Содержание
- Введение
- 1. Актуальность темы
- 2. Цель и задачи исследования, планируемые результаты
- 3. Анализ процесса ректификации
- 4. Разработка концепции САУ
- 4.1. Анализ существующих систем автоматического управления (САУ) объектом и обоснование необходимости совершенствования САУ
- 4.2. Описание, оценка преимуществ и недостатков разработанных альтернативных вариантов концепции САУ
- 4.3. Обоснование выбора и ожидаемые результаты выбранного варианта концепции САУ
- 5. Синтез математической модели объекта
- 5.1. Разработка структурной схемы
- 5.2. Математическая модель объекта
- 6. Выводы
- Список источников
Введение
Ректификация является одним из важнейших процессов в химической промышленности. Ее цель состоит в разделении смеси компонентов с разными температурами кипения на отдельные фракции. Движущая сила ректификации – отличие фактической концентрации компонентов в паровой фазе от равновесной для данного состава жидкой фазы. Парожидкостная система стремится к достижению равновесного состояния. При контакте с жидкостью пар обогащается легколетучими (низкокипящими) компонентами, а жидкость – труднолетучими (высококипящими) компонентами. Жидкость и пар движутся противотоком: пар – вверх, жидкость – вниз. Через определенное время из верха колонны непрерывно стекает жидкость, максимально богатая легкокипящим компонентом, а из низа – высококипящим.
Регулирование процесса дистилляции представляет интерес по нескольким причинам. С научной точки зрения это сложный многомерный процесс, к управлению которым можно применять различные техники. С промышленной же точки зрения более качественное регулирование позволит максимизировать прибыли при более рациональном расходовании сырья, более высокое энергоэффективности и т.п.
1. Актуальность темы
На данный момент проблема автоматизации технологического процесса состоит в том, что настройка регуляторов зачастую происходит эмпирическим путем, что в условиях реального объекта сопряжено с потерями сырья и большим временем ввода системы в эксплуатацию.
Развитие вычислительной техники последних лет сделало возможным применение более совершенного математического аппарата для описания процессов, протекающих в ректификационных колоннах, с целью формирования управляющих воздействий, обеспечивающих наилучшие характеристики выходного продукта и максимальную компенсацию различных возмущений.
Система автоматического управления позволит оптимизировать процессы поддержания основных технологических параметров процесса ректификации и увеличить эффективность установки в качестве и количестве продукции.
2. Цель и задачи исследования, планируемые результаты
Поддержание концентрации дистиллята на заданном уровне – главная задача системы управления. Данный параметр измеряется либо напрямую (датчиком концентрации), либо опосредованно (датчиком температуры), и влияет на расход флегмы, подаваемой в колонну.
Также необходимо обеспечить управление потоком флегмы, возвращаемым в колонну орошением. Это достигается подачей на регулятор расхода сигнала либо с датчика температуры верха колонны, либо с датчика концентрации, в зависимости от выбранной схемы.
Кроме того, требуется сигнализация в случае выхода из заданных пределов давления в колонне (измеряется датчиком давления в верхней части колонны), температуры верха колонны, расхода исходной смеси. При давлении в колонне выше допустимого, а также при прекращении подачи исходной смеси в колонну, должны сработать автоматические устройства защиты, отключающие установку. При этом потоки дистиллята, остатка и теплоносителей перекрываются, а поток флегмы открывается.
В целях как можно более полного контроля процесса и анализа производительности системы необходимо обеспечить сбор, отображение и хранение данных с датчиков температуры верха колонны, расхода питающей смеси, расхода пара в кипятильник.
Ожидаемый экономический и социальный эффект от введения системы – минимизация расхода пара и хладагента, повышение концентрации полезного вещества в выходном продукте при том же объеме исходной смеси, а также сведение к минимуму влияние человеческого фактора на технологический процесс.
