Abstract
Content
- Introduction
- 1. Theme urgency
- 2. The purpose and objectives of the study, expected results
- 3. Overview of Conveyor Belt Automation Solutions
- 4. Developed belt conveyor automation system based on I–7000 PLC
- Conclusion
- References
Introduction
A major contribution to the development of the economy of our region is made by the coal industry. The growth of mining is achieved mainly as a result of technical re-equipment and the introduction of advanced technology with the possibility of further improvement of enterprises on the basis of comprehensive mechanization and automation of production processes and increase labor productivity. The development of the coal mining process, as well as the accelerated sinking of the mine workings, leads to an increase in the amount of methane-air mixture emissions. In coal mines and mines for the delivery of minerals from the face, as well as for transporting it to prefabricated drifts, bremsbergs, slopes and inclined shafts, belt conveyors are widely used.
1. Theme urgency
Conveyor belts are designed to transport minerals through drifts, bremsbergs, slopes and inclined shafts of coal mines and mines.
The increasing volume of mining, the increase in the length of mine workings affect the operating conditions of coal mining equipment and means of transportation, and require their improvement.
In coal mines and mines for the delivery of minerals from the face, as well as for transporting it to prefabricated drifts, bremsbergs, slopes and inclined shafts, belt conveyors are widely used today.
2. The purpose and objectives of the study, expected results
The purpose of the study is the operation efficiency of the main conveyor belt due to the improvement of automation equipment. The article proposes to develop a belt conveyor control system based on the I–7188 XB microcontroller, which will provide control over the main sensors, such as: drive speed sensor, belt speed sensor, drive temperature sensor, belt exit sensor, belt tension and breakage sensor.
The ease of reprogramming modern microcontrollers allows us to further improve the control algorithm without a lot of time and without changing the structure of the system.
3. Overview of Conveyor Belt Automation Solutions
Automation of conveyor transport involves equipping with automatic control and protection equipment. It should provide: [3]
1. The ability to control the conveyor from the central control panel, from the loading point of the conveyor or in local control mode.
2. Operational shutdown of the conveyor from the control panel.
3. Consecutive start-up of conveyors in the reverse order of cargo transportation direction.
4. Automatic warning sound and light signal before starting the conveyor line.
5. Automatic, emergency shutdown of the conveyor drive in case of malfunction of the traction unit, with a prolonged start-up or a decrease in the speed of the traction unit less than 75% of the nominal value.
6. Automatic shutdown of all conveyors transporting cargo to a stopped conveyor, and for scraper conveyors, stop the conveyor to which the cargo is transported in order to avoid trapping the broken chain.
7. Starting any route from the central control panel or from the loading point of conveyors.
8. Operational stop of part of any route from the central control panel or from the place of loading of conveyors without disconnecting the conveyors of the main direction.
9. Re-launching part of any route from the central control panel or from the loading point of conveyors without disconnecting the main conveyors.
The main ways of automation of conveyor transport using the existing automation systems of conveyor belts is the use of equipment AUK–1M, AUK–3, SAUKL, UKI, UST and others.
4. Developed belt conveyor automation system based on I–7000 PLC
Modern trunk conveyor lines are characterized by a considerable length and the use of powerful drives. These are complex automation objects both from the point of view of managing them and ensuring operational safety.
