Реферат по теме выпускной работы
Реферат носит предварительный характер, поскольку время его составления — март–апрель 2019 г., тогда как защита магистерской диссертации запланирована на июнь 2020 г.
Содержание
- Актуальность темы
- 1. Цель и задачи исследования
- 2. Анализ современного состояния вопроса исследования
- 3. Обзор исследований и разработок
- 3.1 Анализ особенностей токарной обработки фасонных поверхностей деталей машин
- 3.2 Классификация деталей с внутренними цилиндрическими поверхностями. Область применения
- 3.3 Схема устройства для нанесения покрытий на внутренние цилиндрические поверхности изделий
- 4. Общий подход и методика повышения эффективности обработки фасонных поверхностей деталей
- 5. Подготовка поверхности деталей к нанесению плазменных потоков
- Выводы
- Список источников
Актуальность темы
Фасонные детали, поверхности которых сформированы криволинейной образующей, достаточно широко используются в различных машинах и механизмах. Механическая обработка таких поверхностей довольно затруднительна и обеспечивается сложной кинематикой движения режущего инструмента относительно обрабатываемой заготовки, а также характеризуется переменными значениями технологических факторов, определяющих условия обработки.
Процесс токарной обработки фасонной поверхности существенно отличается от обработки цилиндрической поверхности, т. к. имеет ярко выраженный переменный характер. Это обусловлено изменением ряда геометрических параметров процесса резания: траектория формообразующего движения, непрерывно изменяющееся направление подачи, изменение мгновенных значений ширины и толщины среза, изменение кинематических углов в плане, кинематических переднего и заднего углов. Как результат, наблюдается изменение сил и температур резания, шероховатости вдоль образующей фасонной поверхности, что в свою очередь Влияет на выбор режимов резания — скорости, подачи. [1].
Важным фактором повышения эффективности обработки фасонных поверхностей является обоснование рациональных условий ее выполнения. В связи с этим весьма актуальны исследования по оптимизации режимов резания, обеспечивающих для заданных условий обработки и требований к качеству обработанных поверхностей максимальную производительность и минимальную себестоимость, что определяет повышение рентабельности машиностроительного производства.
Перспективным вариантом решения проблемы повышения эффективности токарной обработки фасонных деталей является использование современного твердосплавного инструмента с функционально-ориентированными покрытиями особой структуры, что позволяет максимально повысить их общие эксплуатационные свойства за счет местного увеличения характеристик отдельных элементов, поверхностей и/или зон изделия в зависимости от функциональных местных особенностей их эксплуатации.
1. Цель и задачи исследования
Целью работы является повышение производительности и снижение себестоимости токарной обработки фасонных деталей при заданном уровне качества поверхности в условиях переменности параметров процесса резания на основе комплексного обеспечения оптимальных режимов обработки и применения твердосплавного инструмента с функциональноориентированными свойствами.
В соответствии с поставленной целью определены следующие задачи:
- Выполнить анализ особенностей и способов технологического обеспечения эффективности и качества обработки фасонных поверхностей деталей машин.
- Разработать принципы и методику повышения эффективности токарной обработки фасонных поверхностей в условиях переменности параметров процесса резания.
- Установить закономерностии формирования и связи шероховатости поверхности, силовых и температурных характеристик процесса резания с учетом изменяющихся геометрических параметров и параметров среза в процессе обработки.
- Разработать методику многокритериальной оптимизации режимов токарной обработки фасонных поверхностей с учетом переменности параметров процесса резания и технических ограничений.
- Исследовать особенности применения функционально-ориентированного подхода для обеспечения функциональных свойств твердосплавного инструмента и обосновать выбор материала и структуры износостойких покрытий.
