Abstract
Content
- Introduction
- Relevance of the topic
- Caster Casting Technology
- The purpose and objectives of the study, the planned results
- Findings
- References
Introduction
Steel casting at metallurgical enterprises is carried out using a continuous casting machine. These machines cast varietal or slab billet (up to 95% of steel). As a result of casting according to this technology, a continuously cast billet of infinite length is obtained, which must be cut to length to be transported.
Cutting continuously moving billet is carried out using hydraulic, flying shears or gas cutting. High cutting quality is achieved by cutting with hydraulic shears; for round billet it is necessary to use shaped knives.
Relevance of the topic
The production of high-quality metal-rolls assumes the presence of special equipment installed in the rolling mill or continuous casting machine (CCM) in order to carry out separation operations used for cutting products to length. In this regard, varietal shears and saws of various types are widely used. The use of scissors in comparison with circular saws, allows to obtain a number of advantages: the absence of metal losses associated with the removal of chips, and a more uniform load on the scissors nodes. The study of the process of cross-cutting profiles with a circular cross section with varietal scissors requires the determination of the power parameters of the separation operation. The transverse separation of circular profiles with scissors with flat parallel knives leads to the formation of a number of cutting defects, accompanied by a distortion of the shape of the end face of the workpiece (burrs, having distributed). The presence of these defects reduces the quality of rolled products and increases the cost of it to finish. The use of shaped (shaped) knives eliminates a number of circle cutting defects.
Therefore, studies of the energy-power parameters of the cross-cutting process of a round section billet and the design features of knives, which ensure the quality of commercial products and the reduction of the energy-power parameters of separation operations, are an important scientific and technical problem.
Caster Casting Technology
Continuous casting of steel is carried out on continuous casting machines of the continuous caster. The ladle with metal arriving on pouring, the crane is installed on the lifting and rotary stand. The bucket is covered with a lid and turning the stand is transferred to the working position. The intermediate bucket also occupies a working position. The process of continuous casting of steel begins. After pouring one bucket, another bucket with metal, which is in the reserve position on the free arm of the rotary stand, is transferred to the working position of the casting. The metal from the steel ladle through the tundish enters the mold caster. Liquid steel is continuously poured into a water-cooled form called a crystallizer.
Before starting to pour into the mold, a special device with a locking grip is introduced, as the bottom for the first portion of metal. After solidification of the metal, the seed is drawn out of the crystallizer, dragging the forming ingot with it. Receipt of liquid metal continues, and the ingot is continuously growing. In the crystallizer, only the surface layers of the metal harden, forming a solid ingot shell that retains the liquid phase along the central axis.
In the process of casting the mold makes a reciprocating motion with a certain frequency and amplitude, which prevents the solid crust of the workpiece from sticking to the surface of the mold. The level of the metal in the mold is kept constant, which improves the surface quality of the workpiece and stabilizes the casting process.
Further, under the influence of pulling rollers, the billet enters the secondary cooling zone (curved section of the stream), where water is sprayed onto the metal through the nozzles. In this zone, as a result of forced surface cooling, the workpiece hardens over the entire cross section. This process of forming an ingot is a way to get a piece of unlimited length. In addition, due to the continuity of casting and crystallization, complete uniformity of the ingot structure is achieved along its entire length.
After leaving the secondary cooling zone, the workpiece is pulling – the correct machine
SST pulls cast billet from the mold and simultaneously straightens the arcuate billet (having a curvature of the base radius) in a straight line and the billet is fed for cutting to length and then marked. Cut off the measured billet (usually 6-12 m). Cutting is carried out by hydraulic shears. After that, the billet is transported to the device of transverse transport of billets, where it is transmitted to the refrigerator.
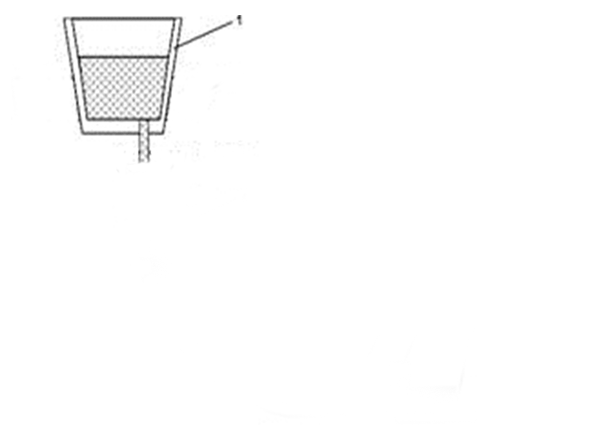
Figure 1 – Diagram of a radial continuous casting machine
The purpose and objectives of the study, the planned results
Purpose of the study – study of the parameters of the hydraulic shears of the continuous casting machine when cutting a billet of circular cross section with a diameter of 200 mm.
Objectives of the study:
- study the technological process and equipment of the continuous casting machine;
- analyze methods and equipment for cutting continuously cast billets;
- analyze the design of hydraulic shears;
- select knife designs for cutting round billet;
- compare the values of the maximum cutting force when cutting a round billet using different knives;
- analyze the stress state of the knives when cutting a round billet using the methods of physical and mathematical modeling;
- establish the influence of the shape of knives on the quality of the cut.
