Abstract
- Introduction
- 1. Theme urgency
- 2. Goal and tasks of the research, expected results
- 3. Review of research and development
- 3.1 Technological process of the loading complex as an object of automation
- 3.2 Overview of known technical solutions for automation of the mine loading complex
- 3.3 Development of the algorithm of operation and circuit solutions for the automation of the mines surface loading complex
- 3.4 Development of the algorithm of operation and wiring diagram of the demonstration stand of the mines surface loading complex
- 4. Operational requirements for the automation system of the loading complex conclusions
- Conclusion
- References
Introduction
Technological complex of a surface mine (TCPS) – this is the concluding stage in the extraction of the mineral in the mine, and this is one of the most important. TKS – is a complex of mining-technical constructions and buildings on the surface of the mine, providing its underground economy, as well as the storage processing (with appropriate facilities) and sent to the consumers of raw materials. In function of the technological complex surface of the mine included: the ventilation of the mine, the flow into shaft power, compressed air, heat, equipment and materials; the descent and ascent of the people; acceptance of the extracted mineral and gangue; sorting and enrichment of minerals; temporary storage of products, and sending them to consumers; dumping tailings; prepare filling materials, process water (at giproshaht); repair of mining machinery and equipment; storage of materials, products and mechanisms; maintenance of the mine workers; management of the administrative and technical services.
1. Theme urgency
At the present stage of development of the national economy, much attention is paid to the problems of increasing the efficiency of using technological and transport equipment, improving the quality of technological processes, increasing the reliability of accounting for material values, and of course, minimization of human intervention in technological processes. One of the problems in the coal industry is the improvement of coal loading works on industrial railway transport. The loading of coal in railway cars is the final link in the technological scheme coal complex surface mine, and, obviously, is a very important object for possible automation. In order to increase efficiency loading operations, a number of measures have been developed aimed at improving the loading and accounting of coal in railway cars [1]. The result of the work was the creation of automated coal loading complexes. The need to implement such installations is determined by that the production capacity of new-built and reconstructed coal enterprises reaches several million tons of coal per year, therefore the volume of daily coal shipment is several hundred wagons per day.
2. Goal and tasks of the research
The purpose of the design – reduced operating costs related to loading of coal by increasing productivity and eliminating emergency situations by the development and application of automation systems loading complex surface of the mine.
The main objectives of the study:
- analysis of the loading complex as the object of automation;
- analysis of existing research on the automation of the loading of the complex surface of the mine;
- development of a mathematical model for automated control;
- circuitry development. Structural, functional diagram of the device of the automation algorithm;
- practical implementation of automated control system. Development mimic automated control of the loading complex.
- development of measures for safe and trouble-free operation of the developed device.
Object of study: Basic technological processes of surface mine.
Investigation Subject: System automation of loading of the complex surface of the mine. The principle of algorithmization of loading.
3. Review of research and development
3.1 Technological process of the loading complex as an object of automation
Transportation of coal by the loading complex is a complex multifunctional process containing sets of interconnected independent processes, the main of which are: loading coal into wagons, loading coal into a number of bins and into motor vehicles, determining the fraction of loaded coal, determining the amount of coal in bins, preventing transportation loss[2].
To carry out the loading of coal into railway cars, complexes for loading coal into railway cars (KPU) are used. The complex for loading coal into railway wagons (coal loading complex) is a combination of mechanisms and devices associated with the general technological process designed to move the wagons, supply coal from the places of its extraction or preliminary storage directly before loading it into the wagons on the same railway line (without intermediate storage), dosing and weighing.
Figure 1 shows the technological scheme of an automated coal loading complex.
