Содержание
- Введение
- 1. Актуальность темы
- 2. Описание объекта исследования
- 3. Обзор исследований и разработок
- 3.1 Обзор международных источников
- 3.2 Обзор найденных патентов
- 4. Описание разработываемого механизма
- Выводы
- Список источников
Введение
Известь – это востребованный строительный материал, который используется в различных сферах. Он является незаменимым, даже несмотря на то, что на сегодня имеются другие современные аналоги.
Основой для получения готового известняка являются обжиговые печи. Они получили широкое распространение в мире благодаря простоте конструкции и эксплуатации. В мире имеется множество различных конструкций, с различными исполнительными механизмами, которые делятся на три части – загрузочное устройство, газовые или другие горелки и выгрузочное устройство. Выгрузочное устройство отвечает за ряд некоторых функций, а именно за регулирование скорости обжигания материала в шахтной печи и непосредственную разгрузку извести.
1. Актуальность темы
Однако не все конструктивные решения данного вида устройства обеспечивают необходимые условия работы. Одними из главных недостатков являются неравномерная разгрузка и сложность реализации. Первый недостаток встречается наиболее часто, из-за чего многие системы так и остались на бумаге и не прошли в производственное использование.
Целью исследования, является сопоставление уже известных систем выгрузки известняка из шахтной печи с разработанным механизмом выгрузки. Основная задача — это сравнить системы, найти общие черты и спроектировать установку, которая будет максимально эффективна и содержать в себе минимум недостатков предыдущих.
2. Описание объекта исследования
Основным атрибутом для производства извести является печь для обжига данного материала. Для того, чтобы производить известь, в качестве горелочного материала применяется различное топливо промышленного типа: естественное, твердое, газообразное, искусственно-твердое и жидкое. Если говорить о самом топливе, то можно выделить - каменные угли, природный газ, кокс, мазут и другие виды горючего топлива подходящие для данной цели, и для данной конструкции печи.
Нагрев самого известняка в печи осуществляется в температурном диапазоне от 200 до 800 градусов по Цельсию. Нагрев доломитов осуществляется в диапазоне от 200-600 градусов по Цельсию. Это сопровождается растрескиванием материала, и увеличением их объема примерно на 3-4%, соответственно снижается и предел прочности на сжатие, процент падения составляет от 40% до 70%. Другими словами, происходит процесс термической диссоциации, впоследствии которой происходит обратимое разложение вещества. Но для завершения процесса необходимо поднять температуру как минимум до 1200 градусов.
Как известно, для чистого известняка упругость при диссоциации равна давлению в атмосфере – 101 кПа при температуре нагрева до 898 градуса. Для прочих карбонатных пород этот показатель может колебаться в весьма ощутимых пределах от 800 до 950 градусов по Цельсию. Во время самого обжига известняка в печи температура диссоциации задается в пределах от 810-850 градусов, соответственно скорость обжигания материала зависит от температуры внутри печи, и коэффициента тепловой передачи между материалами.
Процесс обжига можно описать по принципу деления шахтной печи на отдельные термальные зоны.
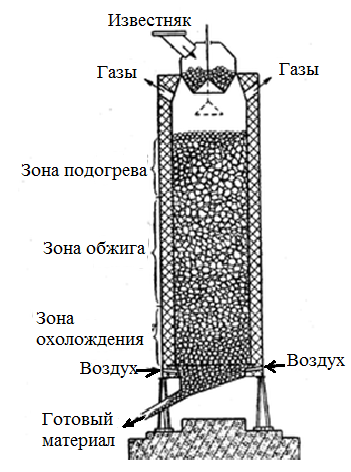
Рисунок 1 – Общий вид и участки процессов обжига известняка в обжиговой печи
3. Обзор исследований и разработок
Главной задачей являлось создать модель разработанного механизма выгрузки, после чего описать принцип его работы. За основу взят механизм выгрузки извести с гидравлическим приводом. После необходимо произвести анализ и найти схожие с устройством конструкционные решения.
