Content
- Introduction
- 1. Relevance of the topic
- 2. The purpose and objectives of the study, expected results
- 3. Factory method for obtaining coal pitch
- 4. Method for forecasting the quality of coal pitch
- Conclusion
- References
Introduction
Among the products of processing coal tar, coal tar pitch occupies a special place both in terms of production and value.
Coal pitch (57–60% by weight of the total amount of processed resin) Is the residue obtained by distillation of coal tar. It is a solid or plastic body that goes into a liquid state when heated. By its chemical nature, coal tar pitch is a multicomponent mixture of multinuclear hydrocarbons and heterocycles formed not only during the production of coal tar during coking of coal, but also during its processing as a result of thermal polycondensation[1].
The quality of the pitch is evaluated by such indicators as the yield of volatile substances, ash content, softening temperature, [2] , as well as group composition. Soluble in various organic solvents. Table 1 gives some characteristics of these group components [3].
Table 1 – Characteristics of the group composition of the pitch
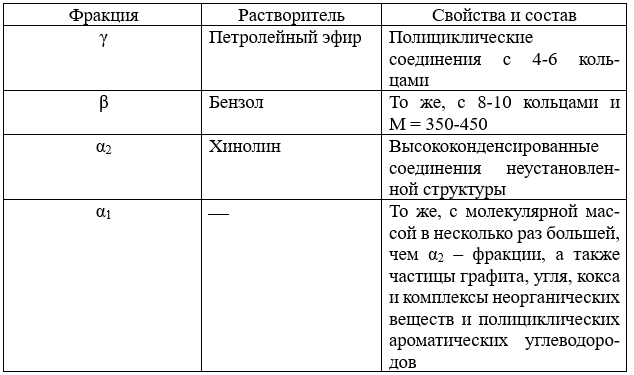
At the moment, pitch is the predominant binder for all types of carbon-graphite materials, electrode products, structural carbon-graphite materials and electro-carbon products [4].
One of the main consumers of this binder is non-ferrous metallurgy (aluminum production) and, in fact, the production of electrodes for various purposes. Thus, aluminum production in Russia accounts for up to 88% of electrode pitch, or up to 52% of consumed pitch (including export, production of pitch coke and blast-furnace refractories) [5].
Exported electrode pitch must meet the requirements of foreign consumer firms, which vary among themselves and contain standards [5] that are often not traditional for the CIS countries.
This work is directed at developing methods for forecasting the quality of coal pitch
1. Relevance of the topic
Currently, the production of our region is faced with factors that make it difficult to obtain high-quality electrode pitch, among which are the following:
• change of technological modes of coking;
• variability in the composition of the feedstock;
• changing market conditions.
Due to the fact that these problems were not previously available and research in this area was not carried out, the creation of a method that allows determining the quality of the pitch in the process of obtaining it is relevant and in demand.
2. The purpose and objectives of the study, expected results
The purpose of th research is the creation of methods of the forecast quality of coal pitch.
Object of study: coal pitch
Subject of research: dynamics of compaction of coal pitch
To achieve this goal, it is necessary to solve the tasks.
Research objectives:
- To develop a method for determining the technological properties of coal pitch;
- With the help of the developed techniques to investigate factory pitch;
- Compare the developed method with the factory method for forecasting pitch quality;
The proposed tasks will be adjusted in the course of the work.
3. Factory method for obtaining coal pitch
Currently, the factories of our region use the technology of producing an electrode binder by thermal oxidation of medium-temperature pitch, obtained by a single evaporation of coal tar in distillation columns. The essence of the method is the heat treatment of medium-temperature pitch at 340–370 °С in cubes—reactors (continuous) with the continuous bubbling of air through the reaction mass. Air oxygen is a factor intensifying the compaction reactions (polycondensation and polymerization), which lead to the necessary changes in the physicochemical properties of the pitch[6].
An increase in temperature or an increase in the duration of heating of the resin leads to the accumulation of high molecular weight products in the resin and pitch. However, at present, the predominance in the raw materials fed to the resin distillation plant for processing is of a low degree of pyrolysis resins (with low values ??of α и α1), which leads to a decrease in the degree of pyrolysis of the raw materials fed to the resin distillation shop.
Upon receipt of electrode pitches from a low-pyrolyzed resin, insignificant mass fractions of primary fractions insoluble in quinoline or in toluene lead to an imbalance of such quality indicators as softening temperature, yield of volatile substances, and the ratio of mass fractions of fractions of group composition.
