Реферат за темою випускної роботи
Реферат носить попередній характер, оскільки час його складання — березень–квітень 2016 року, тоді як захист магістерської дисертації запланована на червень 2017 р.
Зміст
- Актуальність теми
- 1. Мета і задачі дослідження
- 2. Аналіз сучасного стану питання дослідження
- 3. Огляд досліджень і розробок
- 3.1 Аналіз особливостей токарного оброблення фасонних поверхонь деталей машин
- 3.2 Класифікація деталей з внутрішніми циліндричними поверхнями. Галузь застосування
- 3.3 Схема пристрою для нанесення покриттів на внутрішні циліндричні поверхні виробів
- 4. Загальний підхід і методика підвищення ефективності обробки фасонних поверхонь деталей
- 5. Підготовка поверхні деталей до нанесення плазмових потоків
- Висновки
- Перелік посилань
Актуальність теми
Фасонні деталі, поверхні яких сформовані криволінійної котра утворює, досить широко використовуються в різних машинах і механізмах. Механічна обробка таких поверхонь досить скрутна і забезпечується складною кінематикою руху ріжучого інструменту щодо оброблюваної заготовки, а також характеризується змінними значеннями технологічних факторів, що визначають умови обробки.[1].
Процес токарної обробки фасонної поверхні істотно відрізняється від обробки циліндричної поверхні, т. К. Має яскраво виражений змінний характер. Це обумовлено зміною ряду геометричних параметрів процесу різання: траєкторія формотворного руху, безперервно змінюється напрямок подачі, зміна миттєвих значень ширини і товщини зрізу, зміна кінематичних кутів в плані, кінематичних переднього і заднього кутів. Як результат, спостерігається зміна сил і температур різання, шорсткості вздовж котра утворює фасонної поверхні, що в свою чергу Впливає на вибір режимів різання — швидкості, подачі.
Важливим фактором підвищення ефективності обробки фасонних поверхонь є обгрунтування раціональних умов її виконання. У зв'язку з цим дуже актуальні дослідження з оптимізації режимів різання, що забезпечують для заданих умов обробки і вимог до якості оброблених поверхонь максимальну продуктивність і мінімальну собівартість, що визначає підвищення рентабельності машинобудівного виробництва.
Перспективним варіантом вирішення проблеми підвищення ефективності токарної обробки фасонних деталей є використання сучасного твердосплавного інструменту з функціонально-орієнтованими покриттями особливої ??структури, що дозволяє максимально підвищити їх загальні експлуатаційні властивості за рахунок місцевого збільшення характеристик окремих елементів, поверхонь і / або зон вироби в залежності від функціональних місцевих особливостей їх експлуатації.
1. Мета і задачі дослідження
Метою роботи є підвищення продуктивності і зниження собівартості токарного оброблення фасонних деталей при заданому рівні якості поверхні в умовах змінності параметрів процесу різання на основі комплексного забезпечення оптимальних режимів обробки і застосування твердосплавного інструменту з функціональнооріентірованнимі властивостями.
Відповідно до поставленої мети визначені наступні задачі:
- Виконати аналіз особливостей і способів технологічного забезпечення ефективності та якості обробки фасонних поверхонь деталей машин.
- Розробити принципи і методику підвищення ефективності токарної обробки фасонних поверхонь в умовах змінності параметрів процесу різання.
- Встановити закономірності формування і зв'язку шорсткості поверхні, силових і температурних характеристик процесу різання з урахуванням мінливих геометричних параметрів і параметрів зрізу в процесі обробки.
- Дослідити особливості застосування функціонально-орієнтованого підходу для забезпечення функціональних властивостей твердосплавного інструменту і обгрунтувати вибір матеріалу і структури зносостійких покриттів.
