Abstract
This master's work is not completed yet. Final completion: June 2017. Full text of the work and materials on the topic can be obtained from the author or his adviser after that date.
Content
- Relevance of the topic
- 1. Goal and tasks of the research
- 2. Analysis of the modern state of the research question
- 3. Review of researches and development
- 4. Methods and principles of applying functionally–oriented coatings on internal cylindrical surfaces of details of cars
- 5. Surface preparation details for application of plasma flows
- Conclusions
- The list of sources
Relevance of the topic
Modern machine–building industry pays great attention to issues of reliability, efficiency and resources of the machines. Their solution requires the use of materials able to work in various aggressive environments, high temperatures and pressures, high vibrations at variable contact, percussions, static loads, etc.
Improving the quality of products is one of the main factors of competitiveness. Many performance parameters of the product are basically determined by the condition of the surface layer of the material of which it is made. Therefore, the use of scarce and expensive construction materials in the entire volume is impractical. Economically justified the use in the manufacture of machinery use of materials with special coatings that provide the desired combination of properties. For these purposes, it is enough widely used methods of vacuum ion–plasma sputtering [1].
1. Goal and tasks of the research
The aim of this work is the extension of functionality of engineering products by increasing the operational capacity of goods and maximize their adaptation in the manufacture to the operating conditions through the implementation of a special vacuum ion–plasma coatings on internal cylindrical surfaces.
According to a goal the following tasks are defined:
- To make the analysis of a current state of research of processes of drawing vacuum ion–plasma coverings.
- To develop the general classification of vacuum ion–plasma coverings of internal cylindrical surfaces of products of mechanical engineering.
- To give classification of details with internal cylindrical surfaces.
2. Analysis of the modern state of the research question
With the development of scientific and technical progress continuously increase the demands on the machinery. This is due to the fact that the operating parameters of modern machines and mechanisms is constantly increasing, increase of their technical and technological capabilities, as well as expanding the functional structure of the equipment. The trend of reduction of overall dimensions of machine elements and subsystems, continuously increasing their structural and functional compactness while seeking to create an engine with a qualitatively new set of properties and a measure of utility. To achieve this, at present, widely used modern technology manufacturing machines, mechanisms and their elements. Such technologies include the processes of deposition of vacuum ion–plasma coatings to engineering products that contribute to significant increase of technical and economic parameters of the machine during operation [2,3].
3. Review of researches and development
In accordance with the tasks in the work carried out to develop a common classification of vacuum ion–plasma coatings of internal cylindrical surfaces of products, presented in figure 1. This classification is made in the form of three specific groups of coatings of the inner cylindrical surfaces of products, namely traditional coatings, functionally–oriented coatings and combined coatings. While each of these groups can be by a single layer or multilayer coatings.
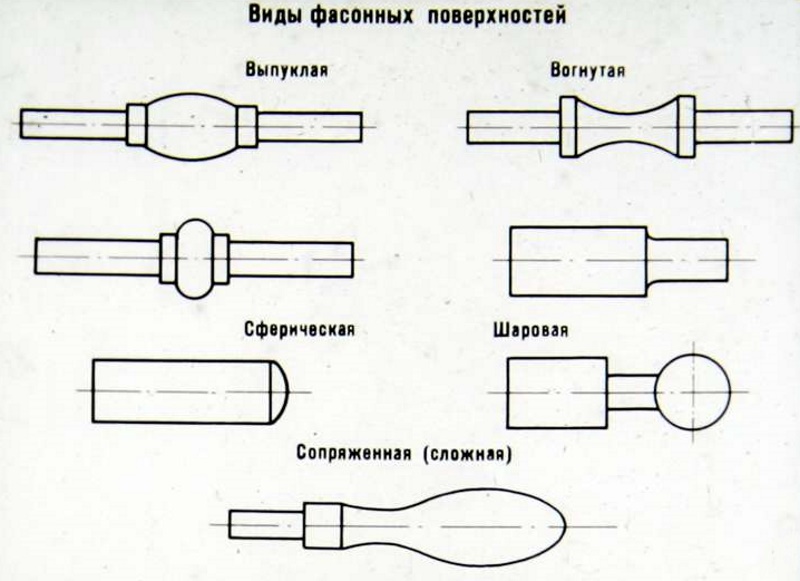
Classification of traditional vacuum ion–plasma coverings is characterized by many parameters, and carried out in the form of single–layer or multilayered coverings.