3.1 Обзор международных источников
После проведенного патентного поиска были найдены для сравнения следующие иностранные патенты механизмов:
- Pat. 3027147 USA, IPC F27B1 / 21 Circular shaft kiln discharge grate /Brakel L.H.; John B. J.; «Cameron and Jones INC» (US). – № 19590811306; filed 06.05.1959; published 27.03.1962
- Pat. 3854635 USA, IPC B65G65 / 58 Sliding car arrangement for a shaft furnace / Tschinkel F.; «Maerz ofenbau» (СН). – № 19730424706; filed 14.12.1973; published 17.12.1974
- Pat. 1598451 USA, IPC C10J3 / 30 Discharge mechanism / Saathoff G. W.; «Combustion utilities Corp.» (USA)
Данные механизмы имеют гидравлические систему, они были разработаны в США. Они будут сравниваться с разработанным аналогом, который также имеет патентную основу.
3.2 Обзор найденных патентов
1. Pat. 3027147 USA, IPC F27B1 / 21 Circular shaft kiln discharge grate / Brakel L.H.; John B. J.; «Cameron and Jones INC» (US). – № 19590811306; filed 06.05.1959; published 27.03.1962.
Изобретение относится к печам непрерывного действия с гравитационным потоком, которые экономически выгодны для широкого использования при обжиге разнообразных твердых материалов в дробленном, а точнее – к выгрузочным устройствам, регулирующим поток выгружаемого сыпучего материала.
Выгрузочное устройство (рис. 4) выполнено в виде колосниковой решетки новой конструкции, взаимодействующей с выгружаемым материалом в печах круглой формы различных типоразмеров. Устройство обеспечивает равномерность распределения выгружаемого материала по периметру печи и, следовательно, его движение по сечению шахты, а также возможность регулирования скорости истечения.
