Реферат за темою випускної роботи
Зміст
- Вступ
- 1. Актуальність теми
- 2. Мета і завдання дослідження
- 3. Огляд досліджень і розробок
- 4. Основні результати досліджень і розробки
- Висновки
- Перелік посилань
Вступ
На великих вугільних шахтах доставка вугілля від очисних забоїв до скіпового підйому здійснюється по багатопотокової лінії конвеєрного транспорту, що складається з дільничних конвеєрних ліній і збірних конвеєрів - магістральних конвеєрних ліній. Дільнична стрічкова конвеєрна лінія забезпечує транспортування вугілля від очисного забою до місця перевантаження на магістральну конвеєрну лінію. Як правило перевантаження здійснюється через проміжний бункер.
Основним видом управління конвеєрним транспортом шахти є автоматизоване управління, технічна суть якого полягає в централізації управління процесами пуску-зупинки конвеєрів в лінії, при забезпеченні автоматичного захисту від розвитку аварії в разі виникнення аварійних ситуацій.
1. Актуальність теми
Сучасні підземні конвеєрні лінії характеризуються значної протяжністю (десятки кілометрів) і розгалуженістю транспортних магістралей, що змінюють з часом свої параметри: довжину, топологію і т.п. В умовах шахт конвеєрна лінія може бути не розгалуженою і розгалуженою. Під не розгалуженою конвеєрною лінією розуміють однопоточну лінію, в якій вантаж на кожен конвеєр надходить тільки з одного попереднього конвеєра, а під розгалуженою - багатопоточну лінію, що складається з розгалужень і збірної частини. Для розгалужених конвеєрних ліній потрібне узгодження режимів роботи основних магістральних конвеєрів з дільничними.
Характерна багатоланковість конвеєрного транспорту, яка визначається великою протяжністю, а також наявністю горизонтальних і похилих виробок, що сполучаються між собою. Це призводить до необхідності в деяких випадках мати каскади послідовно встановлених стрічкових конвеєрів, кількість яких може становити до 10 і більше. Стрічкові конвеєри можуть бути прокладені по горизонтальних виробках, похилим і бремсберговым способом. Іноді в багатоланкових транспортних ланцюгах застосовують різні види транспорту, наприклад, локомотивний по горизонтальний і конвеєрний по похилій виробках. Потрібне узгодження режимів роботи різних видів транспорту.
Стрічкові конвеєри можуть бути обладнані одним приводним електродвигуном або декількома потужними електродвигунами. Наприклад, конвеєр 1Л80 обладнаний одним асинхронним електродвигуном з короткозамкненим ротором типу ВАО2-280L10 потужністю 45 кВт, а магістральний конвеєр 2ЛУ120В обладнаний двома асинхронним електродвигуном з фазним ротором типу АК312 49-6 потужністю 250 кВт кожен і т.д. Сумарна потужність електродвигунів дільничних конвеєрів становить 300-500 кВт, а магістральних - кілька тисяч кіловат, тому підземна транспортна система сучасної вугільної шахти нарівні з підйомними, водовідливними і вентиляторними установками є основним споживачем електроенергії. Частка енергоспоживання конвеєрного транспорту шахти становить близько 20% загальношахтного споживання електроенергії. Потрібне забезпечення роботи конвеєрних установок в енергозберігаючих режимах.
Висока нерівномірність вантажопотоків, що надходять на транспортні установки, так як конвеєрна лінія по своїм технологічним призначенням є транспортним об'єктом, обслуговуючим очисний забій. Технологічні паузи в роботі виїмкових комбайнів, в тому числі при аварійній зупинці лави, і періодична зміна їх швидкості переміщення уздовж лінії очисного вибою є причиною нерівномірності або відсутності вантажопотоків, які також відображаються на завантаженні конвеєра. При цьому характерне значне недовантаження магістральних конвеєрів; тривала робота в режимі холостого ходу. Це негативно позначається на техніко-економічних показниках використання коштів транспорту, тому що вони більшу частину часу своєї роботи мають істотне (в 2 ... 4 рази) недозавантаження, призводять до підвищення питомих витрат електроенергії.
