Реферат по теме выпускной работы
Содержание
- Введение
- 1. Актуальность темы
- 2. Цель и задачи исследования
- 3. Машинный зал – составляющая цеха улавливания
- 4. Структура машинного зала
- 5. Экономические аспекты работы машинного зала
- 6.Эффективность работы
- Выводы
- Список источников
Введение
Большую роль в цехе играет машинно-конденсационное отделение. В машинном зале устанавливается несколько газовых нагревателей. Их еще называют газодувками. Они предназначены для того, чтобы извлекать газ из коксовых печей и пропускать его через специальное оборудование цеха улавливания и цеха сероочистки, а затем очищенный газ возвращать назад в коксовый цех как топливо. Если машинное отделение остановится, то есть не станут функционировать газодувки, то не станут работать коксовые печи и прекратится процесс коксования. Машинно-конденсационное отделение считается одним из самых трудных и ответственных мест на производственном предприятии.
1. Актуальность темы
Стабильное функционирование коксохимического предприятия в целом во многом определяется надежной и оптимальной работой машинного зала цеха улавливания химических продуктов коксования, в частности оборудования машинно–конденсационного отделения. В машинном зале устанавливается несколько газовых нагнетателей (газодувок). Они предназначены для отсоса газ из коксовых печей и создания давления для его подачи через специальное оборудование цеха улавливания и цеха сероочистки вплоть до возврата очищенного газа в коксовый цех для обогрева печей. При аварийной остановке газодувок машинного отделения нарушается гидравлический режим коксования и непродолжительная работа коксовых печей возможна лишь при открытых стояках с выбросами всего газа в атмосферу, где он сразу же воспламеняется. Поэтому оптимизация работы машинно–конденсационного отделения является одной из самых ответственных задач. Это особенно актуально в связи с возросшими требованиями экологических служб.
2. Цель и задачи исследования, планируемые результаты
Целью работы являлась разработка научных принципов совершенствования (модернизации) существующих технологий и специализированного оборудования, повышения качества выпускаемой продукции, создание технологий для производства новых видов готовой продукции. Для получения результата осуществлялось:
• исследование состава и физико–химических свойств исходного сырья как одного из важнейших факторов, влияющих на технологический процесс и на качество получаемого результата;
• математическое моделирование проводимых процессов разделения газа в промышленных установках, разработка технических решений по повышению эффективности работы;
• совершенствование технологических процессов и аппаратурного оформления, разработка рекомендаций по оптимизации параметров процессов и на этой основе улучшение качества товарных продуктов.
3. Машинный зал – составляющая цеха улавливания
Комплекс цехов улавливания коксохимического завода, который правильнее было бы назвать Отделение обработки коксового газа
[1], предназначен для отвода коксового газа от печей, охлаждения его с выделением конденсирующихся смолы,
воды, извлечения из газа аммиака, пиридиновых оснований, бензольных углеводородов, очистки газа от нафталина, сероводорода и цианистого водорода и передачи газа до потребителей или станции повышения давления.
Отделение обработки коксового газа является одним из важнейших технологических узлов коксохимического предприятия, без нормальной работы которого функционирование коксового цеха и всего производства в целом невозможно.