The analysis of this group of coverings of internal cylindrical surfaces of products shows that it is a multiple set of coverings, various on characteristics. These coverings can widely be used for coverings of internal cylindrical surfaces of products depending on functional features of operation of knot in the car.
Function–oriented coverings of products of mechanical engineering are special coverings of its surfaces and/or their separate zones one or a set of various coverings varied by the form, to type, option, quality and technology of drawing which functionally correspond to conditions of their operation in each separate zone of a product [4,5,6].
This group of coatings internal cylindrical surfaces of articles has main features, which are characterized by the following parameters: a qualitatively new set of properties, qualitatively new measure of usefulness, and maximizing performance potential, and other properties. Main types of functionally–oriented coatings are determined by varying parameters of coating the inner cylindrical surfaces of articles. Thus, depending on the varied parameters can be many different types of these coatings, namely: traditional, spotted, zoned, modular, gradient, smoothly — dependent and other types. These types of coatings are determined by the following parameters: number of layers, thickness of each layer, thickness of the spots or zones in each layer, the coating material of each layer and other parameters.
4. Methods and principles of applying functionally–oriented coatings on internal cylindrical surfaces of details of cars
Considering features of wear of various internal cylindrical surfaces, it is possible to establish that perspective approach to development of technology of drawing coverings are function–oriented technologies.
Functionally–oriented technologies of product manufacturing engineering is a special technology, which is based on accurate topologically oriented implementation of many algorithms the impact of technological instruments and means of the processing in necessary micro, macro areas and parts of the product, which functionally correspond to the operating conditions in each individual area. The use of functionally–oriented technologies for engineering allows you to maximize their overall operational parameters at the expense of increasing local technical capabilities and properties of individual elements, surfaces and/or zones of a product depending on the functional local features of their operation. The engineering products manufactured by the proposed technology, the most adapted in its properties to the characteristics of their operation and show their full potential in the car. It should be noted that the proposed new class of technologies complicates the process of manufacturing products, but in General provides a qualitatively new set of properties and the utility value of engineering products in operation.This gives the possibility to significantly improve technical and economic indicators of operation and use of machines and technical systems [8].
The main features of functionally–oriented technologies is that the technological impact of the tools of processing of the product and the process ensure the specified and desired properties of the products made at the following levels: at the level of the entire product as a whole; at the level of plots; at the level of components; at the level of zones; at the level of macrosun; on the micro level; at the level of nanoson.
Thus, exploring a number of functions that perform internal cylindrical surface, you can break them into several zones. Development takes place depending on the effects of non–uniform length apertures surface. The breaking occurs, depending on effects along the length of the uneven surface of the hole. Therefore requires an individual approach to each area to which it applies the functional–oriented technology. To improve performance it is possible to use the principle of concentration and intensification of treatment regimens and reduce the auxiliary time.
5. Surface preparation details for application of plasma flows
The dimensions of parts to be reduced by the amount of the deposited coating selected. The area of the device surface to be coated must have smooth transitions to the adjacent surfaces or the corresponding configuration. Coverings should be applied on grooves and deaf openings at the relation of width or diameter of an opening to its depth not less than 2 mm.
The degree of cleaning of surfaces from contamination largely determines the quality of the deposited coatings. The presence of surface dirt, oxide films, oils decreases the strength of adhesion of the coating to the metal parts and it can cause incorrigible marriage. Particular attention is paid recoverable parts with soil contamination, residues of fuel and lubricants, corrosion products, and others. Cleaning is performed in different ways: mechanical, jetting, immersion, circulation, combined and etc [10].
