Реферат по теме выпускной работы
Содержание
1. Введение
Важной задачей технического процесса на металлургических заводах является широкое внедрение высокопроизводительных комплексов, оснащенных современным электрооборудованием. Их внедрение обеспечивает значительное повышение производительности работы предприятия. Высокая эффективность металла зависит от надежности работы металлургических печей, которая является основным в процессе производительности металла.
В черной металлургии на первый план выдвигаются факторы, обеспечивающие повышение эффективности производства, дальнейшее улучшение качества и расширение сортамента металлопродукции. Один из основных путей решения этих задач – автоматизация технологических процессов в черной металлургии. Широкое внедрение автоматизации технологических процессов в черной металлургии диктуется условиями металлургического производства и ростом потребности в высококачественной металлопродукции.
С увеличением мощности агрегатов и повышения требований к качеству металлопродукции выявилась необходимость перехода от локальных средств автоматического регулирования отдельных параметров к многосвязанному автоматическому регулированию и управлению работой всего агрегата.
2. Цель работы
Поэтому цель работы – усовершенствование системы автоматизации управления рабочими режимами металлургической печи, путем внедрения новых технических решений в существующую аппаратуру управления.
Среди технологических агрегатов черной металлургии важную роль играют прокатные станы, выпускающие конечную продукцию металлургического производства. Качество продукции и производительность станов во многом определяются работой нагревательных печей, причем в большинстве случаев ошибки, возникающие при нагреве металла, уже не могут быть исправлены. И, проявляясь на последующих переделах, эти ошибки приводят к снижению выхода годной продукции.
В условиях нагрева заготовок с переменными геометрическими и теплотехническими параметрами, а также при переменном темпе выдачи заготовок из печей, получение требуемого качества нагрева заготовок возможно лишь при автоматическом управлении работой участка нагревательных печей. Существовавшие ранее системы управления нагревательными печами обеспечивали лишь стабилизацию нескольких отдельных параметров теплового режима работы печей, таких как температура в зонах нагрева, соотношение расходов топлива и воздуха и давления в рабочем пространстве печи. В этих системах задания локальным регуляторам указанных параметров устанавливались вручную сварщиком печи, исходя из его опыта, что подчас в условиях напряженной работы стана приводило к субъективным ошибкам. При этом возникали недогрев заготовок, перерасход топлива, значительное окалинообразование и т.п.
Являясь начальным звеном технологической линии прокатного производства, нагревательные печи в своей работе тесно связаны с ритмом работы прокатного оборудования, и на ряду с этим сохраняют особенности, присущие всем теплотехническим агрегатам. Основное время печи работают в переходных режимах, вызванных изменением сортамента, марки нагреваемых заготовок и темпа их выдачи, и сварщик, даже обладающим большим опытом работы, не в состоянии обеспечить приемлемое (не говоря уже об оптимальном) управление. Кроме того, следует учесть, что стан обслуживают несколько печей и необходимо обеспечить идентичный нагрев заготовок в отдельных печах и согласовать их работу между собой.
3. Объект автоматизации и его особенности
Методические печи предназначены для нагрева металла перед прокаткой и относятся к печам непрерывного действия. За время нагрева заготовки постепенно перемещаются через всю печь от входа к выходу.