В даний час на вугільних підприємствах для підвищення ефективності конвеєрного транспорту застосовуються вугільні акумулятивні бункери і пропонується регулювання швидкості руху конвеєрної стрічки з використанням частотно-регульованого приводу (ЧРП). На малюнку 1 представлена технологічна схема конвеєрної лінії з накопичувальним бункером.В сучасних стрічкових конвеєрах застосовують нерегульований асинхронний електропривод.
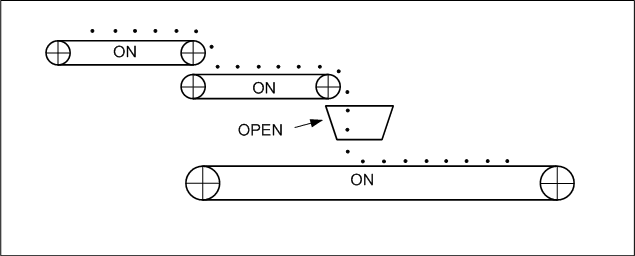
Малюнок – 1 Технологічна схема конвеєрної лінії з накопичувальним бункером
(анімація: 8 кадрів, нескінченний цикл повторення, 42 кілобайт)
Однак доцільність використання ЧРП має ряд спірних моментів. По-перше, діапазон регулювання частоти в сталому режимі для таких механізмів, особливо в похилих виробках, обмежений, щоб говорити про істотну зміну продуктивності. Збільшенню швидкості руху стрічки буде перешкоджати характеристика вантажу, який буде просто падати з конвеєра. При зменшенні частоти обертання необхідно забезпечити робочий момент на валу двигуна, до того ж використовувати високопродуктивний конвеєр для транспортування малого обсягу вантажу просто недоцільно. По-друге, тривала робота перетворювача в режимі знижених частот призведе до необхідності додаткового примусового охолодження як двигуна, так і самого перетворювача.
З точки зору підвищення енергоефективності конвеєрного транспорту доцільніше регулювати не продуктивність конвеєра, а вантажопотік, що надходить на нього, наближаючи його до номінального значення. Найбільш ефективним заходом для запобігання режиму холостого ходу і скорочення часу роботи конвеєрів шляхом забезпечення їх повного завантаження є застосування усереднюючих і акумулюючих бункерів, обсяг і продуктивність розвантаження яких будуть вирівнювати і визначати вантажопотік на забункерной конвеєрної лінії. Наприклад, за найскромнішими підрахунками, виключення холостого ходу і повне завантаження (через бункер) одного потужного магістрального конвеєра дозволить знизити добове електроспоживання до 1 МВт/ год при транспортуванні того ж обсягу горної маси, що істотно позначиться на значенні питомої витрати електроенергії. До того ж, застосування акумулюючих бункерів дозволить на час їх заповнення зупинити магістральні конвеєри великої потужності і перенести час їх роботи на періоди з меншою оплатою за електроенергію (наприклад, на нічний провал
) при розрахунку за диференційованим за зонами доби тарифу.
Пуск конвеєрної лінії повинен здійснюватися в напрямку, зворотному вантажопотоку, причому кожен наступний конвеєр повинен включатися після встановлення нормальної робочої швидкості руху тягового органу попереднього конвеєра. При пуску прикладене пусковий зусилля викликає виникнення пружної хвилі на ділянці стрічки, пов'язаної з приводним барабаном. Ця пружна хвиля поширюється уздовж стрічки, причому швидкість її поширення залежить від багатьох факторів, в тому числі і від зміни сили тертя і прискорення. Беручи до уваги ці особливості при пусковому режимі необхідно забезпечити: плавний пуск (для забезпечення безударного вибору люфтів в зубчастих передачах в початковий період рушіння, запобігання пробуксовки стрічки на приводному барабані) і забезпечення мінімальної тривалості процесу пуску (з метою скорочення пускових втрат в електроприводі з короткозамкненим електродвигуном).
