Реферат по теме выпускной работы
Содержание
- Введение
- 1. Актуальность темы
- 2. Цель и задачи исследования, планируемые результаты
- 3. Описание объекта и предмета исследования
- 4. Методы обработки червячной пары
- 5. Методы нарезки червяка
- 6. Выбор необходимых методов исследований
- Выводы
- Список источников
Введение
В условиях современного состояния промышленности важнейшей целью является развитие технологии машиностроения. Это достигается повышением производительности технологических процессов, повышением качества выпускаемой продукции, повышением уровня их автоматизации, а также снижением себестоимости изготовления единицы продукции. Выполнение этих условий требует более рационального подхода при проектировании новых технологий, а также более тщательной проработки отдельных моментов в проектировании технологических процессов.
Технологические процессы серийного производства имеют ряд особенностей, которые проявляются при проектировании технологий. Среди этих особенностей средняя номенклатура выпускаемых изделий, большая программа выпуска. Применение технологических процессов серийного производства требует более низкой себестоимости единицы изделия по сравнению с изготовлением аналогичных изделий в мелкосерийном и единичном производствах. Это достигается за счет повышения капитальных затрат на технологическую подготовку производства: применением более дорогих станков, оснащённых ЧПУ, применением на ряду со стандартной технологической оснасткой и специальной, более тщательным составлением технологической документации и подбором инструмента, в некоторых случаях применением специального режущего инструмента.
1. Актуальность темы
Червячные передачи являются распространенным видом силовых передач. Качество их работы зависит от точности и качества поверхностей зубьев червячного колеса и червяка, которые достигаются главным образом на этапах отделочной и упрочняющей обработки. Червяк является элементом со сложным периодическим профилем и получается путем механической обработки. Это требует высоких затрат трудоемкости механической обработки и назначения дополнительных припусков, связанных с достижением требуемой точности и качества профиля витка. Отделочная обработка зубьев червячного колеса, ввиду большой площадь поверхности зубчатого венца, требует не меньших затрат трудоемкости, которая значительно увеличивается при повышении требований к точности червячных колес. Поэтому в настоящее время актуальной является задача совершенствование методов обработки червячной пары.
На основании вышеизложенного, данная работа актуальна, и посвящена решению вопросов опрделению и совершенствование методов обработки червячной пары.
2. Цель и задачи исследования, планируемые результаты
Цель работы: Повышение производительности и качества обработки колес за счет совершенствования технологии и нанесения специальных покрытий.
Основные задачи исследования:
- Выполнить анализ условий работы червячного колеса, определить основные требования предъявляемые к колесам для обеспечения надежной и безотказной их работы
- На основе морфологического анализа, определить наиболее рациональные методы обработки.
- Предложить рациональный метод обработки червячного венца.
- Выполнить исследование влияния входных параметров.
- Разработать рекомендации по совершенствование методов обработки червячной пары.
3.Описание объекта и предмета исследования
Червячная или, как ее также называют, зубчато-винтовая передача представляет собой механическую конструкцию, состоящую из зубчатого колеса и специального винта с резьбой – червяка. Червячное колесо – это представитель класса колес косозубого типа. Механическая передача осуществляется за счет зацепления конусовидного червяка об зубчатое колесо. Материал верхнего слоя колеса должен обладать пониженными показателями трения, к внутренней части не предъявляется особенных требований и она может быть исполнена из любого прочного металла.
Основным рабочим органом механизма является червяк (винт с резьбой). Первичный контакт шестеренки начинается по линии, а не в конкретной точке, что является ярким преимуществом данной системы перед аналогичными.
Червяк может иметь один или несколько заходов (как правило, от одного до четырех), направление движения может быть разным: правым или левым. Доминантной частью механизма в большинстве случаев выступает червяк, в качестве субдоминанта – червячное колесо. Основным параметром в механизме является делительный осевой шаг червяка.
