Реферат за темою випускної роботи
Зміст
- Вступ
- 1. Актуальність теми
- 2. Мета і задачі дослідження, заплановані результати
- 3. Огляд досліджень та розробок
- 3.1 Технологічний процес навантажувального комплексу як об'єкт автоматизації
- 3.2 Огляд відомих технічних рішень по автоматизації навантажувального комплексу шахти
- 3.3 Розробка алгоритму роботи і схемних рішень пристрої автоматизації навантажувального комплексу поверхні шахти
- 3.4 Розробка алгоритму роботи і монтажної схеми демонстраційного стенда навантажувального комплексу поверхні шахти
- 4. Експлуатаційні вимоги до системи автоматизації навантажувального комплексу
- Висновки
- Перелік посилань
Вступ
Технологічний комплекс поверхні шахти (ТКПШ) – це заверщают етап у видобутку корисних копалин в шахті, і з цього один з найважливіших. ТКПШ – є комплексом гірничо-технічних споруд і будівель на поверхні шахти, що забезпечує роботу її підземного господарства, а також складування, переробку (при наявності відповідних комплексів) і відправку споживачам видобутої сировини. У функції технологічного комплексу поверхні шахти входять: провітрювання шахти, подача в шахту електроенергії, стисненого повітря, тепла, обладнання та матеріалів; спуск і підйом людей; приймання видобутої корисної копалини і порожньої породи; сортування та збагачення корисних копалин; тимчасове зберігання продукції і відправка її споживачам; відвалоутворення порожніх порід; підготовка закладних матеріалів, технологічної води (на гідрошахтах); ремонт гірських механізмів і обладнання; складування матеріалів, виробів і механізмів; обслуговування трудящих шахти; забезпечення роботи адміністративно-управлінських і інженерно-технічних служб.
1. Актуальність теми
На сучасному етапі розвитку народного господарства велика увага приділяється проблемам підвищення ефективності використання технологічного і транспортного устаткування, поліпшення якості технологічних процесів, підвищення достовірності обліку матеріальних цінностей, і звичайно, мінімізація втручання людини в технологічні процеси. Однією з таких проблем у вугільній промисловості є вдосконалення вугільновантажних робіт на залізничному транспорті промислових підприємств. Навантаження вугілля в залізничні вагони є завершальною ланкою в технологічній схемі вугільного комплексу поверхні шахт, і, очевидно, являє собою дуже важливий об'єкт для можливої автоматизації. З метою підвищення ефективності навантажувальних робіт розроблено ряд заходів, спрямованих на поліпшення процесів навантаження і обліку вугілля в залізничні вагони [1]. Результатом виконаних робіт стало створення автоматизованих вугільновантажних комплексів. Необхідність впровадження подібних установок визначається тим, що виробнича потужність новоспоруджуваної і реконструюються вугільних підприємств досягає декількох мільйонів тонн вугілля в рік, отже, обсяг щодобового відвантаження вугілля становить кілька сот вагонів на добу.
2. Мета і задачі дослідження, заплановані результати
Мета проектування – зниження експлуатаційних витрат на навантаження вугілля за рахунок збільшення продуктивності і виключення аварійних ситуацій шляхом розробки і застосування системи автоматизації навантажувального комплексу поверхні шахти.
Основні завдання дослідження:
- аналіз навантажувального комплексу як об'єкта автоматизації;
- аналіз існуючих розробок по автоматизації навантажувального комплексу поверхні шахти;
- розробка математичної моделі автоматизованого управління;
- розробка схемних рішень. Структурна, функціональна схема пристрою автоматизації, алгоритм роботи;
- практична реалізація системи автоматизованого управління. Розробка мнемосхеми автоматизованого управління вантажним комплексом.
- розробка заходів щодо безпечної та безаварійної експлуатації розробленого пристрою.
Об'єкт дослідження: Основні технологічні процеси поверхні шахти.
Предмет дослідження: Система автоматизації навантажувального комплексу поверхні шахти. Принцип алгоритмізації навантаження.