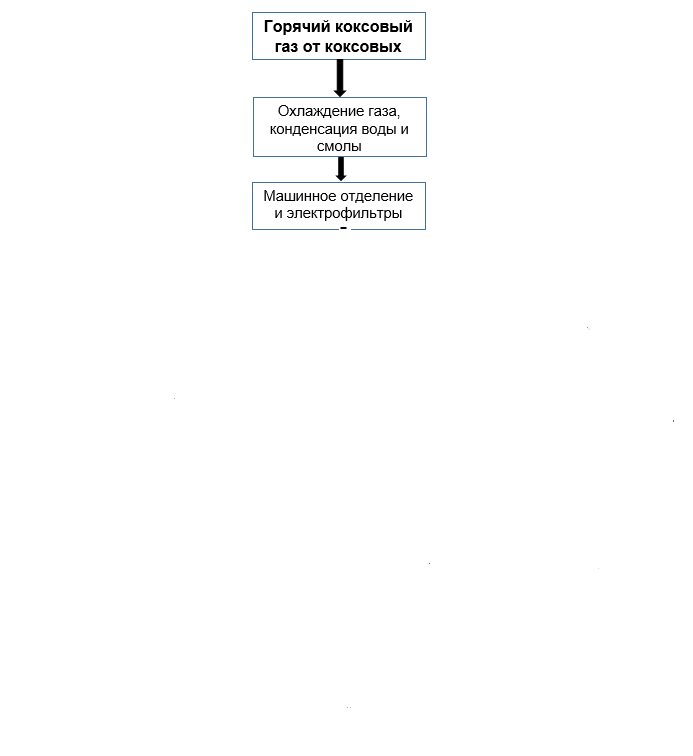
Рис. 1 – Варианты схем (А, Б, В) обработки коксового газа
(анимация: 5 кадров, 5 циклов повторения, 65.3 килобайт)
Последовательность обработки коксового газа на различных предприятиях может различаться. На рис.1 показаны различные варианты схем обработки коксового газа. Вариант В обладает следующими преимуществами:
–аммиачная сероцианоочистка, включающая узел очистки от нафталина, позволяет использовать собственный поглощающий агент и вести последующую обработку газа, свободного от агрессивных и усложняющих работу агентов;
–улавливание аммиака в круговом аммонийно–фосфатном процессе позволяет по простой технологии получать безводный аммиак, не расходуя посторонние реагенты и предусматривать полное уничтожение аммиака;
–исключается сложный узел конечного охлаждения газа, значительно сокращаются затраты тепла и воды.
Возможно частичное использование решений варианта В, например, замена в варианте А производства сульфата аммония на приготовление безводного аммиака. Нафталиноочистка может быть предусмотрена также либо при первичном, либо при конечном охлаждении. Для всех вариантов характерным является обработка большого объема ядовитого и взрывоопасного газа, насыщенного парами воды, при давлениях, незначительно отличающихся от атмосферного (разрежение перед нагнетателем 4 – 5 кПа, а избыточное давление на стороне нагнетания 20 – 30 кПа). Смеси коксового газа с воздухом взрывоопасны при содержании в них коксового газа от 6 до 30% об. Поэтому вся работающая газовая аппаратура должна быть герметичной, все газопроводы, как и все аппараты, должны быть снабжены надежно работающими гидрозатворами и конденсато–отводчиками; большая часть аппаратуры и газопроводов размещается вне помещения. Учитывая значительные перепады температур в течение года, необходимо оснащение трубопроводов системой термокомпенсации, оснащение всех гидрозатворов и конденсатоотводчиков системой обогрева. Эксплуатация газового хозяйства отделения обработки газа [1] усложняется из–за присутствия в газе паров нафталина, аэрозолей нафталина и смолы. Высокая летучесть нафталина и способность его к образованию аэрозолей, равно как и высокая температура его кристаллизации (80 °С), способствуют его перемещению практически по всему газовому тракту и создают опасность образования нафталиновых пробок в газопроводах и других коммуникациях. Необходимо контролировать сопротивление аппаратов и участков газопроводов, уровень жидкости в аппаратах. Контроль сопротивления и отключение аппарата, группы аппаратов, участка газопровода на ревизию, очистку, пропарку или промывку в случае превышения предельно допустимого сопротивления – важное условие нормальной эксплуатации отделения обработки газа.
Токсичность и взрывоопасность коксового газа делает особо ответственной организацию работ при пуске и остановке аппаратуры, при отключении аппаратов или участков газопровода на ремонт. Любые неработающие аппараты или участки газопроводов должны быть отключены заглушками по всем без исключения коммуникациям – по газу, пару, маслу, воде, конденсату, импульсным линиям КИП и т.п., независимо от наличия запорной арматуры. Аппараты должны быть соединены с атмосферой, состояние среды в них должно контролироваться. Существуют некоторые общие правила проектирования и эксплуатации систем газового и водного хозяйства отделения обработки газа.
