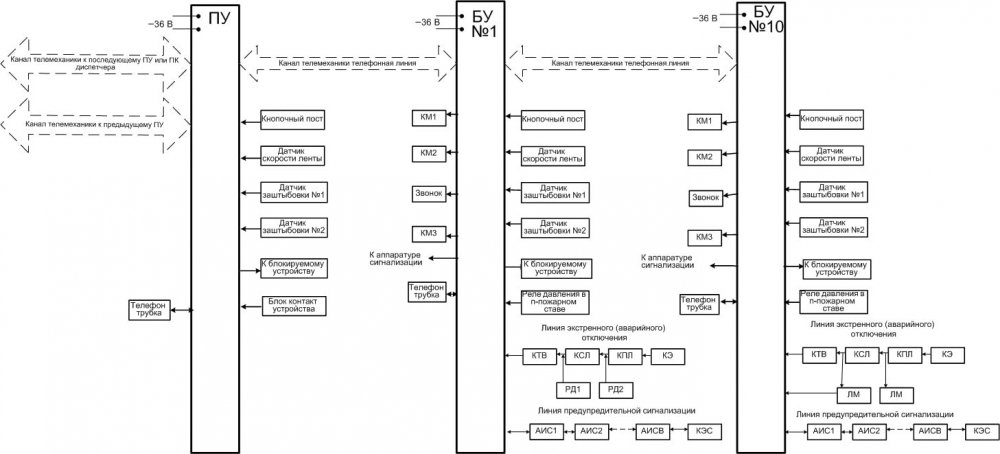
Рисунок – 3 Структурна схема комплекса АУК-3
4. Основные результаты исследований и разработки
Синхронное вращение электродвигателей многодвигательного ленточного конвейера, обусловленное технологическим требованием, обеспечиваетя в основном двумя способами: механическим соединением валов электродвигателей и электрическим соединением обмоток электродвигателей.
При конвейерах большой длины с многодвигательным электроприводом ставится задача автоматического регулирования отдельных двигателей с целью перераспределения нагрузки между ними и обеспечения равномерности натяжения ленты по ее длине.
При наличии на ленточном конвейере нескольких приводных станции место их установки выбирается по диаграмме тяговых усилий таким образом, чтобы тяговое усилие двигателей нескольких станции примерно равнялось усилию однодвигательного электропривода. Для построения диаграммы тяговых усилий вычерчивается трасса конвейера со всеми подъемами и спусками, перегибами, приводными и натяжными станциями, направляющими блоками и барабанами. Затем, если следовать от наименее нагруженного участка конвейера, производится учет потерь в каждом элементе и получается натяжение тягового органа по всей длине. Мощность приводного двигателя конвейера определяется по формуле
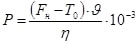
где: Р – мощность двигателя, кВт;
Fн – усилие на набегающем участке тягового органа, Н;
ϑ – скорость перемещаемого тягового органа, м/с;
η – к.п.д. приводного механизма.
Следует, однако, учесть, что для окончательного выбора мощности приводной станции необходимо построить уточненную диаграмму тяговых усилий для каждой ветви. Это уточнение вызвано тем обстоятельством, что сумма усилий всех участков может быть не равна усилию при однодвигательном приводе, что определяется уменьшением сечения тягового органа и соответственно снижением потерь на трение при многодвигательном приводе.
На рисунке 4 показаны распределения тяговых усилий между асинхронными электроприводами трехдвигательного ленточного конвейера.

Рисунок – 4 Схема к объяснению распределения тяговых усилий между асинхронными электроприводами трехдвигательного ленточного конвейера
В соответствии с тяговыми усилиями, определяемыми по рисунку 4 приращения скорости вращения, скольжения и моменты, развиваемые двигателями приводных устройств, подсчитываются по выражениям:
- при уменьшении нагрузки на привод
- при увеличении нагрузки на привод
Учет неравномерности распределения нагрузки приводов, которая может быть вызвана неидентичностью механических характеристик двигателей, целесообразно проводить после определения натяжений в тяговом органе при наиболее тяжелых режимах работы конвейера, так как влияние различия механических характеристик двигателей является постоянно действующим фактором, не зависящим от режима работы конвейера.
В связи с этим, неравномерность нагрузки электродвигателей многодвигательного конвейера может привести к рассогласованию скоростей приводов и порыву ленты. Для решения этой проблемы, на рисунке 4 показана система автоматического управления конвейерной линией при неравномерной загрузке. Экономический эффект повышается за счет применения частотно-регулируемого электропривода. САУКЛ состоит из шкафа управления, трех силовых шкафов и трех преобразователей частоты.
Конструктивно ШУ САУ КЛ выполнен в виде шкафа с панелью, на которой расположены: мнемотабло, индикатор, клавиатура, плата сопряжения.
Шкаф состоит из программируемого логического контроллера (ПЛК) и операторской панели. ПЛК обеспесчивает организацию вычислительного процесса в реальном масштабе времени. Датчик скорости (абсолютный энкодер) фиксирует факт снижения скорости конвейера и соответствующий релейный сигнал вводится и обрабатывается в САУ КЛ. Датчик веса, выполненный в виде роликоопор, сигнализирует о фактической загрузке конвейера и текущие данные также поступают в САУ КЛ.
