Реферат по теме выпускной работы
Содержание
- Введение
- 1. Актуальность темы
- 2. Цель и задачи исследования, планируемые результаты
- 3. Обзор исследований и разработок
- 3.1 Технологический процесс погрузочного комплекса как объект автоматизации
- 3.2 Обзор известных технических решений по автоматизации погрузочного комплекса шахты
- 3.3 Разработка алгоритма работы и схемных решений устройства автоматизации погрузочного комплекса поверхности шахты
- 3.4 Разработка алгоритма работы и монтажной схемы демонстрационного стенда погрузочного комплекса поверхности шахты
- 4. Эксплуатационные требования к системе автоматизации погрузочным комплексом
- Выводы
- Список источников
Введение
Технологический комплекс поверхности шахты (ТКПШ) – это заверщающий этап в добыче полезного ископаемого в шахте, и по этому один из важнейших. ТКПШ – является комплексом горно-технических сооружений и зданий на поверхности шахты, обеспечивающий работу её подземного хозяйства, а также складирование, переработку (при наличии соответствующих комплексов) и отправку потребителям добытого сырья. В функции технологического комплекса поверхности шахты входят: проветривание шахты, подача в шахту электроэнергии, сжатого воздуха, тепла, оборудования и материалов; спуск и подъём людей; приёмка добытого полезного ископаемого и пустой породы; сортировка и обогащение полезных ископаемых; временное хранение продукции и отправка её потребителям; отвалообразование пустых пород; подготовка закладочных материалов, технологической воды (на гидрошахтах); ремонт горных механизмов и оборудования; складирование материалов, изделий и механизмов; обслуживание трудящихся шахты; обеспечение работы административно-управленческих и инженерно-технических служб.
1. Актуальность темы
На современном этапе развития народного хозяйства большое внимание уделяется проблемам повышения эффективности использования технологического и транспортного оборудования, улучшения качества технологических процессов, повышения достоверности учёта материальных ценностей, и конечно, минимизация вмешательства человека в технологические процессы. Одной из таких проблем в угольной промышленности является совершенствование углепогрузочных работ на промышленном железнодорожном транспорте. Погрузка угля в железнодорожные вагоны является завершающим звеном в технологической схеме угольного комплекса поверхности шахт, и, очевидно, представляет собой очень важный объект для возможной автоматизации. В целях повышения эффективности погрузочных работ разработан ряд мероприятий, направленных на улучшение процессов погрузки и учета угля в железнодорожные вагоны[1]. Результатом выполненных работ явилось создание автоматизированных углепогрузочных комплексов. Необходимость внедрения подобных установок определяется тем, что производственная мощность новостроящихся и реконструируемых угольных предприятий достигает нескольких миллионов тонн угля в год, следовательно, объем ежесуточной отгрузки угля составляет несколько сот вагонов в сутки.
2. Цель и задачи исследования, планируемые результаты
Цель проектирования – снижение эксплуатационных расходов на погрузку угля за счет увеличения производительности и исключения аварийных ситуаций путем разработки и применения системы автоматизации погрузочного комплекса поверхности шахты.
Основные задачи исследования:
- анализ погрузочного комплекса как объекта автоматизации;
- анализ существующих разработок по автоматизации погрузочного комплекса поверхности шахты;
- разработка математической модели автоматизированного управления;
- разработка схемных решений. Структурная, функциональная схема устройства автоматизации, алгоритм работы;
- практическая реализация системы автоматизированного управления. Разработка мнемосхемы автоматизированного управления погрузочным комплексом;
- разработка мероприятий по безопасной и безаварийной эксплуатации разработанного устройства.
Объект исследования: Основные технологические процессы поверхности шахты.
Предмет исследования: Система автоматизации погрузочного комплекса поверхности шахты. Принцип алгоритмизации погрузки.
3. Обзор исследований и разработок
3.1 Технологический процесс погрузочного комплекса как объект автоматизации
Транспортировка угля погрузочным комплексом представляет собой сложный многофункциональный процесс, содержащий совокупности взаимосвязанных самостоятельных процессов, основными из которых являются: погрузка угля в вагоны, погрузка угля в ряд бункеров и в автотранспорт, определение фракции загруженного угля, определение объема угля в бункерах, предотвращение потерь ископаемого при транспортировании[2].