Расположение установок отделения обработки газа должно предусматривать высокий коэффициент застройки. Это важно не только для лучшего использования земли, но особенно для сокращения длины коммуникаций. Использование коротких коммуникаций уменьшает капитальные и эксплуатационные затраты, тепловые потери и энергетические затраты на транспортирование газов и жидкостей, повышает надежность и уменьшает инерционность регулирующих устройств. Сокращение протяженности коммуникаций особенно важно при транспортировании кристаллизующихся или выделяющих отложения сред. Это относится, например, к газопроводам коксового газа, насыщенного нафталином. В то же время должна быть предусмотрена возможность доступа к основному оборудованию, возможность ремонта и монтажа–демонтажа наружного оборудования автокранами или автомашинами с монтажной вышкой.
Для сокращения энергозатрат и повышение надежности работы коксового блока и отделения обработки газа необходимо соблюдение следующих условий: наименьшая длина газопроводов; сокращение местных сопротивлений за счет правильного выбора конфигурации и расположения колен, тройников и т.п.; минимальное количество регулирующих устройств (диафрагмы, дроссели и т.п.).
Последнее условие определяет наметившуюся тенденцию использовать для каждого нагнетателя свой самостоятельный газовый поток: от коксовой батареи до выхода газа из системы его обработки. Это упрощает и уменьшает количество регулирующих (распределяющих) устройств. Там, где газовый поток распределяется по параллельно работающим аппаратам (в особенности это относится к газовым холодильникам)
приходится принимать специальные меры для поддержания одинакового сопротивления аппаратов [2]: непрерывная промывка межтрубного пространства первичных газовых холодильников, чтобы предотвратить отложение нафталина, промывка сатураторов и т.п.
Отделение обработки коксового газа – самый крупный потребитель охлаждающей воды, расходуемой на охлаждение газа в первичных холодильниках, на конечное охлаждение газа, на охлаждение потоков циркулирующих растворов и конденсацию паров в цехах улавливания аммиака, сероцианоочистки, улавливания бензольных углеводородов.
Представление о количестве отводимого тепла дает количество воды, теряющейся на испарение в градирнях, составляющее летом 0.42 – 0.55 Нм3/т кокса, а зимой, уменьшающееся до 0.30 –0.39 Нм3/т кокса, что составляет до 1.5% об. от количества воды, циркулирующей в цикле оборотного водоснабжения отделения обработки газа. Кроме того, 0.10 – 0.13 Нм3 воды на 1 т кокса выносится в виде брызг и еще 0.05 Нм3/т
выводится из цикла оборотного водоснабжения (так называемые родувочные воды
), чтобы предотвратить накопление в последнем солей.
В результате система оборотного водоснабжения и градирни оказываются важным элементом цеха улавливания, а от правильного выбора конструктивных решений зависит качество работы основного оборудования, существенно зависящее от температуры газа и. абсорбентов, надежность работы оборудования и, в частности, его коррозия. Дело в том, что на территории коксохимического завода велико число увлажняющих атмосферу объектов: градирни, башни мокрого тушения со шламовыми отстойниками, аэротехники биохимических установок, "воздушки", выбрасывающие водяной пар и пары агрессивных веществ. Увлажнение воздуха серьезно увеличивает опасность коррозии оборудования, что усугубляется еще и значительной запыленностью воздуха. Расположение градирен вблизи увлажняющих воздух аппаратов ухудшает их работу: влажный воздух ухудшает работу градирен, на несколько градусов повышая температуру "мокрого термометра" и, соответственно, увеличивая температуру охлажденной оборотной воды. Серьезную опасность представляет и пыль, находящаяся в атмосфере промышленных предприятий. Большие количества воздуха, проходящие через градирню, освобождаются в ней от пыли, количество которой оказывается значительно больше, чем количество солей и ила, вносимых со свежей водой. Работа системы оборотного водоснабжения в очень большой мере зависит от взаимного расположения градирен, основных установок цеха улавливания и источников пылеобразования. Их размещение должно осуществляться с учетом "розы ветров" и свободного притока свежего воздуха.