2. Анализ современного состояния вопроса исследования
В машиностроении широкое распространение получили детали, сложной формы, поверхность которых ограничена сложным фасонным профилем. К таким деталям относят ковочные, вырубные и вытяжные штампы; матрицы и пуансоны пресс-форм; фасонные валки для прокатки и волочения; подающие и калибровочные валки правильных станов; оправки для раскатки; бегунки колесных, гусеничных, подъемно-транспортных машин; объемные копиры; копировальные ролики и пальцы; направляющие аппараты и др. Несмотря на различное функциональное назначение указанных деталей, они объединены схожими техническими требованиями, связывающими точность размеров, формы и расположения фасонного профиля с точностью изготовления базовых (посадочных) поверхностей. [2,3].
3. Обзор исследований и разработок
3.1 Анализ особенностей токарной обработки фасонных поверхностей деталей машинй
Под деталями сложной формы подразумеваются детали, включающие сложные поверхности. Сложной или фасонной называется поверхность, специально отличающаяся по форме от цилиндрической или плоской поверхности. Обрабатываемые поверхности деталей относят к фасонным, если они образованы криволинейной образующей, комбинацией прямолинейных образующих, расположенных под различными углами к оси детали, или комбинацией криволинейных и прямолинейных образующих. Фасонные поверхности, входящие в конструкцию деталей сложной формы принято делить на основные группы (Рисунок 1.1).
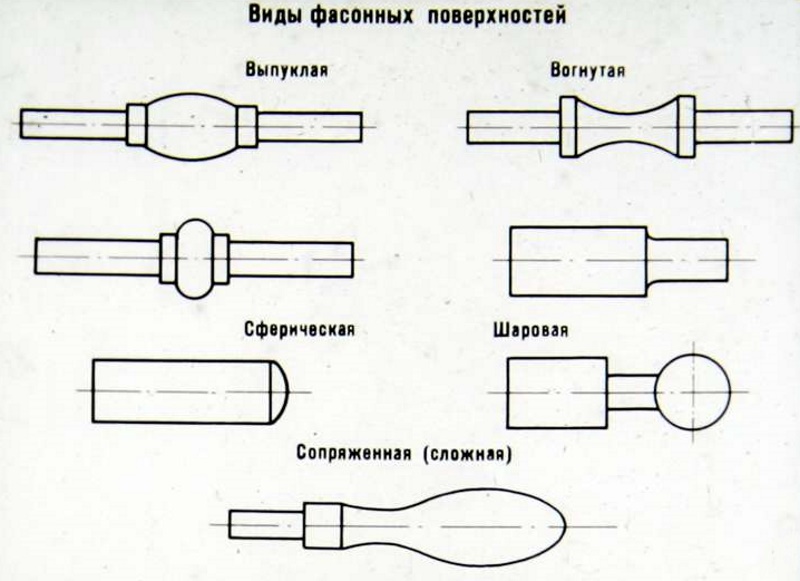
В качестве представителей рассматриваемой группы деталей выбраны ролики прокатного оборудования, направляющие и задающие движение заготовок и проката (рисунок 1.2), использующиеся в вводных роликовых проводках мелкосортных и проволочных станов. Детали эксплуатируются в довольно тяжелых условиях и требуют регулярной замены по причине износа рабочих поверхностей.
