Зміст
- Вступ
- 1. Актуальність теми
- 2. Ціль і завдання дослідження
- 3. Машинний зал – складова цеху уловлювання
- 4. Структура машинного залу
- 5. Економічні аспекти роботи машинного залу
- 6.Ефективність роботи
- Висновки
- Перелік посилань
Вступ
Велику роль в цеху грає машинно-конденсаційне відділення. У машинному залі встановлюється декілька газових нагрівачів. Їх ще називають газодувками. Вони призначені для того, щоб витягувати газ з коксових печей і пропускати його через спеціальне обладнання цеху уловлювання та цеху сіркоочистки, а потім очищений газ повертати назад в коксовий цех як паливо. Якщо машинне відділення зупиниться, тобто не стануть функціонувати газодувки, то не стануть працювати коксові печі та припиниться процес коксування. Машинно-конденсаційне відділення вважається одним з найважчих і відповідальних місць на виробничому підприємстві.
1. Актуальність теми
Стабільне функціонування коксохімічного підприємства в цілому багато в чому визначається надійною і оптимальної роботою машинного залу цеху уловлювання хімічних продуктів коксування, зокрема обладнання машинно – конденсаційного відділення. У машинному залі встановлюється декілька газових нагнітачів (газодувок). Вони призначені для відсмоктування газ з коксових печей і створення тиску для його подачі через спеціальне обладнання цеху уловлювання та цеху сіркоочистки аж до повернення очищеного газу в коксовий цех для обігріву печей. При аварійній зупинці газодувок машинного відділення порушується гідравлічний режим коксування і нетривала робота коксових печей можлива лише при відкритих стояках з викидами всього газу в атмосферу, де він відразу ж запалюється. Тому оптимізація роботи машинно – конденсаційного відділення є однією з найвідповідальніших завдань. Це особливо актуально в зв'язку зі зростанням вимог екологічних служб.
2. Мета і завдання дослідження, плановані результати
Метою роботи була розробка наукових принципів вдосконалення (модернізації) існуючих технологій та спеціалізованого обладнання, підвищення якості продукції, що випускається, створення технологій для виробництва нових видів готової продукції. Для отримання результату здійснювалося:
• дослідження складу і фізико – хімічних властивостей вихідної сировини як одного з найважливіших чинників, що впливають на технологічний процес і на якість одержуваного результату;
• математичне моделювання проведених процесів поділу газу в промислових установках, розробка технічних рішень щодо підвищення ефективності роботи;
• вдосконалення технологічних процесів і апаратурного оформлення, розробка рекомендацій по оптимізації параметрів процесів і на цій основі поліпшення якості товарних продуктів.
3. Машинний зал – складова цеху уловлювання
Комплекс цехів уловлювання коксохімічного заводу, який правильніше було б назвати Відділення обробки коксового газу
, призначений для відводу коксового газу від печей, охолодження його з виділенням конденсуються смоли,
води, вилучення з газу аміаку, піридинових підстав, бензольних вуглеводнів, очищення газу від нафталіну, сірководню і ціаністого водню і передачі газу до споживачів або станції підвищення тиску.
Відділення обробки коксового газу є одним з найважливіших технологічних вузлів коксохімічного підприємства, без нормальної роботи якого функціонування коксового цеху і всього виробництва в цілому неможливо.