На работу градирен влияет величина перегрева оборотной воды в теплообменной аппаратуре выше 42 – 45°С, при этом начинается разложение бикарбоната кальция:
Са(НС03)2 = СаСОз + Н20 + С02.
В результате увеличивается агрессивность паров воды и одновременно начинается отложение мелкодисперсного, плохо растворимого карбоната кальция на металлических конструкциях и насадке градирен. На некоторых заводах отмечались случаи обрушения насадки из–за увеличения ее массы под действием отложений. Опыт ряда отраслей показывает, что стабильный безнакипный режим работы градирен и теплообменной аппаратуры обеспечивается при перепаде температур при нагревании оборотной воды не более 10 °С. Это требует увеличения кратности циркуляции в системе, увеличения расхода электроэнергии, но обеспечивает более стабильную и надежную работу всего оборудования, уменьшает износы оборудования, сокращает числа ремонтов и остановок. Для охлаждения оборотной воды в коксохимической промышленности используют градирни трех основных типов: башенные, вентиляторные напорные и вентиляторные вытяжные, устройство их показано на рис.2. В последние десятилетия преимущественно сооружались вытяжные градирни. Башенные градирни используются, в основном, на старых заводах.
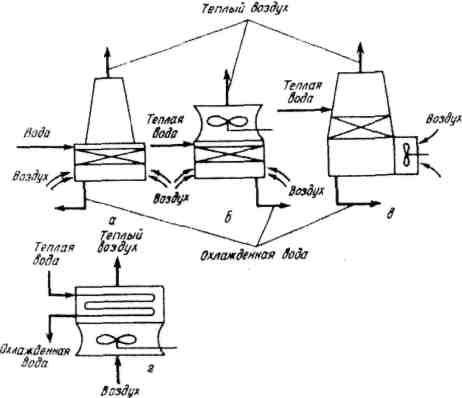
Рис. 2 – Башенные, вентиляторные напорные и вентиляторные вытяжные градирни
Наиболее распространенные вытяжные вентиляторные градирни наименее надежны в работе прежде всего из–за интенсивной коррозии лопастей вентилятора, диффузора, а также всех несущих металлических конструкций и связей верха градирен из–за сильной коррозии и эрозии под действием брызг, водяного пара и агрессивных веществ, выносимых из градирни. На этих градирнях практически ежегодно меняют лопасти вентиляторов и каждые два года – диффузоры, скорость коррозии которых (изготовлены из углеродистой стали) 0.4 – 0.5 мм/год. Серьезное значение имеет стабилизация температуры воды и охлаждение воды перед поступлением в теплообменную аппаратуру. При температуре воды выше 27°С на входе в теплообменники трудно обеспечить необходимое охлаждение газа. Поэтому оправдано оснащение коксохимических предприятий холодильными агрегатами предпочтительно абсорбционного типа (открывается возможность использования имеющихся на предприятии вторичных тепловых ресурсов) для захолаживания ограниченных объемов замкнутой в цикле воды, идущей на доохлаждение газа на основных переделах цехов обработки газа. При этом достаточно применения теплоносителей (хладоносителей) с температурой +5 °С.
Практически все отделения обработки газа работают при давлениях, незначительно превышающих атмосферное, а все решения по отделению обработки газа отвечают этому условию. При изменении давления и температуры улавливания возможны технологические решения, существенно отличающиеся от общепринятых.