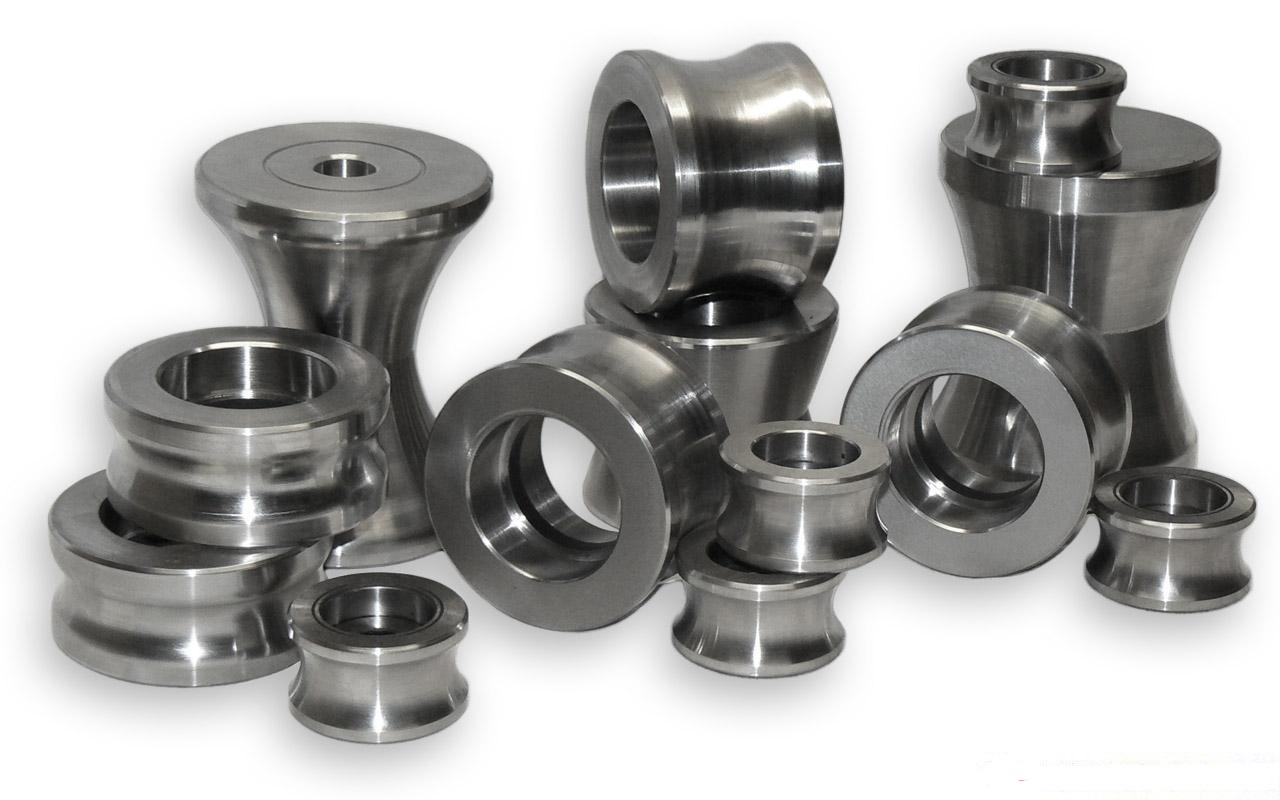
Точность изготовления роликов, направляющих и задающих движение заготовок и проката в прокатной клети соответствует 7-8 квалитету. При этом рациональный выбор материала в сочетании с высокой точностью изготовления и соответствующей термической обработкой обеспечивают их высокую износостойкость при эксплуатации.
Для эффективного управления процессом обработки в этом случае целесообразно выполнять на основе методик, учитывающих весь комплекс переменных параметров процесса и их взаимосвязь. Под качеством продукции понимают совокупность свойств в мере полезности продукции, удовлетворяющих определенным общественным и личным потребностям в соответствии с её назначением. Улучшение качества — важное условие повышения эффективности производства.
3.2 Классификация деталей с внутренними цилиндрическими поверхностями. Область применения
Внутренние цилиндрические поверхности (отверстия) встречаются у большинства деталей машин, механизмов, элементов, как тел вращения, так и не тел вращения. К таким деталям можно отнести тела вращения типа колес, дисков, шкивов, блоков, стержней, втулок, стаканов, колонок, валов, осей, штоков, тела вращения с элементами зубчатого зацепления, а также трубы, сегменты, не тела вращения: корпусные, опорные, емкостные и др.