3. Огляд досліджень та розробок
3.1 Технологічний процес навантажувального комплексу як об'єкт автоматизації
Транспортування вугілля вантажним комплексом являє собою складний багатофункціональний процес, який містить сукупності взаємопов'язаних самостійних процесів, основними з яких є: навантаження вугілля у вагони, вантаження вугілля в ряд бункерів і в автотранспорт, визначення фракції завантаженого вугілля, визначення обсягу вугілля в бункерах, запобігання втрат викопного при транспортуванні[ 2 ].
Для здійснення навантаження вугілля в залізничні вагони використовуються комплекси навантаження вугілля в залізничні вагони (КНВ). Комплекс навантаження вугілля в залізничні вагони (вугільновантажних комплекс) являє собою пов'язане загальним технологічним процесом поєднання механізмів і пристроїв, призначених для пересування вагонів, подачі вугілля від місць його видобутку або попереднього зберігання безпосередньо до завантаження у вагони на одному залізничній колії (без проміжного акумулювання), дозування та зважування.
На рисунку 1 наведена технологічна схема автоматизованого вугільновантажного комплексу.
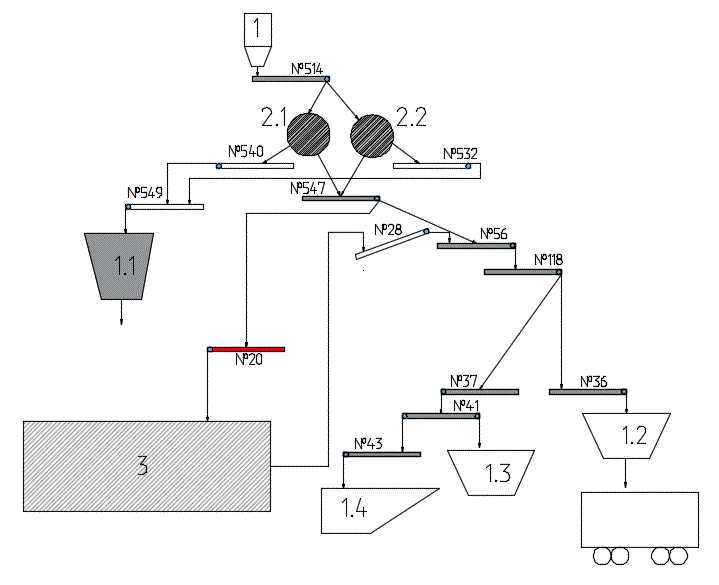
Рисунок 1 – Технологічна схема автоматизованого вугільновантажного комплексу
Умовні позначення:
1 – Бункер скіпового ствола; 1.1 – автомобільний бункер; 1.2 – ж.д. бункер; 1.3 – бункер нової котельні; 1.4 – бункер старої котельні; 2.1 – гуркіт ГЦЛ-1А; 2.2 – гуркіт ГЦЛ; 3 – аварійний склад вугілля; №20, 28, 36, 37, 41, 43, 56, 118, 514, 532, 540, 547, 549 – стрічкові конвеєри.
КНВ включає в себе механізми, що формують потік вугілля (живильники, затвори) з місць його акумулювання, або транспортні механізми, що доставляють вугілля на навантаження безпосередньо від видобувних агрегатів; містить механізми потоково-транспортної системи (ПТС) і пристрої навантаження вугілля та пересування вагонів (маневрові пристрої МП). Кожен залізничну колію, на якому здійснюється завантаження вагонів вугіллям, називають фронтом навантаження, або вантажним фронтом. Під час навантаження вугілля у вагони зазвичай виконуються чотири основні операції, які визначають характер процесу: пересування вагонів, подача вугілля, дозування, вимірювання кількості [3].
Умови автоматизації технологічних комплексів залежать від наступного:
- Способу контролю заповнення вагона (по масі завантаженого вугілля або за обсягом кузова вагона);
- Способу рівномірного розподілу вугілля в вагоні (шляхом переміщення вагона в процесі його заповнення або за допомогою пересувного завантажувального конвеєра);
- Способу транспортування вугілля (з безперервною навантаженням вугілля у вагони або з попередніми накопиченням);
- Організації навантаження складу (за допомогою конвеєра з бункера або по безбункерной схемою);
- Сортності вугілля.