2. Аналіз сучасного стану питання дослідження
З розвитком науково–технічного прогресу безперервно підвищуються вимоги до виробів машинобудування. Це пов'язано з тим, що експлуатаційні параметри сучасних машин і механізмів постійно зростають, збільшуються їх технічні і технологічні можливості, а також розширюється функціональна структура обладнання. При цьому спостерігається тенденція зменшення габаритних розмірів елементів машин і їх підсистем, безперервно зростає їх структурна і функціональна компактність при одночасному прагненні створення машин з якісно новою сукупністю властивостей і мірою корисності. Для досягнення цього в даний час широко використовуються сучасні технології виготовлення машин, їх механізмів і елементів. До подібних технологій відносяться процеси нанесення вакуумних іонно–плазмових покриттів на вироби машинобудування, які сприяють суттєвому підвищенню техніко–економічних параметрів машин при експлуатації [2,3].
3. Огляд досліджень і розробок
3.1 Анализ особенностей токарной обработки фасонных поверхностей деталей машинй
Під деталями складної форми маються на увазі деталі, що включають складні поверхні. Складною або фасонної називається поверхню, спеціально відрізняється за формою від циліндричної або плоскій поверхні. Оброблювані поверхні деталей відносять до фасонним, якщо вони утворені криволінійної котра утворює, комбінацією прямолінійних створюючих, розташованих під різними кутами до осі деталі, або комбінацією криволінійних і прямолінійних утворюють. Фасонні поверхні, що входять в конструкцію деталей складної форми прийнято ділити на основні групи(Рисунок 1.1).
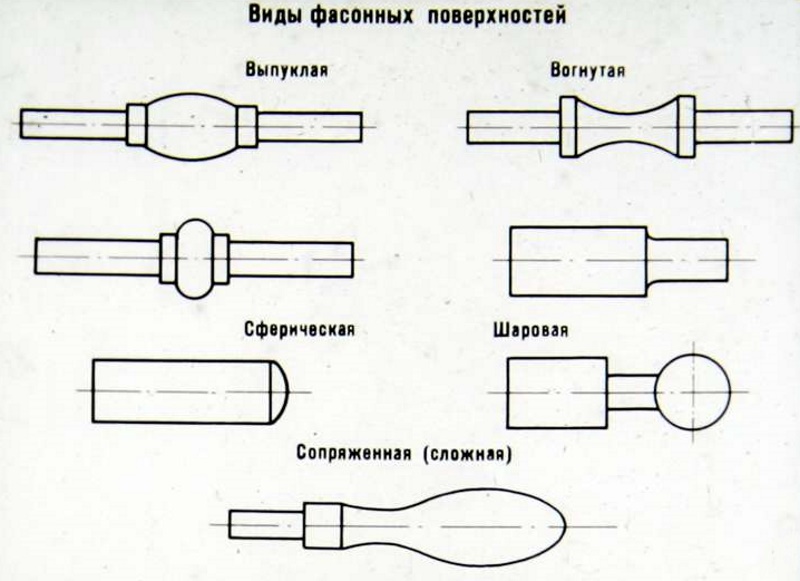
Як представники даної групи деталей обрані ролики прокатного обладнання, направляючі і задають рух заготовок і прокату (рисунок 1.2), що використовуються в вступних роликових проводках дрібносортних і дротяних станів. Деталі експлуатуються в досить важких умовах і потребують регулярної заміни через знос робочих поверхонь.