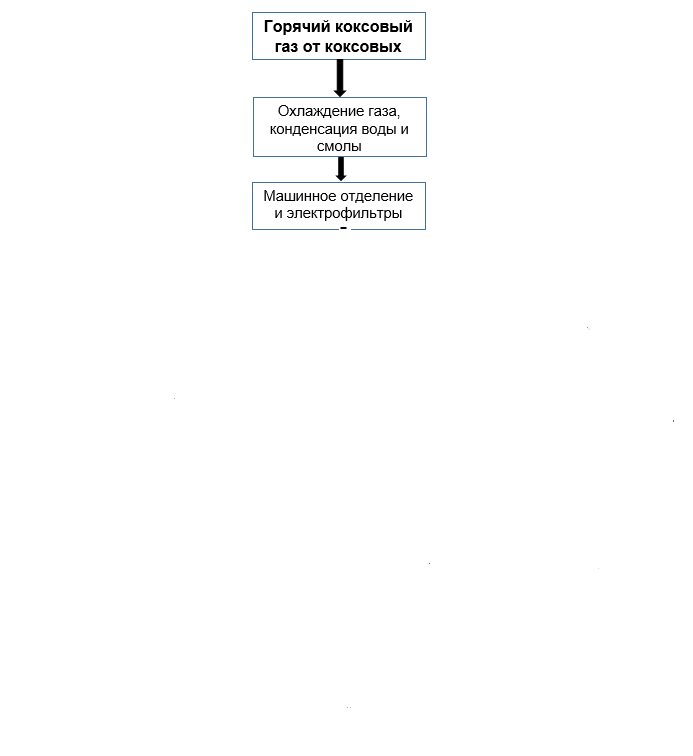
Мал. 1 – Варіанти схем (А, Б, В) обробки коксового газу
(анімація: 5 кадрів, 5 циклів повторення, 65.3 кілобайт)
Послідовність обробки коксового газу на різних підприємствах може відрізнятися. На рис.1 показані різні варіанти схем обробки коксового газу. Варіант В має такі переваги:
– аміачна сероціаноочістка, що включає вузол очищення від нафталіну, дозволяє використовувати власний поглинає агент і вести подальшу обробку газу, вільного від агресивних і ускладнюють роботу агентів;
– уловлювання аміаку в круговому амонійно – фосфатном процесі дозволяє за простою технологією отримувати безводний аміак, що не витрачаючи сторонні реагенти і передбачати повне знищення аміаку;
– виключається складний вузол кінцевого охолодження газу, значно скорочуються витрати тепла і води.
Можливе часткове використання рішень варіанту В, наприклад, заміна в варіанті А виробництва сульфату амонію на приготування безводного аміаку. Нафталіноочістка може бути передбачена також або при первинному, або при остаточному охолодженні. Для всіх варіантів характерним є пробработка великого обсягу отруйного і вибухонебезпечного газу, насиченого парами води, при тисках, незначно відрізняються від атмосферного (розрідження перед нагнітачем 4 – 5 кПа, а надлишковий тиск на стороні нагнітання 20 – 30 кПа). Суміші коксового газу з повітрям вибухонебезпечні при утриманні в них коксового газу від 6 до 30% об. Тому вся працює газова апаратура повинна бути герметичною, всі газопроводи, як і всі апарати, повинні бути забезпечені надійно працюють гідрозатворами і конденсато – відвідників; велика частина апаратури і газопроводів розміщується поза приміщенням. З огляду на значні перепади температур протягом року, необхідно оснащення трубопроводів системою термокомпенсации, оснащення всіх гідрозатворів і конденсатовідвідників системою обігріву. Експлуатація газового господарства відділення обробки газу [1] ускладнюється – за присутності в газі парів нафталіну, аерозолів нафталіну і смоли. Висока летючість нафталіну і здатність його до утворення аерозолів, так само як і висока температура його кристалізації (80 ° С), сприяють його переміщенню практично по всьому газовому тракту і створюють небезпеку утворення нафталінових пробок в газопроводах та інших комунікаціях. Необхідно контролювати опір апаратів і ділянок газопроводів, рівень рідини в апаратах. Контроль опору і відключення апарату, групи апаратів, ділянки газопроводу на ревізію, очищення, пропарювання або промивання в разі перевищення гранично допустимого опору – важлива умова нормальної експлуатації відділення обробки газу.
Токсичність і вибухонебезпечність коксового газу робить особливо відповідальною організацію робіт при пуску і зупинці апаратури, при відключенні апаратів або ділянок газопроводу на ремонт. Будь-які непрацюючі апарати або ділянки газопроводів повинні бути відключені заглушками за всіма без винятку комунікацій – по газу, пару, маслу, воді, конденсату, імпульсним лініях КВП і т.п., незалежно від наявності запірної арматури. Апарати повинні бути з'єднані з атмосферою, стан середовища в них повинно контролюватися. Існують деякі загальні правила проектування і експлуатації систем газового і водного господарства відділення обробки газу.
