Abstract
CONTENT
- FOREWORD
- 1. BRIEF CHARACTERISTIC OF THE RAW MATERIALS USED IN BRIQUETTING
- 1.1. Materials used in briquetting.
- 1.2. Traditional binders used in briquetting.
- 2. PROSPECTS FOR THE USE OF BRIQUETTING IN PROCESSING INDUSTRIAL WASTE IN THE CONDITIONS OF MICRO-PLANTS
- 2.1. Feasibility of using micro-plants for processing metal-containing waste.
- 2.2. Briquetting as the main method of preparing secondary raw materials for processing at a mini-enterprise.
- 2.3. Economic efficiency of using a briquette press in micro-factories in the processing of industrial by-products.
- CONCLUSION
- LIST OF USED SOURCES
FOREWORD
The problems associated with an increase in the share of depreciation scrap with an increased content of undesirable impurities and the accumulation of metal-containing industrial by-products harmful to the environment in the dumps required effective measures to be taken to resolve them. In this regard, the European Slag Association and the Institute for the Industrial Circulation of Secondary Raw Materials were founded. According to the data published by these organizations, the total volume of recycling of metallurgical slags in developed countries has already exceeded 93%, and the processing of industrial waste makes it possible to annually receive useful goods worth more than $ 70 billion [1].
The constantly growing rates of accumulation of secondary raw materials with a sufficiently high concentration of valuable components in them cause an urgent need for their recycling in the CIS countries. Foreign experience allows us to conclude that it is advisable to process and dispose of ferrous metallurgy waste in a special technological complex, which is a micro-plant with an incomplete metallurgical cycle.
1. BRIEF CHARACTERISTIC OF THE RAW MATERIALS USED IN BRIQUETTING
1.1. Materials used in briquetting.
In metallurgical production, a large amount of material resources are used that have a common, terminologically established name: raw materials or raw materials (raw) materials. Technological fuel, in view of its importance, special influence on metallurgical processes, as well as high cost, has been allocated to a separate group.
According to the purpose and nature of consumption, raw metallurgical materials are divided into main and auxiliary. Basic materials make up the main content of the product, eg ores, concentrates. Auxiliary materials are used in the production process as additional and other materials that improve the technological process and product quality, in particular, fluxes, alloying additives, etc.
In what follows, waste will mean raw materials or products of their incomplete processing removed from the technological process (screenings, spills, sludge, dust), as well as secondary oxidation products (scale, welding slag, etc.).
Since for agglomeration by briquetting, only crushed types of raw materials with a particle size of less than 10 mm with a certain fractional composition can be used, in the future, only solid crushed materials will be considered as the main component of the briquetted mixture.
The most important briquetting characteristics of such a material are strength, density, autohesion (adhesive and cohesive) properties, particle shape and size, as well as mineralogical (chemical) composition. In particular, it is difficult to obtain sufficiently strong briquettes from fragile and porous chalk.
The low autohesion properties of sand and coal also do not allow obtaining high strength briquettes from them under normal pressure and without using a binder. Briquettes from coarse and fine ore, pressed under the same conditions, will have significant differences in strength: briquettes from fine ore will be much stronger.
Autohesion properties are an important characteristic of milled materials and dusts. They largely determine the strength of briquettes and depend on the size, shape, specific surface area and material of the particles. Particles are extremely diverse in size and shape (Fig. 1).
Depending on the tasks set for the disposal of waste, material composition or other criteria, different systems of their classification can be used [2].
In the case of agglomeration of waste by briquetting, primary raw materials, materials and waste are classified:
– at the place of production, origin;
– by the nature of formation and removal;
– by the method of extraction, extraction or capture;
– by chemical (material) composition;
– by physical properties;
– according to other (including technological) criteria.
At the place of production, primary raw materials and materials are subdivided into externally supplied and our own. The quality of the supplied materials is regulated by the relevant standards and contractual technical conditions [3].