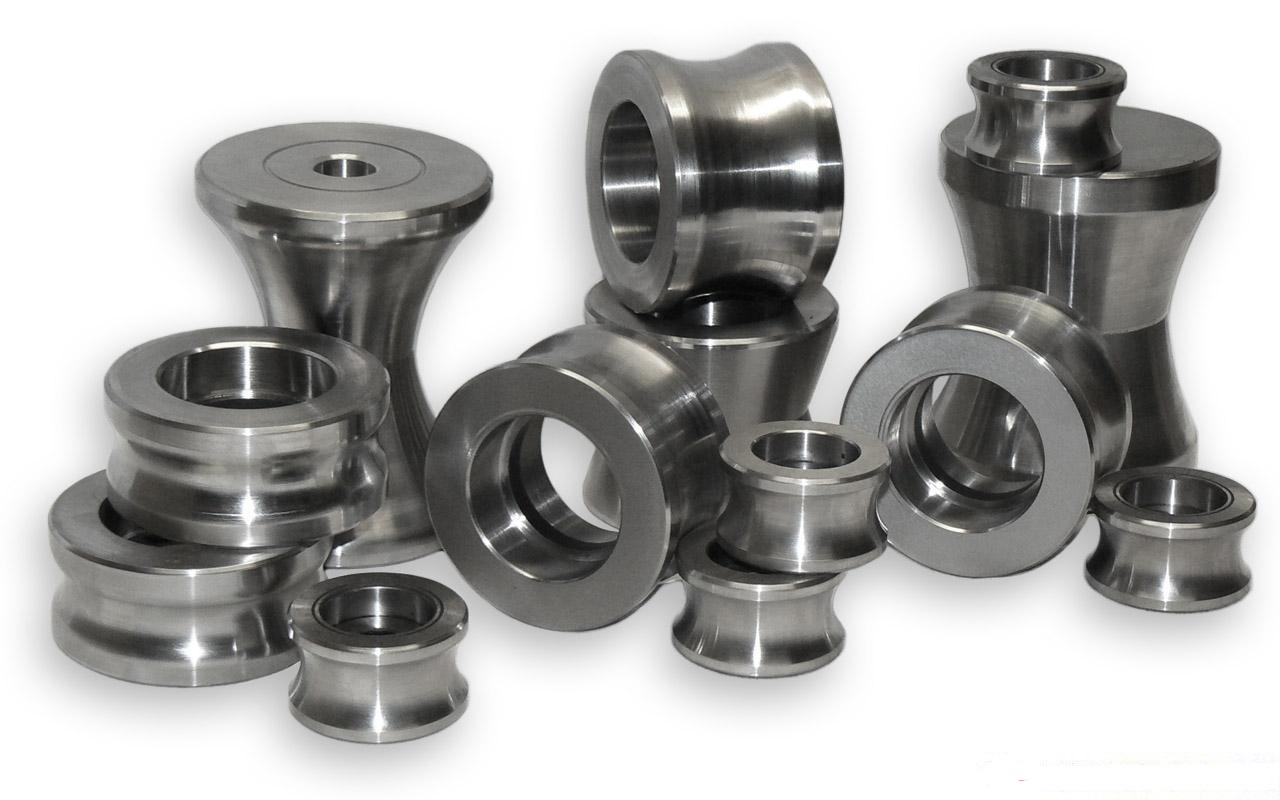
Точність виготовлення роликів, напрямних і задають рух заготовок і прокату в прокатної кліті відповідає 7-8 квалітету. При цьому раціональний вибір матеріалу в поєднанні з високою точністю виготовлення і відповідної термічною обробкою забезпечують їх високу зносостійкість при експлуатації.
Для эффективного управления процессом обработки в этом случае целесообразно выполнять на основе методик, учитывающих весь комплекс переменных параметров процесса и их взаимосвязь. Под качеством продукции понимают совокупность свойств в мере полезности продукции, удовлетворяющих определенным общественным и личным потребностям в соответствии с её назначением. Улучшение качества – важное условие повышения эффективности производства.
3.2 Класифікація деталей з внутрішніми циліндричними поверхнями. Галузь застосування
Внутрішні циліндричні поверхні (отвори) зустрічаються у більшості деталей машин, механізмів, елементів, як тіл обертання, так і не тіл обертання. До таких деталей можна віднести тіла обертання типу коліс, дисків, шківів, блоків, стержнів, втулок, стаканів, колонок, валів, осей, штоків, тіла обертання з елементами зубчастого зачеплення, а також труби, сегменти, не тіла обертання : корпусні, опорні, ємнісні та ін.