Виды червячных передач
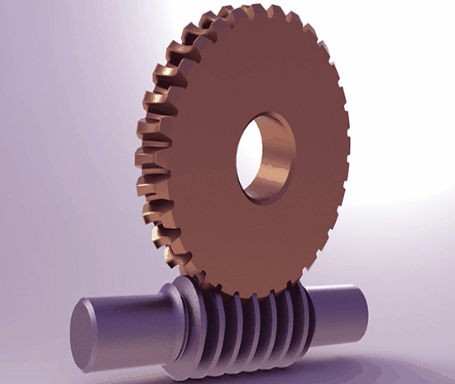
Рисунок 1 – Червячная пара (анимация:3 кадра, 230кб)
Отдельно можно разделить цилиндрические червяки на различные подвиды, в зависимости от формы профиля резьбы:
- Архимодов червяк – трапецевидный профиль с архимедовой спиралью в торце;
- Конволютный – трапепидальный профиль;
- Эвольвентный – эвольвентный профиль;
- С вогнутым профилем витков.
У глобоидных конструкций используется всего два типа формы профилей: трапицеидальный и с вогнутым профилем. Рабочие количество витков в глобоидной передаче выше, чем в цилиндрической, это обуславливает ее мощностные характеристики. Вместе с этим возникает и потребность в дополнительной системе охлаждения, а также точности при исполнении и монтаже.
Преимущества червячных передач
Тихие и плавные в работе данные передачи – это идеальное решение для управления низкомоментными силовыми установками. Компактные размеры позволяют уместить механизм даже в самые ограниченные пространства: это может быть как рулевая часть транспортных средств, так и, например, музыкальные инструменты с толковыми механизмами. Отдельно стоит обратить внимание на свойство самоторможения: оно обеспечивает функцию самоторможения без участия дополнительных устройств управления.
Недостатки червячных передач
Основным недостатком червячной трансмиссии является невысокий КПД, связанный с потерями мощности, присущими любой винтовой паре. Использование данной конструкции подразумевает обязательное применение антифрикционных материалов, исключение которых обычно быстро приводит к заеданию зубцов. Передаваемые мощности не превышают 200 кВт, что в значительной степени ограничивает области применения данных устройств.
Данные механизмы склонны к быстрому износу, как следствие - ремонт и повышенные требования к регулярному техническому обслуживанию, что невыгодно для некоторых решений с экономической точки зрения.
4.Методы обработки червяной пары
Элементами пары червячной передачи являются червяк и червячное колесо, оси которых перекрещиваются обычно под углом 90° (в некоторых механизмах тяжелых станков применяют передачи с осями, перекрещивающимися под углом 45°).
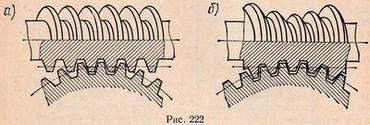
Рисунок 2 – Виды червяков
Червяки бывают цилиндрические (рис.3.1, а) и глобоидные (рис.3.1, б). Сечение витков цилиндрического червяка осевой плоскостью представляет собой рейку с прямолинейными или криволинейными боковыми сторонами. Осевое сечение глобоидного червяка имеет форму круговой прямобочной рейки.
Среди цилиндрических червяков наибольшее распространение для неответственных передач получил винтовой, или архимедов, червяк, представляющий собой как бы обычный винт с трапецеидальной резьбой. Винтовая поверхность этого червяка образуется вращением вокруг оси и одновременным перемещением вдоль оси (за каждый оборот) прямой, проходящей через ось червяка и наклоненной под некоторым углом к оси; при сечении плоскостью, проходящей через ось червяка, витки имеют трапецеидальный профиль (рис.3.2, а). Червячная пара с таким червяком обладает низким КПД и быстро изнашивается, поэтому ее применяют в не ответственных, тихоходных и слабонагруженных передачах.
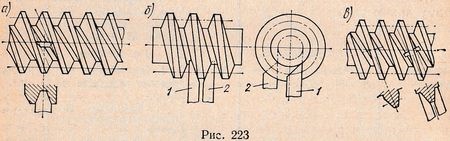
Рисунок 3 – Разновидность цилиндрического червяка
Другой разновидностью цилиндрического червяка является эвольвентный червяк (рис.3.2, б). Он представляет собой как бы цилиндрическое зубчатое колесо с звольвентной винтовой поверхностью. В сечении червяка плоскостями, перпендикулярными оси основного цилиндра, получаются эвольвенты, от которых этот червяк и получил свое название. Червячные пары с эвольвентными червяками часто используют в ответственных передачах при больших нагрузках и скоростях, но изготовление таких передач требует применения специального оборудования и сложных методов обработки.