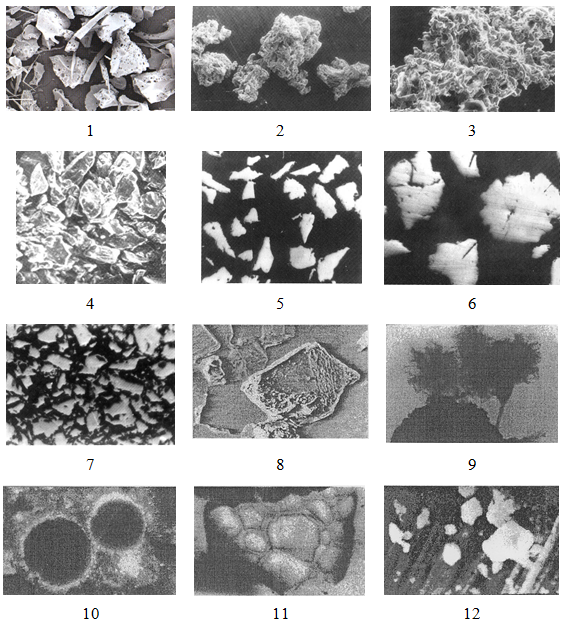
Figure 1 – Appearance and particle structure of some materials used for briquetting.
The quality of our own materials is regulated by internal technical conditions, and lower requirements are set for waste, stimulating their use within the enterprise.
As a classification of waste by place of origin, the nomenclature of sludge presented in the works can serve.
The physical properties that determine the suitability of sludge for agglomeration by granulation include density, dispersity, adhesion and other properties.
Density is an important property of materials, which determines the effectiveness of a particular method of agglomeration. So, during agglomeration, it is desirable that the bulk density of the charge take the maximum value at some optimal value of the bulk density, providing the required gas permeability. When briquetting, on the contrary, one should strive to increase the bulk density, which reduces shrinkage of the material and allows you to get more durable briquettes.
Bulk density is the mass of a unit of freely poured volume of dispersed material. The bulk volume, in addition to the material volume, includes the volume of space between particles and pores. Shaking or vibrating the container provides the bulk density of the densest packing of particles, in which the volume of space between the particles is practically minimal. This density is called shaking density [4][5].
1.2. Traditional binders used in briquetting.
When briquetting many types of crushed raw materials, which have insufficient autohesion properties, even at high pressures (180 MPa and more), it is not possible to obtain strong briquettes without sintering by conventional cold pressing. In such cases, binders are used – auxiliary materials that improve the adhesion of particles and increase the strength of the briquettes to a predetermined level.
Since the additives of such materials can be from several to 10% or more, they must meet the following requirements [6].
• Possess high autohesion properties, i.e. provide high cold and hot strength with minimal binder consumption.
• Provide fast adhesion.
• Introduce the minimum amount of harmful, ballast and other impurities that are unsafe for service personnel and reduce the quality of the final product.
• Do not worsen the conditions for briquetting melting.
• Be common and affordable.
• Do not require complex techniques and operations for their use.
• Provide minimal moisture resistance.
The binder is a determining condition for the strength and, to a large extent, for the recoverability of briquettes. An increase in binder consumption, increasing strength, leads not only to a decrease in useful components in briquettes, but also to a significant increase in their cost.
It is preferable to use the most common and well-researched materials as binders:
– slaked lime (portlandite);
– liquid glass;
– Portland cement;
– alumina cement;
– magnesia cement;
– bischofite;
– bentonite;
– powder lignosulfonate;
– sulfite-alcohol stillage (powder and in solution);
– lignin;
– molasses.