Розташування установок відділення обробки газу повинно передбачати високий коефіцієнт забудови. Це важливо не тільки для кращого використання землі, але особливо для скорочення довжини комунікацій. Використання коротких комунікацій зменшує капітальні та експлуатаційні витрати, теплові втрати і енергетичні витрати на транспортування газів і рідин, підвищує надійність і зменшує інерційність регулюючих пристроїв. Скорочення протяжності комунікацій особливо важливо при транспортуванні кристалізуються або виділяють відкладення середовищ. Це відноситься, наприклад, до газопроводів коксового газу, насиченого нафталіном. У той же час повинна бути передбачена можливість доступу до основного обладнання, можливість ремонту та монтажу – демонтажу зовнішнього обладнання автокранами або автомашинами з монтажною вишкою.
Для скорочення енерговитрат і підвищення надійності роботи коксового блоку і відділення обробки газу, слід дотримуватись таких умов: найменша довжина газопроводів; скорочення місцевих опорів за рахунок правильного вибору конфігурації і розташування колін, трійників і т.п .; мінімальна кількість регулюючих пристроїв (діафрагми, дроселі тощо).
Остання умова визначає тенденцію використовувати для кожного нагнітача свій самостійний газовий потік: від коксової батареї до виходу газу з системи його обробки. Це спрощує і зменшує кількість регулюючих (розподіляють) пристроїв. Там, де газовий потік розподіляється по паралельно працюючим апаратам (особливо це відноситься до газових холодильників)
доводиться приймати спеціальні заходи для підтримки однакового опору апаратів [2]: безперервна промивка міжтрубному простору первинних газових холодильників, щоб запобігти відкладення нафталіну, промивка сатураторів і т.п.
Відділення обробки коксового газу – найбільший споживач охолоджуючої води, що витрачається на охолодження газу в первинних холодильниках, на кінцеве охолодження газу, на охолодження потоків циркулюючих розчинів і конденсацію парів в цехах уловлювання аміаку, сероціаноочісткі, уловлювання бензольних вуглеводнів.
Подання про кількість відведеного тепла дає кількість води, що втрачається на випаровування в градирнях, що становить влітку 0.42 – 0.55 Нм 3 / т коксу, а взимку, що зменшується до 0.30 – 0.39 Нм 3 / т коксу, що становить до 1.5% об. від кількості води, що циркулює в циклі оборотного водопостачання відділення обробки газу. Крім того, 0.10 – 0.13 Нм 3 води на 1 т коксу виноситься у вигляді бризок і ще 0.05 Нм 3 / т
виводиться з циклу оборотного водопостачання (такзвані родувочние води
), щоб запобігти накопиченню в останньому солей.
В результаті система оборотного водопостачання і градирні виявляються важливим елементом цеху уловлювання, а від правильного вибору конструктивних рішень залежить якість роботи основного устаткування, істотно залежить від температури газу і. абсорбентів, надійність роботи обладнання і, зокрема, його корозія. Справа в тому, що на території коксохімічного заводу велике число зволожуючих атмосферу об'єктів: градирні,
вежі мокрого гасіння з шламовими відстійниками, АЕРОТЕХНІКА біохімічних установок, "воздушки", що викидають водяна пара і пари агресивних речовин. Зволоження повітря серйозно збільшує небезпеку корозії обладнання, що посилюється ще і значною запиленістю повітря.
Розташування градирень поблизу зволожуючих повітря апаратів погіршує їх роботу: вологе повітря погіршує роботу градирень, на кілька градусів підвищуючи температуру мокрого термометра
і, відповідно, збільшуючи температуру охолодженої оборотної води. Серйозну небезпеку становить і пил, що знаходиться в атмосфері промислових підприємств. Великі кількості повітря, що проходять через градирню, звільняються в ній від пилу,
кількість якої виявляється значно більше, ніж кількість солей і мулу, що вносяться зі свіжою водою.