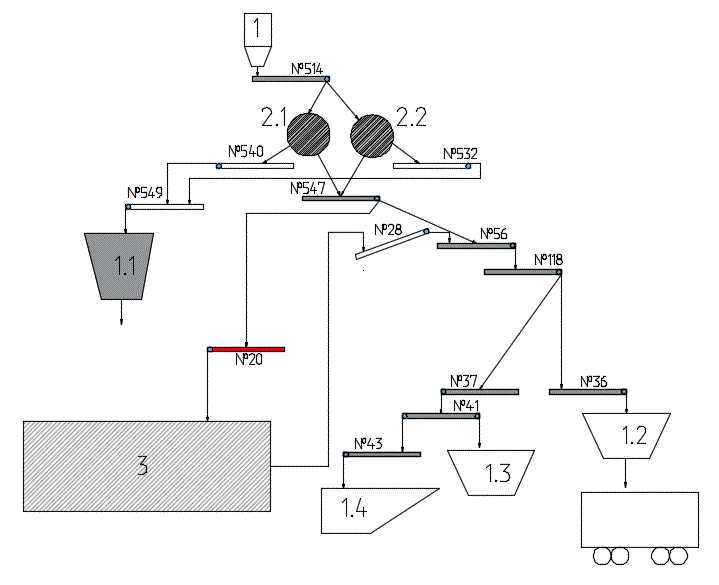
Figure 1 – Technological scheme of an automated coal loading complex
Legend:
1 – Skip barrel hopper; 1.1 – car hopper; 1.2 – railroad hopper; 1.3 – hopper of a new boiler room; 1.4 – bunker of an old boiler room; 2.1 – rumble GTsL-1A; 2.2 – rumble of GTsL; 3 – emergency coal storage; №20, 28, 36, 37, 41, 43, 56, 118, 514, 532, 540, 547, 549 – belt conveyors.
KPU includes mechanisms that form the flow of coal (feeders, gates) from the places of its accumulation, or transport mechanisms that deliver coal for loading directly from the mining units; contains the mechanisms of the flow-transport system (PTS) and coal loading and wagon movement devices (MU shunting devices). Each railway line on which coal is loaded with cars is called a loading front, or cargo front. When loading coal into wagons, four basic operations are usually carried out that determine the nature of the process: moving wagons, supplying coal, dosing, measuring quantity[3].
The conditions for automation of technological complexes depend on the following:
- A method of controlling the filling of a car (by weight of coal loaded or by car body volume);
- The method of uniform distribution of coal in the car (by moving the car during its filling or using a mobile loading conveyor);
- A method of transporting coal (with continuous loading of coal into wagons or with preliminary accumulation);
- Organization of loading the composition (using a conveyor from a hopper or according to a hopper-free scheme);
- Grades of coal.
3.2 Overview of known technical solutions for automation of the mine loading complex
Technological complexes of coal loading differ in the heterogeneity of equipment and technical schemes, which makes it difficult to solve the automation problem. The technological complex includes 3 main groups of equipment: loading devices, mechanisms for promoting cars, scales for weighing.
Boot device used to perform the basic operations of loading coal into wagons and uniform distribution of coal in them. Part of boot devices include stationary and self-propelled conveyors, loading chutes and hopper gates.
To promote used cars trucks and shunting of the device. For weighing of loaded coal wagon scales are different.
Automated complex mechanisms KPA developed institutions Giprouglemash and Gipoglikemicescoe
[4].
The complex includes:
- Mobile feed conveyor-hopper capacity of 2 thousand t/h, equipped with the transporting body of the scraper type, and a sliding groove on the head part, which is moved by means of an adjustable drive on the track;
- Shunting device with a pusher interacting with a coupling of the downloadable and previous cars;
- The device seal to the ice rink, which is lowered with a winch on the surface of the conical top of the coal, and sealing it during the movement of the whole.
- Automated wagon platform scales type 699П200А that control the process of dosing the weight of the loaded coal and the delivery of documents on the results of weighing in the end of a cycle of loading.
- Control equipment.
Figure 2 shows an automated complex of KPA mechanisms.
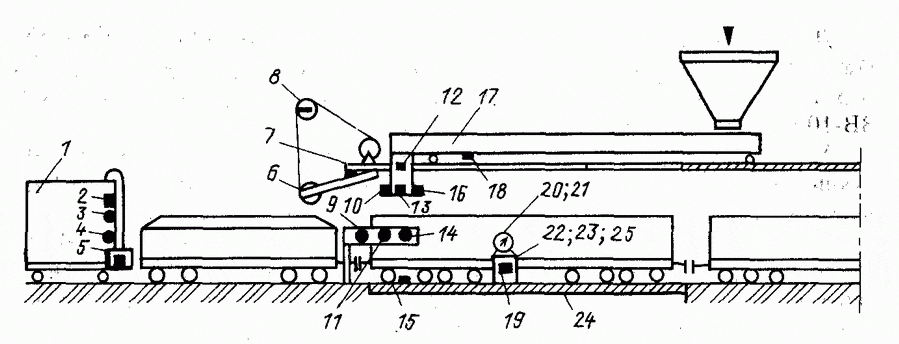
Figure 2 – Automated complex of KPA mechanisms
With the help of automation are controlled by the following provisions of the mechanisms of the complex and load the wagon: the lower position of the traction beam – 5, the initial position of software weighting device – 22, the position of the car relative to the rink – 9, the tension of the hoist rope rink – 8, an intermediate position of the conveyor-hopper – 18, the carriage position relative to the rink – 14, the upper position of the rink – 7, a transfer pusher shunting device to a lower speed – 11, position of the car on the scales – 15, the lower position of the gutter – 13, the position of the arrangements of scales in working condition – 19, the position of the conveyor relative to the carriage – 10, software operating position of the weighting device – 25, the upper position of the traction beam – 2, the level of coal – 16, a transfer pusher shunting device to a lower speed – 4, the position of the beam relative to the traction coupling cars – 3, the load of the car – 20, the upper position of the gutter – 12, ends the recording of the results of loading – 21, the fixed position of the mechanisms of the scales – 23[5].
