Abstract
Content
- Introduction
- 1. The purpose and objectives of the study
- 2. Analytical review of the approaches of the rational work of the CCM
- References
Introduction
Continuous casting is currently the main method of steel casting, in which slab and graded billets are produced. According to the classic technology of the first half of the twentieth century. steel is poured into molds - high cast-iron tanks. After it hardens, the bars "strip", that is, they remove the molds. The weight of ingots is 5-9 tons, sometimes up to 25 tons. But casting steel into molds has disadvantages.
When cooled, steel crystallizes non-uniformly: small crystals form at the very wall of the mold, large ones form in the depth, and bubbles and shells appear between them. In the upper part of the ingot shrinkage occurs. Therefore, the resulting ingots need additional processing - crimping. The upper part of the ingot has to be cut and returned to remelting. According to literary data in world practice, continuous casting of more than 95% of steel grades has been mastered. However, in the post-Soviet space in a number of enterprises they prefer to cast high-alloy steel grades into a mold, for fear of cracks and other defects in the continuous casting machine.
The quality of continuously cast billets largely depends on the correctness of the choice of technological parameters of the casting process, which must be made taking into account the type of continuous casting machine (CCM), cross-sectional dimensions of the workpiece, steel grade. Experimental determination of rational casting parameters, taking into account the above factors, is a complex, time-consuming and lengthy process. The current state of the theory of continuous casting of steel allows determining the main technological parameters by calculation. The calculation of the technological parameters of continuous casting of steel is always done for a specific continuous casting machine. Therefore, for the calculation it is necessary to take into account the metallurgical length of the machine, the height of the mold, the number and length of sections of the secondary cooling zone, the method of secondary cooling at each site.
1. The purpose and objectives of the study
The purpose of this work is to determine the rational technological parameters of the temperature and speed casting mode for high-quality steel grades on continuous caster. To do this, it is necessary to analyze the methods for selecting rational values of temperature-speed parameters. To carry out the heat engineering calculation of ZVO from the condition of complete solidification of the blanks to a pulling-correct unit. On the basis of the data obtained, perform an economic calculation. Analyze the safety of steel casting on the caster.
2. Analytical review of the approaches of the rational work of the CCM
The process of continuous metal casting ensures the consistent (non-stop) casting of a certain number of ladles supplied from steelmaking units, at the same time, the resulting billet is cut into measured lengths in accordance with the requirements of consumers and then sent to a roll in the corresponding rolling shops. In this case, the yield of a suitable billet is 98.5-99.5% of the mass of spilled liquid steel. Casting steel in a continuous way is carried out on special machines, called continuous casting machines (CCM), which have a specific structural architecture, including a swivel stand for replacing steel casting ladles, a tundish, a mold, zone of secondary cooling of the workpiece, pulling the correct mechanism, etc.[1].
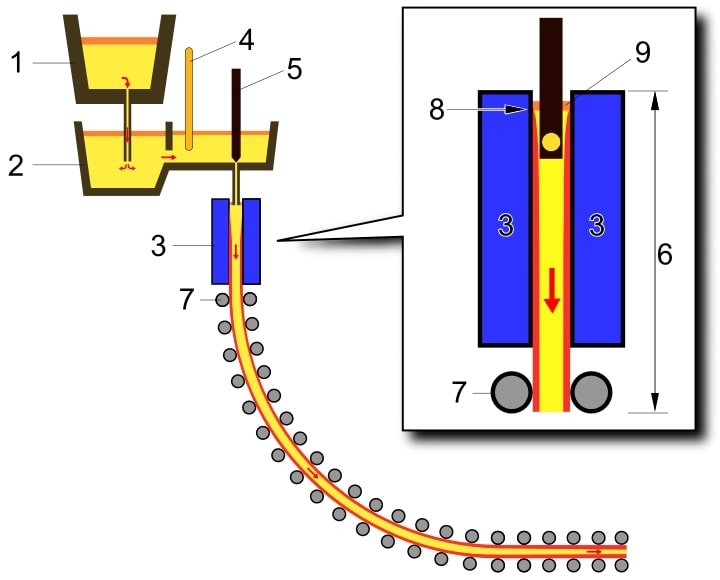
1 - Liquid metal supply bucket; 2 - intermediate bucket; 3 - crystallizer; 4 - Shutter; 5 - Stopper;
6 - Crystallization zone; 7 - Pulling rollers; 8 - the zone of the beginning of crystallization; 9 - Cooling water supply.
The essence of the continuous casting process is that the liquid steel from the steel-teeming ladle enters the tundish, and then into the intensively cooled through-shaped rectangular, square, round or special shaped section - a crystallizer where partial hardening of a continuously extruded ingot occurs and a solid shell is formed, filled with liquid steel in shape and section corresponding to the finished workpiece. Partially hardened billet with the help of a transporting system (pulling stand) enters the secondary cooling zone, where its complete hardening. The resulting ingot is cut to length, cooled and with the help of a roller table or other means of transport is sent to the appropriate rolling mill or warehouse [1].
The main functional elements of the caster include [2]:
• steel casting stand - is designed to place steel casting ladles on it, transfer them from the backup position to the casting position and back, ensure serial casting,
raising and lowering ladles during casting, as well as for continuous weighing of ladles with metal;
• bogie cart - serves to hold it during casting and move from the backup position to the working position;
• tundish - ensures the flow of metal into the mold with a certain flow rate by a well-organized stream, allows you to pour steel into several molds
at the same time, to carry out serial casting using the “smelting to smelting” method when changing the steel-teeming ladles without stopping and reducing the casting speed; tipping bucket is a buffer tank
as it is used to coordinate the flow of metal from the casting ladle into the mold;
• mold - is designed to receive a liquid metal, the formation of an ingot of a given cross-section and its primary cooling (made of copper and cooled in the process of pouring water);
• the mechanism of reciprocating movement of the mold - creates conditions that reduce the likelihood of breakthroughs of the ingot peel at the exit from it,
and also provides full "healing" of the place of a gap which has arisen at the movement of an ingot in a crystallizer;
• secondary cooling zone - allows you to create optimal conditions for the complete solidification of continuously cast ingot, providing
uniform cooling of the workpiece (spraying water with nozzles, maintaining its geometric shape with rollers (preventing buckling) and the required quality of the metal;
• pulling - right machine (TPM) - designed for pulling the cast billet out of the mold, straightening it on radial and curvilinear devices and feeding it to the machine (mechanism) for cutting;
SST provides the seed supply to the mold, keeping it in the mold for the time of sealing gaps, pulling with a continuously cast billet from the mold, separating the seed head from the workpiece, etc .;
• machine (mechanism) for cutting blanks - ensures the separation of continuously cast metal into measured lengths in accordance with the requirements of consumers;
• the seed is intended for the formation of a temporary "bottom" in the mold before the start of casting and subsequent stretching with coupled piece of SST;
• electromagnetic stirring device - allows you to improve the quality of the workpiece.
References
1. Смирнов А.Н. Непрерывная разливка стали: учебник/ А.Н. Смирнов, С.В. Куберский, Е.В. Штепан. – Донецк: ДонНТУ, 2011. – 482с.
2. Бирюков А.Б. Эффективное управление зоной вторичного охлаждения высокоскоростных сортовых МНЛЗ/ А.Б. Бирюков, В.В. Кравцов, И.П.