Для осуществления погрузки угля в железнодорожные вагоны используются комплексы погрузки угля в железнодорожные вагоны (КПУ). Комплекс погрузки угля в железнодорожные вагоны (углепогрузочный комплекс) представляет собой связанное общим технологическим процессом сочетание механизмов и устройств, предназначенных для передвижения вагонов, подачи угля от мест его добычи или предварительного хранения непосредственно до погрузки в вагоны на одном железнодорожном пути (без промежуточного аккумулирования), дозирования и взвешивания.
На рисунке 1 приведена технологическая схема автоматизированного углепогрузочного комплекса.
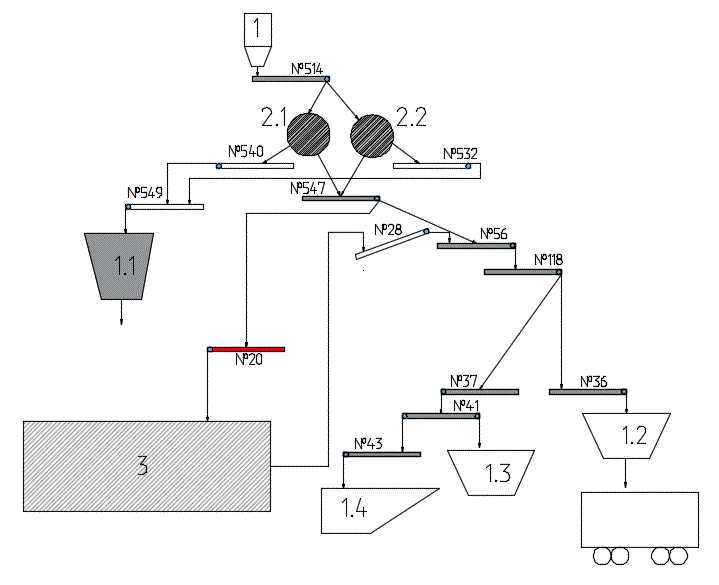
Рисунок 1 – Технологическая схема автоматизированного углепогрузочного комплекса
Условные обозначения:
1 – Бункер скипового ствола; 1.1 – автомобильный бункер; 1.2 – ж.д. бункер; 1.3 – бункер новой котельной; 1.4 – бункер старой котельной; 2.1 – грохот ГЦЛ-1А; 2.2 – грохот ГЦЛ; 3 – аварийный склад угля; №20, 28, 36, 37, 41, 43, 56, 118, 514, 532, 540, 547, 549 – ленточные конвейеры.
КПУ включает в себя механизмы, формирующие поток угля (питатели, затворы) с мест его аккумулирования, или транспортные механизмы, доставляющие уголь на погрузку непосредственно от добычных агрегатов; содержит механизмы поточно-транспортной системы (ПТС) и устройства погрузки угля и передвижения вагонов (маневровые устройства МУ). Каждый железнодорожный путь, на котором осуществляется загрузка вагонов углем, называют фронтом погрузки, или грузовым фронтом. При погрузке угля в вагоны обычно выполняются четыре основные операции, которые определяют характер процесса: передвижение вагонов, подача угля, дозирование, измерение количества[3].
Условия автоматизации технологических комплексов зависят от следующего:
- Способа контроля заполнения вагона (по массе загружаемого угля или по объему кузова вагона);
- Способа равномерного распределения угля в вагоне (путем перемещения вагона в процессе его заполнения или с помощью передвижного загрузочного конвейера);
- Способа транспортирования угля (с непрерывной погрузкой угля в вагоны или с предварительным накоплением);
- Организации погрузки состава (с помощью конвейера с бункера или по безбункерной схеме);
- Сортности угля.
3.2 Обзор известных технических решений по автоматизации погрузочного комплекса шахты
Технологические комплексы погрузки угля отличаются разнородностью техники и технических схем, что затрудняет решение задачи автоматизации. Технологический комплекс включает в себя 3 основные группы оборудования: загрузочные устройства, механизмы для продвижения вагонов, весы для взвешивания.
Загрузочные устройства служат для выполнения основных операций загрузки угля в вагоны и равномерного распределения угля в них. В состав загрузочных устройств входят стационарные и самоходные конвейеры, погрузочные желоба и бункерные затворы.
Для продвижения вагонов применяют тележки и маневровые устройства. Для взвешивания отгружаемого угля служат различные вагонные весы.
