Реферат по теме выпускной работы
Содержание
- Введение
- 1. Актуальность темы
- 2. Цель и задачи исследования
- 3. Обзор исследований и разработок
- 4. Описание модернизированной конструкции шлифовальной головки
- Выводы
- Список источников
Введение
Головной радиопрозрачный антенный обтекатель является важным элементом современных скоростных летальных аппаратов, управляемых методом радиолокационного наведения. Среди элементов летательных аппаратов, геометрические параметры которых определяются аэродинамическими требованиями, распространены детали оживальной формы. Данный тип деталей изготавливают из радиопрозрачных неметаллических материалов, в частности, стекла и ситаллов. При шлифовании деталей оживальной формы кругами с прямолинейной образующей возникает искажение образующей профиля наружной поверхности детали. В отечественных и зарубежных вальцешлифовальных станках широкое распространение при обработке крупногабаритных поверхностей получил метод огибания кругом с профилем в виде дуги окружности. Круги с выпуклой образующей исключают искажение профиля [1].
1. Актуальность темы
В современной промышленности широкое распространение находит изготовление изделий из керамических материалов, благодаря их специфическим свойствам. Эти свойства делают хрупкие неметаллические конструкционные материалы, в частности, ситаллы наиболее пригодными для применения в условиях агрессивных сред океана и космоса, в самолето– и ракетостроении. Из–за высокой твердости материала механическая обработка заготовок возможна лишь абразивным алмазным инструментом. Получение требуемого качества поверхности после механической обработки таких деталей зависит от ряда факторов с учетом того, что одной из важных задач машиностроения является повышение производительности технологических процессов при одновременном снижении их себестоимости [2].
Ситаллы – стеклокристаллические материалы, получаемые путем почти полной стимулированной кристаллизации стекол специального состава. Они занимают промежуточное положение между обычными стеклами и керамикой. Само название ситалл происходит от слов силикат и кристалл; в названии подчеркивается тот факт, что одни из первых стеклокристаллических материалов были получены на основе закристаллизованных силикатных стекол. За рубежом ситаллы называют пирокерамами от греческих слов пирос
– огонь и керамикос
– глиняный. Первая часть названия связана с тем, что стеклокристаллические материалы за рубежом были получены вначале на основе cтекол, содержавших окислы лития, светившиеся при высоких температурах огненным светом, а вторая – с тем, что стеклокристаллические материалы иногда не совсем правильно называли стеклокерамикой.
Содержание кристаллической фазы в ситалле к окончанию процесса кристаллизации достигает 95%, размеры оптимально развитых кристаллов составляют от 0,05 до 1 мкм.Стеклофаза распределена между кристаллами в виде тонких прослоек, скрепляющих сами кристаллы. Изменение размеров изделий при кристаллизации не превышает 1–2%.
Технология получения ситалла состоит из нескольких операций. Сначала изготовляют изделие из стекломассы и подвергают его двухступенчатой термической обработке при температурах 500–700 и 900–1100°С. На первой ступени происходит образование зародышей кристаллизации, а на второй – развитие кристаллических фаз. Содержание кристаллических фаз к окончанию процесса достигает 95%, а размеры кристаллов лежат в пределах от 0,01 до 1 мкм.
Ситаллы – плотные материалы от белого до коричневого цвета, отличающиеся повышенной механической прочностью и химической стойкостью, а также сочетающие высокие диэлектрические и температурные свойства, что позволяет применять их для многих приборов электронной техники, работающих в широком диапазоне частот [3].
К точности и качеству обработанных поверхностей деталей предъявляются высокие требования, так как долговечность машин, работающих с большими скоростями и нагрузками, зависит главным образом от качества поверхности деталей.