Это в свою очередь позволяет равномерно по объему обрабатывать материал с условием введения различных реагентов в соответствующих местах внутри печи.
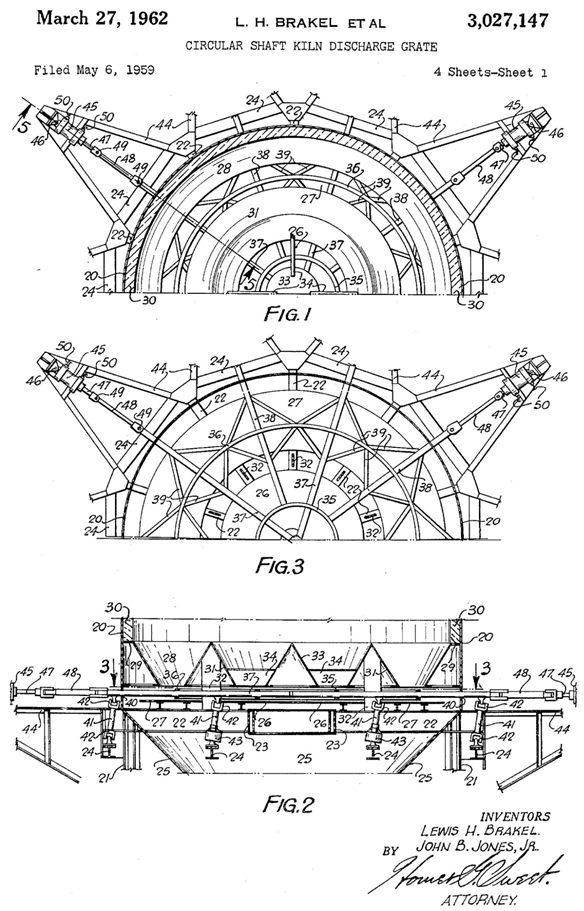
Рисунок 2 – Общий вид механизма выгрузки извести
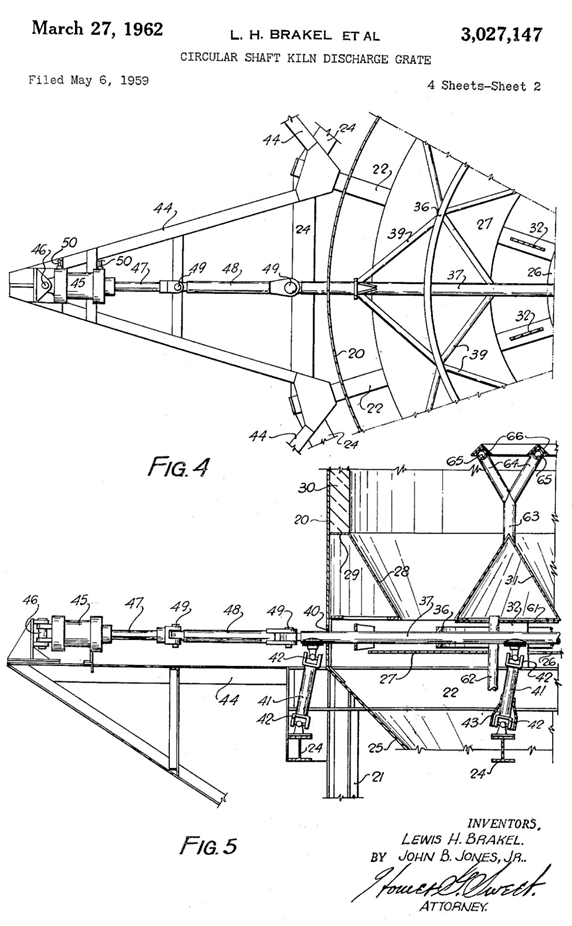
Рисунок 3 – Основные узлы механизма выгрузки
2. Pat. 3854635 USA, IPC B65G65 / 58. Sliding car arrangement for a shaft furnace / Tschinkel F.; «Maerz ofenbau» (СН). – № 19730424706; filed 14.12.1973; published 17.12.1974.
Устройство для выгрузки сыпучего материала из шахтной вертикальной печи (рис. 2) оснащено, по меньшей мере, тремя скользящими (раздвижными) секторами, расположенными ниже выпускного отверстия шахты. Каждый сектор может независимо от остальных перемещаться вовнутрь и обратно относительно центра шахты. Кроме того, противоположные секторы могут располагаться с возможностью их приведения в движение общим приводом.
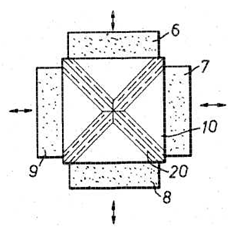
Рисунок 4 – Ориентация секторов устройства для выгрузки сыпучего материала из обжиговой печи: 6, 7, 8, 9 – подвижные секторы; 10 – шахта печи; 20 – свод над границей соседних секторов
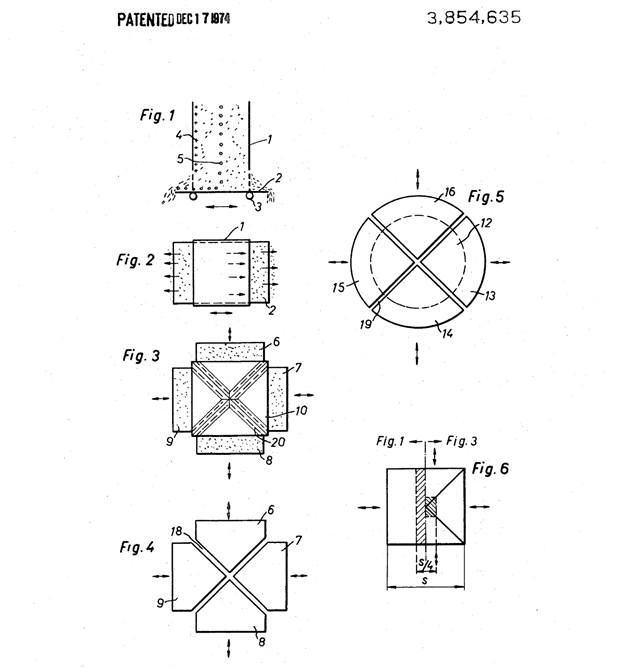
Рисунок 5 – Ориентация секторов устройства для выгрузки и схемы движения
В известном варианте шахтной печи, чья шахта имеет прямоугольную сечение, так называемый подвижный стол используется в качестве разгрузочного устройства. На некотором расстоянии от нижнего конца шахты, расположена пластина, установленная на ролики или колеса, и выталкивается или перемещается вперед и назад для разгрузки материала с шахты. С каждым перемещением подвижного стола, материал выгружают из одной из двух противоположных сторон стола, а столбец материала в шахте медленно опускается к нижнему концу.