2. PROSPECTS FOR THE USE OF BRIQUETTING IN PROCESSING INDUSTRIAL WASTE IN THE CONDITIONS OF MICRO-PLANTS
2.1. Feasibility of using micro-plants for processing metal-containing waste.
The prospect of the emergence of small enterprises specializing in the processing of secondary resources is due to significantly lower investments required for their launch, as well as the possibility of a more flexible solution to the issue of supplies in small volumes of metal products to machine-building plants focused on the production and repair of auxiliary technological equipment for a number of sectors of the domestic economy. In addition, to ensure the rhythmic work of a micro-plant, there is no need to resort to the services of railway transport, since the logistics and volumes of cargo transportation in this case with lower costs can be provided by road transport [7].
The Angolan metallurgical company Companhia Siderurgica do Cuchi (CSC) in 2016 launched a pig iron plant with a capacity of 96 thousand tons/year with a blast furnace with a volume of 119 m3, in which charcoal is used to reduce iron ore [8].
The achieved indicators of the technical and economic efficiency of the use of oxygen mini-cupolas and blast furnaces for the production of pig iron and commercial pig iron from industrial waste indicate the expediency of searching for options for the use of small melting units that allow processing liquid iron and solid metal-containing waste with an increased content of harmful impurities into steel of acceptable quality and thereby increase the added value of the final product of the enterprise.
The structure of such a micro-plant should include preparatory, smelting and bottling departments.
2.2. Briquetting as the main method of preparing secondary raw materials for processing at a mini-enterprise.
The need for preliminary preparation of initial raw materials is due to the fact that components valuable for steelmaking are contained in sludge, slag, mill scale and shavings, i.e. in fine-grained materials that cannot be used in the existing state as a solid part of the charge of an electric arc furnace or oxygen converter. Therefore, the feedstock is subject to obligatory agglomeration. For this purpose, the priority is the briquetting process, which favorably differs in a number of indicators from the methods of agglomeration and the production of pellets. At the same time, in order to preserve the invariability of the composition and properties of the ingredients that form the structure of the briquettes, it is preferable to use the cold briquetting method for their preparation, which is characterized by ease of implementation and low energy consumption. However, such a briquetting technology requires careful selection of the composition and percentage of the materials to be pressed, as well as the used binders of organic or mineral origin [9][10].
At present, stamp and double-roll presses are used to pelletize fine materials. For the successful implementation of the process of forming briquettes of sufficient strength, with minimal energy consumption and high productivity, it is recommended to use two-roll presses equipped with devices for preliminary compaction of the material being pressed. They, in comparison with cyclical stamping presses, all other things being equal, provide greater productivity with 1.5 times less energy consumption.
At the Department of Mechanical Equipment of Ferrous Metallurgy Plants of Donetsk National Technical University, on the basis of the results of the research carried out, a small-sized two-roll press with a capacity of up to 3 t/h has been developed to obtain briquettes used as a charge for smelting pig iron in blast furnaces with a volume of up to 130 m3, as well as for partial replacement scrap metal in the process of steel production in electric arc furnaces or oxygen converters with a tonnage of 3 to 10 tons. This press is designed to work in a micro-plant for the processing of metal waste. Figure 2 shows an experimental sample. Figure 3 shows how it works. Using this sample, comprehensive laboratory studies were carried out in order to obtain information on the process of shaping briquettes from rolling production waste. The mixture for their preparation contained in its composition, in various proportions, mill scale and technological binder with a given moisture content. Low-fired dolomite mixed with ceresite was used as a complex binder.