3. Анализ процесса ректификации
Ректификация – разделение жидких смесей на практически чистые компоненты, отличающиеся температурами кипения, путём многократных испарений жидкости и конденсации паров[1].
В качестве объекта управления имеется ректификационная установка для разделения бинарной смеси, состоящая из тарельчатой ректификационной колонны, выносного кипятильника, дефлегматора и сборника конденсата (рис.1).
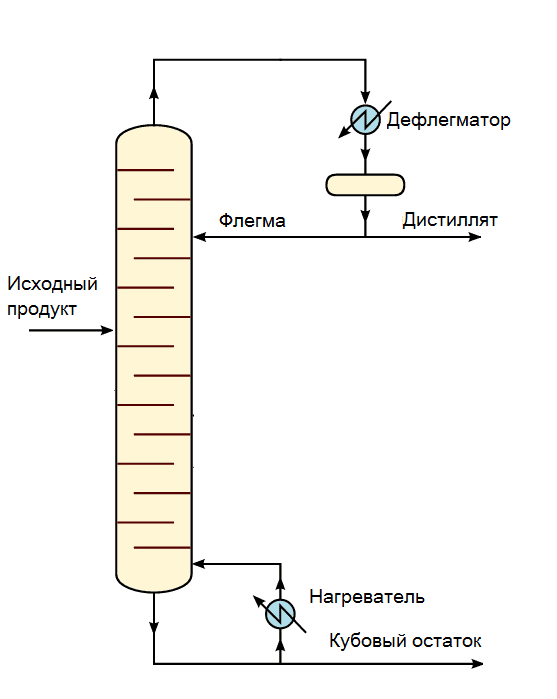
Рисунок 1 – Схема ректификационной установки
С физической точки зрения ректификация возможна, поскольку изначально концентрация отдельных компонентов смеси в паровой и жидкой фазах отличается, но система стремится к равновесию – одинаковому давлению, температуре и концентрации всех веществ в каждой фазе. При контакте с жидкостью пар обогащается легколетучими (низкокипящими) компонентами, в свою очередь, жидкость – труднолетучими (высококипящими) (рис.2). Одновременно с обогащением происходит обмен теплом.
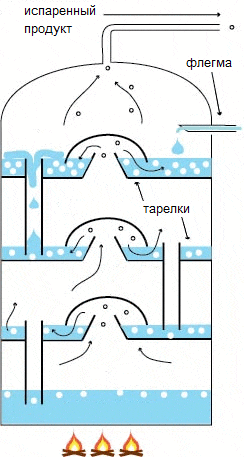
Рисунок 2 – Иллюстрация процессов внутри колонны (анимация: 4 кадра, 10 циклов повторения, 134 килобайт)
После включения жидкость в кубе доводится нагревателем до кипения. Образовавшийся пар поднимается вверх по колонне, затем попадает в дефлегматор, где конденсируется (появляется флегма) и по стенкам трубы возвращается в жидком виде в нижнюю часть колонны, на обратном пути контактируя с поднимающимся паром на тарелках или насадках. Под действием нагревателя флегма снова становится паром, а пар вверху опять конденсируется дефлегматором. Процесс становится циклическим, оба потока непрерывно контактируют друг с другом[1-3].
Показателями эффективности процесса являются составы выходных потоков (кубовая жидкость, дистиллят), содержащих целевой продукт. На чистоту этих целевых продуктов оказывает влияние ряд возмущающих воздействий процесса – состав, параметры тепло- и хладагентов, давление в колонне и другие величины.
Применительно к процессу ректификации поддержание заданного состава целевого потока является целью управления процессом. Состав потока, не содержащего целевого продукта, – кубового остатка – может меняться вследствие изменения состава и скорости подачи исходного питающего потока.
Основные управляющие воздействия – расходы флегмы в колонну и теплоносителя в кипятильник. Причём изменение расхода флегмы относительно быстро приводит к изменению состава дистиллята и одновременно с большим запаздыванием и в значительно меньшей степени – к изменению состава кубового остатка. Изменение же расхода греющего пара приводит в основном к изменению состава кубового остатка; состав флегмы при этом изменяется намного слабее[4].