Автоматизированный комплекс механизмов КПА разработан институтами «Гипроуглемаш» и Гипроуглеавтоматизация
[4].
В состав комплекса входят:
- Передвижной загрузочный конвейер-бункер производительностью 2 тыс. т/ч, оснащенный транспортирующим органом скребкового типа и выдвижным желобом на головной части, который перемещается с помощью регулируемого привода по рельсовому пути.
- Маневровое устройство с толкателем, взаимодействующим со сцепками загружаемого и предшествующего вагонов.
- Устройство уплотнения с катком, опускаемым с помощью лебедки на поверхность конусной вершины угля, и уплотняющим его во время перемещения состава.
- Автоматизированные вагонные платформенные весы типа 699П200А, обеспечивающие управление процессом весового дозирования загружаемого угля и выдачу документов о результатах взвешивания в конце цикла погрузки.
- Аппаратура управления.
На рисунке 2 приведен автоматизированный комплекс механизмов КПА
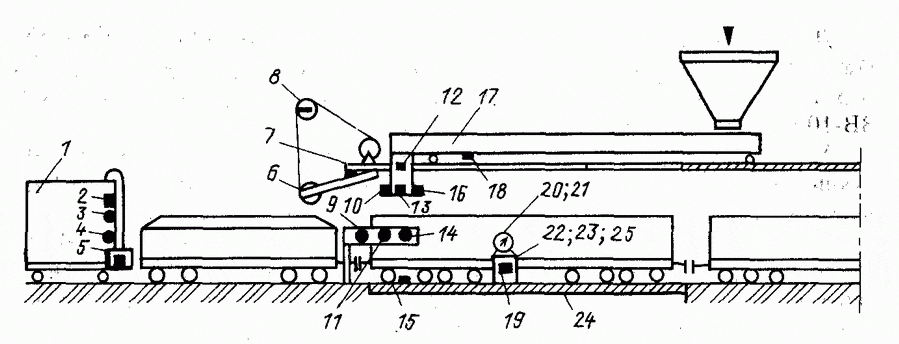
Рисунок 2 – Автоматизированный комплекс механизмов КПА
С помощью средств автоматизации контролируются следующие положения механизмов комплекса и загружаемого вагона: нижнее положение тяговой балки – 5, исходное положение программного устройства весов – 22, положение вагона относительно катка – 9, натяжение каната лебедки катка – 8, промежуточное положение конвейера-бункера – 18, положение вагонов относительно катка – 14, верхнее положение катка – 7, перевод толкателя маневрового устройства на пониженную скорость – 11, положение вагона на весах – 15, нижнее положение желоба – 13, положение механизмов весов в рабочем состоянии – 19, положение конвейера относительно вагона – 10, рабочее положение программного устройства весов – 25, верхнее положение тяговой балки – 2, уровень угля – 16, перевод толкателя маневрового устройства на пониженную скорость – 4, положение тяговой балки относительно сцепки вагонов – 3, окончание загрузки вагона – 20, верхнее положение желоба – 12, окончание регистрации результатов погрузки – 21, фиксированное положение механизмов весов – 23[5].
Система автоматизации технологического комплекса обеспечивает: автоматическое выполнение заданной последовательности технологических операций, автоматическое регулирование процесса заполнения и дозирование вагонов в целях компенсации колебаний веса и интенсивности подачи угля, загрузку вагонов различных типоразмеров и расположенных в составе в любой последовательности. Оператор вводит в систему управления программу загрузки очередного вагона что обеспечивает автоматический режим. Программа набирается на пульте управления периодически во время передвижения составов. Программой задается тип загружаемого вагона, масса вагона инвентарный номер. Оператор также подает первоначальную команду на пуск технологического комплекса, наблюдает за режимом погрузки, контролирует состояние и вносит изменения в положения отдельных механизмов (при рассогласовании их совместной работы).
Технологический комплекс работает следующим образом. Перед началом работы комплекса на пункт погрузки локомотивом подается состав порожних вагонов с остановкой 1-го вагона в зоне действия маневрового устройства. Маневровое устройство сдвигает состав до установки первого вагона на платформу весов, затем начинается загрузка углём вагона с помощью конвейера-бункера. Переключатель выбора режима работы на пульте управления находится в положении Автоматический режим
. Оператор осуществляет пуск механизмов технологического комплекса поточно-транспортной системы и механизмов контроля качества. По окончании цикла загрузки первого вагона автоматически включается привод маневрового устройства для сдвигания груженого вагона с платформы весов, затем – привод опускания катка уплотнителя, прокатывающегося по поверхности угля при движении вагона. В этот момент оператор при необходимости (другой тип вагона) вводит программу загрузки второго вагона.
