Реферат за темою випускної роботи
Зміст
- Вступ
- 1. Актуальність теми
- 2. Мета і задачі дослідження
- 3. Огляд досліджень та розробок
- 4. Опис модернізованої конструкції шліфувальної голівки
- Висновки
- Перелік посилань
Вступ
Головний Радіопрозорий антенний обтічник є важливим елементом сучасних швидкісних літальних апаратів, керованих методом радіолокаційного наведення. Серед елементів літальних апаратів, геометричні параметри яких визначаються аеродинамічними вимогами, поширені деталі ожівальной форми. Даний тип деталей виготовляють з радіопрозорих неметалічних матеріалів, зокрема, скла і ситалів. При шліфуванні деталей ожівальной форми колами з прямолінійною твірною виникає спотворення твірної профілю зовнішньої поверхні деталі. У вітчизняних і зарубіжних вальцешліфувальних верстатах широке поширення при обробці великогабаритних поверхонь отримав метод огибания кругом з профілем у вигляді дуги кола. Кола з опуклою утворює виключають спотворення профілю [1].
1. Актуальність теми
У сучасній промисловості широке поширення знаходить виготовлення виробів з керамічних матеріалів, завдяки їх специфічним властивостям. Ці властивості роблять тендітні неметалеві конструкційні матеріали, зокрема, ситалли найбільш придатними для застосування в умовах агресивних середовищ океану і космосу, в літако- і ракетобудуванні.Через високу твердості матеріалу механічна обробка заготовок можлива лише абразивним алмазним інструментом. Отримання необхідної якості поверхні після механічної обробки таких деталей залежить від ряду факторів з урахуванням того, що одним із важливих завдань машинобудування є підвищення продуктивності технологічних процесів при одночасному зниженні їх собівартості [2].
Ситалли – стеклокристаллические матеріали, одержувані шляхом майже повної викликане кристалізації стекол спеціального складу. Вони займають проміжне положення між звичайними стеклами і керамікою. Сама назва ситалл походить від слів силікат і кристал; в назві підкреслюється той факт, що одні з перших стеклокристаллических матеріалів були отримані на основі закристалізуватися силікатних стекол.
За кордоном ситалли називають пірокерамамі від грецьких слів пірос
– вогонь і Керамікос
– глиняний. Перша частина назви пов'язана з тим, що стеклокристаллические матеріали за кордоном були отримані спочатку на основі cтекол, що містили оксиди літію, що світилися при високих температурах вогненним світлом, а друга – з тим, що стеклокристаллические матеріали іноді не зовсім правильно називали склокерамікою.
Зміст кристалічної фази в Сіталл до закінчення процесу кристалізації досягає 95%, розміри оптимально розвинених кристалів складають від 0,05 до 1 мкм. Стеклофаза розподілена між кристалами у вигляді тонких прошарків, що скріплюють самі кристали. Зміна розмірів виробів при кристалізації не перевищує 1–2%.
Технологія отримання ситалла складається з декількох операцій. Спочатку виготовляють виріб з скломаси і піддають його двоступеневої термічної обробки при температурах 500–700 і 900–1100 ° С. На першому місці відбувається утворення зародків кристалізації, а на другий – розвиток кристалічних фаз. Зміст кристалічних фаз до закінчення процесу досягає 95%, а розміри кристалів лежать в межах від 0,01 до 1 мкм.
Ситалли – щільні матеріали від білого до коричневого кольору, що відрізняються підвищеною механічною міцністю і хімічну стійкість, а також поєднують високі діелектричні і температурні властивості, що дозволяє застосовувати їх для багатьох приладів електронної техніки, що працюють в широкому діапазоні частот [3].
До точності і якості оброблених поверхонь деталей пред'являються високі вимоги, так як довговічність машин, що працюють з великими швидкостями і навантаженнями, залежить головним чином від якості поверхні деталей.