В процессе обработки детали на все составляющие элементы ТОС действуют изменяющиеся по величине и направлению статические и динамические силы, вызывающие относительное смещение составных элементов этой системы как за счет выбора неизбежных зазоров в подвижных и неподвижных соединениях, так и за счет упругих деформаций самих элементов и их контактных поверхностей. Величина этих смещений – податливость системы зависит от многих факторов: величины действующих сил, их сочетания по направлениям; качества и степени износа трущихся поверхностей; характера смазки и др. В связи с многообразием действующих факторов определить заранее величину возникающих смещений и компенсировать их с целью увеличения точности оказывается затруднительным.
2. Цель и задачи исследования
Целью работы является проектирование привода поворота, а также разработка системы автоматического управления поворотом шлифовальной бабки.
Объектом исследования является привод поворота шлифовальной бабки .
Предметом исследования является система управление поворотом шлифовальной бабки при формировани точности наружного контура обтекателя из ситалла при алмазном шлифовании.
3. Обзор исследований и разработок
Технологический процесс обработки изделий включает многооперационную обработку шлифованием как наружного, так и внутреннего их контуров на станках типа РТ 66202, оснащенных агрегатной шлифовальной головкой и системой прямого копирования. В статье приведены результаты исследований динамических характеристик ТОС при шлифовании наружной поверхности детали, схема которой представлена на рис. 1.
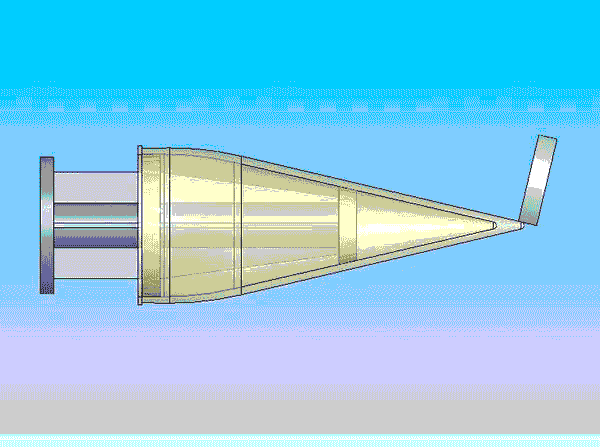
Рисунок 1 – Наружная обработка изделия (анимация: 10 кадров, 10 повторов, 132 килобайт)
Особенности обработки изделий рассматриваемого класса из ситаллов в значительной степени обусловлены следующими факторами. Основные размеры изделия: длина до 1,0 м; максимальный диаметр 450…500 мм; толщина стенки заготовки 20 мм при толщине готового изделия 5 мм. На обработку внутреннего контура изделия затрачивается примерно 18–20 часов машинного времени; обработка наружного контура занимает 6–10 часов при значительной доле ручного труда, применяемого на операции чистовой обработки наружного профиля. Эксплуатационные характеристики изделий предполагают соблюдение повышенных требований по точности и качеству обработки, в частности, обеспечение минимальной глубины дефектности поверхностного слоя, которая определяет продолжительность последующих операций химического травления и упрочнения механически обработанных поверхностей [4].
Для повышения точности механической обработки ситаллового обтекателя необходимо нивелировать факторы влияющие на нее.
Основной причиной образования погрешности на шлифованной поверхности изделия является изменение положения инструмента относительно траектории, заданной формой и профилем детали. Причинами, вызывающими изменение расстояния между заданной и реальной траекториями формообразования, являются вибрации в технологической системе обработки, а также неточности геометрической формы шлифовального круга и погрешность его установки [5].
Рассмотрим факторы, влияющие на точность обработки.
Известно, что при шлифовании
тонкостенных оболочек вращения (схема установки заготовки на станке
представлена на рисунке 2) в зоне контакта заготовки со шлифовальным
кругом возникают изгибные колебания на двух частотах 60±5 Гц
и 123±10 Гц, близких к собственным частотам подсистемы шпиндельный
узел станка – приспособление – заготовка
[6].
