Abstract
Content
- Introduction
- 1. Theme urgency
- 2. Goal and tasks of the research
- 3. Review of research and development
- 3.1 Equipment automation mine drainage installations
- 3.2 Existing methods of cavitation control in pumping units
- 4. Main results of research and development
- Conclusion
- References
Introduction
Mine dewatering systems are one of the most important objects, the automation of which should ensure maximum reliability and efficiency of pumping water from mine workings, safety of mining operations for the extraction of mineral resources.
Reliability and efficiency of the mine dewatering system in automatic mode significantly depends on the degree of accuracy and reliability of information about the current technological parameters of the drainage operation. It is obtained using measurement or control means, preventing and eliminating the development of emergencies in the state of pumping units, diagnosing the state of mechanical equipment, technological protection etc.
1. Theme urgency
One of the features of the functioning of the mine dewatering system is the variability of its operational parameters, that is, performance, pressure and efficiency during operation, which leads to the exit of the pump-operating mode from the industrial use zone. The abnormal modes of operation include the following modes: rupture of the pressure pipe, hydraulic shock, depressurization of the suction pipe, etc. In some cases, this leads to a shift of the operating point to the zone of non-industrial use of the pump unit or the appearance of a cavitation mode [1]. Consequences of cavitation arising in the pump are the intense hydro abrasive wear of the pump impeller and the passage parts of the machine, the suction line, as well as the disruption of the supply.
So far, the existing equipment for the automation of drainage does not perform the functions of monitoring the flow characteristics and there are no means of protection against the occurrence of cavitation in the pump unit.
2. Goal and tasks of the research
The common consequences for all types of leaks and cavitation are [2]: increased power consumption at drainage systems, reduced resource of pumps and pipelines, reduced efficiency of the drainage installation, a sharp deterioration in the operating characteristics of the pumps on the water supply network.
Because of the cumulative effect of a number of factors and intense wear, the parameters of the pumps change: supply, head, efficiency and pipeline capacity, which, in turn, leads to additional electricity costs for drainage. Therefore, to save energy and efficient operation of the drainage installation, the automatic control system of the mine drainage installation should perform the following control functions:
- closing and opening of the regulating valve to maintain the operating point of the pump in the area of industrial use with minor leaks and changes in the resistance of the hydraulic network;
- regulation of operating modes and control of the pump unit, depending on the level of cavitation development.
The purpose of the design is to develop an automatic protection device for a mine dewatering system against abnormal operating modes for preliminary diagnosing the cavitation threshold and eliminating the emergency conditions of operation of the main water recovery installation.
To achieve this goal it is necessary to solve the following tasks:
- develop a device for monitoring the degree of cavitation in the intake pipe;
- develop a protection device and a system for stabilizing the cavitation reserve of the pump unit.
The projected device for automatic protection against abnormal operating conditions of the drainage installation should:
- clearly record the onset threshold and the degree of cavitation development;
- have a small inertia channel measurement and transmission of information;
- have agreement with the electric valve;
- be able to automatically control the pump operating point in the area of its industrial application in accordance with the current conditions and the degree of cavitation;
- have galvanic isolation along the supply channels of the measuring transducers and actuators from the control unit of the device;
- all circuits of the device must be intrinsically safe.
3. Review of research and development
Mine dewatering systems must ensure reliable pumping of water from underground workings at the lowest possible operating costs [3]. In accordance with the requirement of TB, the dewatering system must be equipped with automation equipment. Automatically operating equipment performs operations instead of pump drivers, ensures accuracy, safety and timeliness of these operations. This allows you to extend the turnaround time by eliminating cases of idling drainage and provides an opportunity to save significant funds.
3.1 Equipment automation mine drainage installations
To automate the process of main drainage, there are various equipment: AVN.1M, SAW, VAV, VAV.1M.
The VAV.1M equipment is a modernized version of the previously manufactured equipment, VAV, UAV. VAV.1M is designed for use in operating, restructuring, mines under construction, hazardous for gas and dust, sudden emissions of coal, gas, and provides automatic control of up to three pumps with high voltage motors. Automatic control of pumping units is carried out as a function of the level in the sump with correction of the work schedule in accordance with the established periods of the maximum of the power system [4].
Equipment VAV.1M provides [5]:
- automatic control of the operation of pumping units as a function of water level;
- remote and local manual control of pumping units;
- in case of failure of the working pump, automatic activation of the backup;
- the order of the pumps;
- the sequence of starting and stopping the pumps during their parallel operation;
- prohibition of the commissioning of a faulty pump;
- correction of the pump operation schedule in order to create natural conditions for its shutdown for the period of the maximum of the power system;
- accounting of the operating time of pumping units;
- display of signals on the controller's display of the water level in the sump, pump operation, failure and the type of malfunction in the installation, the time period of the maximum of the power system.
3.2 Existing methods of cavitation control in pumping units
Control of the occurrence of cavitation in the pump unit can be carried out by the amount of vacuum pressure in the supply pipe, and by vacuum height of suction. However, the use of these methods is associated with difficulties in their technical implementation and does not always promptly determine the development of cavitation phenomena.
To control cavitation, correlation ultrasonic methods of controlling the magnitude of the noise of a cavitating fluid in two different sections can be applied [6]. However, the application of this method is difficult in industrial conditions due to the significant influence of the noise factor of working mechanisms on the ratio of useful signal-to-noise.