3. Pat. 1598451 USA, IPC C10J3 / 30. Discharge mechanism / Saathoff G. W.; «Combustion utilities Corp.» (USA). – № 19240751886; filed 24.11.1924; published 31.08.1926.
Изобретение относится к разгрузочным устройствам и более конкретно, к разгрузочному механизму для удаления кокса и золы из газогенераторов типа шахты.
Некоторые разгрузочные механизмы для удаления кокса и золы из газогенераторов типа вала были спроектированы таким образом, что, если колонна топлива в шахте взорвана из периферии - центр - диссоциация топлива из основания колонны с помощью механизма устроена быстрее на периферии, чем в центре.
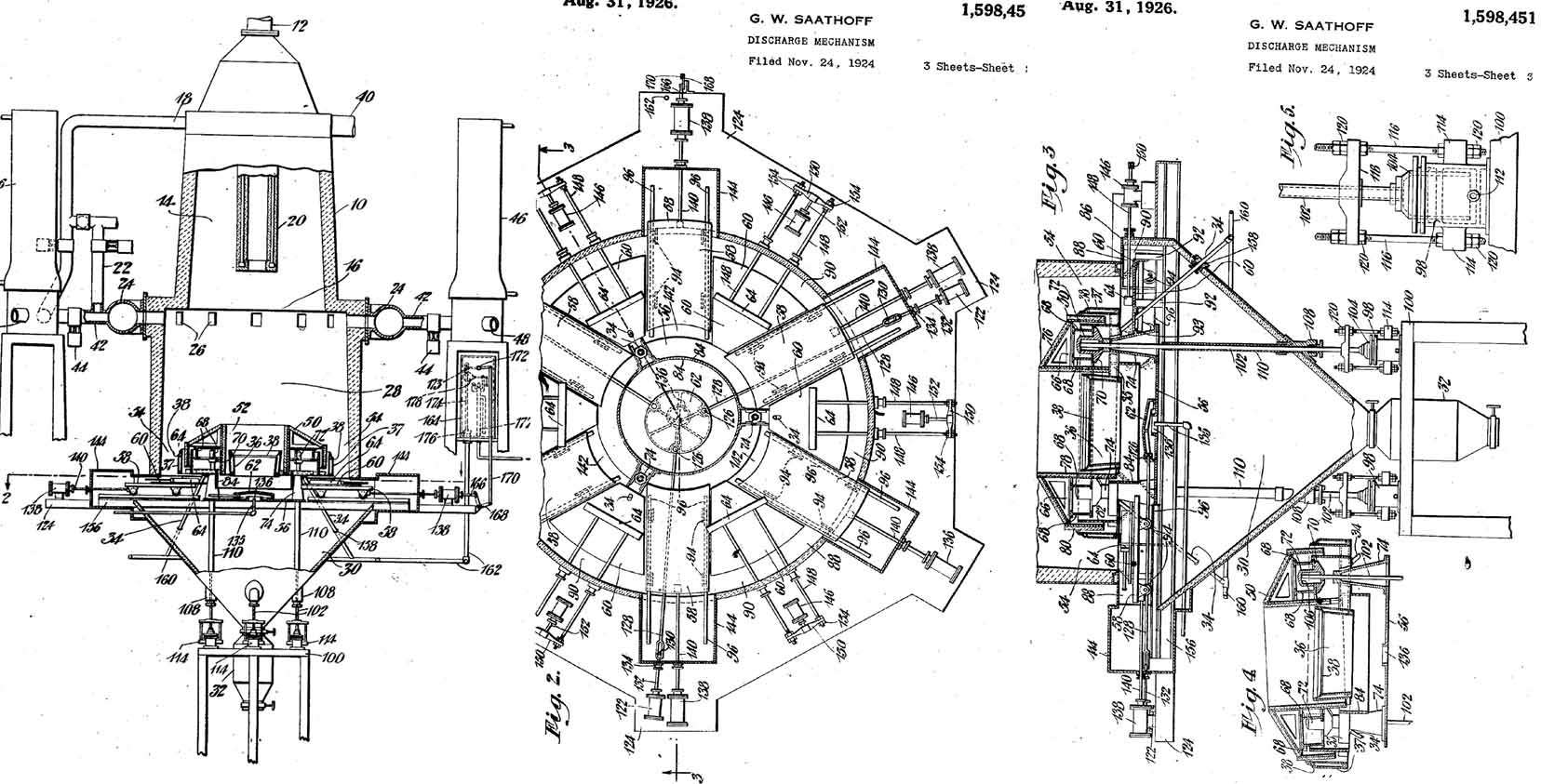
Рисунок 6 – Общий вид механизма, его устройств в разных проекциях
4. Описание разработываемого механизма