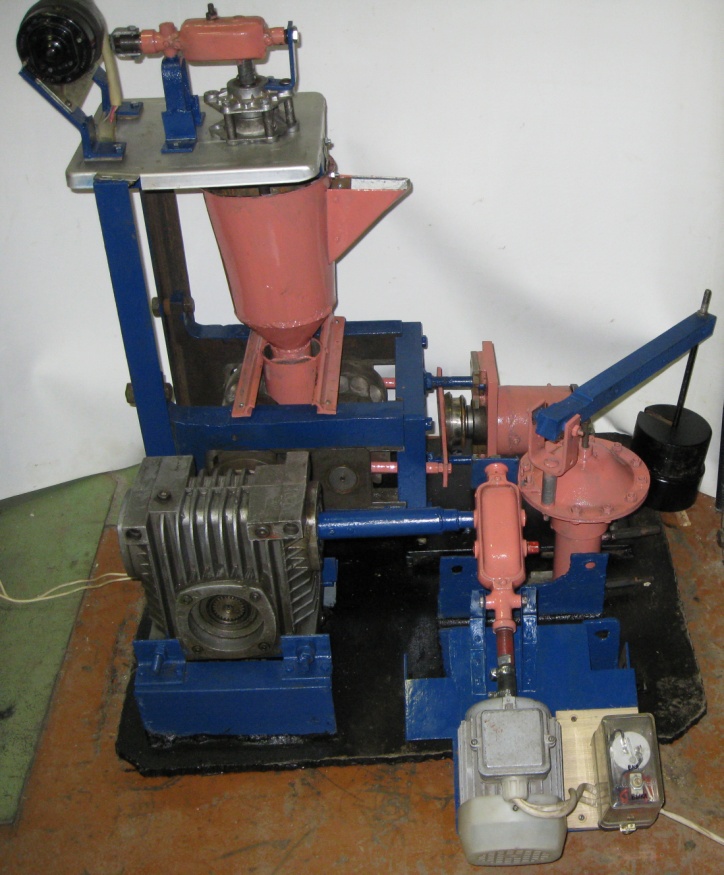
Figure 2 – Experimental sample of a two-roll briquette press.
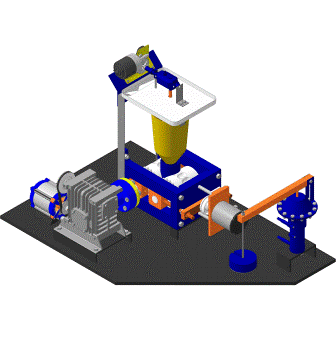
Figure 3 – Three-dimensional model of the press installation.
(animation: volume 223 kb, frames 11, number of repetition cycles 14, delay between frames 100 ms)
The results of tests of the obtained briquettes for impact strength, carried out according to the standard method by their repeated dropping from a height of 2 m onto a metal plate and subsequent determination of the yield of a fraction less than 5 mm, are shown in the table, the data of which indicate that the content of scale and binders in the starting material briquetted mass should be 60–70 and 30–40%, respectively.
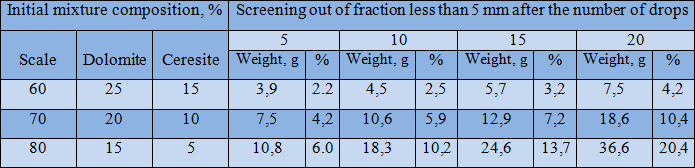
Table 1 – The results of testing the obtained briquettes from mill scale for impact strength.
The industrial waste obtained after briquetting can be used as a substitute for metal charge, fuel and reducing additives, slag mode regulators, deoxidizers and alloying agents.
2.3. Economic efficiency of using a briquette press in micro-factories in the processing of industrial by-products.
A decrease in the level of cost indicators during the construction of a micro-plant and the organization of the production of metal products on it using pre-prepared waste from mining and metallurgical enterprises as a charge, allows predicting a reduction in the payback period of such enterprises in comparison with mini-plants for which it is currently ranges from 5 to 7 years. Along with investment attractiveness, an important incentive to start the development of micro-factories in the CIS countries is the urgent need for effective measures to improve the environmental situation in their industrially developed regions. This will be facilitated by a reduction in the volume of waste accumulated in dumps and sludge storages due to their processing into cast iron and steel[11][12][13].