![]() |
Внутренние цилиндрические поверхности применяются для сопряжения деталей друг с другом, для подвода смазки или охлаждающей жидкости. Они делятся на сквозные и глухие. Первые обработанные на проход, вторые — на определённую глубину. По форме поверхностей цилиндрические отверстия бывают гладкие, ступенчатые, состоящие из участков разных диаметров расположенные на одной оси последовательно одно за другим, и с канавками, а также с резьбой. Отверстия, длина которых превышает 5–6 диаметров, называют глубокими. Технологические процессы нанесения вакуумных ионно–плазменных покрытий на внутренних цилиндрических поверхностях применяются в гидроцилиндрах посадочных устройств (шасси) самолётов, гидроагрегатах авиационной техники, в горно–шахтном и бурильном оборудовании, в машинах и устройствах широкого назначения для повышения эксплуатационной долговечности пар трения ответственных узлов машин, работающих в условиях повышенного коррозионного и механического износа [7]. |
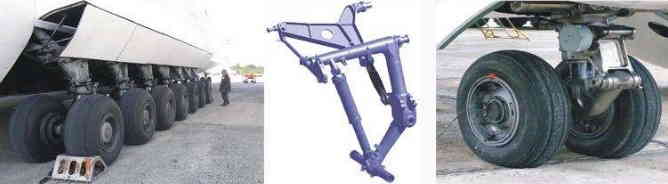
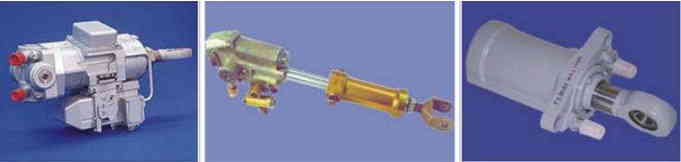
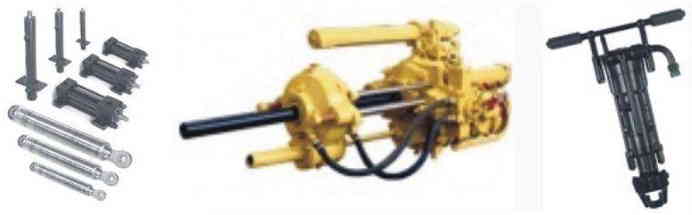
Многообразие изделий машиностроения и их элементов требует более глубокого изучения вопросов нанесения покрытий в труднодоступные места. К таким изделиям можно отнести детали с внутренними цилиндрическими поверхностями. Вместе с тем процессы нанесения вакуумных ионно–плазменных покрытий требуют специального изучения. На рис. 4 показана схема узла, имеющего внутреннюю цилиндрическую поверхность, который состоит из двух элементов, а именно вала 1 вращающегося относительно направляющей втулки 2. Для повышения свойств этого узла на внутреннюю поверхность направляющей втулки нанесено покрытие 3. Это даёт возможность повысить эксплуатационные параметры данного узла. Здесь на рис.1, а показан общий вид узла, на рис.1,б — сечение элемента узла. |
![]() |
3.3 Схема устройства для нанесения покрытий на внутренние цилиндрические поверхности изделий
Для выполнения процесса нанесения вакуумных ионно–плазменных покрытий на внутренние цилиндрические поверхности изделий разработано специальное устройство. На рис. 5 показана принципиальная схема устройства для нанесения покрытий на внутренние цилиндрические поверхности изделий, которая реализует принципиально кинематическую схему 1–го класса движений.
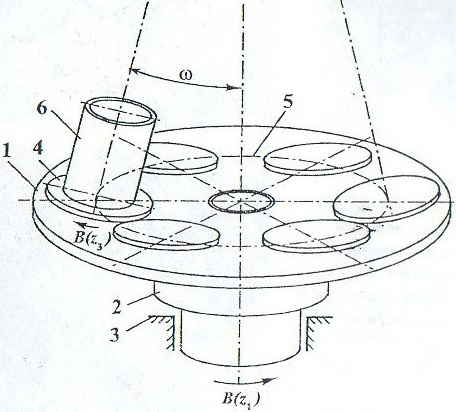
Здесь позиции обозначают следующее:
1 — планшайба устройства;
2 — центральный вал планшайбы;
3 — основание (вакуумная камера);
4 — рабочий стол;
5 — основная окружность планшайбы;
6 — изделие.
Здесь показано:
ω — угол наклона изделия или рабочего стола;
B(z1) — направление вращения планшайбы;
B(z2) — направление вращения рабочего стола.