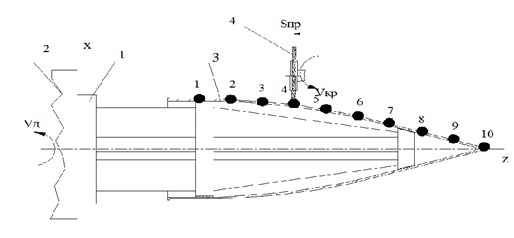
Рисунок 2 – Схема технологической системы при наружном круглом шлифовании заготовки – тонкостенной оболочки вращения из ситалла: 1 – оправка; 2 – шпиндель станка; 3 – обрабатываемая заготовка; 4 – шлифовальный круг 1А1 200х10х3х76 А 315/250–4–М2–01, установленный в агрегатной головке. Точки 1…10 – точки, ограничивающие области изменения параметров рассматриваемой технологической системы
Как показал анализ формирования погрешности обработки наружного контура изделия [7], основная погрешность обработки связана со смещением профилирующей точки на образующей шлифовального круга, при его перемещении вдоль обрабатываемой заготовки. Существующая кинематическая погрешность существенно влияет на точность обработки и может превышать значение динамической в 10 раз.
При увеличении угла поворота оси шлифовального круга (в плоскости оси вращения заготовки и вектора продольной подачи) кинематическая погрешность уменьшается (рис.3), а в случае с изношенным кругом при α=10° полностью исчезает. Однако проблема заключается в невозможности поворота шлифовальной бабки на большие углы (более 5°) из–за опасности касания корпуса бабки и обрабатываемой заготовки [7].
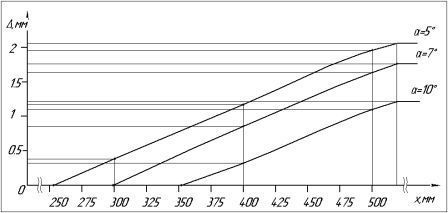
Рисунок 3 – График изменения кинематической погрешности обработки в зависимости от угла поворота оси шлифовального круга [7].
Минимизация погрешностей обработки является важнейшим техническим ограничением при оптимизации процесса шлифования из условий сохранения постоянной формообразующей точки. Для уменьшения кинематической погрешности в течение всего периода обработки данной заготовки можно использовать поворотное устройство, разворачивающее круг при его движении вдоль образующей.
4. Описание модернизированной конструкции шлифовальной головки
С целью получения переменного по длине детали угла поворота шлифовального круга на кафедре махатронных систем машиностроительного оборудования Донецкого национального технического университета была разработана конструкция безлюфтового привода устройства поворота шлифовальной бабки [8]. Привод поворота шлифовальной бабки представляет собой двухступенчатый цилиндрическо–червячный редуктор с двумя подпружиненными червякам. Выходной вал привода – вал червячного колеса – обеспечивает поворот стола с установленной на нем шлифовальной бабкой.
Нами выполнена модернизация безлюфтового привода устройства поворота шлифовальной бабки для более полного использования алмазоносного слоя круга. Шлифовальный круг перенесен на противоположную сторону шпинделя токарного станка, что предотвращает контакт шлифовальной бабки с обрабатываемой заготовкой. Использование такой конструкции шлифовальной головки возможно только в системах с автоматическим управлением, так как в данном случае у оператора станка нет возможности непосредственного визуального наблюдения за процессом обработки. Основным достоинством такой конструкции является возможность осуществления поворота шлифовального круга на необходимый угол из условия обеспечения постоянства формообразующей точки на шлифовальном круге при ее перемещении вдоль контура заготовки, что позволит устранить описанную выше кинематическую погрешность (рис. 4).
