Abstract
Content
- Introduction
- 1. General information
- 2. Electric rolling mill
- 3. Modernization of rolling mills
- 4. Rolling parameters control system
- Conclusion
- List of sources
Introduction
Metallurgy for Donbass is one of the key, in many respects, direction. Here, as nowhere else, the concentration of producers and consumers of metal products is high. The main metallurgical enterprises of the Donbass are:
- Mariupol Illich Iron and Steel Works
- Metallurgical plant
Azovstal
- Donetsk Metallurgical Plant
- Enakievsky metallurgical plant
- Donetsk Metal Rolling Plant
- Alchevsk Metallurgical Plant
Donbass and Azov - the largest base of domestic metallurgy. The city of Mariupol produces the largest amount of metal in the country. Ferrous metallurgy is the leading branch of the heavy industry in the region, which also provides foreign exchange earnings at the end of the coal-coke-metal chain. In turn, the last link in this chain has in the field all the constituent stages of production: sinter, cast iron, steel, rolled products, pipes, metal products.
Ferrous metallurgy is one of the most profitable sectors of the economy of Donbass. Maintaining its potential is extremely important for the economic development of the country. The coal industry, the energy complex, the network of coke-chemical plants, the transport network, including the port of Mariupol, are tied to the infrastructure of the iron and steel industry.
1. General information
All rolling mills operating in metallurgical plants, despite the diversity of structures, are classified by purpose, number and location of work stands and rolls in work stands. Rolling mills, depending on the destination, i.e. on the type of products can be divided into the following three groups:
- Hot rolling mills, which include crimping, billet, rail beamed, varietal, wire, strip, sheet, broadband.
- Cold rolling mills, which include sheet, rolling mill and rolling mills for thin and very thin tape.
- Mills for special purposes - wheel rolling, bandage rolling, for rolling strips and profiles of variable cross section, balls, gears, screws, curved profiles, etc.
The main parameter of crimping, billet and section mills is the diameter of the rolls or gears of the gear stand in mm. If there are several working stands in the mill, the mill's parameter is the roll diameter of the finishing stand. Thus, the name "small section mill 250" means that the diameter of the work rolls or gears of the finishing stand is 250 mm, and its purpose is the production of small section steel.
By the number and location of the working stands, rolling mills are divided into the following five groups: single-stand, linear multi-stand, sequential, semi-continuous and continuous (Fig. 1).
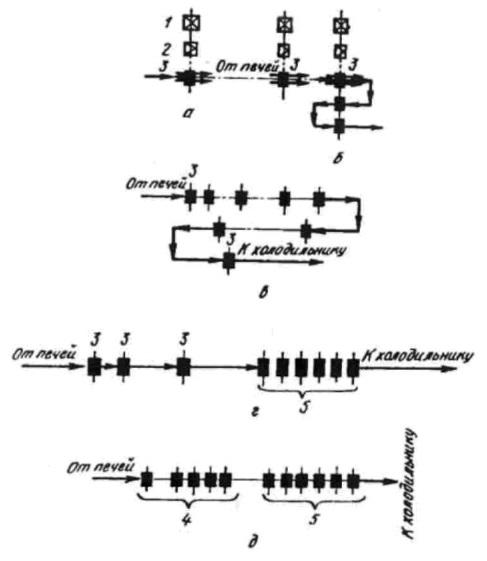
Figure 1 - Technological schemes of rolling mills
According to the location and number of rolls in the working stands and their design, rolling mills are divided into several groups: two-, three-, four- and multi-roll, universal special designs (Fig.2).
Two-roll stands are the most common, and are reversible and non-reversible. In the reverse rolls, the rolls have a variable direction of rotation.
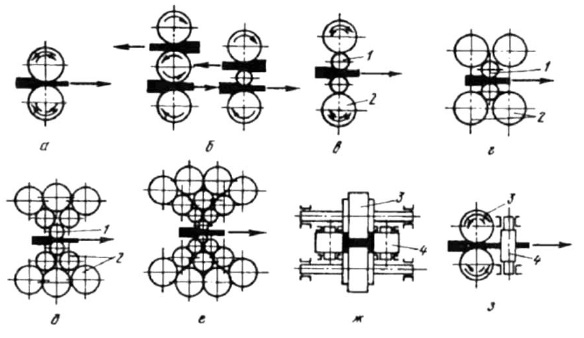
Figure 2 - The layout of the rolls in the working stands: a - double roll stand; b - three-roll varietal and sheet; c - four-roll stand; d - six-level stand; e - twelve mill stand; f - dvadtsatomalkovaya cage; g - universal beam cage; j - universal slab cage
2. Electric rolling mill
Metal can be given the desired shape using various methods. Widespread rolling material. An important role in this process is played by the electric drive of the rolling mill. Its characteristics determine the speed of metal processing, operational reliability, the value of the moment of inertia, etc. The electric drive of the rolling mill is subjected to a shock load exceeding the nominal load of the engines.