В процесі обробки деталі на всі складові елементи ТОС діють змінюються за величиною і напрямком статичні і динамічні сили, що викликають відносне зміщення складових елементів цієї системи як за рахунок вибору неминучих зазорів в рухомих і нерухомих з'єднаннях, так і за рахунок пружних деформацій самих елементів і їх контактних поверхонь. Величина цих зсувів – податливість системи залежить від багатьох чинників: величини діючих сил, їх поєднання за напрямками; якості і ступеня зносу поверхонь, що труться; характеру мастила і ін. В звʼязку з різноманіттям діючих факторів визначити заздалегідь величину виникаючих зсувів і компенсувати їх з метою збільшення точності виявляється скрутним.
2. Мета і задачі дослідження
Метою роботи є проетування приводу повороту, а також розробка системи автоматичного управління поворотом шліфувальної бабки.
Обʼєктом дослідження є привід повороту шліфувальної бабки.
Предметом дослідження є система керування процесом повороту шліфувальної бабки при формуванні точності зовнішнього контуру обтічника з ситалла при алмазному шліфуванні.
3. Огляд досліджень та розробок
Технологічний процес обробки виробів включає багатоопераційної обробку шліфуванням як зовнішнього, так і внутрішнього їх контурів на верстатах типу РТ 66202, оснащених агрегатною шліфувальною головкою і системою прямого копіювання. У статті наведено результати досліджень динамічних характеристик ТОС при шліфуванні зовнішньої поверхні деталі, схема якої представлена на рис. 1
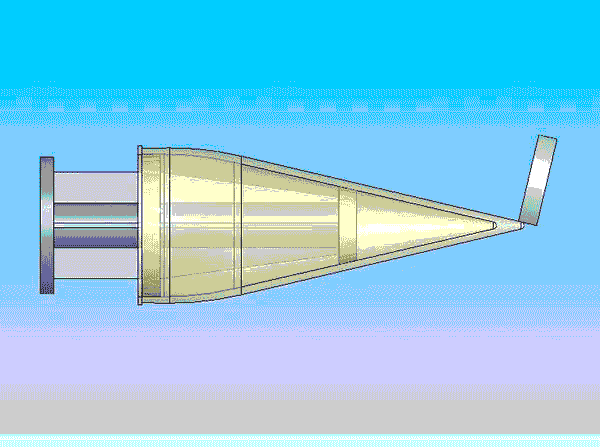
Рисунок 1 – Зовнішня обробка виробу (анімація: 10 кадрів, 10 повторень, 132 кілобайт)
Особливості обробки виробів розглянутого класу з ситалів в значній мірі обумовлені наступними факторами. Основні розміри вироби: довжина до 1,0 м; максимальний діаметр 450…500 мм; товщина стінки заготовки 20 мм при товщині готового виробу 5 мм. На обробку внутрішнього контуру вироби витрачається приблизно 18–20 годин машинного часу; обробка зовнішнього контуру займає 6–10 годин значною мірою ручної праці, що застосовується на операції чистової обробки зовнішнього профілю. Експлуатаційні характеристики виробів припускають дотримання підвищених вимог по точності і якості обробки, зокрема, забезпечення мінімальної глибини дефектності поверхневого шару, яка визначає тривалість наступних операцій хімічного травлення і зміцнення механічно оброблених поверхонь [4].
Для підвищення точності механічної обробки ситаловогообтікача необхідно нівелювати фактори, які впливають на неї.
Основною причиною утворення похибки на шліфованої поверхні виробу є зміна положення в просторі шнструмента щодо траєкторії, заданою формою і профілем деталі. Причинами, що викликають зміну відстані між заданою і реальної траєкторіями формоутворення, є вібрації в технологічній системі обробки, а також неточності геометричної форми шліфувального круга і похибка його установки [5].
Розглянемо фактори, що впливають на точність обробки.
Відомо, що при шліфуванні
тонкостінних оболонок обертання (схема установки заготовки на верстаті
представлена на рисунку 2) в зоні контакту заготовки з шліфувальним
кругом виникають коливання згибу на двох частотах 60 ± 5 Гц
і 123 ± 10 Гц, близьких до власних частот підсистеми шпиндельний
вузол верстата – пристосування – заготовка
[6].