Методическая печь состоит из рабочего пространства, где происходит сжигание топлива и нагрев металла, и ряда систем: отопление, транспортировка заготовок, охлаждения элементов печи, управление тепловым режимом и др.
Методические печи могут различаться числом отапливаемых зон, формой рабочего пространства, способами перемещения метала, подвода топлива и воздуха, сжигания топлива, а также по размерам и производительности, по виду нагреваемого метала, по типу обслуживаемых станов и ряду других признаков.
Уменьшение окисления и обезуглероживания поверхности заготовок из
качественных сталей достигают при двустадийном нагреве. При этом
используют обычно несколько методических печей. В одной из них метал
медленно нагревают до 850–900°C. После этого заготовки подают в другие
печи, где происходит их быстрый
нагрев до конечной температуры.
Качественный нагрев металла характеризуется следующими показателями:
- Температура поверхности заготовки θп, усредненная по ее длине, на выходе из печи соответствует заданному значению с точностью ±10–15 К.
- Заготовки прогреты в достаточной мере, так что перепады температур по толщине заготовок Δθ не превышают допустимых значений Δθдоп. Величина Δθдоп составляет 20–40 К, а в местах соприкосновения заготовок с подовыми трубами равна 50–70 К.
- Перепады температуры по длине заготовок соответствует принятой технологии прокатки.
- Скорость нагрева металла от исходного состояния до 500–700°C не превышает максимального допустимого значения
В методической печи, кроме температуры, можно измерять расход газа и воздуха, избыточность давления газа, теплоту сгорания отопительного газа.
Управление тепловым режимом в методической печи невозможно без исследования тепловых процессов, происходящих в данном объекте управления.
Тепловые балансы по слябу и по газу строятся на основании структурной схемы который представлен на рисунке 1, где приняты следующие обозначения: Qg – теплота, выделившаяся при сгорании топлива (газа), кДж/м3; Qp – теплота, вносимая внешним подогретым воздухом, кДж/м3; Qd – количество тепла, идущего с дымовыми газами, кДж/м3; Qv – количество тепла, идущего в атмосферу, кДж/м3; Qz – количество тепла, которое усваивается материалом сляба, кДж/м3; Td1 – температура дымовых газов в рекуператора, °C; Td2 – температура дымовых газов после рекуператора, °C; Tp1 – температура воздуха в рекуператоре, °C; Tp2 – температура воздуха после рекуператора, °C; Tzz – температура в сварочной зоне методической печи, °C, R – рекуператор.
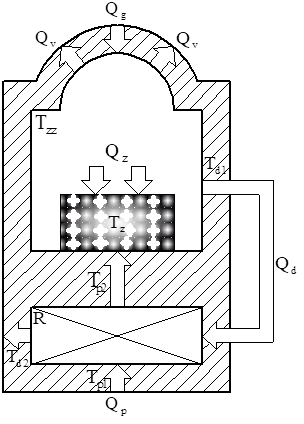
Рисунок 1 – Структурная схема нагрева заготовки в сварочной зоне методической печи (анимация: 3 кадра, задержка 100 мс, 23.9 килобайт)
На основе методов декомпозиции и дальнейшего агрегатирования составим структуру математической модели нагрева заготовки в сварочной зоне методической печи (рисунок 2). Объемный расход природного газа Vg с учетом его текущих компонентов VH2, VCO, VCH4, VC2H4, VCO2, VO2, VN2, VH2O и объемный расход воздуха Vp в соответствии VN2, VO2, коэффициент избытка воздуха α с учетом температуры подогрева воздуха Tp2 образуют дымовые газы при сгорании единицы топлива соответствующего состава Vd: VCO2, VO2, VN2, VH20.
В качестве входящих частей материального баланса выступают теплота сгорания топлива Qg, а также физическое тепло, вносимое подогретым воздухом Qp. В состав расходных частей включают: потери тепла с уходящими газами с продуктами сгорания Qd, и тепло, которое поглощается материалом сляба [1].
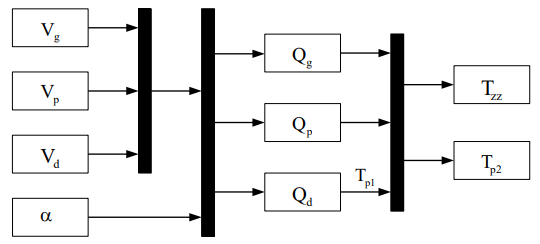
Рисунок 2 – Структура модели нагрева заготовки в сварочной зоне методической печи
Уравнение теплового баланса, которое характеризует процессы в сварочной зоне методической печи имеет вид:
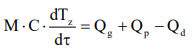
или