Наконец, третьей разновидностью цилиндрического червяка является червяк с прямолинейным профилем в нормальном сечении витка и с удлиненной эвольвентой боковой стороны витка в сечении, поперечном к оси (рис.3.2, в). Такой червяк называют конволютным червяком. Он является разновидностью эвольвентного червяка. Эти червяки более просты в обработке, чем эвольвентные, и обеспечивают достаточную точность зацепления червячной передачи, имеют высокий КПД и износостойкость.
Глобоидные червяки обладают большой поверхностью соприкосновения витков червяка с зубьями червячного колеса, что обусловливает снижение давления, а, следовательно, и износа поверхности зубьев червячной пары. Винтовая нитка у этого червяка образуется при винтовом движении профиля не по цилиндрической поверхности, а по поверхности глобоида. Несмотря на сложность изготовления, их широко применяют при передаче больших мощностей.
5. Нарезание червяков
Простейшим видом обработки червяков является нарезание их на токарном станке резцом с прямолинейным профилем. Для получения правильного профиля витков профиль резца должен иметь контур впадины между зубьями червяка в определенном его сечении и совмещаться при нарезании с плоскостью этого сечения.
Чтобы получить архимедов червяк, профиль резца с прямолинейными кромками должен быть совмещен с плоскостью, проходящей через ось червяка (рис. 3.2, а). Однако с увеличением угла подъема витка нарезание червяка одним резцом становится затруднительным вследствие изменения размера угла, что приводит к выходу из строя режущего инструмента из-за выкрашивания режущей кромки. Поэтому архимедовы червяки при большом угле подъема витков заменяют эвольвентными или конволютными.
Эвольвентный червяк нарезают двумя резцами 1 и 2 (рис.3.2, б), профили режущих кромок которых совмещаются с двумя плоскостями, расположенными касательно к поверхности основного цилиндра с двух сторон. По мере увеличения диаметра основного цилиндра установка резцов выше и ниже центра вызывает определенные трудности вследствие изменений углов резания, поэтому при нарезании эвольвентных червяков применяют профильные резцы, соответствующие контуру нормального сечения впадины червяка с установкой плоскости профиля нормально к ее оси.
Конволютный червяк нарезается резцом, установленным своим профилем в плоскости, параллельной оси червяка, выше или ниже ее на определенную высоту или наклонно к ней, с совмещением оси симметрии профиля резца с осью червяка. Конволютные червяки с прямолинейным рабочим профилем обрабатывают двумя резцами (рис. 3.2, в).
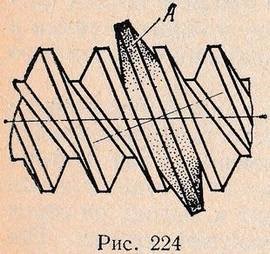
Рисунок 4 – Нарезание червяка дисковой фрезой
Червяки нарезают также профильным резцом и фрезами на фрезерных и резьбофрезерных станках. Нарезание червяков дисковой фрезой – более производительный способ обработки, но при этом искажается профиль червяка в результате подрезки, возникающей из-за различия углов подъема витка у основания и вершины, особенно у многозаходных червяков. Поэтому этот способ обычно применяют для предварительной обработки профиля червяка. При нарезании дисковой фрезой (рис.3.3) с режущими кромками прямолинейного профиля ось вращения фрезы А располагается под углом к оси червяка, равным углу подъема витков червяка.
Различные виды червяков можно нарезать червячной фрезой на обычных зубофрезерных станках. Так, при обработке червячной фрезой с прямолинейными режущими кромками зуба изготовляют эвольвентные червяки. Для нарезания архимедовых и конволютных червяков применяют специальные червячные фрезы с криволинейным профилем режущих кромок. Этот способ обработки при высокой производительности требует наличия сложного инструмента; так как он приводит к искажению профиля поверхностей витков червяка, то его применяют для предварительной обработки.