Основні функціональні вимоги до системи автоматизації конвеєрними установками.
Система автоматизації повинна забезпечувати управління розгалуженими і нерозгалужених конвеєрними лініями, окремими конвеєрами і механізмами в лінії, а також режими пуску і зупинки, захисне відключення механізму блокування і сигналізацію.
Види управління: місцеве автоматизоване керування транспортним механізмом; централізоване автоматизоване управління конвеєрною лінією; автоматичне керування конвеєрною лінією.
Режими пуску: пуск конвеєрної лінії або її частини по командам від оператора або технологічних датчиків в послідовності, яка виключає завал місць перевантажень;
Режими зупинки: оперативний, аварійний і екстрений зупинки конвеєра.
2. Мета і завдання дослідження
В даний час майже всі конвеєрні лінії на шахтах автоматизовані. Однак потенційні можливості автоматизованого управління вичерпані не повністю. Продовжують залишатися актуальними наступні завдання: зниження трудомісткості обслуговування автоматизованих конвеєрних ліній, ймовірності відмов в роботі лінії і часу простоїв лінії в результаті відмови за рахунок поліпшення параметрів надійності і ремонтопридатності апаратури і технічних засобів автоматизації, а також розвитку інформаційних властивостей апаратури автоматизації дозволяють скоротити час пошуку причини і місця відмови; підвищення безпеки експлуатації за рахунок вдосконалення існуючих технічних засобів і створення засобів автоматизації нового функціонального призначення (наприклад, пристрій контролю критичної температури в конвеєрній виробці, пристрій контролю «залипання» силових контактів пускача приводу конвеєра та ін.).
Для шахтних конвеєрних ліній характерні обурення на вході об'єкта управління (дискретний характер забійних вантажопотоків і їх змінна інтенсивність в періоди безперервних надходжень), внутрішні обурення об'єкта управління (екстрені і аварійні зупинки конвеєрів лінії), обурення на виході об'єкта управління, пов'язані з обмеженою пропускною спроможністю пов'язаних транспортних ланок (приймального бункера, рейкового транспорту, вантажного підйому) або з порушенням нормального режиму їх роботи.
Завдання оптимального автоматичного управління зводиться до автоматичного пошуку і автоматичної реалізації такого варіанту реакції системи на обурення, при якому досягається найбільш вигідний за обраним критерієм режим роботи об'єкта. Таким чином, система управління є замкнутої по відношенню до основного технологічного параметру.
Слід мати на увазі, що автоматичне оптимальне управління є більш високим якісним щаблем розвитку загальної проблеми управління конвеєрним транспортом. Однак наявність вищого якісного щабеля не може само по собі служити гарантією доцільності застосування автоматичного оптимального управлінні на всіх шахтних конвеєрних лініях і не зумовлює необхідність повсюдного переходу від автоматизованого управління до оптимального автоматичного. В даному випадку необхідний диференційований підхід, що враховує параметри конкретного технологічного об'єкта (конвеєрної лінії).
Критерії та завдання оптимального автоматичного управління
В даний час досить широко поширена точка зору, згідно з якою основне завдання системи оптимального автоматичного управління конвеєрної лінією полягає в підвищенні фактичної продуктивності цієї лінії або навіть в досягненні максимально можливої продуктивності лінії, але таку постановку задачі не можна вважати прийнятною. Відомо, що конвеєрна лінія по своїм технологічним призначенням є транспортним об'єктом, обслуговуючим очисний забій і, отже, питання про величину фактичної продуктивності даного об'єкта має реальний сенс лише в зіставленні з інтенсивністю забійного вантажопотоку. Без зв'язку з забійними вантажопотоком завдання максимальної продуктивності конвеєрної лінії недостатньо конкретна. Зокрема, з такої постановки завдання випливає необхідність постійної роботи всіх конвеєрів лінії на номінальній або навіть максимально можливій швидкості.