Electric rolling mill called controlled system, the main purpose of which is the conversion of electrical energy into mechanical and recovery in braking conditions. Depending on the type and design features of the equipment, the electric drive can be main, auxiliary, reversible, irreversible, individual or group.
The main electric drives of the rolling mill often contain several engines to ensure the stable operation of complex mechanisms. Reverse type devices require minimal transient time. This is due to the fact that they are used at the beginning of the production line of rolled steel and set the productivity of the entire production.
Correct determination of mechanical characteristics is the first step when choosing an electric drive of a rolling mill. Modern devices should be distinguished by a minimum moment of inertia, rigid mechanical parameters, high overload stability of the moment, large limits of speed control, large starting torque. All these characteristics, including high efficiency, have DC motors with independent excitation. When choosing a main drive for a rolling mill, the following conditions should be taken into account:
- the duration of the continuous operation of the installation;
- significant drive power;
- shock load;
Usually the DC motor should be controlled by the armature voltage. In mathematical calculations, it is assumed that the resistance of the armature circuit and the inductance will be constant, and the demagnetizing action is considered to be compensated. The dependence of the magnetic flux on the magnetizing force will be linear. To build a block diagram of DC motors, they form a system of differential levels, with the help of which they calculate:
- electromotive force of thyristor converter;
- force opposed to the motor electromotive force;
- armature current value;
- the total resistance of the anchor chain;
- the moment developed by the engine;
- total moment of inertia of the drive.
When calculating the rolling mill drive, not only the nominal data, but also the parameters characterizing its performance under overloads at different speeds are taken into account. Technical characteristics of individual electric drives of the rolling mill are determined taking into account the speed of the rolls to which they relate. When calculating the mechanical characteristics of a DC motor, it will be necessary to determine the following values:
- nominal moment;
- perfect idle speed.
The calculation of these values is a mandatory step before the calculation of the rolling mill drive. The nominal moment is calculated by the following formula:
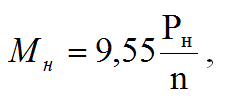
where Mн - is the nominal moment, Pн - is the nominal power, n - is the nominal speed of rotation of revolutions per minute.
Figure 3 shows the appearance of a modern broadband cold rolling mill.
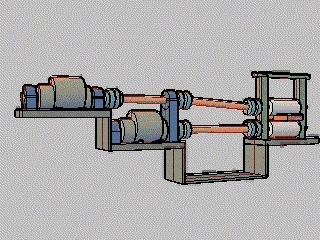
Figure 3 - The appearance of the rolling mill
(7 frames, 6 cycles, 635 kb)
3. Modernization of rolling mills
The rolling mill is a set of equipment intended for plastic deformation of the metal in the rolls (actually rolling), as well as transport and auxiliary operations. The rolling shops or departments generally include equipment for the main line of the rolling mill comprising roughing, intermediate and finishing work stands and transmission mechanisms, as well as heating furnaces, systems for descaling, equipment for transporting, cutting, heat treating, finishing, dressing, winding, marking, packing rolled.
The main objectives of the modernization of rolling production are to obtain finished products of specified sizes and shapes in the required amount, with the lowest possible costs, with a high level of physical and mechanical properties and surface quality. During the modernization, the characteristics of electric drives are improved and modern technical means of automation are installed.
Crimp rolling mills, blooming and slabing, intended for the production of ingots of steel, are historically considered to be not convenient objects for automation. The reason for this is the technology itself reverse rolling, which consists in the fact that the workpiece repeatedly passes through the mill rolls back and forth. With each pass, the roll solution changes, the metal is transferred from caliber to caliber several times and the workpiece rotates 90 degrees (turning). Due to the large number of mechanisms involved in the rolling process, the instability of the state of the metal in terms of temperature, ingot form, presence of scale, the rolling process of even two consecutive ingots may differ, especially during the first passes (passes) through the mill rolls.
4. Rolling parameters control system
To control the rolling processes, it is necessary to constantly monitor the geometric and temperature parameters of rolled products. The effectiveness of management processes in most cases is determined by the many zones of control of roll parameters along the rolling line.
The parameters of the car are measured in two ways: by fixing the moments when the roll passes through certain technological zones and by measuring the quantitative characteristics of the geometrical and temperature parameters of the roll in different technological zones. The main means of obtaining fixed and quantitative characteristics of rolled products are optical and magnetic sensors. The use of magnetic sensors is limited to the temperature range of the rolled material. The most versatile are optical sensors.