Технологические решения и оптимальные условия эксплуатации отделения конденсации и машинного отделения
В отделении конденсации должно быть обеспечено охлаждение коксового газа, выделение из него смолы, конденсация водяных паров, отстой надсмольной воды от смолы, обезвоживание смолы до установленных техническими условиями норм, непрерывная подача в коксовый цех надсмольной воды требуемого напора и количества, передача смолы на склад и в нафталинопромыватели, подача избыточной надсмольной воды на переработку. В машинном отделении должен
быть обеспечен равномерный отсос коксового газа от газосборников коксовых печей и нагнетание его через аппаратуру химических цехов до потребителей газа или повысительной станции. Таким образом, названные отделения оказывают решающее влияние на функционирование практически всех цехов коксохимического производства.
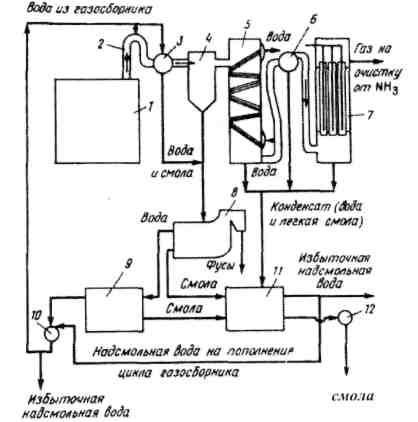
Рис. 3 – Технологическая схема отделения конденсации
1 – коксовые печи; 2 – стояк с клапанной коробкой; 3 – газосборник; 4 – сепаратор; 5 – холодильник; 6 – нагнетатель; 7 – электрофильтр; 8,9,11 – отстойники; 10,12 – насосы
Применение аппаратов воздушного охлаждения газа (АВОГ), понижающих температуру газа примерно до 65 – 67°С, несмотря на необходимость расходования электроэнергии на привод вентиляторов, позволяет более чем в три раза уменьшить потребление оборотной воды на стадии первичного охлаждения газа. Охлаждение газа до конечных температур, заданных технологическим регламентом и Правилами технической эксплуатации коксохимических предприятий, после воздушных холодильников может быть осуществлено либо в трубчатых холодильниках, либо в скрубберах Вентури. Серьезным преимуществом аппаратов с горизонтальными трубками является возможность дополнительного захолаживания газа с помощью холодильной машины за счет разрыва потока охлаждающих сред.
Серьезной проблемой становится поддержание в чистоте теплообменников для охлаждения, циркулирующей в цикле воды, так как использование скрубберов Вентуре предполагает замыкание охлаждающей воды в цикл и охлаждение ее через стенку в аппаратах той или иной конструкции оборотной водой. При эксплуатации первичных холодильников [3] их необходимо систематически пропаривать для очистки поверхности трубок от смолы и кристаллов нафталина. Чтобы исключить выбросы загрязненного пара, его выпускают обычно в коллектор газопровода перед холодильниками. Возможна промывка поверхностей теплообмена маслами или горячей смолой. Традиционная система охлаждения газа в трубчатых холодильниках оборотной водой связана с достаточно строгими требованиями к ее качеству. Вода должна обладать временной жесткостью не более 3 мг-экв/дм3 и иметь содержание взвешенных веществ не более 30 мг/дм3.
Узел разделения воды, смолы и фусов
Узел разделения воды, смолы и фусов оказывается одним из наиболее ответственных в отделении обработки коксового газа. Полнота отделения фусов определяет качество получаемой смолы, качество пека, получаемого из этой смолы, а также и качество электродов, анодных и электродных масс, изготовляемых на базе пекового кокса и каменноугольного пека. Одновременно увеличение количества фусов приводит к увеличению стабильности водосмоляных эмульсий и
увеличению остаточного количества солей в смоле. Это последнее обстоятельство увеличивает интенсивность коррозии оборудования и ухудшает качество продуктов переработки смолы. На рис.4 схематически показано взаимовлияние различных факторов на разделение воды, смолы и фусов и на процессы, протекающие в различных отделениях коксохимического производства.