Більш правильною є постановка завдання про забезпечення необхідної фактичної продуктивності конвеєрної лінії відповідно до інтенсивності забійного вантажопотоку. Однак і цей варіант постановки задачі не може вважатися досить конкретним. На підставі такої постановки завдання можна зробити висновок лише про те, що лінія повинна працювати за принципом змінної швидкості транспортування вантажу в ритмі забійного вантажопотоку.
Головне завдання системи оптимального автоматичного управління полягає в тому, щоб гранично знизити обмежуючий вплив режимів роботи конвеєрної лінії на продуктивність очисного забою, тобто головне завдання системи випливає з тієї допоміжної обслуговуючої технологічної ролі, яку відіграє конвеєрна лінія по відношенню до забою.
Обмежуючий вплив режимів роботи конвеєрної лінії на продуктивність видобувної дільниці проявляється виключно у вигляді простоїв лави через несправність конвеєрного транспорту. Тому головний критерій для систем оптимального автоматичного управління конвеєрними лініями доцільно формулювати в наступному вигляді: мінімальний час простою добувних ділянок за причини відмов конвеєрної лінії або відмов на виході конвеєрної лінії («мінімальний час простою»).
Крім зазначеного завдання, існує інша задача системи оптимального автоматичного управління конвеєрними лініями шахт, яка формулюється як: граничне зниження експлуатаційних витрат на одиницю ваги вантажу.
Критерії для зазначеного завдання формулюються в такий спосіб:
- «Мінімальний витрата електроенергії на транспортування одиниці ваги вантажу» («мінімальні питомі енерговитрати»);
- «Мінімальний знос матеріальної частини конвеєра на транспортування одиниці ваги вантажу» («мінімальна питома знос»).
3. Огляд досліджень і розробок
Оптимальне керування за критерієм «мінімальний час простоїв видобувних дільниць» досягається за рахунок граничного використання акумулюючої здатності лінії, що знаходиться в зоні відмови. Граничне використання акумулюючої здатності лінії, що знаходиться в зоні відмови, досягається шляхом застосування таких методів:
- Регуліровання швидкості стрічки, що забезпечує використання її акумулюючої здатності за рахунок стабілізації погонного навантаження на рівні номінального значення. Спосіб дозволяє використовувати акумулюючу здатність ділянок конвеєрної стрічки, не повністю завантажені в періоди безперервної реалізації забійного вантажопотоку при роботі конвеєрів в нормальному режимі на номінальній швидкості. Параметри регулювання кожного приймаючого вантаж конвеєра визначаються системою автоматичного стеження за станом вантажопотоку на підставі інформації, що формується в межах вимірювального інтервалу суміжного подаючого конвеєра.
- Сінхронізація моментів пуску (зупинки) конвеєра з моментами надходження (припинення надходження) вантажу на його стрічку. Спосіб дозволяє зменшити середню швидкість просування вантажу до точки відмови за рахунок відключення лінії в інтервалах відсутності забійного вантажопотоку, частково або повністю використовувати акумулюючу здатність вільних ділянок конвеєрної стрічки, які не завантажені в періоди відсутності забійного вантажопотоку при роботі конвеєрів в нормальному режимі на номінальній швидкості. Ступінь використання акумулюючої здатності стрічки залежить від фактичного стану завантаження частини лінії, що знаходиться між забоєм і точкою відмови, тобто в зоні відмови. Принципово використання акумулюючої здатності стрічки можливо, якщо на лінії, що знаходиться в зоні відмови, є (в даний момент) вільна ділянка стрічки в головній частині хоча б одного конвеєра. Слід зазначити, що даний спосіб автоматичного визначення послідовності на початкових моментах часу пуску (зупинки) конвеєрів є найбільш загальним і охоплює всі інші відомі способи, які можна розглядати як приватні (обмежені) варіанти цього способу. Для реалізації даного способу управління необхідна інформація про фактичне розташування вантажу по довжині кожного конвеєра лінії. Якщо система управління має обмежену інформацію, наприклад, «конвеєрна лінія завантажена - конвеєрна лінія не завантажена», то в цьому випадку можлива реалізація тільки часних варіантів даного способу:
- при завантаженій конвеєрної лінії - пуск проти вантажопотоку (класичний варіант), прискорений пуск, одночасний регульований пуск;
- при незавантаженої лінії - пуск кожного конвеєра в момент надходження вантажу на його стрічку.
