Abstract
Content
- Introduction
- 1. The relevance of the topic
- 2. The purpose and objectives of the study
- 3. Review of research and development
- 4. Main results of research and development
- Conclusion
- References
Introduction
In large coal mines, coal is transported from the breakage faces to the skip winding through the multi-threaded line of conveyor transport. It consists of local conveyor lines and collecting conveyors - trunk conveyor lines. The local belt conveyor line provides the coal transportation from the skip winding to the transshipment point on the trunk conveyor line. Generally, transshipment is carried out through the transfer hopper.
1. The relevance of the topic
Modern underground conveyor lines are characterized by a considerable length (tens of kilometers) and branching of traffic arteries which in time change their parameters: length, topology, etc. The conveyor line can be unbranched and branched in the conditions of mines. The unbranched conveyor line is a single line where the cargo is supplied on each conveyor from the only one previous conveyor. The branched conveyor line is a multithreaded line, which consists of branches and a unit. It is necessary to coordinate modes of operation of the main trunk conveyor and local conveyors.
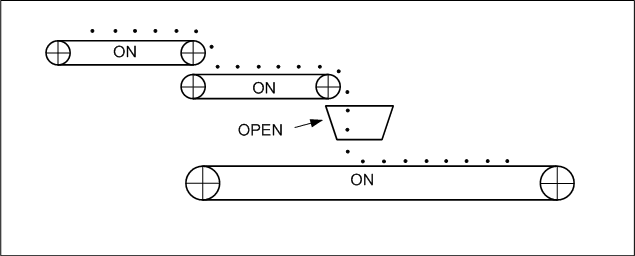
Figure – 1 The flow sheet of the conveyor line with a storage hopper
(animation: 8 frames, infinite repetition cycle, 42 kilobytes)
From the point of view of increasing the energy efficiency of conveyor transport, it is more expedient to regulate not the productivity of the conveyor, but rather the incoming cargo flow, bringing it closer to the nominal value. Many of the peculiar features of the mines atmosphere, where the conveyors work: volume of gas, humidity and chemical aggressiveness determine specific requirements for the conveyors automation equipment in terms of intrinsic safety of the control system, and also special explosion-proof construction.
2. The purpose and objectives of the study
Currently, almost all conveyor lines in mines are automated. However, the potential of automated control has not been exhausted completely. The task of optimal automatic control is coming to automatic search and automatic implementation of a variant of the system response to disturbance, where the most favorable operating mode of the object is achieved by the chosen criterion. Thus, the control system is closed in relation to the main technological parameter.
The main task of the optimal automatic control system is to minimize the limiting effect of the operating modes of the conveyor line on the productivity of the breakage face. The main task of the system follows from that auxiliary serving technological role played by the conveyor line in relation to the face.
In addition to this task, there is another task of the system of optimal automatic control of conveyor lines of mines, which is formulated as: a marginal decrease in operating costs per unit weight of transported cargo.
The criteria for this task are follows:
The minimum power consumption for transporting a unit of cargo weight
(minimum specific energy consumption
);Minimum wear of the material part of the conveyor for transportation of a unit of cargo weight
(minimum specific wear
).
3. Review of research and development
Optimum control according to the criterion minimum downtime of producing unit
is achieved due to the limiting use of the accumulating capacity of the line located in the failure zone.
The modern systems of automatic control of conveyor lines in mines are the following systems:
- automated control system of branched conveyor lines SAUKL;
- complex of automated control of conveyor lines AUK.3 type.
Automated control system of conveyor lines (SAUKL) is designed to:
- Automated management and control of branched and unbranched conveyor lines consisting of belt conveyors for transporting cargo and transportation of people, with the number of pipelines managed by one set of APU and ALS to 60 units and an unlimited number of routes;
- Local or centralized automated management and control of individual pipelines belonging or not belonging to the conveyor line;
- Remote control and status monitoring accompanying accessories;
- Automatic recording and storage of information on the work of the conveyors and related equipment, controls and settings, the protective shutdown and lockout.
SAUKL equipment designed for use in underground mines, hazardous gas and dust.