Возмущающими воздействиями являются изменения расхода исходной смеси, параметры исходной смеси, давление в колонне.
Подытожив все вышесказанное и представив объект в виде «черного ящика», можно получить следующую схему анализа ТП ректификации с точки зрения основных материальных потоков и их информационных переменных (рис. 3).
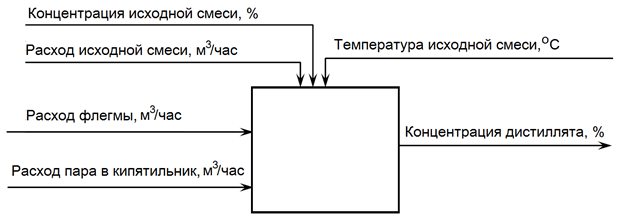
Рисунок 3 – Схема анализа ТП ректификации с точки зрения основных материальных потоков и их информационных переменных
4 Разработка концепции САУ
4.1 Анализ существующих систем автоматического управления (САУ) объектом и обоснование необходимости совершенствования САУ
Наиболее простая система управления ректификационной установкой изображена на рис. 4.
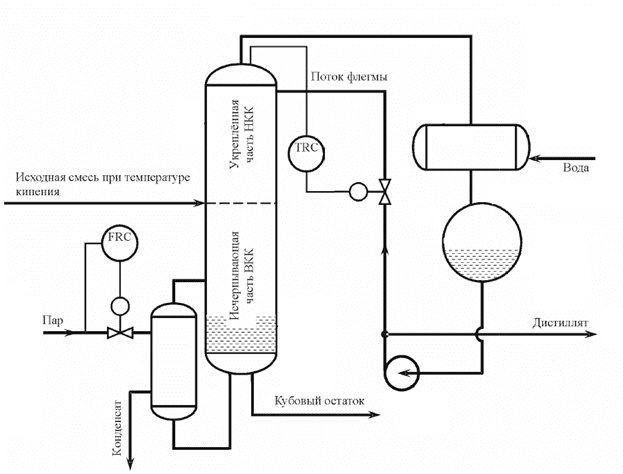
Рисунок 4 – Схема стабилизации процесса ректификации
На рис. 4 осуществляется стабилизация температуры верха колонны и расхода подаваемого в кипятильник пара с помощью локальных одноконтурных систем регулирования. Эти системы связаны между собой через процесс и обеспечивают соблюдение материального и теплового балансов установки[5].
Основной параметр колонны – состав паров вверху колонны. Состав дистиллята регулируют изменением подачи флегмы в колонну. Регулирующий орган устанавливают на линии подачи флегмы в колонну. Согласно правил раздела фаз при разделении бинарной смеси, если давление в колонне постоянно, состав дистиллята и температура верха колонны однозначно связаны. Поэтому в контуре источником информации является температура верха в колонны. Если число тарелок велико, то для улучшения качества регулирования температуру измеряют на так называемой контрольной тарелке, где температура более чувствительна к подаче флегмы и где обеспечивается меньшее запаздывание при изменении состава исходной смеси[6].
Подобная схема из нескольких одноконтурных систем обладает большим запаздыванием и возмущающие воздействия значительно изменяют режим работы объекта[7]. Эти недостатки базовой САУ обуславливают необходимость создания более совершенной системы.
4.2 Описание, оценка преимуществ и недостатков разработанных альтернативных вариантов концепции САУ
Для повышения качества разделения смеси в АСР основных величин вводят корректирующие контуры.
Одна из возможных схем реализации показана на рис.5. Здесь подача флегмы в колонну регулируется трехконтурной системой регулирования. Регулятор состава 1в дает сигнал коррекции на регулятор температуры 1б, а этот, в свою очередь, корректирует задание регулятору расхода 1а[1].