Сучасни системи автоматичного управління конвеєрними лініями
До сучасних систем автоматичного управління конвеєрними лініями шахт належать такі системи:
- - система автоматизованого управління розгалуженими конвеєрними лініями САУКЛ;
- - комплекс автоматизованого управління конвеєрними лініями типу АУК-3.
Система автоматизованого управління конвеєрними лініями САУКЛ
Система автоматизованого управління розгалуженими конвеєрними лініями САУКЛ призначена для:
- централізованого автоматизованого управління і контролю роботи розгалуженими і нерозгалуженими конвеєрними лініями, що складаються з стрічкових конвеєрів, призначених для транспортування вантажу і перевезення людей, з числом конвеєрів, керованих через один комплект АПУ і АЛС до 60 одиниць, і необмеженим числом маршрутів;
- централізованого або місцевого автоматизованого управління і контролю роботи окремими конвеєрами, що входять або не входять до складу конвеєрної лінії;
- телекерування і контролю стану супутнім допоміжним обладнанням (типу
шибер
,перевантажувач
,живильник
); - автоматичної реєстрації і збереження інформації про роботу конвеєрів і супутнього устаткування, командах управління та налаштування, захисних відключеннях і блокуваннях.
Система САУКЛ розрахована на застосування в підземних виробках шахт, небезпечних через газ та пил, але може також застосовуватися на копальнях, збагачувальних фабриках та інших підприємствах.
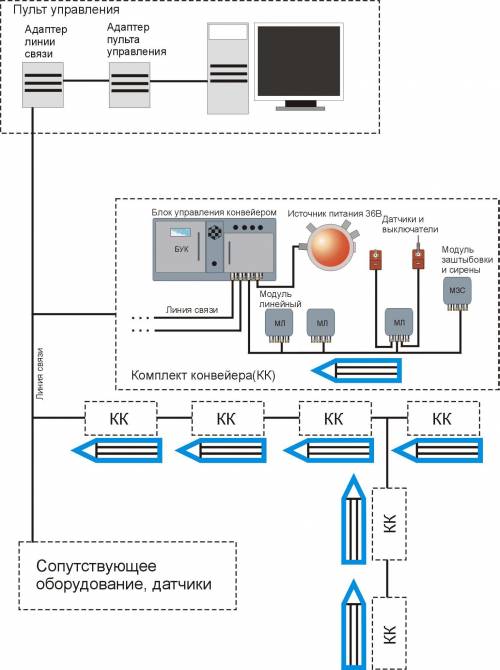
Малюнок – 2 Структурна схема системи САУКЛ
Комплекс автоматизованого управління конвеєрами АУК.3 - апаратура нового покоління на базі мікропроцесорів.
Комплекс автоматизованого управління конвеєрами АУК.3 призначений для автоматизованого управління нерозгалуженими конвеєрними лініями, що складаються з стрічкових і скребкових конвеєрів із загальним числом конвеєрів в лінії до 10 включно, виконавчими органами накопичувальних бункерів, монорейковими канатними дорогами (вантажними), рейковими канатними нагрунтовними дорогами (вантажними) і моноканатними дорогами крісельного типу. Комплекс є комплектуючим виробом стрічкового конвеєра (лінії конвеєрів). Комплекс АУК.3 сумісний з комплексом АУК.1М в частині лінії управління та зв'язку. Комплекс розрахований для експлуатації в шахтах, в тому числі небезпечних по газу і / або пилу в кліматичних районах з помірним і холодним кліматом.