3.2 Огляд відомих технічних рішень по автоматизації навантажувального комплексу шахти
Технологічні комплекси навантаження вугілля відрізняються різноманітністю техніки і технічних схем, що ускладнює вирішення завдання автоматизації. Технологічний комплекс включає в себе 3 основні групи обладнання: завантажувальні пристрої, механізми для просування вагонів, ваги для зважування.
Завантажувальні пристрої служать для виконання основних операцій завантаження вугілля у вагони і рівномірного розподілу вугілля в них. До складу завантажувальних пристроїв входять стаціонарні і самохідні конвеєри, навантажувальні жолоби і бункерні затвори.
Для просування вагонів застосовують візки і маневрові пристрої. Для зважування відвантаженого вугілля служать різні вагонні ваги.
Автоматизований комплекс механізмів КПА розроблений інститутами «Гипроуглемаш» та Гіпроуглеавтоматізація
[4].
До складу комплексу входять:
- Пересувний завантажувальний конвеєр-бункер продуктивністю 2 тисяч т/год, оснащений транспортуючих органом скребкового типу і висувним жолобом на головної частини, який переміщується за допомогою регульованого приводу по рейковому шляху.
- Маневровое пристрій з штовхачем, взаємодіючим із зчіпками завантаження і попереднього вагонів.
- Пристрій ущільнення з катком, опускається за допомогою лебідки на поверхню конусної вершини вугілля, і ущільнюючим його під час переміщення складу.
- Автоматизовані вагонні ваги платформні типу 699П200А, що забезпечують управління процесом вагового дозування завантаження вугілля і видачу документів про результати зважування в кінці циклу навантаження.
- Апаратура управління.
На рисунку 2 наведено автоматизований комплекс механізмів КПА
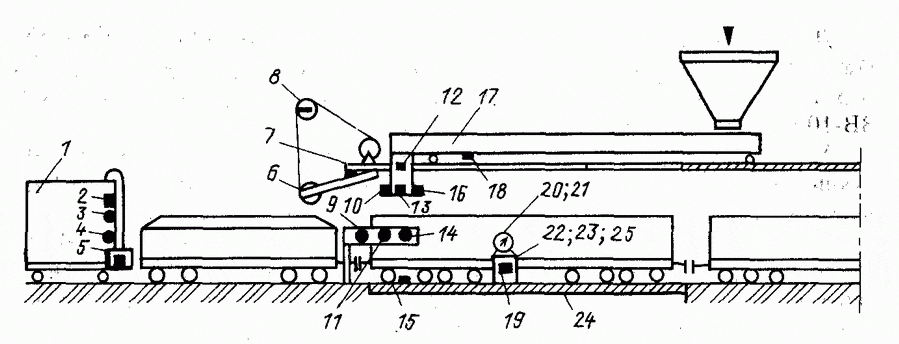
Рисунок 2 – Автоматизований комплекс механізмів КПА
За допомогою засобів автоматизації контролюються наступні положення механізмів комплексу і завантаження вагона: нижнє положення тягової балки – 5, вихідне положення програмного пристрою ваг – 22, стан вагона щодо ковзанки – 9, натяг каната лебідки ковзанки – 8, проміжне положення конвеєра-бункера – 18, положення вагонів щодо ковзанки – 14, верхнє положення ковзанки – 7, переклад штовхача маневрового пристрою на знижену швидкість – 11, стан вагона на вагах – 15, нижнє положення жолоби – 13, положення механізмів ваг в робочому стані – 19, положення конвеєра щодо вагона – 10, робоче положення програмного пристрою ваг – 25, верхнє положення тягової балки – 2, рівень вугілля – 16, переклад штовхача маневрового пристрою на знижену швидкість – 4, положення тягової балки щодо зчіпки вагонів – 3, закінчення завантаження вагона – 20, верхнє положення жолоби – 12, закінчення реєстрації результатів навантаження – 21, фіксоване положення механізмів ваг – 23[5].