После подъема катка маневровое устройство автоматически переводится в режим пониженной скорости дотягивания для обеспечения точной остановки второго (порожнего) вагона на платформе весов. После этого включается механизм опускания желоба до определенного уровня и механизм перемещения конвейера для установки его в исходное положение для начала погрузки. Одновременно поднимается тяговая балка маневрового устройства, весы приводятся в рабочее состояние и на их задатчике дозы оператор устанавливает требуемое значение. Включается конвейер, уголь заполняет вагон. По окончанию заполнения объема первичного конуса угля включается привод перемещения конвейера. Маневровое устройство при этом перемещается в режиме холостого хода, проходя над загруженным ранее первым вагоном. После загрузки вагонов автоматически отключается привод конвейера, включается привод подъема желоба, фиксируется масса угля в вагоне и данные с весов выдаются на цифропечатающее устройство. Тяговая балка опускается и включается привод перемещения конвейера-бункера для установки его в исходное положение. Во время движения конвейера уголь накапливается на его транспортирующем органе. Загрузка вагона заканчивается по сигналу с весов после достижения значения массы вагона. Операции погрузки угля повторяются до полной загрузки последнего вагона состава. Конвейер останавливается в положении окончании цикла. Последний вагон с помощью маневрового устройства сдвигается с платформы весов. Каток-уплотнитель по окончании уплотнения угля в последнем вагоне поднимается в верхнее положение и стопорится[6].
3.3 Разработка алгоритма работы и схемных решений устройства автоматизации технологического комплекса поверхности шахты
На начальном этапе работы устройства осуществляется анализ положения вагона. Далее осуществляется анализ проверки тензодатчика ЖД бункера, в зависимости от которого происходит процесс загрузки вагона. Если в бункере нет необходимого уровня заполнения то включается конвейер №514. После этого открывается задвижка скипового бункера, с выдержкой по времени. На следующем этапе включается грохот, и цепочка конвейеров (№547, 56, 118, 36). Далее производится анализ конвейерныхъ весов устанвленных на конвейере №36, и ожидается сигнал о наличие груза на ленте, после чего производится закрытие шибера бункера скипового ствола. После чего ожидается срабатывание коцевика установленного на конвейере №514, и выключение данного конвейера. Затем с выдержкой по времени происходит ожидание отработки грохота, путем анализа конвейерных весов. При наличии груза на весах грохот еще включен, при его отсутствии – выключается грохот. После этого происходит поочередное отключение конвеферов (№547, 56, 118, 36). Процесс доставки полезного ископаемого в ЖД бункер на этом завершен.
Основной рабочий цикл. В начале работы основного алгоритма выполняется проверка тензодатчика основного бункера, при достаточной заполненности технологическая цепочка погрузки не запускается, при обратном происходит ввод оператором № технологической цепочки. И ее последующая отработка.
На основе алгоритма были разработаны структурная и Функциональная схемы устройства автоматизации погрузочного комплекса
На рисунке 3 приведена структурная схема устройства автоматизации погрузочного комплекса
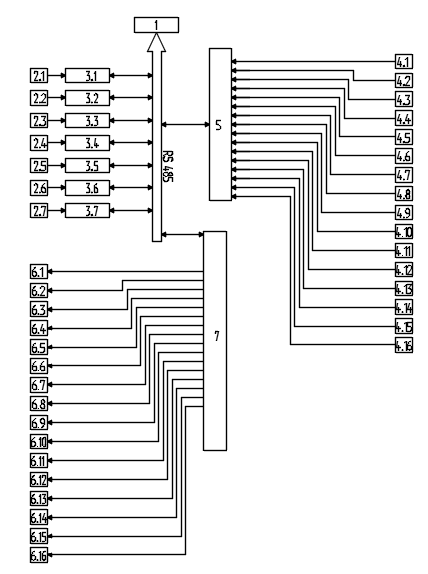
Рисунок 3 – Структураня схема устройства автоматизации погрузочного комплекса
На структурной схеме приняты следующие обозначения:
- ПЛК – 63 – контроллер програмируемый логический;
- ТД – тензодатчик (бункерные и конвейерные весы);
- МВ110-1ТД – тензопреобразователь сигнала;
- ДП – датчик положения;
- МВ110-16Д – модуль дискретного ввода (расширительный блок);
- УР – управляющее реле;
- МВ110-16К – модуль дискретного вывода.