Рисунок 5 – Вариант каскадного регулирования по составу дистиллята
Если кубовый остаток тоже является целевым продуктом, то для обеспечения его чистоты применяют систему регулирования расхода пара в кипятильнике (2а) с коррекцией по температуре в отгонной (исчерпывающей) части колонны (рис.6)[8].
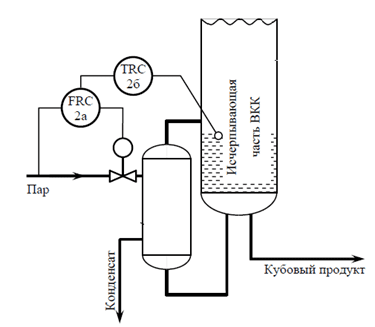
Рисунок 6 – Вариант каскадного регулирования по температуре кубового остатка
Приведенные выше схемы улучшают качество работы, но не способны компенсировать значительные колебания состава и расхода исходной смеси.
При значительном изменении состава исходной смеси в системы регулирования состава дистиллята и кубового остатка вводят дополнительные контура регулирования, обычно коррекцию по составу исходной смеси (рис.7).
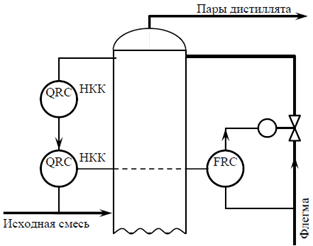
Рисунок 7 – Регулирование расхода флегмы по составу исходной смеси
При отсутствии анализатора состава исходной смеси колебания состава можно компенсировать регулятором соотношения расходов дистиллята и исходной смеси, который является корректирующим для регулятора расхода флегмы (рис.8). Регулятор соотношения получает сигнал коррекции от регулятора состава паров дистиллята[9-12].
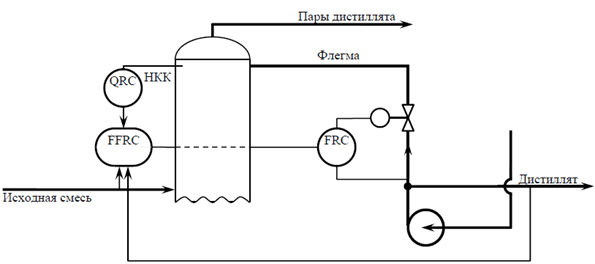
Рисунок 8 – Регулирование с учетом изменения состава исходной смеси
4.3 Обоснование выбора и ожидаемые результаты выбранного варианта концепции САУ
Все приведенные выше варианты реализации регулирования не являются устойчивыми к значительным колебаниям расхода исходной смеси, которые не являются редкостью в условиях реального объекта. Скомпенсировать подобные возмущения позволит введение регулятора соотношения, корректирующего поток флегмы в зависимости от температуры верха колонны и расхода исходной смеси, т.е. двухконтурной системы (рис.9).
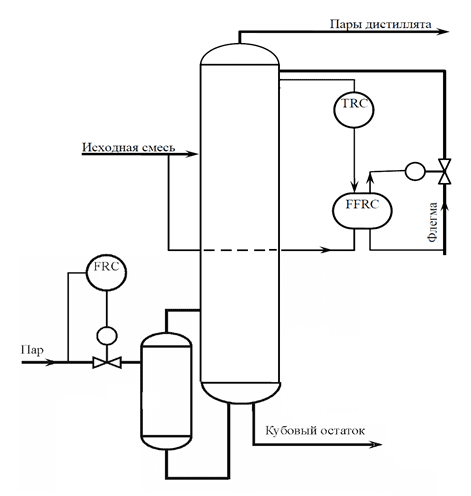
Рисунок 9 – Регулирование с использованием регулятора соотношения с коррекцией по температуре
Задание регулятору соотношения корректируют регулятором температуры дистиллята вверху колонны. При увеличении расхода исходной смеси регулятор соотношения увеличивает расход флегмы и наоборот. Само соотношение расходов корректируется регулятором температуры. Изменение же расхода подаваемого пара оказывает не столь сильное влияние на состав дистиллята и в целом необходимо лишь для поддержания материального баланса в колонне, следовательно, для регулирования подачи пара в кипятильник достаточно использования одноконтурной схемы управления.