In [1], a sensor based on a linear photodetector is used to determine the position and geometrical dimensions of the roll, allowing to determine both the position parameters and the quantitative characteristics of the roll geometry in any of the technological zones. The linear photodetector in the composition of the sensor forms a direction vector, according to which the axis of sight of the sensor is determined. Depending on the orientation of the sensor axis with respect to the rolling line, it is possible to measure geometrical parameters both along the section and along the length. The photodetector of the sensor can operate both in the mode of monitoring the parameters of the actively glowing bar (up to temperatures of about 500 ° C) and in the mode of monitoring the parameters of the “shade” of cold rolled steel.
All sensor functions are implemented by means of a microprocessor controller, which manages the photoreceiver device, monitors its parameters and organizes interface interaction with the computational facilities of the main process automation system. Depending on the configuration of the sensor facilities, a set of implemented functions and features of the interface interaction with the main computer of the system are generated by software.
Determination of the geometric dimensions of the roll is carried out by measuring the length of the projection of the monitored geometric parameter in the plane of the sensor axis. Processing information from the photodetector allows you to create a field of discrete states.
An important parameter of the sensor is to ensure the required interval of periodization of measurements. The required interval value is determined on the basis of an estimate of the resulting measurement error, which is performed in the process of continuous movement of the roll.
The prototype of the sensor has been tested at various technological sites for the production of rolled products under the conditions of continuous billet mill of Krivorozhstal blooming
Also the main parameters that should be controlled during rolling are:
- Push forward or backward; The speed signal is controlled by the software, the signal range is individual.
- Spindle positioning (generates a low speed signal for the stand with the same range as the jog).
For electric controlled [2]:
- The current of the armature circuit of drive motors
- Power supply drive voltage
- Roll rotation speed
- Synchronization of the rotational speeds of the lower and upper rolls of the rolling mill
- generating a speed reference signal for the drives of the upper and lower rolls of the stand
- separation of metal capture / rolling modes
- compliance with the reduction mode for the roll solution and the rolling pattern for the movement of metal in gauges;
- misalignment of the currents and speeds of the drives of the upper and lower rolls and correction of the reference signals when such mismatches occur
- limit values of reductions and a ban on the operation of equipment with gross errors of operators with the issuance of appropriate messages.
The functions of the parameter control system also include the indication of the operating modes of the main drives and the issuance of messages to the attendant on the machine room and to the operator; event logging, the accumulation of statistical data.
The [3] describes the emergency modes control subsystem, which functions autonomously from the control system and provides continuous recording of drive and switching parameters in the control system to preserve the history of emergency processes.
The software implements all the described functions of the system, has the means for organizing the required data collection and processing processes, allowing to perform all automated functions in real time in all regulated modes of the system. Software control is built in accordance with the following principles:
- multitasking (simultaneous execution of several tasks);
- software hierarchy (different priorities for programs of different levels);
- openness (possibility of modification and expansion);
- flexibility (the ability to quickly reconfigure management programs and make changes to technological databases);
- reliability (compliance with a given algorithm of work, the absence of false actions).
Conclusion
The use of modern hardware and software in the management of rolling mills allows for the implementation of, in addition to the main, a number of additional (service) functions that provide increased operational reliability and a certain comfort in the work of the service personnel.
List of sources
- Moore E.F. Gedanken-experiments on sequential machines / E.F. Moore // Automata studies, Annals of mathematical studies. – 1956. – vol. 34. – pp. 129-153.
- О.И. Демьяненко, А.А. Коринь. Система автоматического контроля и учета проката на НЗС 900/700/500 / О. И. Демьяненко, А. А. Коринь, и др. – Металл и литье Украины. 2004. – 65-67 с.
- Двухровневая система повышенной надежности для автоматизации управления раскроем заготовок на прокатном стане / Материалы восьмого международного на учно-практического семинара «Практика и перспективы развития партнерства в сфере высшей школы». – Донецк-Таганрог. апрель 2007. – 87-95 с.
- Ш. Адамия. Оптимизация динамических нагрузок прокатных станов/ Ш. Адамия. – М.: Металлургия, 1978.
- Роман Федоряк, Константин Лейковский, Алексей Светличный. Система контроля технологии и управления скоростными режимами прокатного стана – Донецк. 2001.
- Ito M. Algebraic theory of automata and languages / M. Ito. – World Scientific Publishing, 2004. – 199 pp.
- А.А. Восканьянц. Автоматизированное управление процессами прокатки / А.А. Восканьянц. – М. 2010.
- Гусев Б.С. ', Достлев Ю.С., Краснокутский В.Л. Средства контроля параметров горячего прокатасистеме автоматизации технологических процессов прокатных станов / Гусев Б.С. ', Достлев Ю.С., Краснокутский В.Л. – Донецк., 2004.
- Уэйкерли Д. Проектирование цифровых устройств / Д. Уэйкерли. – М.: Постмаркет, 2002. – Том 2. – 528 с.
- Breeding K. Digital design fundamentals / K. Breeding. – Prentice Hall, 1992. – 446 pp.
- Привод прокатного стана [Электронный ресурс]. – Режим доступа: http://fif-group.ru....