![]() |
Внутрішні циліндричні поверхні застосовуються для сполучення деталей один з одним, для підведення мастила або охолоджувальної рідини. Вони діляться на наскрізні і глухі. Перші оброблені на прохід, другі — на певну глибину. За формою поверхонь циліндричні отвори бувають гладкі, ступінчасті, що складаються з ділянок різних діаметрів розташовані на одній осі послідовно одне за іншим, і з канавками, а також з різьбленням. Отвори, довжина яких перевищує 5–6 діаметрів, називають глибокими. Технологічні процеси нанесення вакуумних іонно–плазмових покриттів на внутрішніх циліндричних поверхнях застосовуються в гідроциліндрах посадочних пристроїв (шасі) літаків, гідроагрегатах авіаційної техніки, в гірничо–шахтному і бурильному обладнанні, в машинах і пристроях широкого призначення для підвищення експлуатаційної довговічності пар тертя відповідальних вузлів машин, працюючих в умовах підвищеного корозійного і механічного зносу [7]. |
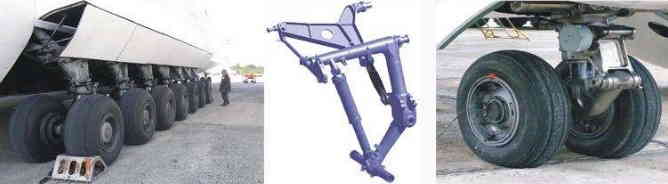
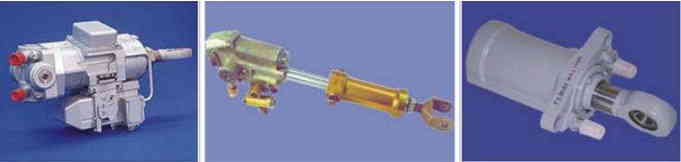
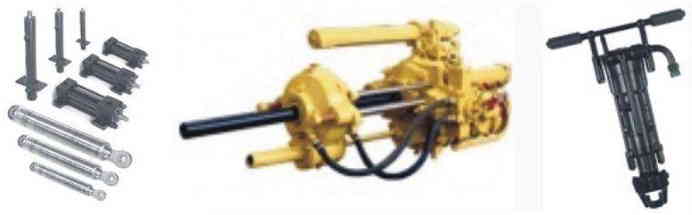
Різноманіття виробів машинобудування та їх елементів вимагає більш глибокого вивчення питань нанесення покриттів в важкодоступні місця. До таких виробів можна віднести деталі з внутрішніми циліндричними поверхнями. Разом з тим процеси нанесення вакуумних іонно–плазмових покриттів вимагають спеціального вивчення. На рис.4 показана схема вузла, що має внутрішню циліндричну поверхню, який складається з двох елементів, а саме вала 1, що обертається відносно направляючої втулки 2. Для підвищення властивостей цього вузла на внутрішню поверхню направляючої втулки нанесено покриття 3. Це дає можливість підвищити експлуатаційні параметри цього вузла. Тут на рис.1,а показаний загальний вигляд вузла, на рис.1,б — перетин елементу вузла. |
![]() |
3.3 Схема пристрою для нанесення покриттів на внутрішні циліндричні поверхні виробів
Для виконання процесу нанесення вакуумних іонно–плазмових покриттів на внутрішні циліндричні поверхні виробів розроблено спеціальний пристрій. На рис.5 показана принципова схема пристрою для нанесення покриттів на внутрішні циліндричні поверхні виробів, яка реалізує принципово кінематичну схему 1–го класу рухів.
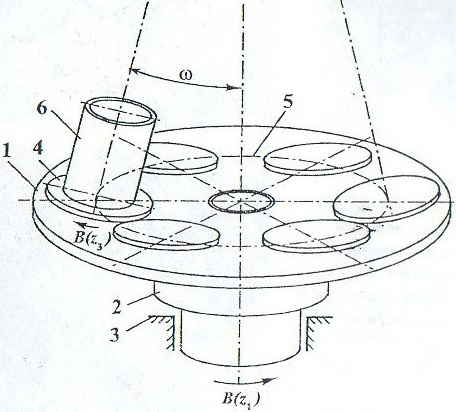
Тут позиції означають наступне:
1 — планшайба пристрою;
2 — центральний вал планшайби;
3 — основа (вакуумна камера);
4 — робочий стіл;
5 — основна окружність планшайби;
6 — виріб.
Тут показано:
omega; — кут нахилу виробу або робочого столу;
B(z1) — напрямок обертання планшайби;
B(z2) — напрямок обертання робочого столу.