Automation system provides: automatic execution of the specified sequence of technological operations, automatic control of filling and dosing of cars in order to compensate for fluctuations of weight and flow rate of coal, loading of wagons of various sizes and located in the composition in any order. The operator enters into the control system program download next train providing an automatic mode. The program is typed in on the remote control periodically during the movement of trains. The program sets a type of a loaded car, the car weight inventory number. The operator also takes the initial start command of the technological complex, watching the loading mode, monitors the status of and changes in provisions separate arrangements (subject to misalignment of their joint work).
Technological complex is as follows. Before beginning work at the point of loading the locomotive served the composition of the empty cars to the stop of the 1st car in the area of the shunting device. Shunting device moves the part to the installation of the first car onto the weighing platform, and then starts to load the coal car with conveyor-hopper. Switch operation mode selector on the remote control is in the Auto mode
. The operator performs a start-up technological complex continuous-handling systems and quality control mechanisms. At the end of the boot cycle the first car automatically turns on shunting the drive device for moving the loaded carriage from the platform of the scales, and then – drive lowering rink sealer, rolled on the surface of the coal when driving the car. At this point the operator when needed (another type of car) insert the boot program of the second carriage.
After lifting the rink shunting unit is automatically set to a lower speed dotyagivaya to ensure the accurate stop of the second (empty) wagon on a platform scale. Then turn on the mechanism of the lowering of the chute to a certain level and the mechanism of movement of the conveyor for installation in original position to start loading. At the same time rises the traction beam shunting devices, scales are in working condition and the set dose, the operator establishes the desired value. Included conveyor, coal fills the car. At the end of the filling volume of the primary cone coal turn drive the movement of the conveyor. Shunting device is moved to idle, passing over previously loaded the first wagon. After loading the cars automatically shut off the conveyor drive includes the drive of the lifting of the chute, a fixed weight of coal in the car and the data weights are given on tsifropechatayuschee device. The traction beam goes up and turns on the transfer drive of the conveyor-hopper to install it in its original position. During movement of the conveyor the coal is accumulated on its conveying body. Download car ends at a signal from the balance after reaching the weight of the car. The loading operation of the coal again before full loading of the last car of the composition. The conveyor stops at the position of the end of the cycle. The last car with the help of a shunting device, movable platform scales. Ice skating is a sealer at the end seal of coal in the last car raised to the upper position and is locked[6].
3.3 Development of the algorithm of operation and circuit solutions for the automation of the mines surface loading complex
At the initial stage of operation of the device is carried out a situation analysis of the car. Next is the validation analysis, strain gauge train hopper, depending on which is the process of loading the carriage. If the bunker does not have the required fill level is enabled on the conveyor №514. After this, the gate valve skip the hopper, the shutter in time. The next stage included a roar, and the chain conveyors (№547, 56, 118, 36). Next is the analysis ustanovlennyh belt scales on the conveyor №36, and is expected to signal the presence of cargo on the ribbon, which is performed after the gate closure of the hopper of the skip shaft. Then expected operation Kosevich installed on the conveyor №514, and the shutdown of the pipeline. Then dwell time is the waiting of working off of the screen, through the analysis of belt scales. In the presence of cargo on the scales crashing still included, in his absence – off noise. After this happens turn off coniferou (№547, 56, 118, 36). The shipping process of the mineral railway in the bunker is complete.
The Main working cycle. In the beginning the main algorithm checks the load cell main bin, with sufficient fullness process chain loading does not start, the reverse is input by the operator of the technological chain. And its subsequent development.