На данном устройстве условно показано только одно изделие, установленное на рабочем столе. При нанесении покрытия на всех рабочих столах устанавливаются изделия. Рациональное значение угла наклона изделия к направлению действия потока плазмы, определяется в следующих пределах:

d0 — внутренний диаметр цилиндрической поверхности изделия;
l — длина цилиндрического изделия;
ω0 — максимальный угол наклона оси цилиндрической поверхности к направлению действия потока плазмы (ω0=0,50...1,00).
Таким образом, в данной работе на основании системного подхода разработана общая классификация вакуумных ионно–плазменных покрытий внутренних цилиндрических поверхностей изделий машиностроения. Она даёт возможность вести направленный поиск и выбор рациональных вариантов покрытий для каждого конкретного практического случая эксплуатации изделия. А также разработана схема устройства для напыления вакуумных ионно–плазменных покрытий на внутренние цилиндрические поверхности изделий.
В целом выполненная работа даёт возможность решать вопросы, связанные с повышением качества изготовления изделий в машиностроении.
4. Общий подход и методика повышения эффективности обработки фасонных поверхностей деталей
Цель процесса механической обработки — достижение требуемых исходных характеристик — необходимой геометрической формы обработанной поверхности (включая микро и макрогеометрию), и физико-механических свойств поверхностного слоя за минимальное время или с минимальной себестоимостью. С этой позиции процесс обработки рассматривается как управляемый объект.
Все внешние влияния на процесс делятся на управляемые и неуправляемые. К управляемым относятся те влияния, которыми можно целенаправленно варьировать в определенном диапазоне: скорость резания, смазочно-охлаждающие технологические среды, материал инструмента, подача формообразующего движения, поперечная подача, формообразующая траектория. Такие входные влияния, как исходная поверхность заготовки, исходная инструментальная поверхность, материал детали, являются заданными и выступают в роли возмущений. Скорость модификации возмущений существенно зависит от назначенных режимов резания и оценивается в сравнении с основным временем обработки и динамическими характеристиками технологической обрабатывающей системы.[8].
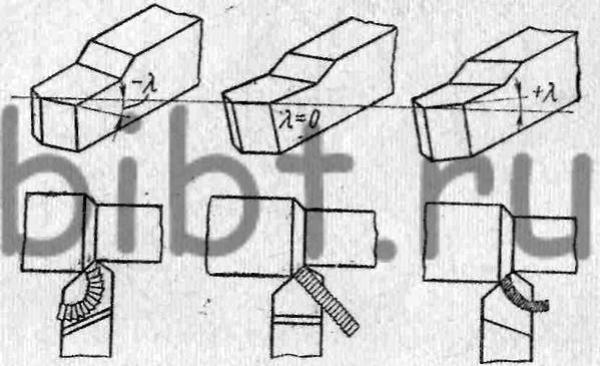
Известно, что для любого процесса резания, геометрические параметры слоя припуска определяют процесс в целом. Эти параметры зависят от формы заготовки, фактической формы инструментальной поверхности и фактической траектории формообразующего движения, которая определяет взаимное расположение инструмента и заготовки при обработке. В результате геометрического взаимодействия с удалением припуска формируется обработанная поверхность, а также ее макро- и микрогеометрия. Наиболее сложные процессы происходят при формировании фи- 32 зико-механических свойств поверхностного слоя (шероховатость, характер и величина остаточных напряжений, структурные преобразования)..
Эксплуатационные свойства деталей и узлов машин существенно зависят от качества их сопрягающихся поверхностей и поверхностного слоя, которые определяются геометрическими (макроотклонение, волнистость, шероховатость) и физикомеханическими (микротвердость, остаточные напряжения, структура) характеристиками и взаимным расположением микронеровностей на сопрягаемых элементах. [8,9]:
При этом процесс обработки фасонной поверхности характеризуется постоянным изменением параметров процесса резания, что обуславливает необходимость детального исследования их взаимного влияния, установления связей и закономерностей их влияния на процессы в зоне резания.