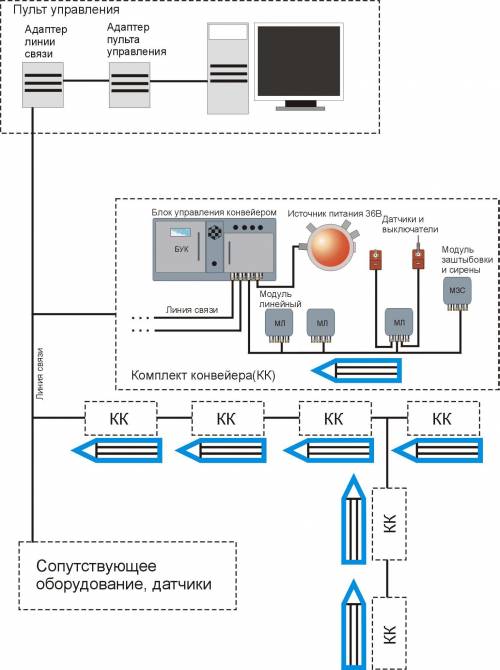
Figure – 2 Block diagram of the system SAUKL
AUK.3 complex – a new generation of equipment based on microprocessors and provides the following controls:
- local automated control of conveyor;
- automated management of the conveyor line;
- automatic control of the conveyor line, carried out by teams of technology sensors with the necessary protective shutdowns and lockouts;
- the automatic start sequence conveyors included in a line in a row in the reverse direction of movement of traffic;
- run part of the conveyor line;
- Start conveyor assembly line without stopping the conveyor is already working;
- off of the assembly line;
- control a single conveyor without control panel.
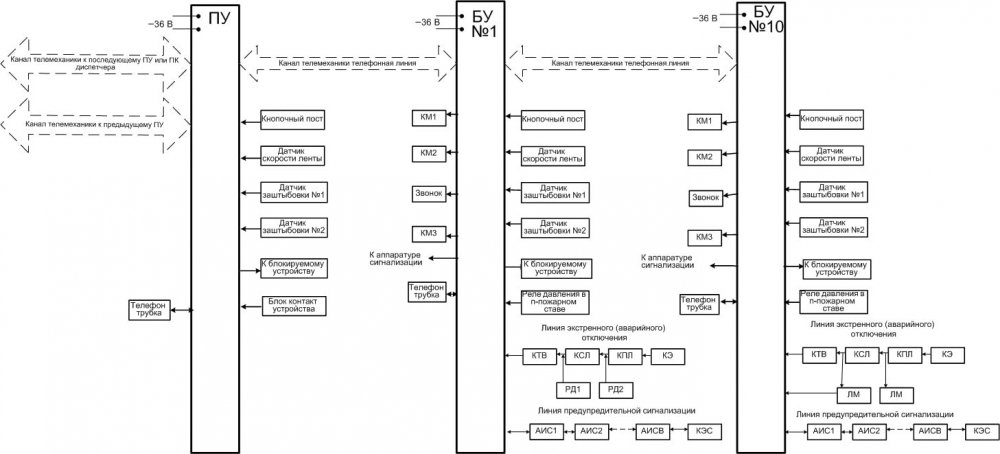
Figure – 3 Structural scheme of the complex AUK.3
4. Main results of research and development
Synchronous rotation of electric motors of the multiengined belt conveyor, due to the technological requirement, is provided basically in two ways: mechanical joint of the motor shaft and electrical coupling of the armature winding.
The task for long-center conveyers with the multimotor drive is to automatically regulate individual engines with a view to reallocation of load between them and ensure uniformity of belt tension along its length.
Figure 4 shows the distribution of tractive effort between asynchronous electric drives of a three-motor belt conveyor.

Figure – 4 The diagram to explain the distribution of traction forces between asynchronous electric drives of a three-motor belt conveyor
In this connection, the irregularly distributed load of the motors of the multiengined conveyor can lead to a misalignment between the speeds of the drives and the bursting of the belt. To solve this problem, figure 3 shows the system for automatic control of the conveyor line with the irregularly distributed load. The economic effect is enhanced by the use of a frequency-controlled electric drive. SAUKL consists of a control cabinet, three power cabinets and three frequency converters.