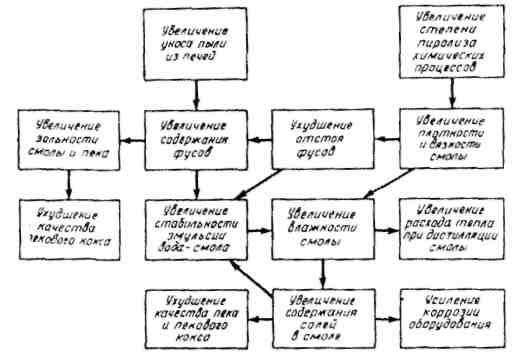
Рис. 4 – Факторы, влияющие на разделение воды
Одной из главных задач этого отделения является полное и равномерное отсасывание коксового газа от печей путем поддержания заданного разрежения перед первичными газовыми холодильниками. Это постоянство поддерживается автоматически обычно с помощью струйных регуляторов, передающих управляющий импульс либо на задвижку на байпасе нагнетателя (при электрическом приводе), либо (при паровом приводе) на вентиль подачи пара в паровую турбину.
При налаженной системе регулирования колебания давления в газовом тракте не превышают 0.1 - 0.2 кПа, что достаточно для всего газового тракта, кроме узла газосборника. Точность регулирования давления в последнем должна быть не менее 10-20 Па. Поэтому на отводном от коксовых печей газопроводе непосредственно за газосборником устанавливают самостоятельный дроссельный клапан, соединенный с самостоятельным регулятором.
Для повышения или, точнее, для обеспечения надежности работы нагнетателей необходимо:
1. Иметь постоянно готовый к запуску резервный нагнетатель, как и резервные роторы для нагнетателей, должным образом законсервированные.
2. Постоянно работающую систему смазки подшипников, сопряженную систему охлаждения циркулирующего масла.
3. Систематически контролируемую систему стока конденсата из нагнетателей и прилегающих к ним участков газопро-водов.
4. Иметь сигнальные устройства, предупреждающие об аварийном прекращении подачи масла на охлаждение подшипников, о превышении допустимой температуры подшипников.
В случае использования парового привода обязательно применяются автоматы, ограничивающие превышение предельного числа оборотов вала. Для очистки газа от смоляного тумана можно применять электрофильтры, обеспечивающие при температуре газа 20 - 30°С остаточное содержание смолы 0.05 г/Нм3. Обычно применяют электрофильтры с трубчатыми осадительными электродами при линейной скорости газа в электрофильтре около 1.8 м/с при напряжении тока 50 - 80 кВ. Проходные изоляторы могут покрываться налетом влаги, конденсирующейся из газа, что может вызвать утечку газа. Поэтому клапанные коробки электрофильтров обогревают паром так, чтобы температура в них была по меньшей мере на 10 °С выше, чем в аппарате. Желательно, чтобы клапанные коробки, особенно на нагнетании, обязательно были заполнены коксовым газом.
4. Структура машинного зала
Машинный зал цеха улавливания химических продуктов коксования предназначен: – для непрерывного отсоса коксового газа газодувными машинами из газосборников коксовых печей [4] и его транспортировки под давлением под давлением через аппараты очистки газа и улавливания химических продуктов коксования, с последующей подачей очищенного коксового газа на обогрев коксовых печей, на ТЭЦ для выработки пара, электроэнергии и технологические нужды химических цехов и на гараж размораживания УПЦ. Оборудование машинного зала должно обеспечивать его работу по первой категории надежности – исключение даже краткосрочной остановки процесса отсоса и транспортировки газа, что связано с недопустимостью: – сбора неочищенного коксового газа в атмосферу; – потери давления в газовом тракте завода и химических аппаратах; – транспортировки котлов ТЭЦ[5] и прекращением генерации электроэнергии.