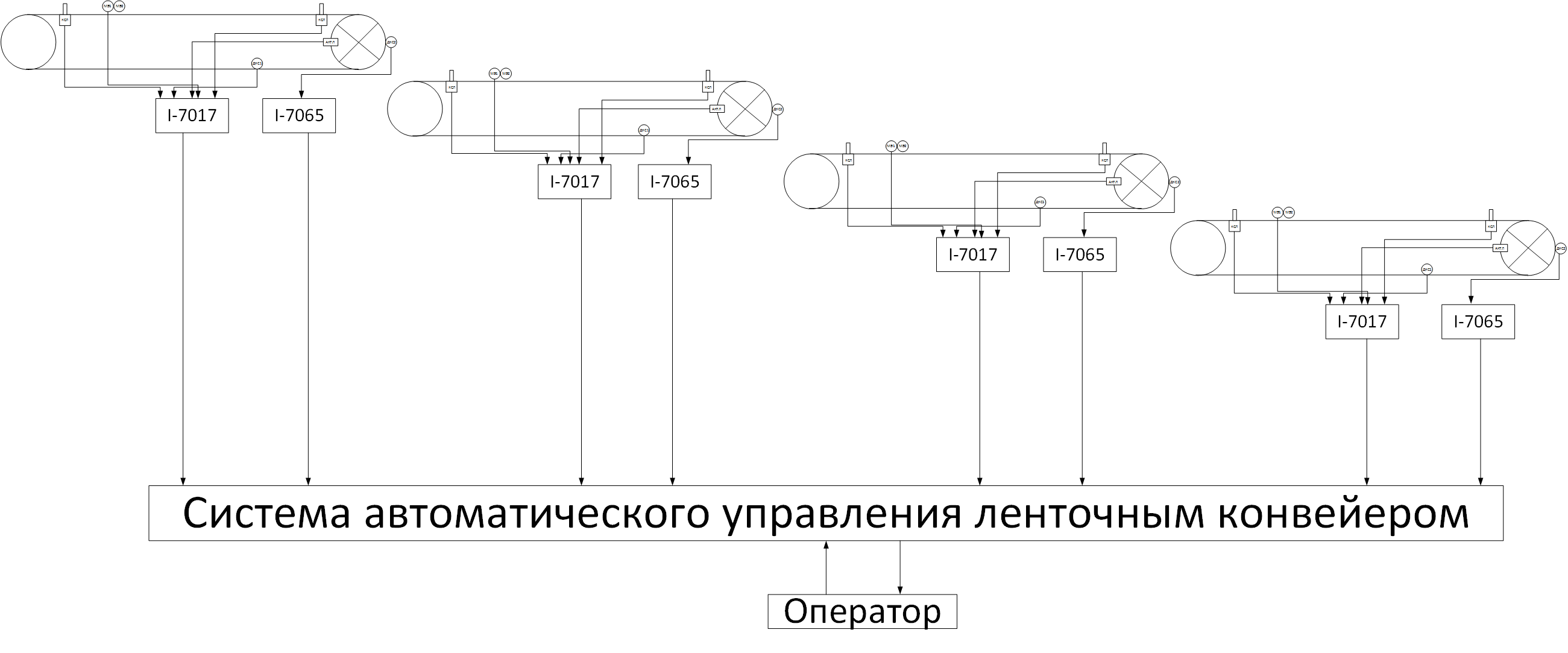
Рисунок 1 — Functional diagram of automation of control of a conveyor belt based on a microcontroller I–7188
Diagram 1.1 indicates:
KSL1–4 — sensors for monitoring the deletion of the tape; ME1–2 — electromagnetic pressure gauges; DKS–1 — tape speed sensor; DKS–2 — drive speed sensor; ACTL — temperature sensor drive.
To control the roll out of the belt, the KSL&ndash2 sensor is used, located on the roller bearings of the conveyor. When the tape comes off in any direction, the flexible cable drive is affected, which accordingly causes the sensor tip to deviate from its central position, the ring magnetic system moves and the contacts close or open. After the deflection stops, the spring returns the magnetic system to its original position.[4]
The control and management of the belt tension force is carried out by the conveyor control device. The tension station is activated when the belt tension corresponds to the lower permissible limit set on the electromagnetic pressure gauge (ME2). The tension station will shut off as soon as the tension reaches the upper permissible limit. When the emergency electromagnetic pressure gauge (ME1) is triggered, the signal enters the automatic conveyor control system and it turns off.[5]
The principle of operation of the sensor for controlling the speed of the tape is that with the linear movement of the tape, the measuring wheel of the sensor also rotates, due to this, pulses are generated at each rotation of the coding disk associated with it by a certain angle.[6]
The drive drum speed sensor is installed so that it is triggered by the passage of bosses on the drum. The principle of operation is based on the fact that when passing through the sensitivity zone of the sensor of each structural element of the controlled mechanism, it generates one current pulse. Thus, the pulse repetition rate is directly related to the rotation speed of the drive drum.[7]
Temperature control of drive drums of conveyor belts is carried out using ACTL–2. It disables the drive motor of the conveyor when the drums are heated above the permissible (65 ± 10 ° C). This prevents the ignition of the tape during its slipping. With this heating of the drum, the ferrite sensor sharply decreases, due to this, the signal of the coil and the induced EMF in the winding decrease. The relay trips, the lamp dies, and the control circuit of the conveyor magnetic starter breaks. [2]
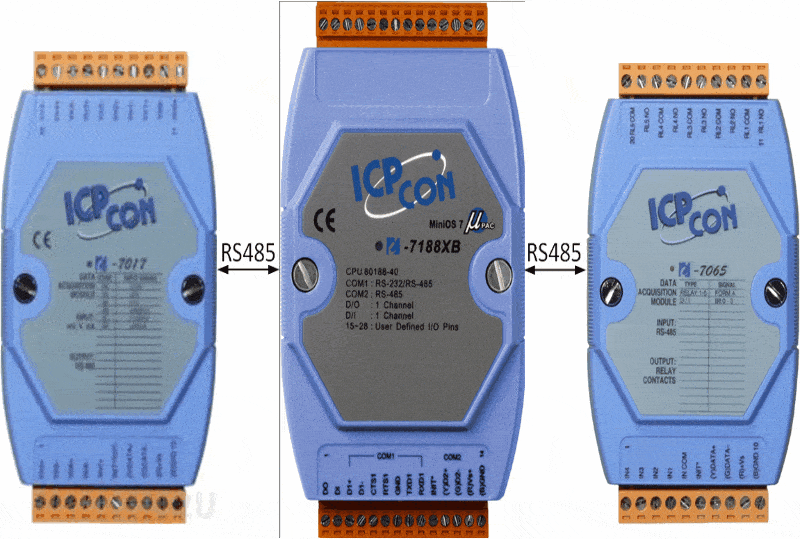
Рисунок 2 — The block diagram of the automation of belt conveyor control based on the microcontroller I–7188