Для условий ректификационного цеха наилучшим образом подходит схема регулирования подачи флегмы с применением регулятора соотношения с коррекцией по температуре верха.
5. Синтез математической модели объекта
5.1. Разработка структурной схемы
Выбранная в предыдущем разделе схема управления соответствует следующей структурной схеме (рис.10).
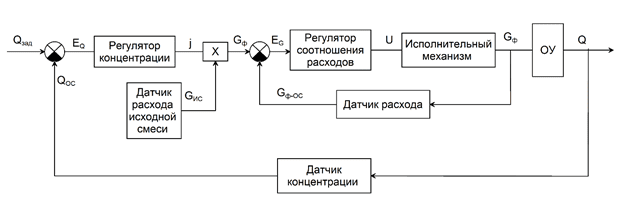
Рисунок 10 – Структурная схема системы
где Qзад – заданное значение концентрации, %;
Qос – значение концентрации с датчика обратной связи, %;
EQ – рассогласование концентраций, %;
j – коэффициент соотношения расходов;
GИС – расход исходной смеси, м3/ч;
Gф – расход флегмы, м3/ч;
EG – рассогласование расходов флегмы, м3/ч;
Gф-ОС – значение расхода флегмы с датчика обратной связи, м3/ч;
U – управляющее воздействие (открытие клапана), %/с;
Q – выходное значение концентрации продукта.
Как видно из схемы, на вход подается требуемое значение концентрации, которую необходимо поддерживать, затем вычисляется рассогласование между заданным значением концентрации и фактической концентрацией, измеряемой специальным датчиком, после чего рассогласование поступает на регулятор концентрации, который вычисляет соотношение расходов флегмы и исходной смеси, способное обеспечить требуемую концентрацию. После того как был вычислен необходимый расход флегмы, он сравнивается с фактическим расходом флегмы на текущий момент, вычисляется рассогласование расхода флегмы и подается на регулятор соотношения расходов, который генерирует управляющее воздействие на исполнительный механизм (клапан).
5.2. Математическая модель объекта
Чтобы смоделировать массообменные процессы внутри колонны, необходимо проанализировать процесс на каждой из тарелок колонны (рис.11). N – количество тарелок, f – номер тарелки питания,Vi – поток пара через i-тую тарелку, Li – поток жидкости, стекающей через i-тую тарелку, Gf, Gd, Gw – объемные расходы питающей смеси, дистиллята и кубового остатка соответственно, xi и yi – содержания низкокипящей фракции в жидкой и паровой фазе соответственно. Распределение вышеперечисленных параметров по тарелкам колонны изображено на рис. 11.