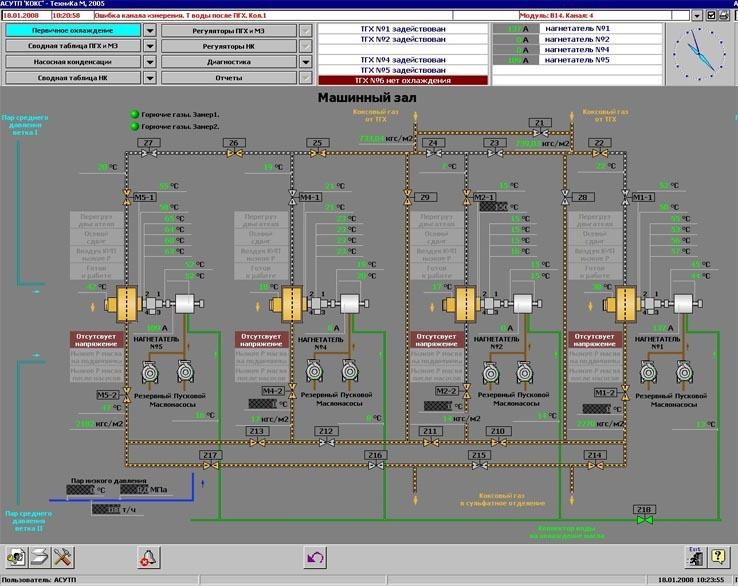
Рис. 5 – Cтруктура работы оборудования машинного зала следующая
В связи с тем, что структура работы оборудования машинного зала следующая:
– в работе одна, или несколько одновременно работающих газодувных машин;( при этом непрерывная продолжительность работы газодувной машины – не более 5000 ч)
– одна газодувная машина в резерве;
– одна газодувная машина в ремонте ( или в резерве после ремонта).
В машинном зале на ЯКХЗ
установлено 5 газодувных машин, из них 3 газодувные машины с электроприводом и 2 газодувные машины с приводом от паровой турбины.
При работе завода в составе 4–Х коксовых батарей [6] (№№ 1, 4, 5, 6) одновременно в работе находилось две газодувные машины. При этом, первая категория надежности выдерживалась условно, из–за практически полного физического износа турбоприводов на газодувках №2 и №3. Программой технического перевооружения предусматривались полная замена этих газодувок или, как минимум, их переоборудование на электропривод.
При работе завода в составе двух коксовых батарей (№ 1, № 5) машинный зал будет работать по схеме:
– одна газодувная машина в работе;
– одна газодувная машина в резерве;
– одна газодувная машина в ремонте, что может быть обеспечено тремя газодувными машинами с электроприводами.
Нормальный срок эксплуатации газодувных машин отечественного производства составляет 20 лет, импортного производства – 15 лет ( по данным Классификатора основных средств коксохимических предприятий
, УХИН, 2010г.), фактический срок службы газодувных машин составляет более 50 лет.
В настоящее время, газодувные машины №№ 2,3 выведены из эксплуатации из–за физического износа и отсутствия запасных частей к турбинам.
5. Экономические аспекты работы машинного зала
При работе КБ №1 и КБ №5, на минимальных периодах коксования, будет производиться до 38 тыс.м3/ч коксового газа. Для перекачки данного объема коксового газа достаточно одной газодувной машины из имеющихся в наличии машин с электрическим приводом мощностью от 1100 кВт до 1250 кВт.
Расход электроэнергии при работе газодувной машины близок к максимальным значениям мощности электродвигателя и, в интервале от минимального до максимального объема перекачиваемого газа, практически не изменяется:
- производительность газодувной машины - величина постоянная и зависит отее конструктива. Удержание заданных параметров разряжения коксового газа перед газодувной машиной осуществляется струйным регулятором путем байпасирования коксового газа с нагнетания на всас, т.е. чем меньше выработка газа, тем выше степень байпасирования.
В 2016г. У ПАО Донецккокс
была приобретена б/у газодувная машина ( 1977г. Выпуска) типа 750-23-8 с электродвигателем мощностью 630 кВт и номинальной производительностью по газу до 45 тыс. м3/ч. По цене 1500 тыс.грн. с НДС ( или в рублях – 3000 тыс.руб. по курсу 2,0 руб./грн.)
(Примечание: стоимость новой газодувной машины данного типа у производителя Дальневосточный Завод Энергетического Машиностроения
(г.Хабаровск) составляет 510 158 евро без НДС).