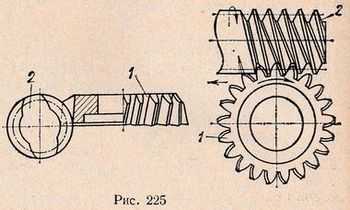
Рисунок 5 – Нарезание долбяком
Производительным методом обработки, обеспечивающим высокую точность, является нарезание червяка на специальных станках (типа «Корнелис») долбяком (рис.3.4). Долбяку 1 сообщают движение подачи вдоль оси червяка 2. Кроме того, долбяку и червяку сообщается вращательное движение обкатки. В результате сочетания этих движений нарезаются все витки червяка. При этом методе обработки профиль поверхности червяка не искажается. Однако необходимость изготовления долбяков для каждого угла подъема витков нарезаемых червяков увеличивает затраты на подготовку производства, поэтому применение этого метода экономично только в крупносерийном или массовом производстве.
Червячные колеса нарезают на зубофрезерных станках червячными фрезами тремя методами:
- радиальной подачи;
- тангенциальной подачи;
- комбинированным методом.
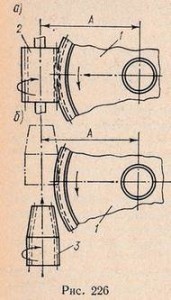
Рисунок 6 – Метод тангенциальной подачи
При методе радиальной подачи (рис.6, а) заготовка 1, находясь все время в зацеплении с червячной фрезой 2, подается в направлении фрезы до установленного размера А, при этом фреза совершает только вращательное движение. На червячном колесе получается правильный профиль зубьев при полном зацеплении червячной фрезы с заготовкой. Недостаток указанного метода заключается в том, что червячная фреза работает не всеми режущими кромками и изнашиваются лезвия только средней части фрезы, постоянно находящиеся в контакте с заготовкой. Этим методом нарезают зубья червячного колеса на обычном зубофрезерном станке без дополнительного специального суппорта. Настройка цепи деления станка при этом аналогична настройке при нарезании цилиндрических зубчатых колес с прямым зубом. Дополнительную настройку радиального перемещения стола производят в зависимости от заданной радиальной подачи.
При методе тангенциальной подачи (рис.6, б) заготовку червячного колеса 1 устанавливают на размер межцентрового расстояния А и фрезу 3 вводят в зацепление с заготовкой, перемещая ее в осевом направлении. Фреза 3 имеет коническую заборную часть и, работая всеми своими режущими кромками, изнашивается равномерно. В процессе резания фреза не только вращается, но и перемещается поступательно по оси. При этом заготовка 1 кроме основного вращательного движения, связанного с зацеплением, должна иметь дополнительное вращательное движение, скорость которого зависит от осевого перемещения фрезы 3, иначе зубья фрезы будут срезать зубья заготовки. Осевое перемещение фрезы 3 и дополнительное вращение заготовки 1 осуществляет специальный суппорт, который при нарезании червячных колес устанавливают на зубофрезерном станке.
Комбинированный метод нарезания червячных колес представляет собой последовательное сочетание методов радиальной и тангенциальной подач, причем первый применяют для предварительного нарезания зубьев, а второй – для окончательной обработки. Под окончательную обработку оставляют соответствующий припуск, который должен компенсировать погрешность предыдущей обработки. При комбинированном методе применяют как червячные фрезы, так и профильные резцы, причем применение последних для окончательной обработки червячного колеса обеспечивает высокую точность.
6. Выбор необходимых методов исследований
Ввиду отсутствия прямых функциональных зависимостей между погрешностями обработки фрезы на заточном и затыловочном станках и получающимися из-за них погрешностями профиля зуба колеса, авторам приведенной выше работы в тот период не удалось конкретизировать методику расчета допусков на отклонения элементов зуба фрезы, формирующих ее производящую поверхность.