Система автоматизації технологічного комплексу забезпечує: автоматичне виконання заданої послідовності технологічних операцій, автоматичне регулювання процесу заповнення і дозування вагонів з метою компенсації коливань ваги та інтенсивності подачі вугілля, завантаження вагонів різних типорозмірів і розташованих в складі в будь-якій послідовності. Оператор вводить в систему управління програму чергового завантаження вагону що забезпечує автоматичний режим. Програма набирається на пульті управління періодично під час пересування складів. Програмою задається тип завантаження вагона, маса вагона інвентарний номер. Оператор також подає первинну команду на пуск технологічного комплексу, спостерігає за режимом навантаження, контролює стан і вносить зміни в положення окремих механізмів (при розузгодженні їх спільної роботи).
Технологічний комплекс працює наступним чином. Перед початком роботи комплексу на пункт навантаження локомотивом подається склад порожніх вагонів з зупинкою 1-го вагону в зоні дії маневрового пристрою. Маневровое пристрій зрушує складу до установки першого вагона на платформу ваг, потім починається завантаження вугіллям вагона за допомогою конвеєра-бункера. Перемикач вибору режиму роботи на пульті управління знаходиться в положенні Автоматичний режим
. Оператор здійснює пуск механізмів технологічного комплексу поточно-транспортної системи й механізмів контролю якості. По закінченні циклу завантаження першого вагона автоматично включається привід маневрового пристрої для зрушування навантаженого вагона з платформи ваг, потім – привід опускання ковзанки ущільнювача, прокатывающегося по поверхні вугілля при русі вагона. У цей момент оператор при необхідності (інший тип вагона) запроваджує програму завантаження вагона.
Після підйому ковзанки маневровое пристрій автоматично переводиться в режим зниженої швидкості дотягування для забезпечення точної зупинки другого (порожнього) вагона на платформі ваг. Після цього включається механізм опускання жолоби до певного рівня і механізм переміщення конвеєра для установки його в початкове положення для початку навантаження. Одночасно піднімається тягова балка маневрового пристрої, ваги наводяться в робочий стан і на їх задатчике дози оператор встановлює необхідне значення. Включається конвеєр, вугілля заповнює вагон. По закінченню заповнення обсягу первинного конуса вугілля включається привід переміщення конвеєра. Маневровое пристрій при цьому переміщається в режимі холостого ходу, проходячи над завантаженим раніше першим вагоном. Після завантаження вагонів автоматично відключається привід конвеєра, включається привід підйому жолоби, фіксується маса вугілля у вагоні і дані з ваг видаються на цифропечатающее пристрій. Тягова балка опускається і включається привід переміщення конвеєра-бункера для установки його в початкове положення. Під час руху конвеєра вугілля накопичується на його транспортуючому органі. Завантаження вагона закінчується по сигналу з ваг після досягнення значення маси вагона. Операції завантаження вугілля повторюються до повного завантаження останнього вагона складу. Конвеєр зупиняється в положенні закінчення циклу. Останній вагон з допомогою маневрового пристрою зрушується з платформи ваг. Каток-ущільнювач по закінченні ущільнення вугілля в останньому вагоні підіймається у верхнє положення і стопориться[6].
3.3 Розробка алгоритму роботи і схемних рішень пристрої автоматизації навантажувального комплексу поверхні шахти
На початковому етапі роботи пристрою здійснюється аналіз стану вагона. Далі здійснюється аналіз перевірки тензодатчика ЗД бункера, в залежності від якого відбувається процес завантаження вагона. Якщо в бункері немає необхідного рівня заповнення то включається конвеєр №514. Після цього відкривається засувка скіпового бункера, з витримкою часу. На наступному етапі включається гуркіт, і ланцюжок конвеєрів (№547, 56, 118, 36). Далі проводиться аналіз конвейерныхъ ваг устанвленных на конвеєрі №36, і очікується сигнал про наявність вантажу на стрічці, після чого проводиться закриття шибера бункера скіпового ствола. Після чого очікується спрацьовування коцевика встановленого на конвеєрі №514, і вимикання даного конвеєра. Потім з витримкою часу відбувається очікування відпрацювання гуркоту, шляхом аналізу конвеєрних ваг. При наявності вантажу на вагах гуркіт ще включений, при його відсутності – вимикається гуркіт. Після цього відбувається почергове відключення конвеферов (№547, 56, 118, 36). Процес доставки корисної копалини в ЗД бункер на цьому завершено.