Робота системи оборотного водопостачання в дуже великій мірі залежить від взаємного розташування градирень, основних установок цеху уловлювання та джерел пилоутворення. Їх розміщення повинно здійснюватися з урахуванням "троянди вітрів" та вільного припливу свіжого повітря.
На роботу градирень впливає величина перегріву оборотної води в теплообмінних апаратурі вище 42 – 45 ° С, при цьому починається розкладання бікарбонату кальцію:
Са (НС03) 2 = СаСОз + Н20 + С02.
В результаті збільшується агресивність парів води і одночасно починається відкладення дрібнодисперсного, погано розчинної карбонату кальцію на металевих конструкціях і насадки градирень. На деяких заводах відзначалися випадки обвалення насадки з – за збільшення її маси під дією відкладень. Досвід ряду галузей показує, що стабільний безнакіпний режим роботи градирень і теплообмінної апаратури забезпечується при перепаді температур при нагріванні оборотної води не більше 10 ° С. Це вимагає збільшення кратності циркуляції в системі, збільшення витрати електроенергії, але забезпечує більш стабільну і надійну роботу всього обладнання, зменшує знос устаткування, скорочує числа ремонтів і зупинок. Для охолодження оборотної води в коксохімічній промисловості використовують градирні трьох основних типів: баштові, вентиляторні напірні і вентиляторні витяжні, влаштування їх показано на рис.2. В останні десятиліття переважно споруджувалися витяжні градирні. Баштові градирні використовуються, в основному, на старих заводах.
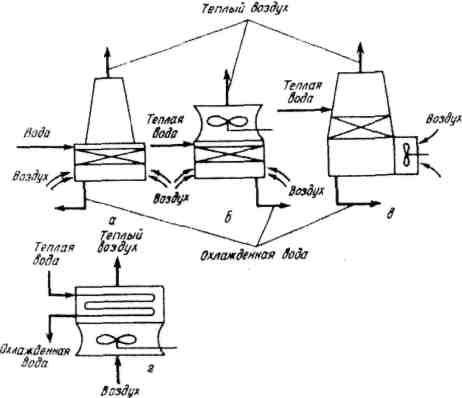
Рис. 2 – Баштові, вентиляторні напірні і вентиляторні витяжні градирні
Найбільш поширені витяжні вентиляторні градирні найменш надійні в роботі перш за все з – за інтенсивної корозії лопатей вентилятора, дифузора, а також всіх несучих металевих конструкцій і зв'язків верху градирень з – за сильної корозії і ерозії під дією бризок, водяної пари і агресивних речовин , що виносяться з градирні. На цих градирнях практично щорічно змінюють лопаті вентиляторів і кожні два роки – дифузори, швидкість корозії яких (виготовлені з вуглецевої сталі) 0.4 – 0.5 мм/рік. Серйозне значення має стабілізація температури води і охолодження води перед надходженням в теплообмінну апаратуру. При температурі води вище 27 ° С на вході в теплообмінники важко забезпечити необхідне охолодження газу. Тому виправдано оснащення коксохімічних підприємств холодильними агрегатами переважно абсорбційного типу (відкривається можливість використання наявних на підприємстві вторинних теплових ресурсів) для захолажіванія обмежених обсягів замкнутої в циклі води, що йде на доохолодження газу на основних переділах цехів обробки газу. При цьому досить застосування теплоносіїв (холодоносіїв) з ??температурою +5 ° С.
Практично всі відділення обробки газу працюють при тисках, незначно перевищують атмосферний, а всі рішення щодо відділення обробки газу відповідають цій умові. При зміні тиску і температури уловлювання можливі технологічні рішення, що істотно відрізняються від загальноприйнятих.