Как известно, основными параметрами любой из характеристик качества изделия являются не только абсолютная величина поля рассеяния погрешностей, порождаемая совокупным действием случайных факторов, но и середина поля рассеяния, координата которой, имеющая свой знак и величину, определяет расположение поля рассеяния п, в конечном итоге, диапазон изменения параметра качества. Это необходимо учитывать при проектировании и изготовлении червячных фрез для червячных колес для обеспечения плавности работы червячных передач.
Таким образом, в области назначения допусков на формообразование профилей рабочего и производящего червяков первоочередной технологической задачей является распределение между погрешностями изготовления червяка на отклонение профиля витка червяка передачи от профиля производящего червяка (погрешность винтовой поверхности витка червяка по определению Г ОСТ 3675–81 или погрешность производящей поверхности инструмента – по стандарту более ранней редакции).
Вторая задача - исходя из норм плавности передачи. определить положения середин полей допусков на геометрические элементы профилей червяка и фрезы, учитывая также влияние периодических переточек фрезы.
Третья задача - определить влияние погрешностей настройки элементов наладки заточного, затыловочного и червячно-шлифовального станков и назначить допуски на тс элементы, которые изменяются в процессе обработки фрез и червяков, в частности, расчетный радиус (диаметр) шлифовального круга, профилированного для обработки соответствующей поверхности зубьев червячной фрезы или витка червяка.
Подавляющее большинство применяемых в машино- и станкостроении червячных передач проектируют на основе архимедова червяка и, соответственно, наибольшее распространение получили червячные фрезы для червячных колес с прямолинейным или близким к нему исходным контуром в осевом сечении червяка и классическим соответствием размеров производящего червяка фрезы и рабочего червяка передачи.
Однако в последние годы определились новые направления в области исследования и совершенствования технологии производства червячных передач, проектирования и применения червячных фрез для червячных колес:
- червячные фрезы и их станочные наладки для нарезания червячных колес к передачам с локализованным контактом;
- применение унифицированного инструмента для колес червячных передач на основе регулирования шага зацепления при изготовлении червяков (метод первичности инструмента);
- производство червячных фрез для нарезания колес глобоидных передач;
- технологическое обеспечение изготовления червячных фрез для колес передач с жидкостным трением, передач с червяками типа 2Т и др.
Обобщение и развитие научного и практического опыта производства червячных передач, включая проектирование и изготовление червячных фрез для червячных колес, с учетом многообразия применяемых сегодня и перспективных типов зацеплений‚ описано в дальнейших главах.
Выводы
В работе рассмотрены: требования, предъявляемые к червячным передачам, причины выхода из строя и снижения эксплуатационных свойств червяков; особенности обработки профиля червячного колеса, подвергаемых нанесению износостойких покрытий. Проведен анализ рассмотренных методов обработки, и способы их совершенствования. Поставлены цели и задачи будущих исследований.
Список источников
- Справочник технолога-машиностроителя. В 2 т. Т.1. / под ред. А. Г.Косиловой, Р. К. Мещерякова. – Москва: Машиностроение, 1986. –656 с.
- Обработка металлов резанием: справочник технолога / под общ ред. А. А. Панова. – Москва: Машиностроение, 1988. – 736 с.
- Александров Л. И., Артеменко Л. П., Костюк Д. И. Зубчатые передачи. Харьков: Издательство харьковского университета, 1964. 276 с.
- Адам Я. И., Антонов О. И., Жарков В. В., Копф И. А., Овумян Г. Г. Чистовая обработка зубьев крупных закаленных колес // Вестник машиностроения, 1980. № 9
- Айрапетов Э. Л., Апархов В. И., Мельникова Т. Н., Филимонова Н. И. Неравномерность распределения статической нагрузки в косозубых и шевронных зубчатых передачах // Вестник машиностроения, 1997. № 10.
- Айрапетов Э. Л., Афонский Б Д., Генкин Б. Д., Луценко В. И., Мдинарадзе Н. И. Об анализе кинематической погрешности зубчатых передач с использованием фильтрации// Вестник машиностроения, 1985. № 3.
- Байков А. Н., Шрайбман С. М. Нарезание колес с малым числом зубьев на зубодолбежном станке // Вестник машиностроения, 1973. № 7.