Основний робочий цикл. На початку роботи основного алгоритму виконується перевірка тензодатчика основного бункера, при достатній заповнювання технологічна ланцюжок навантаження не запускається, при зворотному відбувається введення оператором № технологічного ланцюжка. І її подальша відпрацювання.
На основі алгоритму були розроблені структурна і функціональна схеми пристрою автоматизації навантажувального комплексу
На рисунку 3 приведена структурна схема пристрою автоматизації навантажувального комплексу
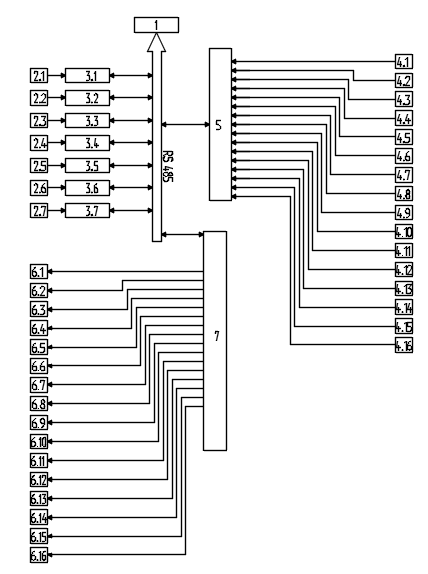
Рисунок 3 – Структурна схема пристрою автоматизації навантажувального комплексу
На структурній схемі прийняті наступні позначення:
- ПЛК – 63 – контролер програмований логічний;
- ТД – тензодатчик (бункерні і конвеєрні ваги);
- МВ110-1ТД – тензопреобразователь сигналу
- ДП – датчик положення;
- МВ110-16Д – модуль дискретного вводу (розширювальний блок) ;
- КР – керуюче реле
- МВ110-16К – модуль дискретного виводу.
На рисунку 4 приведена функціональна схема пристрою автоматизації навантажувального комплексу.
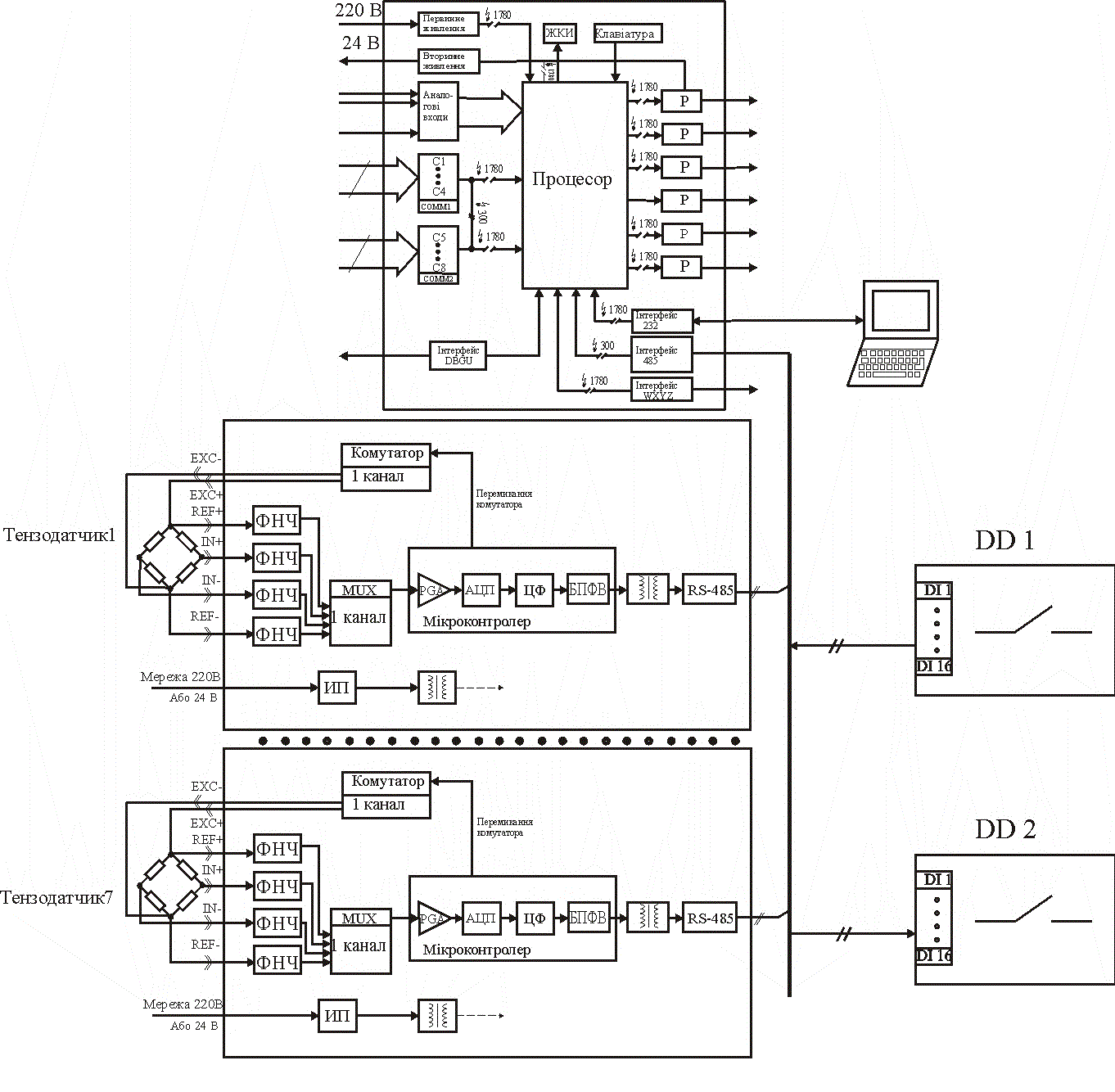
Рисунок 4 – Функціональна схема пристрою автоматизації навантажувального комплексу
3.4 Розробка алгоритму роботи і монтажної схеми демонстраційного стенда навантажувального комплексу поверхні шахти
Опис роботи алгоритму:
Початок роботи стенду управляється оператором, а саме розмиканіем контакту, і подачі напруги. Платформа з розташованими на ній вагонами приводиться в рух двигуном. Платформа рухається до тих пір поки не спрацьовує індуктивний датчик зчитування нумерації вагонів, встановлений безпосередньо на задвіжде основного бункера, що забезпечує точне розташування вагона під основним бункером. Після спрацьовування датчика, платформа зупиняється, для навантаження. Процес вантаження починається установкою рівня заповнення основного бункера оператором на ПЛК, за допомогою оптичного датчика в основному бункері. Потім оператор вибирає 1 з додаткових бункерів і відкриває засувку обраного бункера, після чого основний бункер наповнюється до виставленого рівня, і при його досягненні, засувка закривається. Оператор відкриває засувку основного бункера, і вміст висипається в вагон, після цього засувка закривається, і датчик рівня встановлюється в початкове положення. Далі процес повторюється до тих пір, поки кількість вагоном менше 4. При заповненні всіх наявних вагонів, платформа заїжджає в кінцеве положення, звідки вона повертається включенням тумблера в початкове положення.
На рисунку 5 наведено алгоритм роботи блоку управління стенду навантажувального комплексу шахти.