Технологічні рішення і оптимальні умови експлуатації відділення конденсації і машинного відділення
У відділенні конденсації має бути забезпечено охолодження коксового газу, виділення з нього смоли, конденсація водяної пари, відстій надсмольної води від смоли, зневоднення смоли до відповідати вимогам ДСТУ норм, безперервна подача в коксовий цех надсмольної води необхідного напору і кількості, передача смоли на склад і в нафталінопромивателі, подача надлишкової надсмольної води на переробку. У машинному відділенні повинен
бути забезпечений рівномірний відсмоктування коксового газу від газосборніков коксових печей і нагнітання його через апаратуру хімічних цехів до споживачів газу або підвищувальні станції. Таким чином, названі відділення мають вирішальний вплив на функціонування практично всіх цехів коксохімічного виробництва.
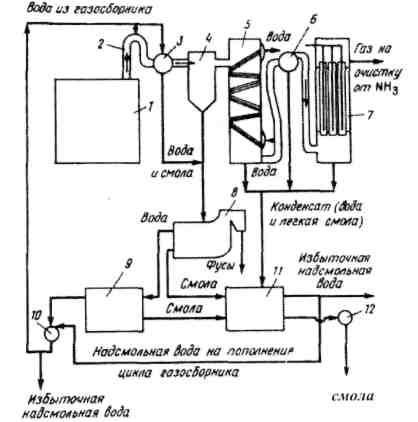
Рис. 3 – Технологічна схема відділення конденсації
1 – коксові печі; 2 – стояк з клапанною коробкою; 3 – газосборнік; 4 – сепаратор; 5 – холодильник; 6 – нагнітач; 7 – електрофільтр; 8,9,11 – відстійники; 10,12 – насоси
Застосування апаратів повітряного охолодження газу (АВОГ), що знижують температуру газу приблизно до 65 – 67 ° С, незважаючи на необхідність витрачання електроенергії на привід вентиляторів, дозволяє більш ніж в три рази зменшити споживання оборотної води на стадії первинного охолодження газу. Охолодження газу до кінцевих температур, заданих технологічним регламентом і Правилами технічної експлуатації коксохімічних підприємств, після повітряних холодильників може бути здійснено або в трубчастих холодильниках, або в скрубберах Вентурі. Серйозною перевагою апаратів з горизонтальними трубками є можливість додаткового захолажіванія газу за допомогою холодильної машини за рахунок розриву потоку охолоджуючих середовищ.
Серйозною проблемою стає підтримка в чистоті теплообмінників для охолодження, що циркулює в циклі води, так як використання скруберів Вентурі передбачає замикання охолоджуючої води в цикл і охолодження її через стінку в апаратах тієї чи іншої конструкції зворотному водою. При експлуатації первинних холодильників[3] їх необхідно систематично пропарювати для очищення поверхні трубок від смоли і кристалів нафталіну. Щоб виключити викиди забрудненого пара, його випускають зазвичай в колектор газопроводу перед холодильниками. Можлива промивка поверхонь теплообміну маслами або гарячою смолою. Традиційна система охолодження газу в трубчастих холодильниках оборотною водою пов'язана з досить суворими вимогами до її якості. Вода повинна володіти тимчасовою жорсткістю не більше 3 мг-екв / дм 3 і мати вміст завислих речовин не більше 30 мг / дм 3 .
Вузол поділу води, смоли і фусов
Вузол поділу води, смоли і фусов виявляється одним з найбільш відповідальних у відділенні обробки коксового газу. Повнота відділення фусов визначає якість одержуваної смоли, якість пеку, одержуваного з цієї смоли, а також і якість електродів, анодних і електродних мас, виготовлених на базі пекового коксу і кам'яновугільного пеку. Одночасно збільшення кількості фусов призводить до збільшення стабільності водосмоляних емульсій і
збільшення залишкової кількості солей в смолі. Ця остання обставина збільшує інтенсивність корозії устаткування і погіршує якість продуктів переробки смоли. На рис.4 схематично показано взаємовплив різних факторів на поділ води, смоли і фусов і на процеси, що протікають в різних відділеннях коксохімічного виробництва.