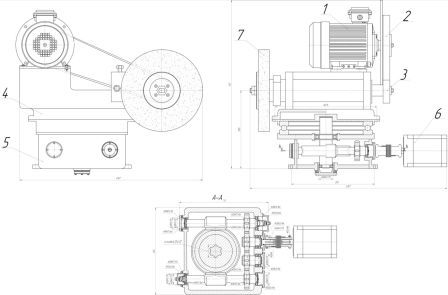
Рисунок 4 – Конструкция модернизированной шлифовальной бабки и поворотного устройства (1 – двигатель привода круга, 2 – ременная передача, 3 – шпиндельный узел, 4 – корпус, 5 – поворотное устройство, 6 – шаговый двигатель привода поворотного устройства, 7 – шлифовальный круг)
В качестве направляющего элемента устройства поворота применен упорный подшипник, что уменьшило влияние момента трения в направляющих на общий момент сопротивления повороту. На основании уточненных исходных данных произведен повторный расчет зубчатых передач редуктора, для минимизации габаритов поворотного устройства. Для выбора двигателя поворотного устройства произведен расчет динамических характеристик привода. Общий момент сопротивления определялся по формуле:
В ходе расчета также определен предельный угол, на который необходимо развернуть шлифовальный круг, используя уравнение параболического участка образующей наружной поверхности обрабатываемой детали:
Дифференцируя уравнение второго участка, получим угол наклона касательной в конечной точке параболического участка
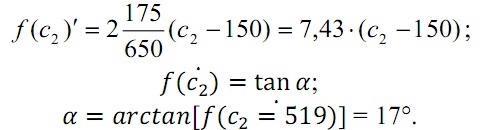
Для обеспечения постоянства контакта образующей шлифовального круга и контура обрабатываемой детали необходимо регулировать угол поворота оси шлифовального круга по всей длине детали. Также определено предельное значение углового ускорения системы (при переходе от конической части к параболической), которое необходимо для расчета динамических характеристик привода:
Значение углового ускорения позволяет определить момент инерции вращающихся элементов конструкции поворотного устройства.
Выводы
Магистерская работа посвящена проектированию и исследованию системы управления для обработки тонкостенных деталей из ситаллов. При написании данного реферата магистерская работа еще не завершена. Окончательное завершение: июнь 2020 года. Полный текст работы и материалы по теме могут быть получены у автора или его руководителя после указанной даты.
Список источников
- Суздальцев Е. И. Радиопрозрачные, высокотермостойкие материалы ХХI века / Е. И. Суздальцев // Огнеупоры и техническая керамика. – 2002. – №3. – С. 42–50.
- Кальченко В. И. Шлифование криволинейных поверхностей крупногабаритных деталей. – М.:Машиностроение, 1979.
- Ситталы и их применение [Электронный ресурс]. Режим доступа: https://studopedia.su/10_156739_sitalli-i-ih-primenenie.html.
- Калафатова Л. П. Прогнозирование качества поверхностного слоя при обработке изделий из технических ситаллов // Приложение №9 к журналу
Инженерный журнал. Справочник
Инженерия поверхности. – М.: Машиностроение. – 2002. – №9. – С.5–8. - Калафатовa Л. П., Гусев В. В., Олейник С. Ю. Исследование динамического состояния технологической системы алмазно–абразивной обработки тонкостенных оболочек из ситаллов // Вісник СевНТУ: зб. наук. пр. Вип. 128/2012. Серія: Машиноприладобудування та транспорт. – Севастополь, 2012 с. 60–67.
- Гусев В. В. Исследование динамических характеристик элементов системы СПИД при шлифовании деталей сложной пространственной формы из ситаллов / В. В. Гусев, Л. П. Калафатова, И. С. Каракуц // Надійність інструменту та оптимізація технологічних систем. Збірник наукових праць. – Краматорск, 2007. – Вип. №21. – С. 148–155.
- Гусев В. В. Влияние кинематической погрешности шлифования на точность обработки антенных обтекателей / В. В. Гусев, Л. П.Калафатова, Д. В. Поколенко//Сучасні технології в машинобудуванні: Зб. наук.праць.
- Быхалов А. Г. Устранение кинематической погрешности обработкипри наружном глубинном алмазном шлифовании антенного обтекателя /А. Г. Быхалов, В. В. Гусев // Інженер. Студентський науково–технічний журнал. – Донецьк: ДонНТУ, 2007. – №8. – С. 34–37.