На даному пристрої умовно показаний тільки один виріб, встановлений на робочому столі. При нанесенні покриття на всіх робочих столах встановлюються вироби. Раціональне значення кута нахилу виробу до напряму дії потоку плазми, визначається в наступних межах:

d0 — внутрішній діаметр циліндричної поверхні виробу;
l — довжина циліндричного виробу;
ω0 — максимальний кут нахилу осі циліндричної поверхні до напрямку дії потоку плазми (ω0=0,50...1,00).
Таким чином, в даній роботі на підставі системного підходу розроблена загальна класифікація вакуумних іонно–плазмових покриттів внутрішніх циліндричних поверхонь виробів машинобудування. Вона дає можливість вести спрямований пошук і вибір раціональних варіантів покриттів для кожного конкретного практичного випадку експлуатації виробу. А також розроблена схема пристрою для напилення вакуумних іонно–плазмових покриттів на внутрішні циліндричні поверхні виробів.
В цілому виконана робота дає можливість вирішувати питання, пов'язані з підвищенням якості виготовлення виробів в машинобудуванні.
4. Загальний підхід і методика підвищення ефективності обробки фасонних поверхонь деталей
Мета процесу механічної обробки — досягнення необхідних вихідних характеристик - необхідної геометричної форми обробленої поверхні (включаючи мікро і макрогеометрії), і фізико-механічних властивостей поверхневого шару за мінімальний час або з мінімальною собівартістю. З цієї позиції процес обробки розглядається як керований об'єкт.
Всі зовнішні впливи на процес діляться на керовані і некеровані. До керованих відносяться ті впливу, якими можна цілеспрямовано варіювати в певному діапазоні: швидкість різання, мастильно-охолоджуючі технологічні середовища, матеріал інструменту, подача формотворного руху, поперечна подача, формотворчих траєкторія. Такі вхідні впливу, як вихідна поверхня заготовки, вихідна інструментальна поверхня, матеріал деталі, є заданими і виступають в ролі збурень. Швидкість модифікації збурень істотно залежить від призначених режимів різання і оцінюється в порівнянні з основним часом обробки і динамічними характеристиками технологічної обробної системи.[8].
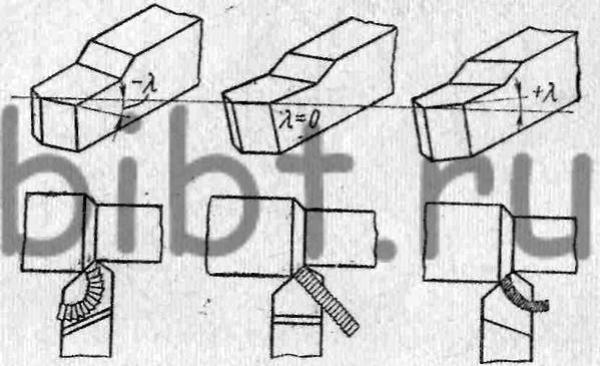
Відомо, що для будь-якого процесу різання, геометричні параметри шару припуску визначають процес в цілому. Ці параметри залежать від форми заготовки, фактичної форми інструментальної поверхні і фактичної траєкторії формотворного руху, яка визначає взаємне розташування інструменту та заготовки при обробці. В результаті геометричного взаємодії з видаленням припуску формується оброблена поверхня, а також її макро- і геометрія. Найбільш складні процеси відбуваються при формуванні фі- 32 Зіко-механічних властивостей поверхневого шару (шорсткість, характер і величина залишкових напруг, структурні перетворення).
Эксплуатационные свойства деталей и узлов машин существенно зависят от качества их сопрягающихся поверхностей и поверхностного слоя, которые определяются геометрическими (макроотклонение, волнистость, шероховатость) и физикомеханическими (микротвердость, остаточные напряжения, структура) характеристиками и взаимным расположением микронеровностей на сопрягаемых элементах.[8,9]:
При цьому процес обробки фасонної поверхні характеризується постійною зміною параметрів процесу різання, що обумовлює необхідність детального дослідження їх взаємного впливу, встановлення зв'язків і закономірностей їх впливу на процеси в зоні різання.