При обработке фасонной поверхности сложный характер изменения кинематических геометрических параметров лезвия инструмента и параметров среза поверхностного слоя существенно усложняет анализ влияния этих параметров на формирование шероховатости поверхности, режимы обработки, силовые и температурные характеристики процесса резания.
3. Количественного соответствия множества функциональных элементов, в которых действует множество различных элементарных функций при эксплуатации, множеству реализации технологических воздействий и множеству элементов обеспечения необходимых свойств в функциональных элементах изделия на каждом уровне глубины технологии. При обработке криволинейного контура (рисунок 1.3) увеличивается угол подъема профиля и ширина среза, а толщина уменьшается, следовательно, возрастает усадка стружки, она минимальна на участках начала контура и максимальна на участках в конце контура. Чем больше усадка, тем больше действительная площадь сечения среза отличается от теоретической. Из множества факторов, влияющих на усадку стружки, выделяются два основных: вязкость обрабатываемого материала и скорость резания. С ростом подачи увеличивается площадь остаточного сечения среза и уменьшается действительная срезаемая площадь. С увеличением глубины резания уменьшается доля остаточного сечения среза и, следовательно, интенсивность ее влияния на силу резания.
5. Подготовка поверхности деталей к нанесению плазменных потоков
Размеры деталей должны быть уменьшены на толщину напыляемых покрытий, которую выбирают. Участок поверхности изделия, подлежащий напылению, должен иметь плавные переходы к примыкающим поверхностям либо соответствующую конфигурацию. Покрытия на пазы и глухие отверстия следует наносить при отношении ширины или диаметра отверстия к его глубине не менее 2 мм.
Степень очистки поверхности деталей от загрязнения во многом определяет качество нанесенных покрытий. Наличие на поверхности грязи, оксидных плёнок, масла, уменьшается прочность сцепления покрытия с металлом детали, и это может послужить причиной неисправимого брака. Особое внимание уделяют восстанавливаемым деталям, имеющим почвенные загрязнения, остатки топливно–смазочных материалов, продукты коррозии и др. Очистку производят различными способами: механическим, струйным, погружением, циркуляционным, комбинированным и др. [10].
При подготовке поверхность обезжиривают органическими растворителями, моющими составами, щелочными растворами и эмульсиями по ГОСТ 9–402–80, затем промывают водой. После этого детали сушат в сушильном шкафу при температуре 60–150 °С или обдувают сжатым воздухом.
В отдельных случаях применяют обезжиривание с помощью протирочного материала, смоченного уайт–спиртом или бензином, с соблюдением соответствующих правил промсанитарии и противопожарной безопасности. Детали, содержащие глубокие пазы, масляные каналы и другие места, затрудняющие удаление загрязнений, кроме поверхностного обезжиривания подвергают нагреву в печи при температуре 220–340 °С в течение 2–3 ч для выгорания масла.
Предварительная обработка деталей перед напылением включает также активацию поверхности, влияющей на прочность сцепления посредством изменения интенсивности физико–химического взаимодействия контактирующих материалов. Механическое сцепление напыляемых частиц с основой происходит за счёт их растекания и заклинивания. Поэтому прочность сцепления во многом определяется параметрами шероховатости поверхности (Ra — среднеарифметическое отклонение профиля микрорельефа; Rz — высота неровностей микрорельефа).
Для придания шероховатости поверхности основы используют следующие основные способы обработки [11]:
- дробеструйную или пескоструйную обработку;
- механическую обработку поверхности;
- нанесение на поверхность изделия подслоя материала, обладающего высокой адгезией к основному металлу (например, молибдена или алюминида никеля).
Установлено, что прочность сцепления покрытия при различных способах предварительной обработки основы изменяется. Деформирование и растекание напыляемых частиц на шероховатой поверхности зависит от топографии поверхности и, прежде всего, от шага неровностей. Если впадина слишком узкая, то напыляемая частица будет затекать в смежную впадину. При слишком широкой впадине малые напыляемые частицы могут не заклиниваться в ней и разбрызгиваться. Покрытие формируется преимущественно в канавках. На выступах образуется слой относительно меньшей толщины.