В рассматриваемом механизме имеется четыре связанных между собой элементов – ножей-скребков. Связь осуществлена при помощи соединительных осей, а также планок Сама выгрузка готового известняка осуществляется при помощи ножей. Происходит это за счет пересыпания материала через края выгрузочного стола, путем его выталкивания ножами. При этом основные движения исполняются исключительно ножами-скребками, в то время как сам стол остается неподвижным. Также была изменена сама конструкция шахты, и в конце она имеет коническое завершение. Сделано это для того, чтобы материал со своим естественным углом откоса не пересыпался за сами края ножей.
Общий вид и кинематическая схема устройства показаны ниже.
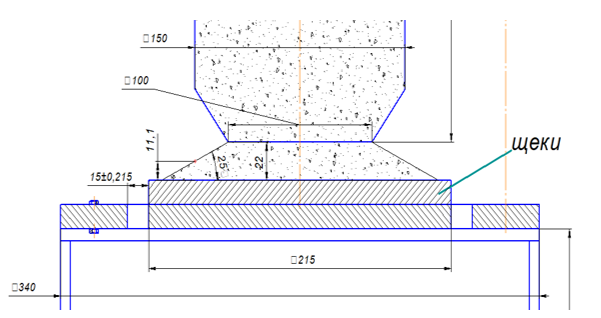
Рисунок 7 – Общий вид механизма выгрузки
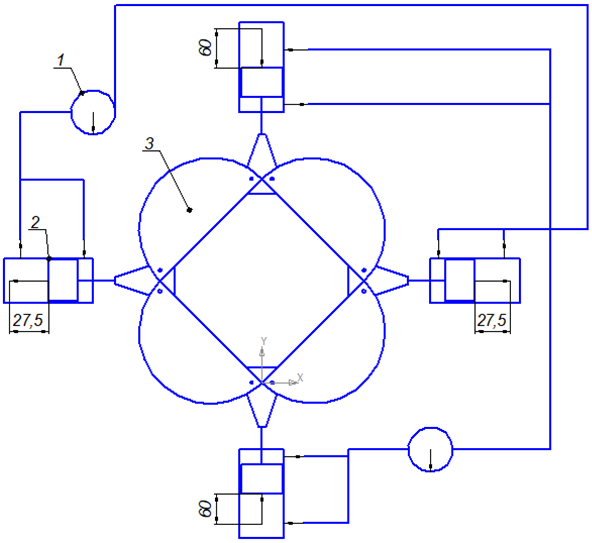
Рисунок 8 – Кинематическая схема механизма; 1 – насос; 2 – гидроцилиндр; 3- нож-скребок.