Findings
During the first stage of research, the technological process and equipment of the continuous casting machine was studied; made a review and comparison of methods and equipment for cutting continuously cast billets; A patent search for hydraulic shear structures has been performed; Knife designs selected – straight; chevron; profile with a constant radius; profile with a parabolic edge; profile with variable radius; The physical model of the profile knives was made and their stressed state was studied by the optical polarization method.
References
- Машины и агрегаты металлургических заводов. В 3-х томах. Т.2 Машины и агрегаты сталеплавильных цехов. Учебник для вузов
- Целиков А. И., Полухин П. И., Гребенник В. М. и др. 2-е изд., перераб. и доп. – М.: Металлургия, 1988, – 432 с.
- Патент СССР № 1682056 Авторы: Данченко, Соболенко, Кисиль, Ивченков, Коломоец, Ребрин // Блок ножей для резки проката цилиндрического поперечного сечения
- Патент РФ № 2156676 Филатов А. А., Ванинский М. М., Середкин В. П., Жуков А. А. // Летучие ножницы для резки непрерывнолитого слитка // Патент России № 2156676
- Патент РФ № 2033300 Рубинштейн Ю. Е., Бойко Ю. П., Лебедев В. И., Худанов В. К., Блинов А. П., Бояринцев А. В., Кузьменко С. Г. // Устройство для резки непрерывнолитых слитков // Патент России № 2033300
- Установка ножниц – Руководство по эксплуатации, – НКМЗ
- Сатонин А. В. Исследование энергосиловых параметров процесса поперечного разделения непрерывнолитых сортовых заготовок на ножницах: Вып. 35, 2011 – (Сб. науч. тр. ДонГТУ) // Сб. науч. тр. ДонГТУ – С. 131–137
- Сидоров В. А. Анализ отказов узлов привода холодильника МНЛЗ / В. А. Сидоров // Металлургические процессы и оборудование – 2009, – № 2 (16) – С. 28–33
- Сатонин А. В. Численная методика расчета энергосиловых параметров процесса горячей поперечной резки непрерывнолитых сортовых заготовок / А. В. Сатонин, С. М. Стриченко, А. В. Завгородний, А. А. Житлова // Обработка материалов давлением: сборник научных трудов ДГМА, – Краматорск, – 2011, – № 2, – С. 43–46
- Шинкаренко О. М. Совершенствование режимов работы гидравлических прессов с насосно-аккумуляторным приводом на холостом ходе / Шинкаренко О. М., Корчак Е. С. // Обработка материалов давлением: Обработка материалов давлением: сборник научных трудов ДГМА, – Краматорск, – 2011, – № 2 (27), – С. 190–194
- Денищенко П. Н. Анализ энергосиловых параметров процесса разделения на ножницах сортовых профилей в горячем состоянии / Денищенко П. Н., Боровик П. В., Петров П. А., Стриченко С. М. // Обработка материалов давлением: сборник научных трудов ДГМА, – Краматорск, – 2011, – № 4
- Петров П. А. Математическое моделирование энергосиловых параметров процесса поперечной резки круглых сортовых профилей / Петров П. А., Стриченко С. М., Бойко И. И., Сытник А. А. // Обработка материалов давлением: сборник научных трудов ДГМА, – Краматорск, 2012, – № 1 (30), – С. 227–232
- Боровик П. В. Теоретический анализ процесса горячей резки на ножницах / Боровик П. В. // Обработка материалов давлением: сборник научных трудов ДГМА, – Краматорск, 2012, – № 1 (30), – С. 218–222
- Ворожко С. С. Моделирование ударной резки слитка / Ворожко С. С., Кладова О. Ю., Нарыжный А. Г., Слюсаренко Т. В. // Обработка материалов давлением: сборник научных трудов ДГМА, – Краматорск, 2012, – № 3 (32), – С. 185–191
- Боровик П. В. Теоретический анализ бокового усилия при горячей резке параллельными ножами / Боровик П. В. // Обработка материалов давлением: сборник научных трудов ДГМА, – Краматорск, 2012, – № 4 (33), – С. 132–135
- Боровик П. В. Повышение качества резки проката шевронными ножами / Боровик П. В. // Обработка материалов давлением: сборник научных трудов ДГМА, – Краматорск, 2013, – № 1 (34), – С. 245–250
- Боровик П. В. Анализ напряженно-деформированного состояния металла при разделении квадратного профиля на ножницах // Обработка материалов давлением: сборник научных трудов ДГМА, – Краматорск, – 2014, – № 2
- Сатонин А. В. Имитационное моделирование спектра рабочей нагрузки процесса поперечной резки сортовых профилей на ножницах / Сатонин А. В., Боровик П. В., Петров П. А. // Обработка материалов давлением: сборник научных трудов ДГМА, – Краматорск, – 2014, – № 2
- Петров П. А. Обоснование параметров и совершенствование конструкции ножей поперечной резки сортового проката : дис. канд техн. наук : 05.02.13 : защищена 15.02.2018 / Петров П. А. – Алчевск, 2017, с. 11–13