Комплекс управління АУК-3 забезпечує наступні види управління:
- місцеве автоматизоване управління конвеєром;
- централізоване автоматизоване управління конвеєрною лінією;
- автоматичне керування конвеєрною лінією, що здійснюється за командами технологічних датчиків з дотриманням необхідних захисних відключень і блокувань;
- автоматичний послідовний запуск конвеєрів, включених в лінію в порядку, зворотному напрямку руху вантажопотоку;
- запуск частини конвеєрної лінії;
- пуск конвеєрів конвеєрної лінії без зупинки вже працюючих конвеєрів;
- відключення частини конвеєрної лінії;
- управління одиночним конвеєром без застосування пульта управління.
У режимі управління бункером:
- місцеве автоматизоване управління виконавчим органом бункера;
- автоматичне керування виконавчим органом бункера, що здійснюється за командами технологічних датчиків або лінії управління, з дотриманням необхідних захисних відключень і блокувань.
У режимі управління канатною дорогою: місцеве автоматизоване управління канатною дорогою.
У режимі роботи ретранслятором: ретрансляція даних про стан складових частин комплексу.
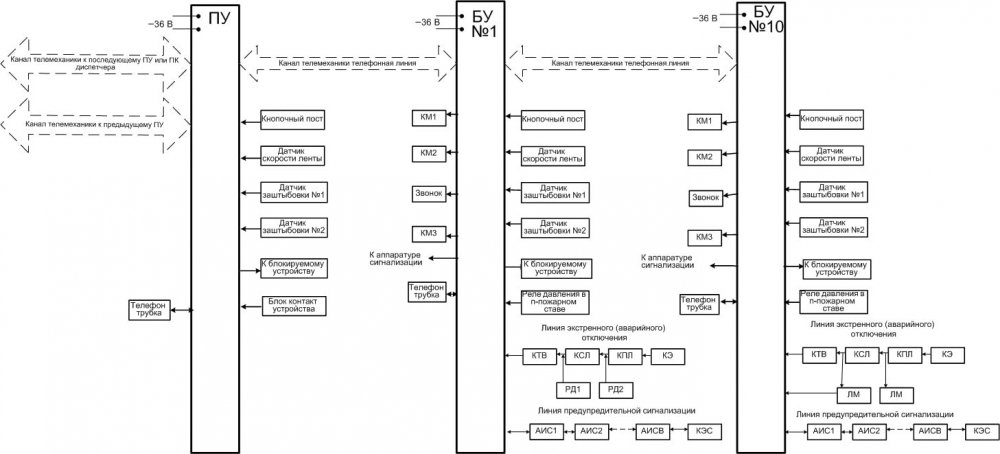
Малюнок – 3 Структурна схема комплексу АУК-3
4. Основні результати досліджень і розробки
Синхронне обертання електродвигунів багатодвигунного стрічкового конвеєра, обумовлене технологічною вимогою, забезпечується в основному двома способами: механічним з'єднанням валів електродвигунів і електричним з'єднанням обмоток електродвигунів.
При конвеєрах великої довжини з багатодвигунним електроприводом ставиться завдання автоматичного регулювання окремих двигунів з метою перерозподілу навантаження між ними і забезпечення рівномірності натягу стрічки по її довжині.
При наявності на стрічковому конвеєрі декількох приводних станцій місце їх установки обирається по діаграмі тягових зусиль таким чином, щоб тягове зусилля двигунів кількох станції приблизно дорівнювало зусиллю однодвигунного електроприводу. Для побудови діаграми тягових зусиль викреслюється траса конвеєра з усіма підйомами та спусками, перегинами, приводними і натяжними станціями, направляючими блоками і барабанами. Потім, якщо слідувати від найменш навантаженого ділянки конвеєра, проводиться облік втрат в кожному елементі і виходить натяг тягового органу по всій довжині. Потужність приводного двигуна конвеєра визначається за формулою
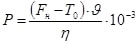
де: Р –потужність двигуна, кВт;
Fн – зусилля на набігаючій ділянці тягового органу, Н;
ϑ – швидкість переміщення тягового органу, м/с;
η – к.к.д. приводного механізму.