При обробці фасонної поверхні складний характер зміни кінематичних геометричних параметрів леза інструменту і параметрів зрізу поверхневого шару істотно ускладнює аналіз впливу цих параметрів на формування шорсткості поверхні, режими обробки, силові і температурні характеристики процесу різання.
Кількісного відповідності безлічі функціональних елементів, в яких діє безліч різних елементарних функцій при експлуатації, безлічі реалізації технологічних впливів і безлічі елементів забезпечення необхідних властивостей в функціональних елементах вироби на кожному рівні глибини технологіПрі обробці криволінійного контуру (рисунок 1.3) збільшується кут підйому профілю і ширина зрізу, а товщина зменшується, отже, зростає усадка стружки, вона мінімальна на ділянках початку контуру і максимал ьна на ділянках в кінці контуру. Чим більше усадка, тим більше дійсна площа перетину зрізу відрізняється від теоретичної.З безлічі факторів, що впливають на усадку стружки, виділяються два основних: в'язкість оброблюваного матеріалу і швидкість різання. З ростом подачі збільшується площа залишкового перетину зрізу і зменшується дійсна зрізується площа. Зі збільшенням глибини різання зменшується частка залишкового перетину зрізу і, отже, інтенсивність її впливу на силу різання.
5. Підготовка поверхні деталей до нанесення плазмових потоків
Розміри деталей мають бути зменшені на товщину напилюваних покриттів, яку вибирають. Ділянка поверхні виробу, що підлягає напиленню, повинна мати плавні переходи до примикаючих поверхонь або відповідну конфігурацію. Покриття на пази і глухі отвори слід наносити при відношенні ширини або діаметру отвору до його глибини не менше 2 мм.
Міра очищення поверхні деталей від забруднення багато в чому визначає якість нанесених покриттів. Наявність на поверхні бруду, оксидних плівок, масла, зменшується міцність зчеплення покриття з металом деталі, і це може послужити причиною невиправного браку. Особливу увагу приділяють відновлюваним деталям, що мають грунтові забруднення, залишки паливно–мастильних матеріалів, продукти корозії та ін. Очищення роблять різними способами: механічним, струминним, зануренням, циркуляційним, комбінованим та ін [10].
При підготовці поверхню знежирюють органічними розчинниками, миючими складами, лужними розчинами і емульсіями по ГОСТ 9–402–80, потім промивають водою. Після цього деталі сушать в сушильній шафі при температурі 60–150 °С або обдувають стислим повітрям.
В окремих випадках застосовують знежирення за допомогою протирального матеріалу, змоченого уайт–спиртом або бензином, з дотриманням відповідних правил промсанитарии і протипожежній безпеці. Деталі, що містять глибокі пази, масляні канали і інші місця, що утрудняють видалення забруднень, окрім поверхневого знежирення піддають нагріву в печі при температурі 220–340 °С впродовж 2–3 ч для вигорання масла.
Попередня обробка деталей перед напиленням включає також активацію поверхні, що впливає на міцність зчеплення за допомогою зміни інтенсивності фізико–хімічної взаємодії контактуючих матеріалів. Механічне зчеплення напилюваних часток з основою відбувається за рахунок їх розтікання і заклинювання. Тому міцність зчеплення багато в чому визначається параметрами шорсткості поверхні (Ra — середньоарифметичне відхилення профілю мікрорельєфу; Rz — висота нерівностей мікрорельєфу).
Для надання шорсткості поверхні основи використовують наступні основні способи обробки [11]:
1. дробеструменну або піскоструминну обробку;
2. механічну обробку поверхні;
3. нанесення на поверхню виробу подслоя матеріалу, що володіє високою адгезією до основного металу (наприклад, молібдену або алюмініду нікелю)
Встановлено, що міцність зчеплення покриття при різних способах попередньої обробки основи змінюється. Деформація і розтікання напилюваних часток на шорсткій поверхні залежить від топографії поверхні і, передусім, від кроку нерівностей. Якщо западина занадто вузька, то напилювана частка затікатиме в суміжну западину. При занадто широкій западині малі напилювані частки можуть не заклинюватися в ній і розбризкуватися. Покриття формується переважно в канавках. На виступах утворюється шар відносно меншої товщини.