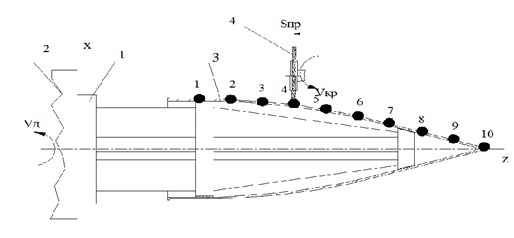
Рисунок 2 – Схема технологічної системи у випадку зовнішнього круглого шліфування заготовки – тонкостінної оболонки обертання з ситалла: 1 – оправлення; 2 – шпиндель верстата; 3 – оброблювана заготовка; 4 – шліфувальний круг 1А1 200х10х3х76 А 315/250 – 4 – М2 – 01, встановлений в агрегатній голівці. Точки 1 … 10 – точки, що обмежують області зміни параметрів даної технологічної системи
Як показав аналіз формування похибки обробки зовнішнього контуру вироби [7], основна похибка обробки пов'язана зі зміщенням профілюючою точки на утворює шліфувального круга, при його переміщенні уздовж оброблюваної заготовки. Існуюча кінематична похибка істотно впливає на точність обробки і може перевищувати значення динамічної в 10 разів.
При збільшенні кута повороту осі шліфувального круга (в площині осі обертання заготовки і вектора повздовжньої подачі) кінематична похибка зменшується (рис.3), а у випадку з зношеним кругом при α=10° повністю зникає. Однак проблема полягає в неможливості повороту шліфувальної бабки на великі кути (більше 5°) Через небезпеку торкання корпусу бабки і оброблюваної заготовки [7].
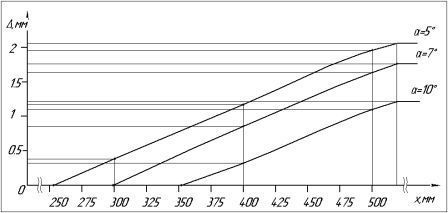
Рисунок 3 – Графік змінення кінематичної похибки обробки в залежності від кута повороту вісі шліфувальної голівки [7].
Мінімізація похибок обробки є найважливішим технічним обмеженням при оптимізації процесу шліфування з умов збереження постійної формотворної точки. Для зменшення кінематичної похибки протягом всього періоду обробки даної заготовки можна використовувати поворотний пристрій, розгортаються коло при його русі вздовж твірної.
4. Опис модернізованої шліфувальної голівки
З метою отримання змінного по довжині деталі кута повороту шліфувального круга на кафедрі махатронних систем машинобудівного обладнання Донецького національного технічного університету була розроблена конструкція безлюфтового приводу пристрою повороту шліфувальної бабки [8]. Привід повороту шліфувальної бабки являє собою двоступеневий циліндрично–черв'ячний редуктор з двома пружними черв'якам. Вихідний вал приводу – вал черв'ячного колеса – забезпечує поворот столу з встановленої на ньому шліфувальною бабкою.
Нами виконано модернізацію безлюфтового приводу пристрою повороту шліфувальної бабки для більш повного використання алмазоносного шару круга. Шліфувальний круг перенесений на протилежну сторону шпинделя токарного верстата, що запобігає контакт шліфувальної бабки з оброблюваної заготівлею. Використання такої конструкції шліфувальної головки можливо тільки в системах з автоматичним управлінням, так як в даному випадку у оператора верстата немає можливості безпосереднього візуального спостереження за процесом обробки.Основною перевагою такої конструкції є можливість здійснення повороту шліфувального круга на необхідний кут з умови забезпечення сталості формотворною точки на шліфувальному колі при її переміщенні уздовж контуру заготовки, що дозволить усунути описану вище кінематичну похибка (рис. 4).