Based on the algorithm developed structural and Functional schemes of automation of the loading complex.
Figure 3 is a block diagram of an automation device loading of the complex
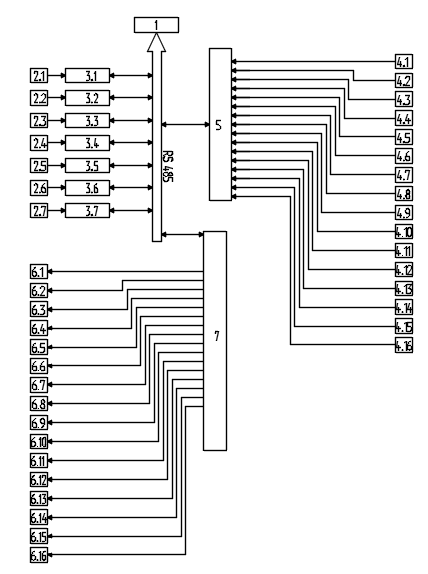
Figure 3 – Structural diagram of a loading complex automation device
The following notation is used in the structural diagram:
- PLC – 63 – programmable logic controller;
- SG – strain gauge (hopper and conveyor scales);
- IM110-1SG – strain gauge signal;
- PS – position sensor;
- IM110-16D – discrete input module (expansion unit);
- CR – control relay;
- IM110-16К – discrete output module.
3.4 Development of the algorithm of operation and wiring diagram of the demonstration stand of the mines surface loading complex
Description of the algorithm:
The start of operation of the stand is controlled by the operator, namely, opening the contact, and applying voltage. A platform with wagons located on it is driven by an engine. The platform moves until the inductive sensor for reading the numbering of cars installed directly on the gate of the main hopper, which ensures the exact location of the car under the main hopper, is triggered. After the sensor is triggered, the platform stops for loading. The loading process begins by setting the filling level of the main hopper by the operator on the PLC, using an optical sensor in the main hopper. Then the operator selects 1 of the additional bins and opens the valve of the selected hopper, after which the main hopper is filled to the set level, and when it is reached, the valve closes. The operator opens the valve of the main hopper, and the contents are poured into the car, after which the valve closes, and the level sensor is set to its initial position. Further, the process is repeated until the number of wagons is less than 4. When filling all available wagons, the platform enters the end position, from where it returns by turning on the toggle switch to its original position.
Figure 5 shows the algorithm of the control unit of the stand of the loading complex of the mine.
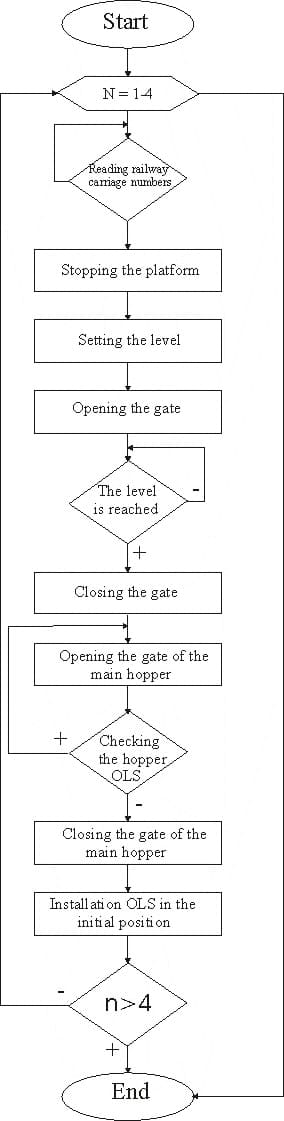
Figure 5 – The algorithm of the control unit of the stand of the loading complex of the mine
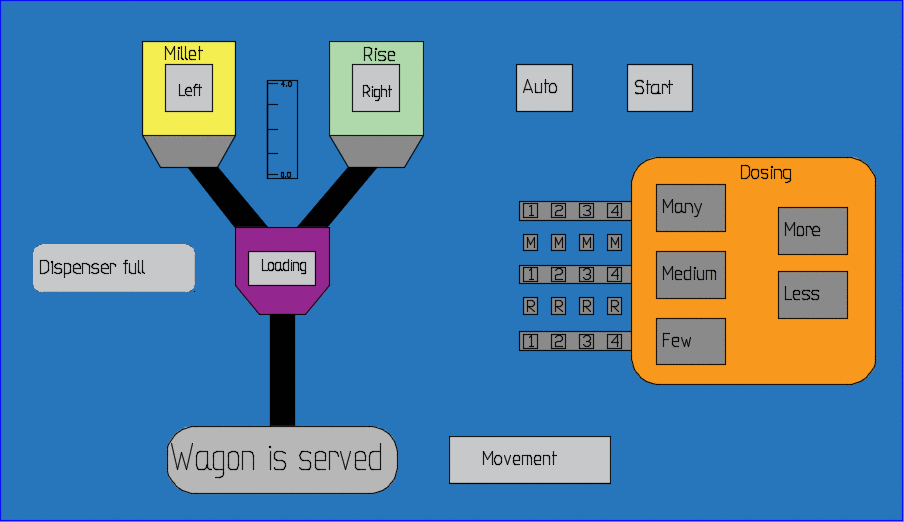
Figure 6 – Wiring diagram of the mine loading complex stand
(animation: 7 frames, 8 cycles, 304kb)
4. Operational requirements for the automation system of the loading complex conclusions
When operating the automation system of the loading complex of the mine surface, the requirements of the Safety Rules for Coal Mines must be observed.