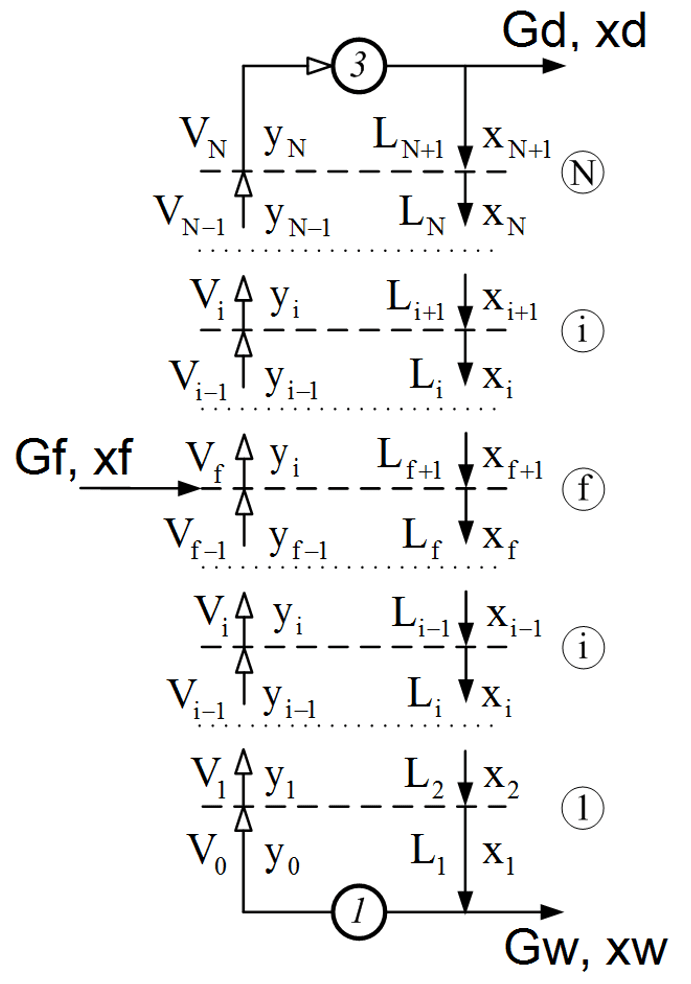
Рисунок 11 – Распределение параметров процесса по тарелкам колонны
Основные уравнения материального баланса в колонне[10-14]:
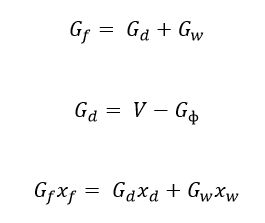
Для построения математической модели примем следующие допущения:
- поток пара в укрепляющей части колонны (выше тарелки питания) постоянен, т.е. Vi = V+Vf, i=(f+1)…N, где V – поток пара, подаваемый в колонну из кипятильника, а Vf – испаренная часть смеси, подаваемой на тарелку питания;
- поток пара в исчерпывающей части колонны (ниже тарелки питания) постоянен, т.е. Vi = V, i=1…f;
- поток жидкости в укрепляющей части колонны (выше тарелки питания) постоянен, т.е. Li = Gф, i=(f+1)…N;
- поток жидкости в исчерпывающей части колонны (ниже тарелки питания) постоянен, т.е. Li = Gф + Lf, i=1…f, где Lf – жидкая часть смеси, подаваемой на тарелку питания.
При принятии вышеизложенных допущений уравнения материального баланса имеют следующий вид:
- для куба колонны (i=0):
где MB – количество вещества в кубе колонны, кмоль.
- для исчерпывающей части колонны (ниже тарелки питания) (i=1...f):
где M – слой вещества на тарелке колонны, кмоль.
- для тарелки питания (i=f):
- для укрепляющей части колонны (выше тарелки питания) (i=f...N):
- для дефлегматора (i=N+1):
где Md – количество вещества в дефлегматоре, кмоль.
Концентрация вещества в газообразном виде на каждой тарелке может быть найдена через уравнение равновесия[15]:
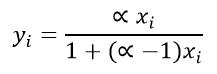
где α – относительная летучесть.
Таким образом, для моделирования колонны с 14 тарелками необходимо составить систему из 16 дифференциальных уравнений первого порядка (по одному уравнению для каждой из тарелок и по уравнению для дефлегматора и куба колонны).
Для выполнения вычислений предполагается использовать пакет прикладных программ Matlab, в частности графическую среду моделирования Simulink.
Выводы
Разработка системы управления технологическим процессом ректификации является не только инженерным вопросом, но и сложной математической задачей, решение которой позволит значительно улучшить качество выходных продуктов процесса и обеспечить независимость этого качества от колебаний входных величин, что, в свою очередь, поднимет эффективность установки, уменьшит финансовые затраты на поддержание процесса, и увеличит стоимость целевого продукта за счет более высокой его концентрации.