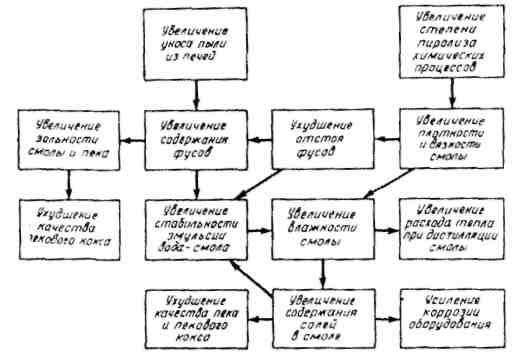
Рис. 4 – Фактори, що впливають на розподіл води
Однією з головних завдань цього відділення є повне і рівномірне відсмоктування коксового газу від печей шляхом підтримки заданого розрідження перед первинними газовими холодильниками. Це сталість підтримується автоматично зазвичай за допомогою струменевих регуляторів, що передають керуючий імпульс або на засувку на байпасе нагнітача (при електричному приводі), або (при паровому приводі) на вентиль подачі пари в парову турбіну.
При налагодженій системі регулювання коливання тиску в газовому тракті не перевищують 0,1-0,2 кПа, що досить для всього газового тракту, окрім вузла газосборника. Точність регулювання тиску в останньому повинна бути не менше 10-20 Па. Тому на відвідної від коксових печей газопроводі безпосередньо за газосборником встановлюють самостійний дросельний клапан, поєднаний з самостійним регулятором.
Для підвищення або, точніше, для забезпечення надійності роботи нагнітачів необхідно:
1. Мати постійно готовий до запуску резервного нагнітач, як і резервні ротори для нагнітачів, належним чином законсервовані.
2. Постійно працюючу систему змащення підшипників, пов'язану систему охолодження циркулюючого масла.
3. Систематично контрольовану систему стоку конденсату з нагнітачів і прилеглих до них ділянок газопром-водів.
4. Мати сигнальні пристрої, що попереджають про аварійний припинення подачі масла на охолодження підшипників, про перевищення допустимої температури підшипників.
В разі використання парового приводу обов'язково застосовуються автомати, що обмежують перевищення граничного числа обертів вала. Для очищення газу від смоляного туману можна застосовувати електрофільтри, що забезпечують при температурі газу 20 - 30 ° С залишковий вміст смоли 0.05 г / Нм 3 . Зазвичай застосовують електрофільтри з трубчастими осадітельного електродами при лінійної швидкості газу в електрофільтрі близько 1.8 м / с при напрузі струму 50 - 80 кВ. Прохідні ізолятори можуть покриватися нальотом вологи, що конденсується з газу, що може викликати витік газу. Тому клапанні коробки електрофільтрів обігрівають парою так, щоб температура в них була щонайменше на 10 ° С вище, ніж в апараті. Бажано, щоб клапанні коробки, особливо на нагнітанні, обов'язково були заповнені коксівним газом.
4. Структура машинного залу
Машинний зал цеху уловлювання хімічних продуктів коксування призначений: – для безперервного відсмоктування коксового газу газодувних машинами з газосборніков коксових печей і його транспортування під тиском під тиском через апарати очищення газу і уловлювання хімічних продуктів коксування, з подальшою подачею очищеного коксового газу на обігрів коксових печей, на ТЕЦ для вироблення пари, електроенергії та технологічні потреби хімічних цехів і на гараж розморожування УПЦ. Устаткування машинного залу повинно забезпечувати його роботу за першою категорією надійності – виняток навіть короткострокової зупинки процесу відсмоктування і транспортування газу, що пов'язано з неприпустимістю: – збору неочищеного коксового газу в атмосферу; – втрати тиску в газовому тракті заводу і хімічних апаратах; – транспортування котлів ТЕЦ [5] і припиненням генерації електроенергії.