При подготовке поверхности следует учитывать следующее [12]:
- какая прочность сцепления нанесенного покрытия может быть достигнута с помощью данного способа подготовки поверхности;
- какова твердость поверхности обрабатываемого изделия;
- какой толщины отверстие можно напылять;
- какой способ будет наиболее экономичным.
Выводы
Выполнен анализ основных особенностей и способов технологического обеспечения обработки фасонных поверхностей. Установлена актуальность решения комплексной задачи повышения производительности и снижения себестоимости за счет определения оптимальных режимов резания в условиях переменности параметров процесса токарной обработки и применения твердосплавного инструмента с покрытиями с функционально-ориентированными свойствами.
Разработана методика повышения эффективности обработки фасонных поверхностей за счет обоснованного сочетания оптимальных режимов обработки и специального инструмента, обеспечивающего требуемые эксплуатационные функции в условиях переменности параметров процесса резания. Установлены коэффициенты, характеризующие изменения геометрических параметров лезвия инструмента — углов в плане (до 4-х раз), параметров срезаемого слоя (до 4-х раз) и скорости резания (до 2-х раз) вдоль криволинейной образующей фасонной поверхности.
Список источников
- Барвинок В.А. — Управление напряжённым состоянием и свойства плазменных покрытий. — М.: Машиностроение, 1990. — 384 с.: ил.
- Машиностроение. Энциклопедия. / Ред. совет: К.В.Фролов (пред.) и др. — М.: Машиностроение. Технологии, оборудование и системы управления в электронном машиностроении. Т. III — 8/Ю.В. Панфилов, Л.К. Ковалев, В.А. Блохин и др.; Под общ. ред. Ю.В. Панфилова. 2000. — 744 с.
- Нанесение износостойких покрытий на быстрорежущий инструмент / Ю.Н. Внуков, А.А. Марков, Л.В. Лаврова, Н.Ю. Бердышев. — К.: Тэхника, 1992. — 143 с.
- Михайлов А.Н., Михайлов В.А., Михайлова Е.А. Повышение эффективности токарной обработки фсонных поверхностей твердосплавным инструментом с износостойкими покрытиями с функциональноориентированными свойствами — М.: Машиностроение. 05.02.08. 2016. С. 1–186.
- Mikhaylov A., Mikhaylov V., Mikhaylova E. Bases of synthesis of special functionally–oriented vacuum covers of workpieces of mechanical engineering. // Jhe 31 Internationaly Attendeol Scientitic Conference of the Military Technical Academy “Modern Technologits in the 21 th Century”. — Bucharest: MTA, 2005. P.127–131.
- Петряева И.А., Михайлов В.А., Михайлова Е.А. Основы синтеза нового класса вакуумных ионно–плазменных покрытий изделий машиностроения // Conferinta Stiintifica Internationala Iasi–Chisinau: Tehnologii Moderne. Calitate. Restructurari. TMCR 2005. Chisinau, 2005. Vol. 2. P. 327–331.
- Сайт с описаним ионно–плазменных технологических устройств и технологией нанесения функциональных покрытий на труднодоступные внутренние поверхности http://www.itm.dp.ua/RUS/Technol/Tech00010.html.
- Михайлов А.Н. Основы синтеза функционально–ориентированных технологий. — Донецк: ДонНТУ, 2009. — 346 с.
- Михайлов А.Н. Общие особенности функционально–ориентированных технологий и принципы ориентации их технологических воздействий и свойств изделий. // Машиностроение и техносфера XXI века. Сборник трудов XIV международной научно–технической конференции в г. Севастополе 17–22 сентября 2007 г. В 5–ти томах. — Донецк: ДонНТУ, 2007. Т. 3. С. 38–52.
- Лащенко Г.И. — Плазменное упрочнение и напыление. — К.: "Екотехнологія" 2003. — 64 с.
- Metal Coat Technologyhttp://www.mctse.ru/index.php/faq/37-q-podgotovka-k-napyleniyu.
- Open Library — открытая библиотека учебной информации http://oplib.ru/random/view/774043.