Для достижения поставленных целей были решены следующие задачи:
- Был проанализирован технологический процесс ректификации. Управляющим воздействием было принято изменение расхода флегмы, подаваемой в колонну орошением.
- Были проанализированы существующие схемы автоматизации подобными объектами, выявлены их преимущества и недостатки в контексте решаемой задачи и по итогам исследования был сделан вывод, что лучшим выбором для заданных условий будет концепция управления через контроль соотношения расходов флегмы и исходной смеси с коррекцией по температуре верха колонны.
- Была получена математическая модель объекта управления, являющаяся системой из 16 дифференциальных уравнений первого порядка,
Дальнейшие исследования направлены на следующие аспекты:
- Разработка закона управления на основе имеющейся модели.
- Подбор технических элементов для реализации системы управления реальным объектом.
При написании данного реферата магистерская работа еще не завершена. Окончательное завершение: май 2019 года. Полный текст работы и материалы по теме могут быть получены у автора или его руководителя после указанной даты.
Список источников
- Кузьменко Н. В. Учебное пособие для студентов заочной формы обучения по дисциплине «Автоматизация технологических процессов и производств» / Кузьменко Н. В. – Ангарск: АГТА, 2005. – 78 с.
- Дудникова Е. Г. Автоматическое управление в химической промышленности: учебник для вузов / Дудникова Е. Г. – Москва: Химия, 1987. – 111 с.
- Голубятников В. А. Автоматизация технологических процессов в химической промышленности. / Голубятников В. А., В. В. Шувалов – Москва. : Химия. 1985. – 212 с.
- Бондарь А.Г. Математическое моделирование в химической технологии / Бондарь А.Г. – Киев: «Вища школа», 1973. – 274 с.
- Исакович Р.Я. Aвтоматизация производственных процессов нефтяной и газовой промышленности. / Исакович Р.Я., Логинов В.И., Попадько В.Е. – Москва: Недра, 1983. – 324 с.
- Холоднов В.А. Математическое моделирование и оптимизация химико-технологических процессов : практ. руководство. / Холоднов В.А., Дьяконов В.П. – СПб.: Профессионал, 2003. – 312 с.
- Vu Trieu Minh Modeling and Control of Distillation Column in a Petroleum Process / Vu Trieu Minh, Ahmad Majdi Abdul Rani // Mathematical Problems in Engineering. – Tronoh, Malaysia – 2009. – P. 4-5.
- Денисенко В.В. Компьютерное управление технологическим процессом, експериментом, оборудованием. / Денисенко В.В. – М.: Горячая линия – Телеком, 2009. – 608 с.
- Филлипс Ч. Системы управления с обратной связью. / Филлипс Ч., Харбор Р. – М.: Лаборатория Базовых Знаний, 2001. – 616 с.
- Денисенко В. В. ПИД-регуляторы вопросы реализации часть 2/ Денисенко В. В. – СТА. – 2008. – № 1. – С. 86-99.
- Денисенко В. В. ПИД-регуляторы: принципы построения и модификации / Денисенко В. В. – СТА. – 2007. – № 1. – С. 77-88.
- Лукас В. А. Теория автоматического управления: Учебник для вузов – 2-е издание./ Лукас В. А. – М: Недра, 1990. – 416 с.
- Дорф Р. Современные системы управления / Р. Дорф, Р. Бишоп. Пер. с англ Б. И. Копылова. – М.:Лаборатория Базовых Знаний, 2002. – 832 с.
- Перельмутер В.М. Пакеты расширения MATLAB. Control System Toolbox & Robust Control Toolbox / Перельмутер В.М. – М.: СОЛОН-ПРЕСС, 2008. – 224 с.
- Дудников Е. Г. Автоматическое управление в химической промышленности / Дудников Е. Г. – М.: Химия, 1987. – 368 с.