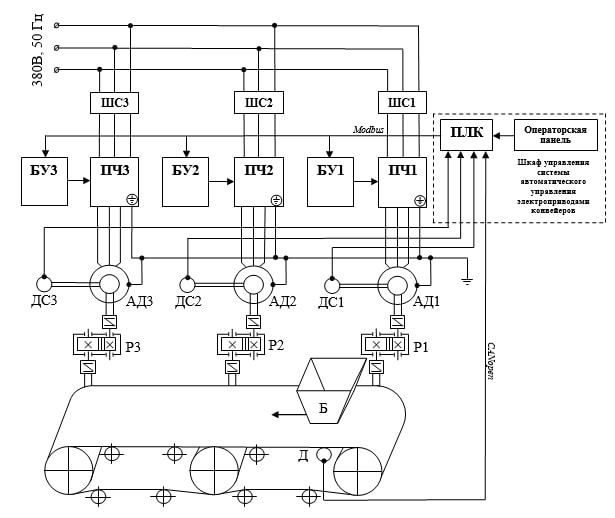
Figure – 5 Automatic control system for conveyor lines:
The work of this system is as follows. The size of the pieces of transported rock mass, which depends on its physical and mechanical properties and methods of destruction, is the main factor determining the loading of the conveyor. Thus, DV1 is loaded first, and the ore mass signal from the weight sensor is fed into the Programmable Logic Controller. A feedback channel for weight and speed, designed to obtain the actual data on each cycle of the control system, implements the CANopen communication network. In turn, a command is sent to the control units of the IF-AD system from the PLC. The programmable logic controller is connected with this system via a special communication channel - the Modbus protocol, implemented on Ethernet communication connectors. This function allows, for a short time, to control a multiengined drive, to have the necessary information in time. The absolute encoder connected to the rotor AD informs the functional controller of the motor speed, in order to maintain synchronous rotation of all three AE with the irregularly distributed load of the conveyor.
Conclusion
In the course of the course, requirements have been put forward to the system for monitoring and controlling the conveyor transport of the mine, the distinguishing feature of which is the coordination of the operating modes of the facilities depending on their current state and the magnitude of the cargo flow from the face.
Thus, this modernized control system of the three-motor asynchronous electric drive of the belt conveyor allows synchronous rotation of all conveyor drives in case of the irregularly distributed load. This is achieved through the coordinated work of all elements of SAUKL. The advantage of this system is that it completely eliminates slipping of the barrel-type drives, which is the main reason of the the bursting of the belt. The exclusion of slippage and the achievement of synchronous rotation of the drive motors will increase the service life of the belt, that have a significant importance.
At the time of writing this abstract, the master's thesis is not completed yet. Final completion: June 2018. Full text of the thesis and related materials can be obtained from author or his scientific adviser after the specified date.
Список источников
- Белов М.П., Новиков В.А., Рассудов Л.Н. Автоматизированный электропривод типовых производственных механизмов и технологических комплексов. – М.: Академия, 2004. – 576 с.
- Требования к автоматизации шахтных конвейеров и конвейерных линий. – М.: Недра, 1981. – 25с.
- Р. В. Мерцалов, Г. И. Солод, П. М. Трухин и др. Подземные механизированные бункера. – М.: Недра, 1985г. – 224с.
- Базер Э. Я., Богомолов А. С., Гудалов В. П. и др.: Под ред. Пейсаховича Г. Я. и Ремизова П. П. Справочник по шахтному транспорту. – М.: Недра, 1977. – 624с.
- Гаврилов П. Д., Гимельштейн Л. Я., Медведев А. Е. Автоматизация производственных процессов. Учебник для вузов. М.: Недра, 1985, 215 с.
- Шахмейстер Л. Г., Дмитриев В. Г. Теория и расчет ленточных конвейеров – 2-е изд., перераб. и доп. – М.: Машиностроение, 1987. – 336 с.
- Батицкий В. А., Куроедов В. И., Рыжков А. А. Автоматизация производственных процессов и АСУ ТП в горной промышленности: Учебник для техникумов. – 2-е изд., перераб. и доп. – М.: Недра, 1991. – 303с.
- Полунин В. Т., Папоян Р. Л. Эффективность регулирования скорости шахтных конвейеров. Научные труды МГИ, № 5. – М. – 1965.
- Петков О. Н. Разработка и исследование системы автоматического управления скоростью ленточного конвейера по входному грузопотоку / Диссертация на соискание ученой степени кандидата технических наук. – М.: Московский Ордена Трудового Красного Знамени Горный Институт, 1984. – 143с.
- Кречнев Э.Г., Селищев Ю.А. Об экономической эффективности применения регулируемых приводов в ленточных типажных конвейерах // Сборник «Конвейерный и рельсовый транспорт в горной промышленности» – М.: Недра, 1968. – С. 81–87.
- 3. Солод Г.И. О целесобразности применения многоприводных конвейеров // Сборник «Вопросы рудничного транспорта». – Киев: 1972. – С. 202–207.