Слід, однак, врахувати, що для остаточного вибору потужності приводної станції необхідно побудувати уточнену діаграму тягових зусиль для кожної гілки. Це уточнення викликано тією обставиною, що сума зусиль всіх ділянок може не дорівнює зусиллю при однодвигунному приводі, що визначається зменшенням перетину тягового органу і відповідно зниженням втрат на тертя при багатодвигунному приводі.
На малюнку 4 показані розподіли тягових зусиль між асинхронними електроприводами тридвигунного стрічкового конвеєра.

Малюнок – 4 Схема до пояснення розподілу тягових зусиль між асинхронними електроприводами тридвигунного стрічкового конвеєра
Відповідно до тягових зусилль, обумовлених по малюнку 2 збільшення швидкості обертання, ковзання і моменти, що розвиваються двигунами приводних пристроїв, підраховуються за формулами:
- при зменшенні навантаження на привід
- при збільшенні навантаження на привід
Облік нерівномірності розподілу навантаження приводів, яка може бути викликана неідентичністю механічних характеристик двигунів, доцільно проводити після визначення натягів в тяговому органі при найбільш важких режимах роботи конвеєра, так як вплив відмінності механічних характеристик двигунів є постійно діючим фактором, що не залежать від режиму роботи конвеєра.
У зв'язку з цим, нерівномірність навантаження електродвигунів багатодвигунного конвеєра може привести до неузгодженості швидкостей приводів і розриву стрічки. Для вирішення цієї проблеми, на малюнку 3 показана система автоматичного управління конвеєрної лінією при нерівномірному завантаженні. Економічний ефект підвищується за рахунок застосування частотно-регульованого електроприводу. САУКЛ складається з шафи управління, трьох силових шаф і трьох перетворювачів частоти .
Конструктивно ШУ САУ КЛ виконаний у вигляді шафи з панеллю, на якій розташовані: мнемотабло, індикатор, клавіатура, плата сполучення.
Шафа складається з програмованого логічного контролера та операторської панелі. ПЛК забезпечує організацію обчислювального процесу в реальному масштабі часу. Датчик швидкості (абсолютний енкодер) фіксує факт зниження швидкості конвеєра і відповідний релейний сигнал вводиться і обробляється в САУКЛ. Датчик ваги, виконаний у вигляді роликоопор, сигналізує про фактичне завантаження конвеєра і поточні дані також надходять в САУКЛ.
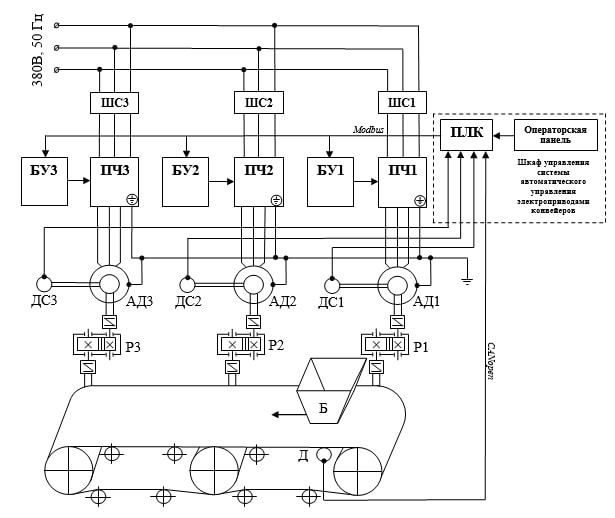
Малюнок – 5 Система автоматичного управління конвеєрними лініями
Робота даної системи полягає в наступному. Крупність шматків транспортованої горної маси, що залежить від її фізико-механічних властивостей і способів руйнування, є головним фактором, що визначає завантаження конвеєра. Таким чином, першим завантажується ЕП1, і сигнал про масу руди від датчика ваги надходить в ПЛК. Канал зворотного зв'язку за вагою і швидкості, призначений для отримання фактичних даних на кожному циклі системи управління, здійснює комунікаційна мережа CANopen. У свою чергу, з ПЛК подається команда на блоки управління системи ПЧ-АД. З даною системою ПЛК з'єднаний через спеціальний канал зв'язку - протокол Modbus, що реалізовується на комунікаційних роз'ємах Ethernet. Така функція дозволяє, за короткий час, управляти багатодвигунним електроприводом, своєчасно володіти потрібною інформацією. Абсолютний енкодер, приєднаний до ротора АД, інформує функціональний контролер про швидкість двигуна, з метою підтримки синхронності обертання всіх трьох АТ при нерівномірному завантаженні конвеєра.
