Abstract
Contents
- 1. Introduction
- 2. The goal of the work
- 3. The object of automation and its features
- Conclusions
- List of sources
1. Introduction
An important task of the technical process at the metallurgical plants is the wide introduction of high–performance complexes equipped with modern electrical equipment. Their implementation provides a significant increase in the productivity of the company. The high efficiency of the metal depends on the reliability of the operation of the metallurgical furnaces, which is the main in the process of metal productivity.
In the ferrous metallurgy, the factors that ensure the increase of production efficiency, further improvement of the quality and expansion of the metal product class are put forward on the foreground. One of the main ways of solving these problems is automation of technological processes in ferrous metallurgy. The widespread introduction of automation of technological processes in ferrous metallurgy is dictated by the conditions of metallurgical production and the growing demand for high–quality metal products.
With the increase in aggregate capacity and increased requirements for the quality of metal products, it became necessary to switch from local the means of automatic adjustment of individual parameters to the multi–connected automatic adjustment and control of work of the whole unit.
2. The goal of the work
Therefore, the goal of the work is to improve the automation system. control of operating conditions of the metallurgical furnace, by introducing New technical solutions to the existing control equipment.
Among the technological units of ferrous metallurgy is an important role play rolling mills producing final products metallurgical production. Product quality and productivity states are largely determined by the work of heating furnaces, and in most of the errors that occur when heating the metal, no longer can be fixed. And, manifested in subsequent revisions, these are errors lead to a decrease in the yield of suitable products.
In the conditions of heating the workpieces with variable geometric and thermotechnical parameters, as well as with a variable rate of issue billets from furnaces, obtaining the required quality of heating of billets possible only with the automatic management of the site heating furnaces. Institutes that were previously in control heating furnaces provided only stabilization of several separate parameters of the thermal mode of operation of furnaces, such as temperature in the zones of heating, the ratio of fuel and air consumption and pressure in the working space of the furnace. In these systems, the task is local the regulators of the specified parameters were set manually by the welder furnace, based on his experience, that sometimes I will be in a state of stress led to subjective errors. At the same time there was insufficient heat billets, fuel overcurrent, significant scale formation, etc.
Being the starting point of the rolling mill line production, heating furnaces in their work are closely related to the rhythm the work of rolling equipment, and in line with this, retain the features, inherent in all heat engineering units. The main furnace time is working in the transitional modes caused by the change of the varietal, the mark heat the blanks and the pace of their issue, and the welder even owns great work experience, not able to provide acceptable (not to mention already about the optimal) management. In addition, it should be noted that the state Serves several furnaces and it is necessary to provide identical heating Blanks in individual furnaces and coordinate their work with each other.
3. The object of automation and its features
Technological furnaces are intended for heating the metal before rolling and relate to continuous furnaces. During the heating of the workpiece gradually moved through the entire stove from the entrance to the exit.
Technological furnace consists of the working space where it occurs combustion of fuel and heating of metal, and a number of systems: heating, transportation of billets, cooling of furnace elements, control thermal regime, etc.
Technological furnaces may differ in the number of heating zones, the form working space, ways of moving metal, supplying fuel and air, fuel combustion, as well as size and performance, by the fact that the metal is heated, by the type of serviced states, and others signs
Reducing the oxidation and degradation of the surface of the billets with qualitative steels are achieved with two–stage heating. With usually use several methodical furnaces. One of them is metal slowly heated to 850–900 ° C. After that, the workpieces are fed to others furnaces, where their "rapid" heating to the final temperature occurs.
High–quality metal heating is characterized by the following indicators:
- The surface temperature of the workpiece θп, averaged over its length, on the furnace output corresponds to a specified value with an accuracy of ± 10–15 K.
- The workpieces are heated to a sufficient degree, so that the temperature drops on the thickness of the & Delta; & theta; do not exceed the permissible values Δθдоп. Value Δθдоп is 20–40 K, and in places where the billets collide with underwater pipes is 50–70 K.
- Temperature fluctuations along the length of the workpiece corresponds to the accepted rolling technologies.
- The speed of heating the metal from the original state to 500–700 °C not exceeds the maximum allowable value.
In a methodical furnace, except for temperature, it is possible to measure the flow of gas and air, excess pressure of gas, heat of combustion of heating gas.
Management of thermal regime in a methodical furnace is impossible without research of thermal processes occurring in this object management.
Heat balances on slabs and gas are built on the basis of structural The scheme is presented in Figure 1, where the following are adopted marking: Qg – heat released during combustion of fuel (gas), kJ / m3; Qp – the heat supplied by the external heated air, kJ / m3; Qd – amount of heat coming from flue gases, kJ / m3; Qv – amount of heat entering the atmosphere, kJ / m3; Qz – amount of heat absorbed by the material of the slab, kJ / m3; Td1 – temperature of flue gases in the recuperator, ° C; Td2 – temperature of flue gases after recuperator, ° C; Tp1 – air temperature in the recuperator, ° C; Tp2 – air temperature after recuperator, ° C; Tzz – temperature in the welding zone of the furnace, ° C, R – recuperator.
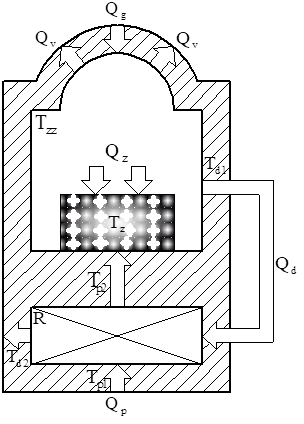
Figure 1 – Structural diagram of the heating of the workpiece in the welding zone of the furnace (animation: 3 frames, 100 ms delay, 23.9 kilobytes)
Based on the methods of decomposition and further aggregation we will make a structure mathematical model of heating of the workpiece in the welding zone methodical furnace (figure 2). Volumetric consumption of natural gas Vg taking into account its current Components VH2, VCO, VCH4, VC2H4, VCO2, VO2, VN2, VH2O and volumetric flow air Vp corresponding to VN2, VO2, excess air ratio α with taking into account the temperature of the heating of air Tp2 form flue gases at Combustion units of fuel of the corresponding composition Vd: VCO2, VO2, VN2, VH20.
As the input parts of the material balance are warmth the combustion of fuel Qg, as well as the physical heat brought in by the heated air Qp. The composition of the consumable parts include: heat loss with gases with products of combustion Qd, and heat that is absorbed slab material [1].
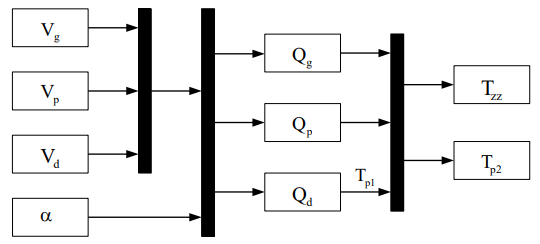
Figure 2 – Structure of the model of heating of the workpiece in the welding zone of the methodical furnace
Equation of thermal balance, which characterizes the processes in the welding zone of the furnace has the form:
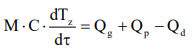
or