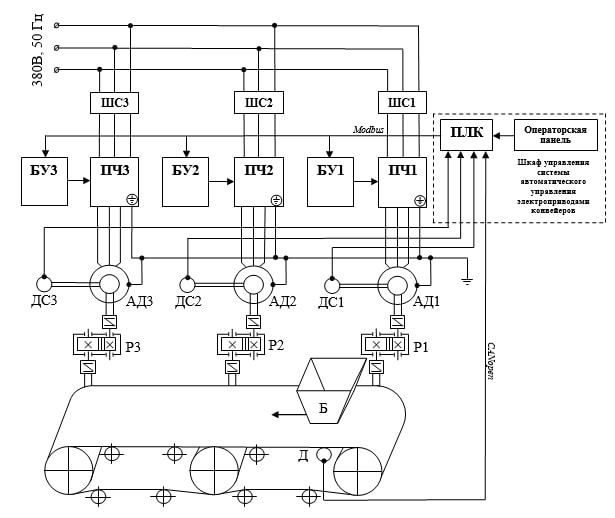
Рисунок – 5 Система автоматического управления конвейерными линиями
Работа данной системы заключается в следующем. Крупность кусков транспортируемой горной массы, зависящая от ее физико-механических свойств и способов разрушения, является главным фактором, определяющим загрузку конвейера. Таким образом, первым загружается ЭП1, и сигнал о массе руды от датчика веса поступает в ПЛК. Канал обратной связи по весу и скорости, предназначенный для получения фактических данных на каждом цикле системы управления, осуществляет коммуникационная сеть CANopen. В свою очередь, с ПЛК подается команда на блоки управления системы ПЧ-АД. С данной системой ПЛК соединен через специальный канал связи – протокол Modbus, реализуемый на коммуникационных разъемах Ethernet. Такая функция позволяет, за малое время, управлять многодвигательным электроприводом, своевременно обладать нужной информацией. Абсолютный энкодер, присоединенный к ротору АД, информирует функциональный контроллер о скорости двигателя, с целью поддержания синхронности вращения всех трех АД при неравномерной загрузке конвейера.
Выводы
В ходе работы были выдвинуты требования к системе мониторинга и управления конвейерным транспортом шахты, отличительной особенностью которых является координация режимов работы установок в зависимости от их текущего состояния и величины грузопотока с очистного забоя.
Таким образом, данная модернизированная система управления трехдвигательным асинхронным электроприводом ленточного конвейера позволяет поддерживать синхронное вращение всех приводов конвейера при неравномерной загрузке. Это достигается за счет согласованной работы всех элементов САУКЛ. Преимущество системы в том, что она полностью исключает пробуксовку барабанных приводов, которая является главной причиной порыва ленты. Исключение пробуксовки и достижение синхронности вращения приводных электродвигателей, позволит увеличит срок службы ленты, что имеет существенное значение.
Во время написания данного реферата магистерская работа еще не завершена. Окончательное завершение: июнь 2018 года. Полный текст работы и материалы по теме могут быть получены у автора или его руководителя после указанной даты.
Список источников
- Белов М.П., Новиков В.А., Рассудов Л.Н. Автоматизированный электропривод типовых производственных механизмов и технологических комплексов. – М.: Академия, 2004. – 576 с.
- Требования к автоматизации шахтных конвейеров и конвейерных линий. – М.: Недра, 1981. – 25с.
- Р. В. Мерцалов, Г. И. Солод, П. М. Трухин и др. Подземные механизированные бункера. – М.: Недра, 1985г. – 224с.
- Базер Э. Я., Богомолов А. С., Гудалов В. П. и др.: Под ред. Пейсаховича Г. Я. и Ремизова П. П. Справочник по шахтному транспорту. – М.: Недра, 1977. – 624с.
- Гаврилов П. Д., Гимельштейн Л. Я., Медведев А. Е. Автоматизация производственных процессов. Учебник для вузов. М.: Недра, 1985, 215 с.
- Шахмейстер Л. Г., Дмитриев В. Г. Теория и расчет ленточных конвейеров – 2-е изд., перераб. и доп. – М.: Машиностроение, 1987. – 336 с.
- Батицкий В. А., Куроедов В. И., Рыжков А. А. Автоматизация производственных процессов и АСУ ТП в горной промышленности: Учебник для техникумов. – 2-е изд., перераб. и доп. – М.: Недра, 1991. – 303с.
- Полунин В. Т., Папоян Р. Л. Эффективность регулирования скорости шахтных конвейеров. Научные труды МГИ, № 5. – М. – 1965.
- Петков О. Н. Разработка и исследование системы автоматического управления скоростью ленточного конвейера по входному грузопотоку / Диссертация на соискание ученой степени кандидата технических наук. – М.: Московский Ордена Трудового Красного Знамени Горный Институт, 1984. – 143с.
- Кречнев Э.Г., Селищев Ю.А. Об экономической эффективности применения регулируемых приводов в ленточных типажных конвейерах // Сборник «Конвейерный и рельсовый транспорт в горной промышленности» – М.: Недра, 1968. – С. 81–87.
- 3. Солод Г.И. О целесобразности применения многоприводных конвейеров // Сборник «Вопросы рудничного транспорта». – Киев: 1972. – С. 202–207.