Under such conditions, the use of thermooxidative technology often makes it incompatible to bring the group composition of the electrode pitch to the required values ??while maintaining at the proper level the remaining quality indicators (primarily, the softening temperature). This is especially true in the production of the most liquid high-temperature pitch brands for electrode products.
4. Method for forecasting the quality of coal pitch
The existing technology under the changed conditions does not allow to obtain pitch with the given values ??of the yield of volatiles (for grade А – 59–63 %, for grade B – 58–62 %), when the heating temperature is increased, the amount of volatile substances increases (depending on the grade of pitch), which negatively affects the final product.
Given the above factors, we have proposed ways to maintain the release of volatile substances at the required level, such as:
• an increase in the residence time of the pitch in the reactors;
• exclusion of air supply to the reaction mass.
Apart from the function of a participant in the thermal oxidation reaction, air sparging through the pitch provides mixing of the heated mass. The interruption of the air supply will inevitably lead to a violation of the temperature regime in the reactor.
The easiest way is proposed to ensure uniform heating of the reaction mass and thereby avoid local overheating of the substance – the use of mechanical agitator (Fig 1.).
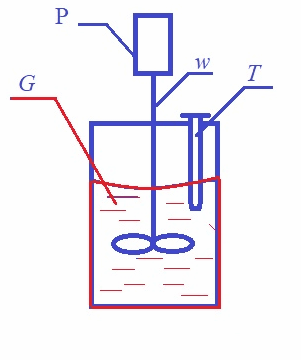
Figure 1 – Stirrer reactor
(animation: 4 frames, 78 kbit)
(G – coal pitch, P – motor, w – stirrer, T – connection point of the thermocouple)
At the moment, this is difficult to do in factory conditions, so we used a laboratory setup (Fig. 2).
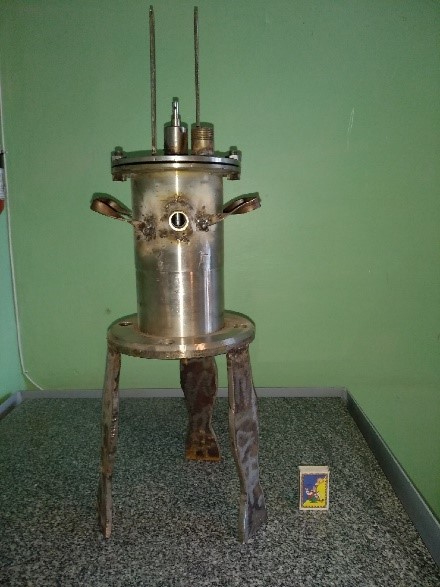
Figure 2 – Laboratory setup
For the experiment , the temperature range of 340–370 °С, was selected, since it is precisely this interval that is maintained in factory reactors. Achieving and maintaining this temperature is carried out using an external heater.
This installation provides measurements of temperature, pressure, sampling.
Conclusion
The obtained experimental and theoretical data can be used to improve the technology for producing coal pitch.
The above data does not is final and will be supplemented during the execution of the graduate work
References
- Кисельков Д. М.,Москалев И. В., Стрельников В. Н. Углеродные материалы на основе каменноугольного сырья:
Вестник Пермского Научного центра
2/2013г C. 13 - ГОСТ 10200–83 Пек каменноугольный электродный. Технические условия
- Макаров Г. Н., Харлампович Г. Д. Химическая технология твердых горючих ископаемых: Учеб. для вузов/Под ред. Г. Н. Макарова и Г. Д. Харламповича. – М.: Химия. 1986. – 335–340 с.
- Кауфман А. А. Технология коксохимического производства: уч. пособ. [для студ. выс. учеб. зав.] / А. А. Кауфман, Г. Д. Харлампович. – Е: ВУХИН, 2005. С. 288.
- Сидоров О. Ф., Селезнев А. Н. Перспективы производства и совершенствования потребительских свойств каменноугольных электродных пеков // Российский химический журнал. 2006. Т. 1, № 1. С. 17–18
- Губанов С. А., Букка А. А.;, Иващенко Е. Ю. Технологические особенности производства каменноугольного пека из низкопиролизованных каменноугольных смол и варианты совершенствования процесса/ С. А. Губанов, А. А. Букка, Е. Ю. Иващенко, В. Х. Мушта, В. А. Вытовтов // науч. тех. журн. Кокс и химия – 2017. – № 11 С. 37–38.