The requirements are as follows:
- before putting into operation of automation equipment, service personnel must familiarize themselves with the rules of technical operation of the equipment;
- during operation in the mine, it is forbidden to disassemble, repair and adjust the elements, with the exception of measures involving the replacement of thermal power plants;
- during installation, commissioning or repair of equipment, when the shell is opened, it is necessary to transfer the blocking disconnector of the starter, which feeds the automation device, to the
Disabled
position;
The installation contains the works related to the supply voltage, which causes the necessity of disconnecting the device power supply, i.e. work is performed with the removal of the voltage[7]. Therefore, when carrying out such works necessary to comply with the Instructions for the safe conduct of work in underground electrical installations
that is this:
- before starting work with the relief you need to make the necessary disconnection and to take measures that prevent the supply voltage to and from work as a result of incorrect or inadvertent inclusion of switching devices;
- post posters
Not to include – people work
on the drives of switching devices, which can be energized to the place of work, you can install the necessary barriers; - verify the voltage absence voltage on the conductive parts.
Conclusion
As a result of this diploma project, criteria for managing the loading complex using the device were developed automated management of the loading complex, which ensures its optimal operation.
Based on these control criteria, a device for automated weight control and the direction of coal movement was developed, which satisfies the declared to her requirements. That is, the automation device allows you to control the operation of the loading complex in accordance with the task of optimal functioning.
A structural and schematic diagram of the device has been developed that reflect the structure of the device. An algorithm has been developed that describes the sequence of devices.
And, as a result of this work, a device was developed for automated control of coal loading at the surface complex of the mine.
The introduction of this device in the mine is economically feasible.
When writing this Abstract, the master's work is not yet completed. Final completion: June 2020. The full text of the work and materials on the topic can be obtained from the author or his manager after the specified date.
References
- Батицкий В. А., Куроедов В. И., Рыжков А. А. Автоматизация производственных процессов и АСУ ТП в горной промышленности. М.: Недра, 1991. 303 с.
- Попович Н. Г., Данильчук Г. И., Лисовский В. С., Янчук Г. М. Автоматизация производственных процессов угольных шахт–К.: Вища школа, 1978. 336 с.
- Авласенко Ю. Г., Ковалевский М. М. Автоматизация шахтных установок. Государственное издательство технической литературы УССР, Киев 1958. 296 с.
- Толпежников Л. И. Автоматическое управление процессами шахт и рудников / Л. И. Толпежников – Москва: Недра, 1985. 352 с.
- Бедняк Г. И. Автоматизация производства на угольных шахтах / Г. И. Бедняк, В. А. Ульшин, В. П. Довженко и др. Киев: Техника, 1989. – 272 с.
- Мелькумов Л. Г. Автоматизация технологических процессов угольных шахт /Л. Г. Мелькумов, Н. Я. Лазукин, Б. Х. Богопольский, Р. Л. Розенберг. Москва: Недра, 1973. 352 с.
- Каминский М. Л. Монтаж приборов и систем автоматизации / М. Л. Каминский, В. М. Каминский. Москва: Высшая школа, 1997. 304 с.
- НПАОП 10.0-5.18-04. Инструкция по противопожарной защите угольных шахт