(animation: 9 frames, 5 cycles of repetition, 1261 kilobytes)
MC I–7188 — controller module c. ICP DAS; I–7017 — module 8–channel analog input c. ICP DAS I–7065 — the discrete input / output module with power relay c. ICP DAS; BP — power supply; RS–485 — standard of the physical layer of the asynchronous interface, providing communication between the controller and expansion modules.
Depending on the number of conveyors in the conveyor line, the number of expanders of types I–7017 and I–7065 will change.
Conclusion
The developments were carried out on a microprocessor base using the controller module I–7188 XB. The circuit provides for circuit connections to the controller module and expansion modules, ensuring intrinsic safety of the electrical connection circuits, since the developed automatic control system should work in underground mine conditions in an explosive atmosphere. In particular, voltage dividers and comparators carry out galvanic isolation of the communication line of the system with contact sensors, and also protect the microcontroller of the device from possible overvoltages in the connecting lines of the sensors using diodes and resistors.
The following sensors were selected as monitored sensors: KSL–2 — tape exit sensors; DKS — belt speed sensor and the same drive drum speed sensor; ACTL–2 — temperature sensor of the drive drum; ME — electromagnetic manometers which serve for control of a tape tension.
References
- В. А. Батицкий, В. И. Куроедов, А. А. Рыжков. Автоматизация производственных процессов и АСУТП в горной промышленности.
- Датчики для автоматизации в угольной промышленности. Справочник / Под ред. В. А. Ульшина.- М.: Недра, 1988.
- Требования к автоматизации шахтных конвейеров и конвейерных линий. – М.: Недра, 1981.
- Овсянников, Ю. А. Автоматизация подземного оборудования: справ. рабочего / Ю. А. Овсянников, А. А. Кораблев, А. А. Топорков. - Москва: Недра, 1990. - 287с.
- Стадник, Н.И. Справочник по автоматизации шахтного конвейерного транспорта / Н.И. Стадник, В.Г. Ильюшенко, С.И. Егоров и др. – Киев: Техника, 1992. – 436 с.
- Петков О. Н. Разработка и исследование системы автоматического управления скоростью ленточного конвейера по входному грузопотоку / Диссертация на соискание ученой степени кандидата технических наук. – М.: Московский Ордена Трудового Красного Знамени Горный Институт, 1984. – 143с.
- Каминский, М. Л. Монтаж приборов и систем автоматизации / М. Л. Каминский, В. М. Каминский .– Москва: Высшая школа, 1997 . – 304 с.