При снижении потребления электроэнергии газодувной машины с 1000 до 630 кВт/ч ежемесячная экономия электрической энергии (стоимость 1 кВт*ч = 3,6 руб) составит 266 тыс.кВт*ч на сумму 957 600 руб.
Характеристика газодувной машины типа 750–23–8 [7] с электродвигателем мощностью 630 кВт
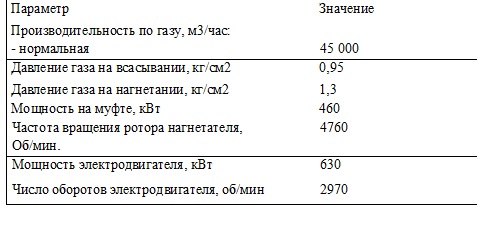
6.Эффективность работы
Таким образом, экономическая эффективность сохраняется при работе завода в составе как двух, так и трех коксовых батарей. Теоретически, работа в паре большой и малой газодувной машин способна обеспечить транспортировку до 95 тыс.м3/ч коксового газа, что соответствует объему коксового газа при работе 4-х коксовых батарей ( КБ №5, КБ №1, КБ №4, КБ №6).
При работе 3-х коксовых батарей (КБ №5, КБ №1, КБ №4) на полной загрузке, объем коксового газа увеличится до 57-62 тыс.м3/ч ( в зависимости от программы производства различных видов коксовой продукции). Данный объем коксового газа, с учетом регулировки разряжения по батареям и байпасирования должен перекачиваться двумя газовыми машинами: одной из имеющихся газодувных машин с помощью электродвигателя 1 100-1250 кВт и приобретаемой машиной с электродвигателем 630 кВт.
С вводом в эксплуатацию малой газодувной машины в маш.зале будет четыре газодувки с электроприводом, что соответствует первой категории надежности:
1 или 2 машины в работе – 1 в резерве – 1 в ремонте
Этим достигается возможность своевременного проведения капитальных ремонтов с обеспечением стабильной работы машинного зала.
Остаток финансирования на 23.08.2017г. 7 493,8 тыс.руб.
Снижение затрат на потребление электроэнергии 957,6 тыс.руб./мес.
Срок окупаемости проекта 7,8 мес.
Срок ввода в эксплуатацию 1 марта 2018г.
Выводы
Таким образом можно сделать вывод, что анализ машинного зала и некоторые технологические расчеты позволили выявить ряд существенных недостатков и обосновать направления дальнейших исследований и разработок. Известная конструкция установки получения имеет низкую эффективность. Повышение эффективности работы машинного зала достигнуто изменением нагнетателей на газодувные машины. На данный момент магистерская работа находится в стадии написания. Окончательное завершение: июль 2019 года. Полный текст работы и материалы по теме могут быть получены у автора или его руководителя после указанной даты.
Список источников
- Постійний технологічний регламент № 8: виробництво сірчаної кислоти контактним методом за схемою ДК – ДА введено в дію директором Макіївського Державного хімічного заводу № 8 – 1997. – 62 с.
- Инструкция по эксплуатации пылеулавливающей установки беспылевой выдачи кокса батареи № 1 коксового цеха ОАО «ЯКХЗ»-2007. – 49
Основные правила техники безопасности при прохождении производственной практики
/Методические указания кафедры МАХП, ДонНТУ- ПАО
Ясиновский коксохимический завод
: Главная страница.- [Электронный ресурс] Украина. Донецк.-2013. - Гомельский А.З. Аппаратчики коксохимеческих производств. 2 издание. Харьков-Москва.Металлургиздат, 1953. 384 с
- Дмитриев М.М., Абуховский Е.М. Краткий справочник коксохимика. Москва: Металлургиздат, 1960, 253с.
- Лейбович Р.Е., Яковлева Е.И., Филатов А.Б. Технология коксохимеческого производства. 3 издание, Перераб. и доп.-М.:Металлургия, 1982- 360с.