In addition, the analysis of literary sources shows that the most effective is the use of ultrasonic cavitation control devices that respond to changes in the physical properties of a fluid, for example, the magnitude of the speed of passage of elastic oscillations in a cavitating fluid depending on the percentage of free air [7]. This method of cavitation control is the simplest and accurate to implement.
4. Main results of research and development
The algorithm of operation of the device for the protection of mine drainage installation from abnormal operating modes
The protection device of the mine drainage installation from abnormal modes of operation should perform the functions assigned to it, that is, function as follows.
After turning on the power source, the device interrogates the primary piezoelectric transducer about the cavitation state of the pumping unit, that is, whether there is a cavitation in the suction line or at the inlet of the pump impeller. Having received a signal from the transducer, the device selects two levels of cavitation: the cavitation threshold, that is, when cavitation is just beginning or is already ending (non-intensive cavitation) and the zone of intensive cavitation.
If the pump enters the so-called zone of intense cavitation, the device starts regulating the operating mode of the pump in order to remove it from the cavitation zone, that is, increase its cavitation margin. The device acts on the electric actuator valve installed on the discharge pipe. The valve rotates and changes the hydraulic pressure of the injection pipeline, thereby changing its hydraulic characteristic, and with it the mode of operation of the pump unit. Control of the operating mode of the water-removal unit is carried out until the pump is withdrawn from the cavitation zone or until the operating point on the hydraulic characteristic of the pump moves to the border of the industrial use zone. In this case, any further control of the damper is unacceptable, so in this case the device automatically excludes the automatic control loop of the pump and will work only in the mode of issuing information on the cavitation state of the drainage installation.
Figure 1 shows the algorithm of operation of the device for monitoring and protecting the main water-removal unit from cavitation.
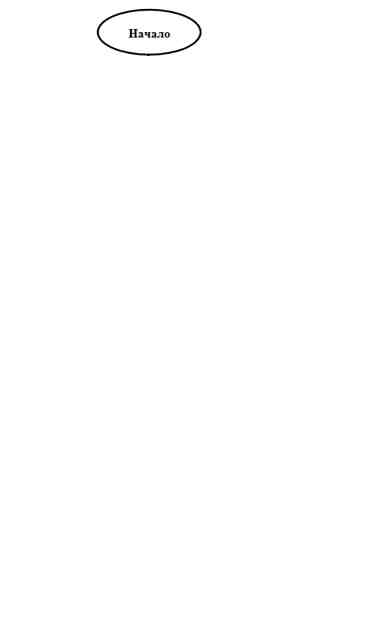
Figure 2 – The algorithm of operation of the device for the protection of mine drainage installation from abnormal operating modes
(animation: 8 frames, 188 kilobytes)
As can be seen from Figure 1, the operation of the circuit begins with the supply of voltage (block 2) and a signal from the piezoelectric transducer about the cavitation state of the drainage installation.
In block 3, the conditions for regulating the pump mode and the limit of operation of the device control loop are established. It is possible to move the working point of the pump along the characteristics of the pump until the angle of rotation of the valve meets the limiting coefficient of the curve of the hydraulic characteristics of the discharge pipe.
In block 4, the first cavitation boundary is established, which corresponds to the cavitation threshold in the non-intensive cavitation zone.
In block 5, the light signaling that the main drainage installation is located in the zone of non-intensive cavitation is reflected.
In block 6, a second cavitation line is laid, which corresponds to the zone of intense cavitation. The location of the pump within this zone is unacceptable, therefore, block 8, performs a protection (regulation) circuit protection robot of an automation device, the functions of which include the stepped adjustment of the angle of rotation of the valve.
The angle is adjusted until the pump is removed from the zone of intense cavitation or the operating point of the pump is close to the boundary of its industrial use.
Conclusion
As a result of consideration of the mine drainage installation as an automation object, the basic requirements for the device and automatic control system and protection of the mine drainage installation against cavitation were formulated. A critical analysis of existing automation systems made it possible to establish that there is currently no continuous control over the threshold and degree of cavitation in the pump unit. This made it possible to outline the main directions for improving the means and systems for automation of mine drainage plants and to develop an automatic control algorithm that ensures high efficiency of the mine drainage operation.
A method for determining the intensity of cavitation, an operation algorithm and a block diagram of a device for protecting a mine drainage installation from abnormal operation modes have been developed. Thus, through the use of the device being developed, it is possible to increase the reliability and efficiency of the drainage installation in automatic mode, significantly improve the working conditions of workers, increase safety, and also improve the technical and economic indicators of the enterprise as a whole.
References
- Гейер В.Г. Шахтные вентиляторные и водоотливные установки. - М.: Недра, 1987. – 270 с.
- Шевчук С.П. Повышение эффективности водоотливных установок- К.: Техника, 1991. – 53 с.
- Попов В.М. Водоотливные установки. – М.: Недра, 1990. - 294 с.
- Батицкий В.А., Лухолетов В.И., Рыжков А.А. Автоматизация производственных процессов и АСУТП в горной промышленности. - М.: Недра, 1991. - 303 с.
- Научные труды высших учебных заведений Литовской ССР. – Ультразвук. – Каунасс. – 1979, №11.
- Карелин В.Я. Кавитационные явления в центробежных и осевых насосах. - М.: Недра, 1975. – 353 с.
- Шутилов В.А Основы физики ультразвука. - Л.: Изд-во Ленинградского университета, 1980. – 280 с. – 288 с.