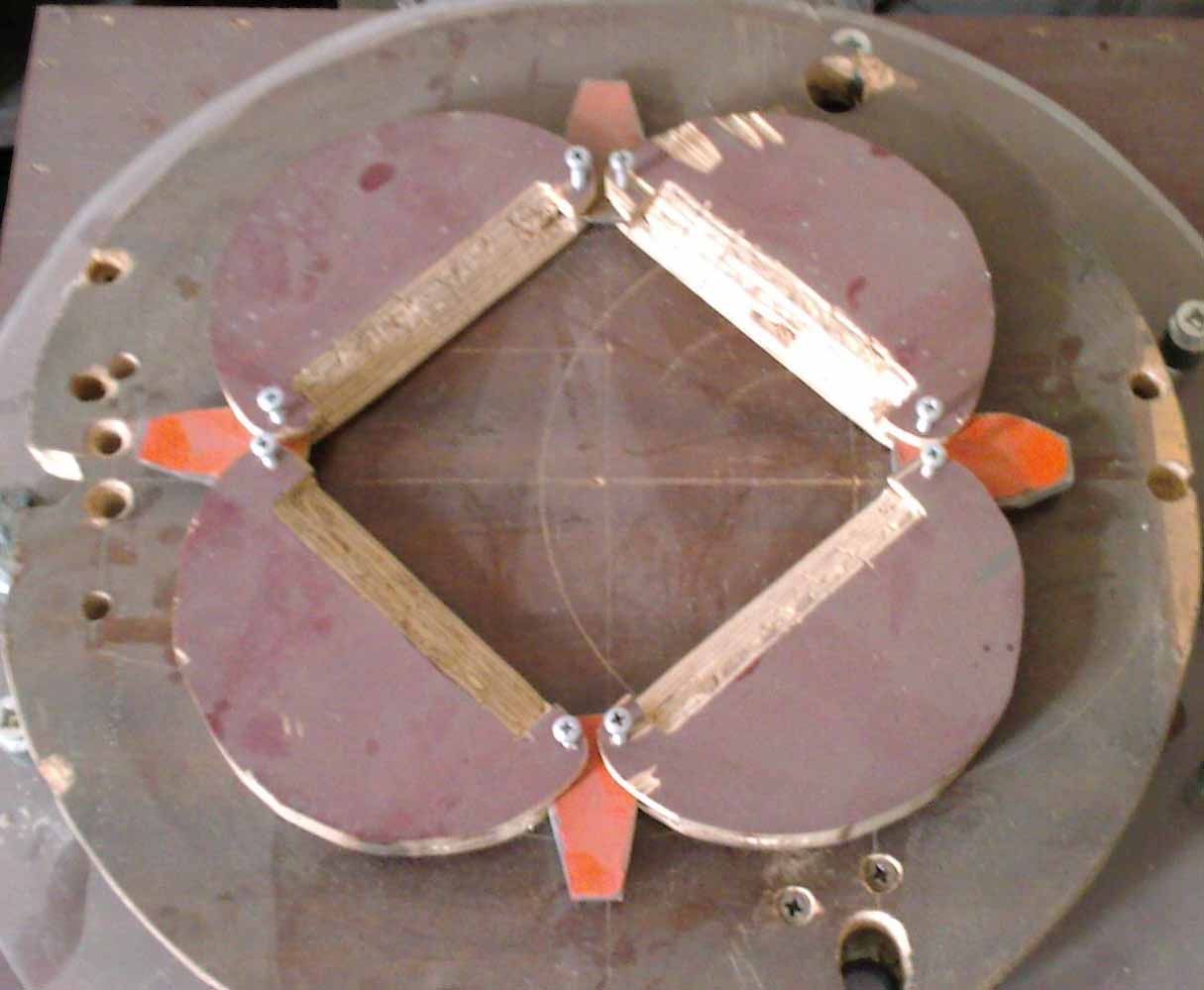
Рисунок 9 – Общий вид выгрузочного механизма.