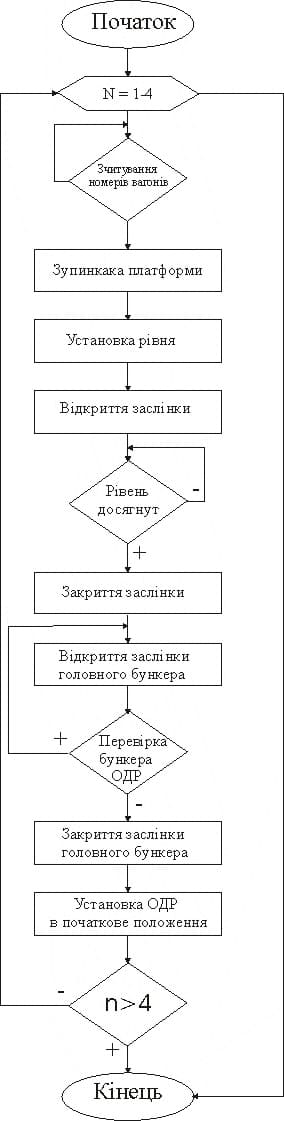
Рисунок 5 – Алгоритм работы блока управления стенда погрузочного комплекса шахты
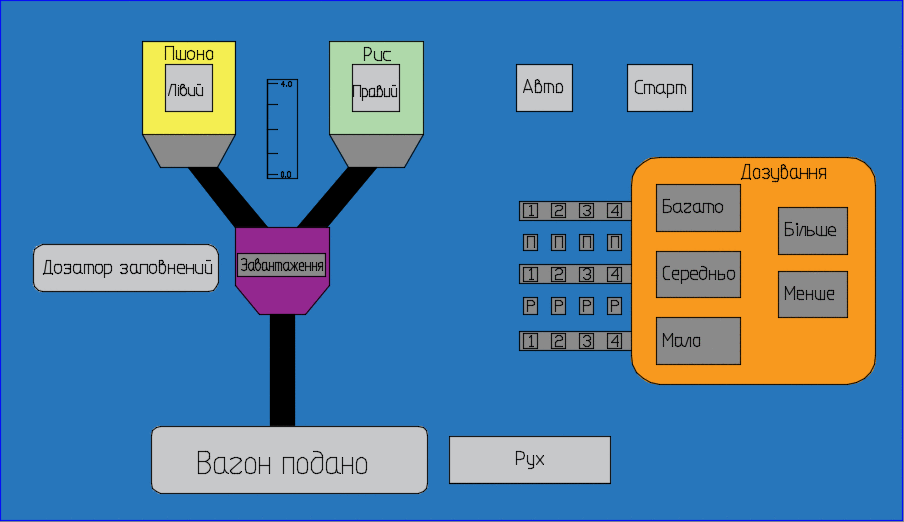
Рисунок 6 – Монтажна схема стенду навантажувального комплексу шахти
(анимация: 7 кадров, 8 циклов, 276кб)
4. Експлуатаційні вимоги до системи автоматизації навантажувального комплексу
При експлуатації системи автоматизації навантажувального комплексу поверхні шахти повинні бути дотримані вимоги Правил безпеки у вугільних шахтах.
Вимоги наступні:
- перед введенням в експлуатацію апаратури автоматизації обслуговуючий персонал зобов'язаний ознайомитися з правилами технічної експлуатації апаратури;
- при експлуатації в шахті забороняється робити розбирання, ремонт і регулювання елементів, за винятком заходів, що передбачають заміну ТЕС;
- при монтажі, наладці або ремонті апаратури, коли відкривається оболонка, необхідно перевести блокуючий роз'єднувач пускача, який живить пристрій автоматизації, в положення
Вимкнене
;
При використанні вимірювальних приладів необхідно дотримання наступних умов:
- при вимірах в ланцюгах з напругою понад 42В (підключення ППІ) слід включати і відключати прилад при виключеному напрузі в досліджуваної ланцюга;
- неприпустимо перемикання пристрою з одного виду вимірювання на інший, а також перемикання діапазонів вимірювань без відключення від досліджуваної схеми;
- підключати пристрій до досліджуваної ланцюга з допомогою щупів однією рукою, тримаючись за ізолюючу втулку щупа. Інша рука повинна бути вільною, щоб уникнути проходження електричного струму через організм людини;
- при дослідженні електричної схеми пристрою потрібно розташовувати так, щоб при знятті показань була виключена небезпека дотику до частин схеми, які знаходяться під напругою.