На рисунке 4 приведена функциональная схема устройства автоматизации погрузочного комплекса
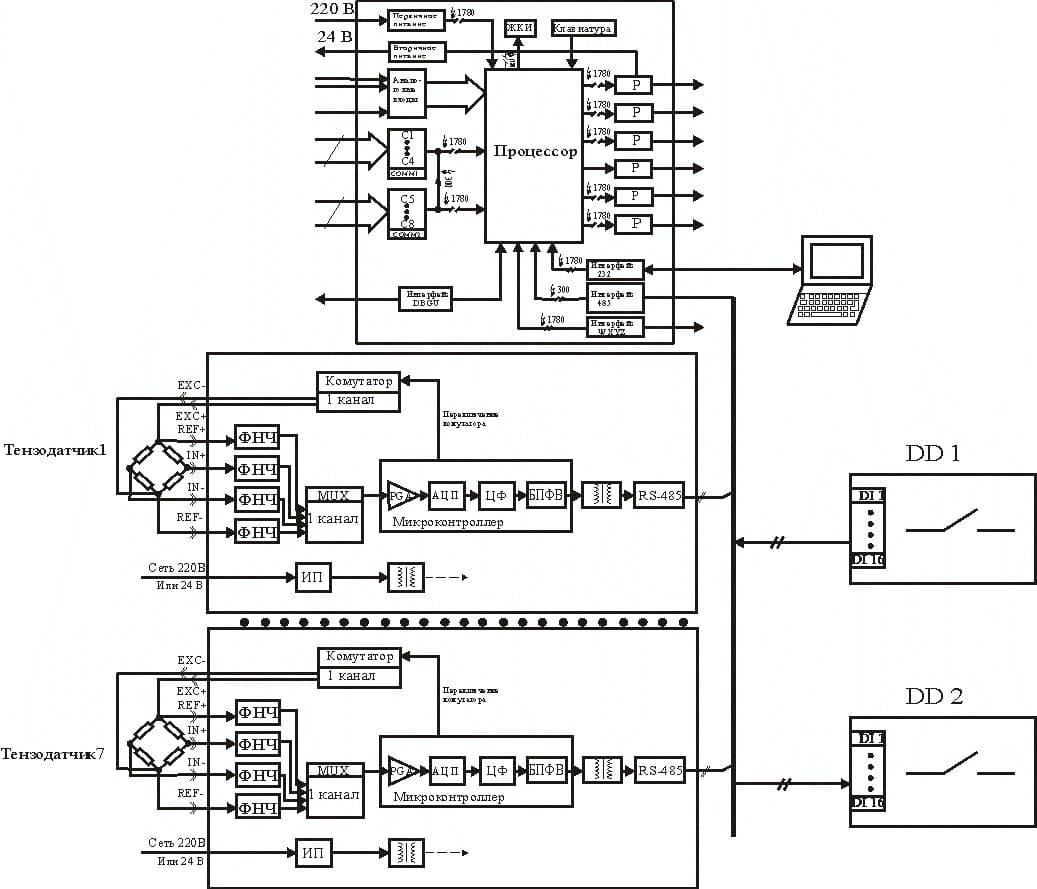
Рисунок 4 – Функциональная схема устройства автоматизации погрузочного комплекса
3.4 Разработка алгоритма работы и монтажной схемы демонстрационного стенда погрузочного комплекса поверхности шахты
Описание работы алгоритма :
Начало работы стенда управляется оператором, а именно розмыканием контакта, и подачи напряжения. Платформа с расположенными на ней вагонами приводится в движение двигателем. Платформа движется до тех пор пока не срабатывает индуктивный датчик считывания нумерации вагонов, установленный непосредственно на задвижде основного бункера, что обеспечивает точное расположение вагона под основным бункером. После срабатывания датчика, платформа останавливается, для погрузки. Процесс погрузки начинается установкой уровня заполнения основного бункера оператором на ПЛК, при помощи оптического датчика в основном бункере. Затем оператор выбирает 1 из дополнительных бункеров и открывает задвижку выбранного бункера, после чего основной бункер наполняется до выставленного уровня, и при его достижении, задвижка закрывается. Оператор открывает задвижку основного бункера, и содержимое высыпается в вагон, после этого задвижка закрывается, и датчик уровня устанавливается в начальное положение. Далее процес повторяется до тех пор, пока количество вагоном меньше 4. При заполнении всех имеющихся вагонов, платформа заезжает в концевое положение, откуда она возвращается включением тумблера в исходное положение.