The equation of the thermal balance of the recuperator is described by the equation:

Thermal balance equation for combustion of natural gas without consideration heat loss on the absorption of slabs, has the form:

where Qg – heat released during combustion of fuel, kJ / m3; Qp – the heat supplied by the outside air, kJ / m3; Qd – amount of heat coming from the flue gases, kJ / m3; M – weight of workpiece, kg; C – heat capacity of air heater trimming, kJ / (kg. ° C) Tz – temperature of the workpiece, ° C. V – volume flow of substance relative to each component, m3 / m3; Η p - air loss Η p = 0.95 - 0.99.
Thus, the equation of thermal balance, which describes the process the heating of the metal in the welding zone of the furnace, has the form:

Convert the equation (2):

or

Given equation (2), equation (4) takes the form of:

The basis for obtaining an equation that characterizes heating billets in the welding zone of the furnace, there is:

where Q – specific heat flux, W / m2; P – the heated surface, m2; M – weight, kg; C – specific heat of a body, kJ / m3 ° C.
The left part of the expression characterizes the arrival of thermal energy by conditions of external heat transfer, and rights - assimilated its quantity for conditions of the internal.
The thermal balance of slabs in the furnace has the form:

The ratio M / P – the massive load of the heated body. For the plate:

where kn = 1 is the mass load factor
Heat flow density with external convective heat exchange:
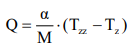
where α – coefficient of heat transfer to the metal surface, W / m2 * s.
Modification of the equation of thermal balance in the welding zone Methodical furnace will allow to receive transfer functions in the future constituent objects. The analysis of thermal laws will allow us to investigate the temperature regime of the methodical furnace, and, consequently, the quality ingot heating
Conclusions
The system of automatic temperature control is investigated modes in a methodical furnace. As a result of critical analysis, It is established that the system of automatic control of work is used the heating zone of the methodical furnace does not function as efficient management, which leads to a decrease in the quality of heating slabs, as well as to overfill fuel
When considering the process of heating the metal work in Methodical furnace has been found to support a given temperature the mode affects the uniformity of the metal workpiece warming up.
The simulation of the metal heating process in the methodical is carried out furnace The analysis and research of temperature regimes at various technological parameters of the heating process of slabs.
Further implementation of the management system on the base Microcontroller allows you to increase the level of automation of this of the object, improve the quality of the heating of the workpiece, reduce fuel consumption by heat treatment of the slab.
At the time of writing this abstract, the master's thesis has not yet been completed. Final completion: June 2019. Full text of work and materials on the topic can be obtained from the author or his manager after the specified date.
List of sources
- Буглак, Л. И. Автоматизация методических печей. / Л.И. Буглак – М.,
Металлургия
, 1981.- 196 с. - Каганов, В. Ю. Автоматизация управления металлургическими проессами. / В. Ю. Каганов, О. М. Блинов, М. М. Беленький – М.,
Металлургия
, 1974.- 416 с. - Блинов, О. М. Основы металлургической теплотехники. / О. М. Блинов, Ю. Д. Глебов, И. А. Прибытков – М.,
Металлургия
, 1973.– 280 с. - Каганов, В. Ю. Автоматизация металлургических печей / В. Ю. Каганов, О. М. Блинов, Г. М. Глинков, – М.,
Металлургия
, 1975.– 376 с., ил. - Солодовников В. В. и др. Основы теории и элементы систем автоматического регулирования [Текст] / В. В. Солодовников. – М.: Машиностроение, 1985. – 534 с.
- Шагов Н. И. Теплотехника и автоматизация металлургических печей [Текст] / Н. И. Шагов.— Магнитогорск: Металлургиздат., 1969. — 527 с.
- Иванцов Г. П. Нагрев металла [Текст] / Г. П. Иванцов. — Свердловск: Металлургиздат., 1985. — 215 с.
- Самарский А. А., Введение в теорию разностных схем [Текст]/ А. А. Самарский. — М.: Наука., 1971. — 552 с.
- Скворцов А. А. Влияние внешних воздействий на процесс формирования слитков и заготовок [Текст] / А. А. Скворцов. — М.: Металлургиздат., 1991. — 454 с.
- Кривандин В. А. Теплотехника металлургического производства [Текст] / В. А. Кривандин. – М.: МИСИС, 2002. – 736 с.