Принцип работы завязан на гидравлической системе, которая состоит из двух насосов и четырех гидроцилиндров. Цикл их движения связан непосредственно на прямую. Вся система питается двумя насосами одновременно, и в то время как два цилиндра работают на растяжение ножей скребков, и перемещаются на расстояние 27,5 миллиметров назад, другие два цилиндра сжимают ножи, и двигаются на 60 миллиметров вперед. Точно такой же принцип работы, и в обратную сторону только со сменой движений исполнительной пары. Соответственно расстояние хода увеличивается, так как последующие движения гидроцилиндров происходят уже из рабочего положения элементов. Такими движениями обожжённый известняк пересыпается за края стола.
Выводы
По итогу были найдены некоторые патенты на изобретения, что были максимально схожи по конструкции и совпадали по характеру приводящих в действие механизмов. Все они были приведены в отчете вместе с их чертежами и описанием. После этого осуществлялся анализ, который выявил недостатки и схожести рассматриваемых систем.
Как выяснилось есть множество систем, которые очень схожи по конструкции и характеру движения, включая исполнительные элементы. Часть из них очень сложны в эксплуатации, а другие простые. Но по большей части их всех объединяет общий недостаток - неравномерная или быстрая разгрузка материала. Также стоит отметить, что техническое исполнение некоторых из них очень сложное и их использование может быть нецелесообразным.
Дальнейшие исследования направлены на получение данных эксперимента и разработка системы расчета с получением теоритических зависимостей.
Во время написании данного реферата магистерская работа еще не была завершена.
Список источников
- Расширенный поиск патентов – Google; [Электронный ресурс]. – Режим доступа: Расширенный поиск патентов.
- Патенты на изобретения РФ и патентный поиск по библиотекам России и других государств; [Электронный ресурс]. – Режим доступа: Патенты на изобретения РФ.
- Патентный поиск в базе патентов и изобретений, зарегистрированных в РФ и СССР, бесплатные патентные исследования; [Электронный ресурс]. – Режим доступа: Патентный поиск в базе патентов и изобретений СССР.
- Расчеты печей силикатной промышленности. В.Н. Гурина, И.Б. Ревва – 2-е издание, Томский политехнический университет. 2011 г.
- Печи для производства извести, Справочник А.В. Монастырев, А.В. Александров. «Металлургия», Москва – 1979 г. – 10-70 с.
- Приводы машин: Справочник/В. В. Длоугий, Т. И. Муха, А. П.Цупиков, Б. В. Януш; Под общ. редакцией В. В. Длоугого. – 2-е изд., перераб. И доп. – Л.: Машиностроение, Ленингр. отд-ние, 1982. – 383 с.
- Башта Т. М. Гидропривод и гидропневмоавтоматика//М., «Машиностроение», 1972, 230 с.
- Монастырев А.В., Александров А.В. Печи для производства извести.Справочник. – М.: Металлургия, 1979. – 232 с.
- Табунщиков Н.П. Производство извести. – М.: Химия, 1974. – 240 с.
- Монастырев А.В. Производство извести. – М.: Высшая школа, 1978. –225 с.
- Производство извести и сатурационного газа на сахарных заводах / Н.П. Табунщиков, Э.Т. Аксенов, Р.Я. Гуревич, Л.Д. Шевцов. – М.: Легкая и пищевая промышленность, 1981. – 176 с.
- Баренбойм А.М., Галиева Т.М., Гинзбург Д.Б. и др. – М.: Строй-издат, 1964.
- Левченко П.В. Расчеты печей и сушил силикатной промышленности.– М.: Высшая школа, 2002. – 368 с.
- Никифорова Н.М. Теплотехника и теплотехническое оборудова-ние предприятий промышленности строительных материалов и изделий. – М.: Высшая школа, 1981. – 270 с.
- Огнеупоры и огнеупорные изделия. – М.: Издательство стандартов, 1975. – 671 с.
- Воробьев Х.С., Мазуров Д.Я. Теплотехнологические процессы и аппараты силикатных производств. – М.: Высшая школа, 1965. – 773 с.