На рисунке 5 приведен алгоритм работы блока управления стенда погрузочного комплекса шахты.
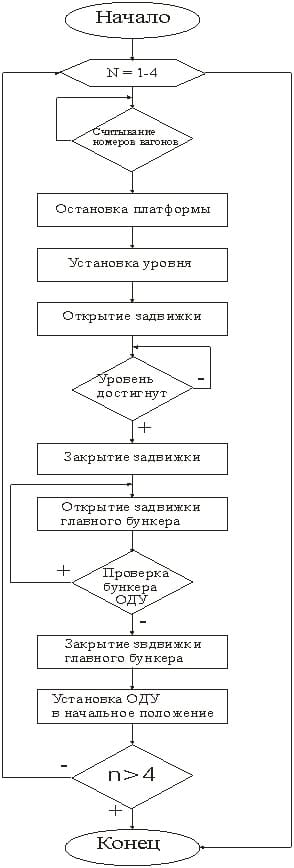
Рисунок 5 – Алгоритм работы блока управления стенда погрузочного комплекса шахты
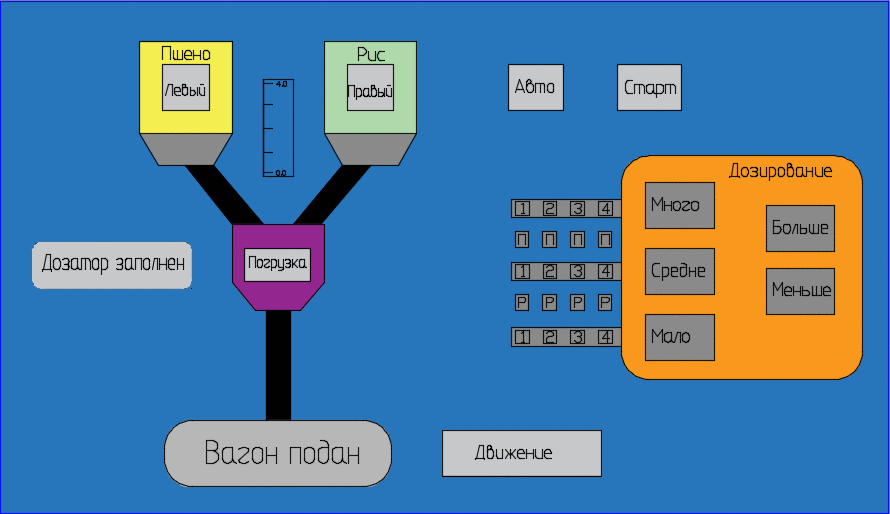
Рисунок 6 – Монтажная схема стенда погрузочного комплекса шахты
(анимация: 7 кадров, 8 циклов, 277кб)
4. Эксплуатационные требования к системе автоматизации погрузочным комплексом
При эксплуатации системы автоматизации погрузочного комплекса поверхности шахты должны быть соблюдены требования Правил безопасности в угольных шахтах.
Требования следующие:
- перед вводом в эксплуатацию аппаратуры автоматизации обслуживающий персонал обязан ознакомиться с правилами технической эксплуатации аппаратуры;
- при эксплуатации в шахте запрещается делать разборку, ремонт и регулировку элементов, за исключением мероприятий, предусматривающих замену ТЭС;
- при монтаже, наладке или ремонте аппаратуры, когда открывается оболочка, необходимо перевести блокирующий разъединитель пускателя, который питает устройство автоматизации, в положения
Отключенное
;
При использовании измерительных приборов необходимо соблюдение следующих условий:
- при измерениях в цепях с напряжением свыше 42В (подключение ППИ) следует включать и отключать прибор при исключенном напряжении в исследуемой цепи;
- недопустимо переключение устройства с одного вида измерения на другой, а также переключение диапазонов измерений без отключения от исследуемой схемы;
- подключать устройство к исследуемой цепи с помощью щупов одной рукой, держась за изолирующую втулку щупа. Другая рука должна быть свободной во избежание прохождения электрического тока через организм человека;
- при исследовании электрической схемы устройства нужно располагать так, чтобы при снятии показаний была исключена опасность прикосновения к частям схемы, которые находятся под напряжением.