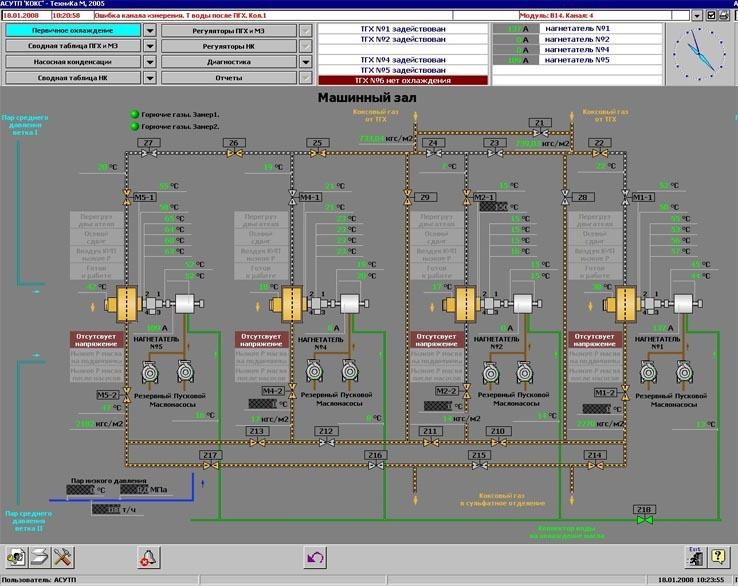
Рис. 5 – Cтруктура роботи обладнання машинного залу наступна
У зв'язку з тим, що структура роботи обладнання машинного залу наступна:
– в роботі одна, або кілька одночасно працюючих газодувних машин; (при цьому безперервна тривалість роботи газодувних машини – не більше 5000 год)
– одна газодувних машина в резерві;
– одна газодувних машина в ремонті (або в резерві після ремонту).
В машинному залі на ЯКХЗ
встановлено 5 газодувних машин, з них 3 газодувние машини з електроприводом і 2 газодувние машини з приводом від парової турбіни.
При роботі заводу в складі 4 – Х коксових батарей [6](№№ 1, 4, 5, 6) одночасно в роботі було задіяно дві газодувние машини. При цьому, перша категорія надійності дотримувалися умовно, з – за практично повного фізичного зносу турбопріводов на газодувками №2 і №3. Програмою технічного переозброєння передбачалися повна заміна цих газодувок або, як мінімум, їх переобладнання на електропривод.
При роботі заводу в складі двох коксових батарей (№ 1, № 5) машинний зал буде працювати за схемою:
– одна газодувних машина в роботі;
– одна газодувних машина в резерві;
– одна газодувних машина в ремонті, що може бути забезпечено трьома газодувних машинами з електроприводами.
Нормальний термін експлуатації газодувних машин вітчизняного виробництва становить 20 років, імпортного виробництва – 15 років (за даними Класифікатора основних засобів коксохімічних підприємств
, УХІН, 2010р.), Фактичний термін служби газодувних машин становить понад 50 років.
В даний час, газодувние машини №№ 2,3 виведені з експлуатації з – через фізичний знос і відсутність запасних частин до турбін.
5. Економічні аспекти роботи машинного залу
При роботі КБ №1 і КБ №5, на мінімальних періодах коксування, буде проводитися до 38 тис.м3 / год коксового газу. Для перекачування даного обсягу коксового газу достатньо однієї газодувних машини з наявних машин з електричним приводом потужністю від як 1100 кВт до 1250 кВт.
Витрата електроенергії при роботі газодувних машини близький до максимальних значень потужності електродвигуна і, в інтервалі від мінімального до максимального обсягу перекачується газу, практично не змінюється:
- продуктивність газодувних машини - величина постійна і залежить отеє конструктиву. Утримання заданих параметрів розрядження коксового газу перед газодувних машиною здійснюється струменевим регулятором шляхом байпасірованія коксового газу з нагнітання на всас, тобто чим менше вироблення газу, тим вище ступінь байпасірованія.
У 2016р. У ПАТ Донецьккокс
була придбана б / у газодувних машина (1977р. Випуску) типу 750-23-8 з електродвигуном потужністю 630 кВт і номінальною продуктивністю по газу до 45 тис. М3 / год. За ціною 1500 тис.грн. з ПДВ (або в рублях – 3000 тис.руб. за курсом 2,0 грн. / грн.)
(Примітка: вартість нової газодувних машини даного типу у виробника Далекосхідний Завод Енергетичного Машинобудування
(г.Хабаровск) становить 510 158 євро без ПДВ).