Висновки
В ході роботи були висунуті вимоги до системи моніторингу та управління конвеєрним транспортом шахти, відмінною рисою яких є координація режимів роботи установок в залежності від їх поточного стану та величини вантажопотоку з очисного забою.
Таким чином, дана модернізована система управління тридвигунним асинхронним електроприводом стрічкового конвеєра дозволяє підтримувати синхронне обертання всіх приводів конвеєра при нерівномірному завантаженні. Це досягається за рахунок злагодженої роботи всіх елементів САУКЛ. Перевага системи в тому, що вона повністю виключає пробуксовку барабанних приводів, яка є головною причиною розриву стрічки. Виключення пробуксовки і досягнення синхронності обертання приводних електродвигунів, дозволить збільшити термін служби стрічки, що має істотне значення.
Під час написання даного реферату магістерська робота ще не завершена. Остаточне завершення: червень 2018 року. Повний текст роботи та матеріали по темі можуть бути отримані у автора або його керівника після зазначеної дати.
Список источников
- Белов М.П., Новиков В.А., Рассудов Л.Н. Автоматизированный электропривод типовых производственных механизмов и технологических комплексов. – М.: Академия, 2004. – 576 с.
- Требования к автоматизации шахтных конвейеров и конвейерных линий. – М.: Недра, 1981. – 25с.
- Р. В. Мерцалов, Г. И. Солод, П. М. Трухин и др. Подземные механизированные бункера. – М.: Недра, 1985г. – 224с.
- Базер Э. Я., Богомолов А. С., Гудалов В. П. и др.: Под ред. Пейсаховича Г. Я. и Ремизова П. П. Справочник по шахтному транспорту. – М.: Недра, 1977. – 624с.
- Гаврилов П. Д., Гимельштейн Л. Я., Медведев А. Е. Автоматизация производственных процессов. Учебник для вузов. М.: Недра, 1985, 215 с.
- Шахмейстер Л. Г., Дмитриев В. Г. Теория и расчет ленточных конвейеров – 2-е изд., перераб. и доп. – М.: Машиностроение, 1987. – 336 с.
- Батицкий В. А., Куроедов В. И., Рыжков А. А. Автоматизация производственных процессов и АСУ ТП в горной промышленности: Учебник для техникумов. – 2-е изд., перераб. и доп. – М.: Недра, 1991. – 303с.
- Полунин В. Т., Папоян Р. Л. Эффективность регулирования скорости шахтных конвейеров. Научные труды МГИ, № 5. – М. – 1965.
- Петков О. Н. Разработка и исследование системы автоматического управления скоростью ленточного конвейера по входному грузопотоку / Диссертация на соискание ученой степени кандидата технических наук. – М.: Московский Ордена Трудового Красного Знамени Горный Институт, 1984. – 143с.
- Кречнев Э.Г., Селищев Ю.А. Об экономической эффективности применения регулируемых приводов в ленточных типажных конвейерах // Сборник «Конвейерный и рельсовый транспорт в горной промышленности» – М.: Недра, 1968. – С. 81–87.
- 3. Солод Г.И. О целесобразности применения многоприводных конвейеров // Сборник «Вопросы рудничного транспорта». – Киев: 1972. – С. 202–207.