In the preparation of the surface is degreased by organic solvents, detergent compounds, alkaline solutions and emulsions according to GOST 9–402–80, then washed with water. After that, parts are dried in a drying Cabinet at a temperature of 60–150 °C, or blowing compressed air.
In some cases, apply degreasing with cleaning material dampened with alcohol or gasoline, in compliance with the relevant rules, industrial sanitation and fire safety. Details having deep grooves, the oil passages, and other places difficult to remove impurities other than degreasing the surface is subjected to heating in an oven at 220–340 ° C for 2–3 hours to burn oil.
In the preparation of the surface should consider the following [12]:
- which adhesion strength of the coating can be achieved by this method of surface preparation;
- what is the hardness of the surface of the workpiece;
- what is the thickness of the hole can be sprayed;
- which method will be most economical.
Conclusions
Function–oriented technologies are perspective for many scopes of application, including for internal cylindrical surfaces of details of cars. The main feature of this approach — the best adaptation of a product to service conditions. This, in turn, significantly increases the service life of parts, as decreases and becomes uniform wear process, and as a result, productivity increases.
The list of sources
- Барвинок В.А. — Управление напряжённым состоянием и свойства плазменных покрытий. — М.: Машиностроение, 1990. — 384 с.: ил.
- Машиностроение. Энциклопедия. / Ред. совет: К.В.Фролов (пред.) и др. — М.: Машиностроение. Технологии, оборудование и системы управления в электронном машиностроении. Т. III — 8/Ю.В. Панфилов, Л.К. Ковалев, В.А. Блохин и др.; Под общ. ред. Ю.В. Панфилова. 2000. — 744 с.
- Нанесение износостойких покрытий на быстрорежущий инструмент / Ю.Н. Внуков, А.А. Марков, Л.В. Лаврова, Н.Ю. Бердышев. — К.: Тэхника, 1992. — 143 с.
- Михайлов А.Н., Михайлов В.А., Михайлова Е.А. Методика и основные принципы синтеза функционально–ориентированных вакуумных ионно–плазменных покрытий изделий машиностроения. // Упрочняющие технологии и покрытия. — М.: Машиностроение. №7. 2005. С. 3–9.
- Mikhaylov A., Mikhaylov V., Mikhaylova E. Bases of synthesis of special functionally–oriented vacuum covers of workpieces of mechanical engineering. // Jhe 31 Internationaly Attendeol Scientitic Conference of the Military Technical Academy “Modern Technologits in the 21 th Century”. — Bucharest: MTA, 2005. P.127–131.
- Михайлов А.Н., Михайлов В.А., Михайлова Е.А. Основы синтеза нового класса вакуумных ионно–плазменных покрытий изделий машиностроения // Conferinta Stiintifica Internationala Iasi–Chisinau: Tehnologii Moderne. Calitate. Restructurari. TMCR 2005. Chisinau, 2005. Vol. 2. P. 327–331.
- The website with the description of ion–plasma technological devices and technology of deposition of functional coatings on hard to access, internal surfaces http://www.itm.dp.ua/RUS/Technol/Tech00010.html.
- Михайлов А.Н. Основы синтеза функционально–ориентированных технологий. — Донецк: ДонНТУ, 2009. — 346 с.
- Михайлов А.Н. Общие особенности функционально–ориентированных технологий и принципы ориентации их технологических воздействий и свойств изделий. // Машиностроение и техносфера XXI века. Сборник трудов XIV международной научно–технической конференции в г. Севастополе 17–22 сентября 2007 г. В 5–ти томах. — Донецк: ДонНТУ, 2007. Т. 3. С. 38–52.
- Лащенко Г.И. — Плазменное упрочнение и напыление. — К.: "Екотехнологія" 2003. — 64 с.
- Metal Coat Technologyhttp://www.mctse.ru/index.php/faq/37-q-podgotovka-k-napyleniyu.
- Open Library — открытая библиотека учебной информации http://oplib.ru/random/view/774043.