При підготовці поверхні слід враховувати наступне [12]:
1. яка міцність зчеплення нанесеного покриття може бути досягнута за допомогою даного способу підготовки поверхні;
2. яка твердість поверхні оброблюваного виробу;
3. якої товщини отвір можна напилювати;
4. який спосіб буде найбільш економічним.
Висновки
Виконано аналіз основних особливостей і способів технологічного забезпечення обробки фасонних поверхонь. Встановлено актуальність вирішення комплексного завдання підвищення продуктивності і зниження собівартості за рахунок визначення оптимальних режимів різання в умовах змінності параметрів процесу токарної обробки та застосування твердосплавного інструменту з покриттями з функціонально-орієнтованими властивостями.
Розроблено методику підвищення ефективності обробки фасонних поверхонь за рахунок обґрунтованого поєднання оптимальних режимів обробки і спеціального інструменту, що забезпечує необхідні експлуатаційні функції в умовах змінності параметрів процесу різання. Встановлено коефіцієнти, що характеризують зміни геометричних параметрів леза інструменту — кутів в плані (до 4-х разів), параметрів зрізаного шару (до 4-х разів) і швидкості різання (до 2-х разів) уздовж криволінійної котра утворює фасонної поверхні.
Перелік посилань
Барвинок В.А. — Управление напряжённым состоянием и свойства плазменных покрытий. — М.: Машиностроение, 1990. — 384 с.: ил.
Машиностроение. Энциклопедия. / Ред. совет: К.В.Фролов (пред.) и др. — М.: Машиностроение. Технологии, оборудование и системы управления в электронном машиностроении. Т. III — 8/Ю.В. Панфилов, Л.К. Ковалев, В.А. Блохин и др.; Под общ. ред. Ю.В. Панфилова. 2000. — 744 с.
Нанесение износостойких покрытий на быстрорежущий инструмент / Ю.Н. Внуков, А.А. Марков, Л.В. Лаврова, Н.Ю. Бердышев. — К.: Тэхника, 1992. — 143 с.
Михайлов А.Н., Михайлов В.А., Михайлова Е.А. Методика и основные принципы синтеза функционально–ориентированных вакуумных ионно–плазменных покрытий изделий машиностроения. // Упрочняющие технологии и покрытия. — М.: Машиностроение. №7. 2005. С. 3–9.
Mikhaylov A., Mikhaylov V., Mikhaylova E. Bases of synthesis of special functionally–oriented vacuum covers of workpieces of mechanical engineering. // Jhe 31 Internationaly Attendeol Scientitic Conference of the Military Technical Academy “Modern Technologits in the 21 th Century”. — Bucharest: MTA, 2005. P.127–131.
Михайлов А.Н., Михайлов В.А., Михайлова Е.А. Основы синтеза нового класса вакуумных ионно–плазменных покрытий изделий машиностроения // Conferinta Stiintifica Internationala Iasi–Chisinau: Tehnologii Moderne. Calitate. Restructurari. TMCR 2005. Chisinau, 2005. Vol. 2. P. 327–331.
Сайт з описом іонно–плазмових технологічних пристроїв і технологією нанесення функціональних покриттів на важкодоступні внутрішні поверхні http://www.itm.dp.ua/RUS/Technol/Tech00010.html.
Михайлов А.Н. Основы синтеза функционально–ориентированных технологий. — Донецк: ДонНТУ, 2009. — 346 с.
Михайлов А.Н. Общие особенности функционально–ориентированных технологий и принципы ориентации их технологических воздействий и свойств изделий. // Машиностроение и техносфера XXI века. Сборник трудов XIV международной научно–технической конференции в г. Севастополе 17–22 сентября 2007 г. В 5–ти томах. — Донецк: ДонНТУ, 2007. Т. 3. С. 38–52.
Лащенко Г.И. — Плазменное упрочнение и напыление. — К.: "Екотехнологія" 2003. — 64 с.
Metal Coat Technologyhttp://www.mctse.ru/index.php/faq/37-q-podgotovka-k-napyleniyu.
Open Library — открытая библиотека учебной информации http://oplib.ru/random/view/774043.