Уравнение теплового баланса рекуператора описывается уравнением:

Уравнение теплового баланса при сгорании природного газа без учета потерь тепла на усвоение слябов, имеет вид:

где Qg – теплота, выделившаяся при сгорании топлива, кДж/м3; Qp – теплота, вносимая наружным воздухом, кДж/м3; Qd – количества тепла, идущего с дымовыми газами, кДж/м3; М – масса заготовки, кг; С – теплоемкость обмуровки воздухоподогревателя, кДж/(кг.°C) Tz – температура заготовки, °C. V – объемный расход вещества относительного для каждого компонента,м3/м3; ηp – потери воздуха, ηp = 0,95 – 0,99.
Таким образом уравнение теплового баланса, которое описывает процесс нагрева металла в сварочной зоне методической печи, имеет вид:

Преобразуем уравнение (2):

или

Учитывая уравнение (2), уравнение (4) примет вид:

Основой для получения уравнения, которое характеризует нагрев заготовки в сварочной зоне методической печи, является:

где Q – удельный тепловой поток, Вт / м2; P – поверхность, которая обогревается, м2; M – масса, кг ; C – удельная теплоемкость тела, кДж / м3 °C.
Левая часть выражения характеризует приход тепловой энергии по условиям внешнего теплообмена, а правая – усвоенную ее количество по условиям внутреннего.
Тепловой баланс по слябу в методической печи имеет вид:

Соотношение M/P – массовая нагрузки нагреваемого тела. Для пластины:

где kn = 1 – коэффициент массовой нагрузки
Плотность теплового потока при внешнем конвективном теплообмене:
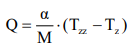
где α – коэффициент теплопередачи к поверхности металла, Вт / м2 * с.
Модификация уравнения теплового баланса в сварочной зоне методической печи позволит в дальнейшем получить передаточные функции составляющих объекта. Анализ тепловых законов позволит исследовать температурный режим методической печи, а, следовательно, и качество нагрева слитков.
Выводы
Исследована система автоматического управления температурными режимами в методической печи. В результате критического анализа, установлено, что применяемая система автоматического управления работой зон нагрева методической печи не выполняет функции эффективного управления, что приводит к снижению качества нагрева слябов, а также к перерасходу топлива.
При рассмотрении процесса нагрева заготовки металла в методической печи установлено, что поддержание заданного температурного режима влияет на равномерность прогрева заготовки металла.
Проведено моделирование процесса нагрева металла в методической печи. Выполнен анализ и исследование температурных режимов при различных технологических параметрах процесса нагрева слябов.
Дальнейшая реализация системы управления на базе микроконтроллера позволяет повысить уровень автоматизации данного объекта, улучшить качество нагрева заготовки, уменьшить расход топлива на термическую обработку сляба.
На момент написания данного реферата магистерская работа еще не завершена. Окончательное завершение: июнь 2019 года. Полный текст работы и материалы по теме могут быть получены у автора или его руководителя после указанной даты.
Список источников
- Буглак, Л. И. Автоматизация методических печей. / Л.И. Буглак – М.,
Металлургия
, 1981.- 196 с. - Каганов, В. Ю. Автоматизация управления металлургическими проессами. / В. Ю. Каганов, О. М. Блинов, М. М. Беленький – М.,
Металлургия
, 1974.- 416 с. - Блинов, О. М. Основы металлургической теплотехники. / О. М. Блинов, Ю. Д. Глебов, И. А. Прибытков – М.,
Металлургия
, 1973.– 280 с. - Каганов, В. Ю. Автоматизация металлургических печей / В. Ю. Каганов, О. М. Блинов, Г. М. Глинков, – М.,
Металлургия
, 1975.– 376 с., ил. - Солодовников В. В. и др. Основы теории и элементы систем автоматического регулирования [Текст] / В. В. Солодовников. – М.: Машиностроение, 1985. – 534 с.
- Шагов Н. И. Теплотехника и автоматизация металлургических печей [Текст] / Н. И. Шагов.— Магнитогорск: Металлургиздат., 1969. — 527 с.
- Иванцов Г. П. Нагрев металла [Текст] / Г. П. Иванцов. — Свердловск: Металлургиздат., 1985. — 215 с.
- Самарский А. А., Введение в теорию разностных схем [Текст]/ А. А. Самарский. — М.: Наука., 1971. — 552 с.
- Скворцов А. А. Влияние внешних воздействий на процесс формирования слитков и заготовок [Текст] / А. А. Скворцов. — М.: Металлургиздат., 1991. — 454 с.
- Кривандин В. А. Теплотехника металлургического производства [Текст] / В. А. Кривандин. – М.: МИСИС, 2002. – 736 с.