The results of the analysis of statistical data on the amount of capital investments required for the construction of metallurgical enterprises indicate that the start-up of a full-cycle plant implies costs of at least $ 1,000 per ton of the planned annual production of metal products, for a mini-plant this indicator is halved and is 500–600 USD/t. Therefore, when commissioning a micro-plant, a further decrease in the required investments should be expected. This forecast is based on the fact that the micro-plant can function as an auxiliary section of the foundry of a large machine-building enterprise or be based on the territory of local factories of various profiles, including repair and house-building ones, which had previously ceased production. In this case, due to partial or full use of the existing infrastructure, capital costs for foundation and construction work will be significantly reduced. Special attention should be paid to the reduction of production costs in terms of the production of metal products at micro-factories, due to a decrease in its cost. Rough calculations of the cost of obtaining a ton of products in the conditions of processing industrial metal-containing waste using an oxygen converter with a rotating body, taking into account the increased consumption of refractories for its lining due to intensive mechanical stirring of the melt (table data), showed that the cost of steel is reduced by about 10 % and this is due to the low cost of the initial charge.
CONCLUSION
As a result of this work, an analysis was made of the prospects for using a briquette press in micro-plants for processing a charge with an increased content of harmful impurities, as well as by-products of metallurgical production, including valuable components. In accordance with the indicated concept, the micro-plant should include a preparatory site for agglomeration by briquetting of fine fractional waste from the coal mining, coke-chemical and metallurgical industries as the main one at the enterprise; smelting chambers with furnaces or units for smelting iron and steel; casting and (or) casting span, in which castings can be obtained, as well as billets for the final rolling processing. The economic efficiency of production at the micro-plant is due to the relatively low cost of the processed charge materials.
LIST OF USED SOURCES
- Робин Виннер. Переработка вторичного сырья // Металлолом. – 2011 – №2 – С.9
- Иванченко В.В. Нерудные материалы в металлургических шламах ОАО КГМК
Криворожсталь
/ В.В. Иванченко, А.В. Кекух, П.И. Оторвин и др. // Металлург. и горноруд. пром-сть. – 2004. – № 3. – С. 17–21. - Классен П.В. Гранулирование / П.В. Классен, И.Г. Гришаев, И.П. Шомин. – М.: Химия, 1991. – 320 с.
- Коузов П.А. Основы анализа дисперсного состава промышленных пылей и измельченных материалов / П.А. Коузов. – Л.: Химия, 1987. – 264 с.
- Производство конвертерной извести во вращающихся печах с шахтным подогревателем: Технологическая инструкция ТИ 232–163–98. – ОАО Металлургический комбинат
Азовсталь
. – 1998. – 30 с. - Монастырёв А.В. Печи для производства извести: Справочник / А.В. Монастырёв, А.В. Александров. – М.: Металлургия, 1979. – 232 с.
- Смирнов А.Н., Сафонов В.М., Дорохова Л.В. Металлургические мини-заводы.- Донецк: ООО
Норд-Пресс
, 2005.– 465 с. - Овчинников А.М. Модернизация оборудования и реконструкция заводов черной металлургии за рубежом // Черная металлургия: Бюл. ин-та
Черметинформация
. 2016. № 2. С. 96 – 100. - Кокорин В.Н., Григорьев А.Н., Кокорин М.В. и др. Промышленный рециклинг техногенных отходов.- Ульяновск: УлГТУ, 2005.– 42 с.
- Далмиа И.К. Производство и применение в доменной печи брикетов нового поколения // Металлург. 2012. № 3. С. 39 – 41.
- Еронько С.П., Климович Н.А. Перспективы использования и проблематика создания мини-агрегата для переработки некачественной шихты и металлсодержащих отходов // Черная металлургия: Бюл. ин-та
Черметинформация
. 2016. № 5. С. 26 – 31. - Сафонов В. М., Смирнов А.Н. Ядро мини-металлургии. Современная электродуговая печь: основные параметры и концептуальные решения // Металл. 2004. № 10 (58). С. 28 – 36.
- Бойченко Б.М., Охотский В.Б., Харлашин П.С. Конвертерное производство стали: теория, технология, качество стали, конструкция агрегатов, рециркуляция материалов и экология.– Днепропетровск: РВА
Днепро-ВАЛ
, 2006.– 452 с..