При зниженні споживання електроенергії газодувних машини з 1000 до 630 кВт / год щомісячна економія електричної енергії (вартість 1 кВт * год = 3,6 руб) складе 266 тис.кВт * год на суму 957 600 руб.
Характеристика газодувних машини типу 750 – 23 – 8 [7] з електродвигуном потужністю 630 кВт
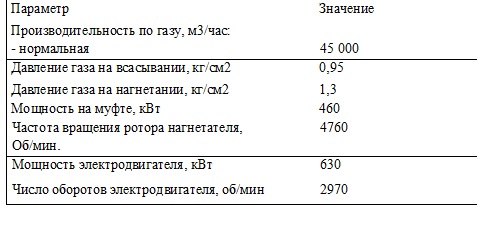
6.Еффектівность роботи
Таким чином, економічна ефективність сохраняется при роботі заводу в складі як двох, так і трьох коксових батарей. Теоретично, робота в парі великої і малої газодувних машин здатна забезпечити транспортування до 95 тис.м3 / год коксового газу, що відповідає обсягу коксового газу при роботі 4-х коксових батарей (КБ №5, КБ №1, КБ №4, КБ № 6).
При роботі 3-х коксових батарей (КБ №5, КБ №1, КБ №4) на повному завантаженні, обсяг коксового газу збільшиться до 57-62 тис.м3 / год (в залежності від програми виробництва різних видів коксової продукції ). Даний обсяг коксового газу, з урахуванням регулювання розрядки по батареях і байпасірованія повинен перекачуватися двома газовими машинами: однією з наявних газодувних машин за допомогою електродвигуна 1 100-1250 кВт і купується машиною з електродвигуном 630 кВт.
З введенням в експлуатацію малої газодувних машини в маш.зале буде чотири газодувки з електроприводом, що відповідає першій категорії надійності:
1 або 2 машини в роботі - 1 в резерві - 1 в ремонті
Цим досягається можливість своєчасного проведення капітальних ремонтів із забезпеченням стабільної роботи машинного залу.
Залишок фінансування на 23.08.2017г. 7 493,8 тис.грн.
Зниження витрат на споживання електроенергії 957,6 тис.руб. / Міс.
Термін окупності проекту 7,8 міс.
Термін введення в експлуатацію 1 березня 2018 р.
Висновки
Таким чином можна зробити висновок, що аналіз машинного залу і деякі технологічні розрахунки дозволили виявити ряд істотних недоліків і обґрунтувати напрями подальших досліджень і розробок. Відома конструкція установки отримання має низьку ефективність. Підвищення ефективності роботи машинного залу досягнуто зміною нагнітачів на газодувние машини. На даний момент магістерська робота знаходиться в стадії написання. Остаточне завершення: липень 2019 року. Повний текст роботи та матеріали по темі можуть бути отримані у автора або його керівника після зазначеної дати.
Перелік посилань
- Постійний технологічний регламент № 8: виробництво сірчаної кислоти контактним методом за схемою ДК – ДА введено в дію директором Макіївського Державного хімічного заводу № 8 – 1997. – 62 с.
- Инструкция по эксплуатации пылеулавливающей установки беспылевой выдачи кокса батареи № 1 коксового цеха ОАО «ЯКХЗ»-2007. – 49
Основные правила техники безопасности при прохождении производственной практики
/Методические указания кафедры МАХП, ДонНТУ- ПАО
Ясиновский коксохимический завод
: Главная страница.- [Электронный ресурс] Украина. Донецк.-2013. - Гомельский А.З. Аппаратчики коксохимеческих производств. 2 издание. Харьков-Москва.Металлургиздат, 1953. 384 с
- Дмитриев М.М., Абуховский Е.М. Краткий справочник коксохимика. Москва: Металлургиздат, 1960, 253с.
- Лейбович Р.Е., Яковлева Е.И., Филатов А.Б. Технология коксохимеческого производства. 3 издание, Перераб. и доп.-М.:Металлургия, 1982- 360с.