Монтаж апаратури містить у собі проведення робіт, пов'язаних з подачею напруги живлення, яке служить причиною необхідності відключення пристрою живлення, тобто роботи виконуються зі зняттям напруги[7]. Тому, при проведенні таких робіт необхідно дотримуватися Інструкції з безпечного проведення робіт у підземних електроустановках
, що складається в наступному:
- перед початком проведення робіт зі зняттям напруги необхідно зробити необхідні відключення і вжити заходів, що перешкоджають подачі напруги до місця роботи внаслідок помилкового або мимовільного включення комутаційних апаратів;
- вивісити плакати
Не включати – працюють люди
на приводах комутаційних апаратів, з допомогою яких може бути подано напругу до місця роботи, встановити при необхідності огородження; - перевірити показником напруги відсутність напруги на струмопровідних частинах.
Пожежна безпека в місці установки апаратури автоматизації , кількість і види технічних засобів протипожежного захисту,
використовувані вогнегасних засоби, джерела і засоби подавання води для пожежогасіння, запас спеціальних вогнегасних речовин (порошкових, пінних та ін)
визначаються Інструкцією з протипожежного захисту вугільних шахт (далі – ДНАОП 1.1.30-5.34-96), затвердженою наказом Держнаглядохоронпраці від 18.01.96 №7, ДНАОП 11.1.30-5.18-96 КД 12.01.401-96, а також чинними Правилами безпеки у вугільних шахтах
[8].
Висновки
В результаті виконання даного дипломного проекту були розроблені критерії управління роботою вантажного комплексу з застосуванням пристрою автоматизованого управління вантажним комплексом, за якими досягається його оптимальна робота.
Прийнявши за основу ці критерії управління була розроблено пристрій автоматизованого контролю ваги і напрямок руху вугілля, яке задовольняє заявленим до неї вимогам. Тобто, пристрій автоматизації дозволяє контролювати роботу навантажувального комплексу відповідно до поставленим завданням оптимального функціонування.
Розроблено структурну і принципова схеми пристрою, які відображають структуру побудови пристрою. Розроблено алгоритм, який описує послідовність роботи пристроїв.
І, як результат проведеної роботи було розроблено пристрій автоматизованого контролю навантаження вугілля на поверхневому комплексі шахти.
Впровадження даного пристрою на шахті економічно обгрунтовано.
При написанні даного реферату магістерська робота ще не завершена. Остаточне завершення: червень 2020 року. Повний текст роботи та матеріали по темі можуть бути отримані у автора або його керівника після зазначеної дати.
Перелік посилань
- Батицкий В. А., Куроедов В. И., Рыжков А. А. Автоматизация производственных процессов и АСУ ТП в горной промышленности. М.: Недра, 1991. 303 с.
- Попович Н. Г., Данильчук Г. И., Лисовский В. С., Янчук Г. М. Автоматизация производственных процессов угольных шахт–К.: Вища школа, 1978. 336 с.
- Авласенко Ю. Г., Ковалевский М. М. Автоматизация шахтных установок. Государственное издательство технической литературы УССР, Киев 1958. 296 с.
- Толпежников Л. И. Автоматическое управление процессами шахт и рудников / Л. И. Толпежников – Москва: Недра, 1985. 352 с.
- Бедняк Г. И. Автоматизация производства на угольных шахтах / Г. И. Бедняк, В. А. Ульшин, В. П. Довженко и др. Киев: Техника, 1989. – 272 с.
- Мелькумов Л. Г. Автоматизация технологических процессов угольных шахт /Л. Г. Мелькумов, Н. Я. Лазукин, Б. Х. Богопольский, Р. Л. Розенберг. Москва: Недра, 1973. 352 с.
- Каминский М. Л. Монтаж приборов и систем автоматизации / М. Л. Каминский, В. М. Каминский. Москва: Высшая школа, 1997. 304 с.
- НПАОП 10.0-5.18-04. Инструкция по противопожарной защите угольных шахт