Монтаж аппаратуры содержит в себе проведение работ, связанных с подачей напряжения питания, которое служит причиной необходимости отключения устройства питания, то есть работы производятся со снятием напряжения[7]. Поэтому, при проведении таких работ необходимо соблюдать Инструкции по безопасному проведению работ в подземных электроустановках
, что состоит в следующем:
- перед началом проведения работ со снятием напряжения необходимо сделать необходимые отключения и принять меры, которые препятствуют подаче напряжения к месту работы вследствие ошибочного или невольного включения коммутационных аппаратов;
- вывесить плакаты
Не включать – работают люди
на приводах коммутационных аппаратов, с помощью которых может быть подано напряжение к месту работы, установить при необходимости ограждения; - проверить показателем напряжения отсутствие напряжения на токопроводящих частях.
Пожарная безопасность в месте установки аппаратуры автоматизации , количество и виды технических средств противопожарной защиты,
используемые огнетушащих средства, источники и средства подачи воды для пожаротушения, запас специальных огнетушащих веществ (порошковых, пенных и др.)
определяются Инструкцией по противопожарной защите угольных шахт (далее – ГНАОТ 1.1.30-5.34-96), утвержденной приказом Госнадзорохрантруда от 18.01.96 №7, ГНАОТ 11.1.30-5.18-96, КД 12.01.401-96, а также действующими Правилами безопасности в угольных шахтах
[8].
Выводы
В результате выполнения данного дипломного проекта были разработаны критерии управления работой погрузочного комплекса с применением устройства автоматизированного управления погрузочным комплексом, по которым достигается его оптимальная работа.
Приняв за основу эти критерии управления была разработано устройство автоматизированного контроля веса и направление движения угля, которое удовлетворяет заявленным к ней требованиям. То есть, устройство автоматизации позволяет контролировать работу погрузочного комплекса в соответствии с поставленной задачей оптимального функционирования.
Разработана структурная и принципиальная схемы устройства, которые отображают структуру построения устройства. Разработан алгоритм, который описывает последовательность работы устройств.
И, как результат проведенной работы было разработано устройство автоматизированного контроля погрузки угля на поверхностном комплексе шахты.
Внедрение данного устройства на шахте экономически обосновано.
При написании данного реферата магистерская работа еще не завершена. Окончательное завершение: июнь 2020 года. Полный текст работы и материалы по теме могут быть получены у автора или его руководителя после указанной даты.
Список источников
- Батицкий В. А., Куроедов В. И., Рыжков А. А. Автоматизация производственных процессов и АСУ ТП в горной промышленности. М.: Недра, 1991. 303 с.
- Попович Н. Г., Данильчук Г. И., Лисовский В. С., Янчук Г. М. Автоматизация производственных процессов угольных шахт–К.: Вища школа, 1978. 336 с.
- Авласенко Ю. Г., Ковалевский М. М. Автоматизация шахтных установок. Государственное издательство технической литературы УССР, Киев 1958. 296 с.
- Толпежников Л. И. Автоматическое управление процессами шахт и рудников / Л. И. Толпежников – Москва: Недра, 1985. 352 с.
- Бедняк Г. И. Автоматизация производства на угольных шахтах / Г. И. Бедняк, В. А. Ульшин, В. П. Довженко и др. Киев: Техника, 1989. – 272 с.
- Мелькумов Л. Г. Автоматизация технологических процессов угольных шахт /Л. Г. Мелькумов, Н. Я. Лазукин, Б. Х. Богопольский, Р. Л. Розенберг. Москва: Недра, 1973. 352 с.
- Каминский М. Л. Монтаж приборов и систем автоматизации / М. Л. Каминский, В. М. Каминский. Москва: Высшая школа, 1997. 304 с.
- НПАОП 10.0-5.18-04. Инструкция по противопожарной защите угольных шахт