p>
center>
Рисунок 4 – Конструкція модернізованої шліфувальної бабки і поворотного пристрою (1 – двигун приводу кола, 2 – ремінна передача, 3 – шпиндельний вузол, 4 – корпус, 5 – поворотний пристрій, 6 – кроковий двигун приводу поворотного пристрою, 7 – шліфувальний круг)
В якості направляючого елемента пристрою повороту застосований завзятий підшипник, що зменшило вплив моменту тертя в напрямних на загальний момент опору повороту. На підставі уточнених вихідних даних проведений повторний розрахунок зубчастих передач редуктора, для мінімізації габаритів поворотного пристрою. Для вибору двигуна поворотного пристрою зроблений розрахунок динамічних характеристик приводу. Загальний момент опору визначався за формулою:
де Mj – момент інерції обертових елементів шліфувальної бабки;; Mтр – момент тертя в напрямних; MF – момент від дії сили різання.
,В ході розрахунку також визначено граничний кут, на який необхідно розгорнути шліфувальний круг, використовуючи рівняння параболічного ділянки утворює зовнішній поверхні оброблюваної деталі:
Диференціюючи рівняння другого ділянки, отримаємо кут нахилу дотичній в кінцевій точці параболічного ділянки
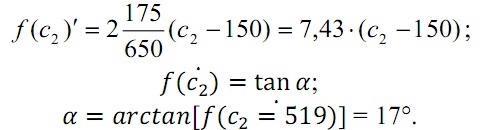
Для забезпечення сталості контакту утворює шліфувального круга і контуру оброблюваної деталі необхідно регулювати кут повороту осі шліфувального круга по всій довжині деталі. Також визначено граничне значення кутового прискорення системи (при переході від конічної частини до параболічної), яке необхідно для розрахунку динамічних характеристик приводу:
Значення кутового прискорення дозволяє визначити момент інерції обертових елементів конструкції поворотного пристрою.
Висновки
Магістерська робота присвячена проектуванню і дослідженню системи управління для обробки тонкостінних деталей з ситалів. При написанні даного реферату магістерська робота ще не завершена. Остаточне завершення: червень 2020 року. Повний текст роботи та матеріали по темі можуть бути отримані у автора або його керівника після зазначеної дати.
Перелік посилань
- Суздальцев Е. И. Радиопрозрачные, высокотермостойкие материалы ХХI века / Е. И. Суздальцев // Огнеупоры и техническая керамика. – 2002. – №3. – С. 42–50.
- Кальченко В. И. Шлифование криволинейных поверхностей крупногабаритных деталей. – М.:Машиностроение, 1979.
- Ситталы и их применение [Электронный ресурс]. Режим доступа: https://studopedia.su/10_156739_sitalli-i-ih-primenenie.html.
- Калафатова Л. П. Прогнозирование качества поверхностного слоя при обработке изделий из технических ситаллов // Приложение №9 к журналу
Инженерный журнал. Справочник
Инженерия поверхности. – М.: Машиностроение. – 2002. – №9. – С.5–8. - Калафатовa Л. П., Гусев В. В., Олейник С. Ю. Исследование динамического состояния технологической системы алмазно–абразивной обработки тонкостенных оболочек из ситаллов // Вісник СевНТУ: зб. наук. пр. Вип. 128/2012. Серія: Машиноприладобудування та транспорт. – Севастополь, 2012 с. 60–67.
- Гусев В. В. Исследование динамических характеристик элементов системы СПИД при шлифовании деталей сложной пространственной формы из ситаллов / В. В. Гусев, Л. П. Калафатова, И. С. Каракуц // Надійність інструменту та оптимізація технологічних систем. Збірник наукових праць. – Краматорск, 2007. – Вип. №21. – С. 148–155.
- Гусев В. В. Влияние кинематической погрешности шлифования на точность обработки антенных обтекателей / В. В. Гусев, Л. П.Калафатова, Д. В. Поколенко//Сучасні технології в машинобудуванні: Зб. наук.праць.
- Быхалов А. Г. Устранение кинематической погрешности обработкипри наружном глубинном алмазном шлифовании антенного обтекателя /А. Г. Быхалов, В. В. Гусев // Інженер. Студентський науково–технічний журнал. – Донецьк: ДонНТУ, 2007. – №8. – С. 34–37.