Реферат за темою випускної роботи
Склад
- ВСТУП
- 1. КОРОТКА ХАРАКТЕРИСТИКА СИРОВИНИ, ВИКОРИСТАНОЇ ПРИ БРИКЕТУВАННІ
- 1.1. Матеріали, використовувані при брикетуванні.
- 1.2. Традиційні сполучні, використовувані при брикетуванні.
- 2. ПЕРСПЕКТИВИ ВИКОРИСТАННЯ БРИКЕТУВАННЯ ПРИ ПЕРЕРОБЦІ ПРОМИСЛОВИХ ВІДХОДІВ В УМОВАХ МІКРО-ЗАВОДІВ
- 2.1. Доцільність застосування мікро-заводів з переробки металовмісних відходів.
- 2.2. Брикетування як основний спосіб підготовки вторинної сировини до переробки на міні-підприємстві.
- 2.3. Економічна ефективність використання брикетного преса в умовах мікро-заводів при переробці побічних продуктів промислового виробництва.
- ВИСНОВОК
- СПИСОК ВИКОРИСТАНИХ ДЖЕРЕЛ
ВСТУП
Проблеми, пов'язані зі збільшенням частки амортизаційного брухту з підвищеним вмістом небажаних домішок і накопиченням в відвалах металоємких побічних промислових продуктів, що завдають шкоди навколишньому середовищу, зажадали прийняття дієвих заходів щодо їх вирішення. У зв'язку з цим свого часу були засновані Європейська асоціація по шлаку і Інститут промислової циркуляції вторинної сировини. За даними, опублікованими цими організаціями, сумарний обсяг утилізації металургійних шлаків в розвинених країнах вже перевищив 93%, а переробка промислових відходів дозволяє щорічно отримувати корисні товари на суму, що перевищує 70 млрд.доларів.[1]
Зовсім інша картина, яка відображає стан справ в даній області людської діяльності, спостерігається в країнах СНД. Наприклад, в Україні площа, яку займає звалищами промислових відходів, перевищує 160 тис. гектарів, а їх щорічний приріст вже досяг 1 млрд. тонн.
У Російській Федерації тільки в зоні розташування Магнітогорського металургійного комбінату за піввіковий проміжок часу його роботи в шламосховищах накопичилося понад 11 млн. тонн побічних продуктів з вмістом в них заліза до 30%.
Постійно зростаючі темпи накопичення вторинних сировинних матеріалів з досить високою концентрацією в них цінних компонентів викликають нагальну потребу їх рециклінгу. Зарубіжний досвід дозволяє зробити висновок про те, що переробку та утилізацію відходів чорної металургії доцільно виконувати в умовах спеціального технологічного комплексу, що є мікро-заводом з неповним металургійним циклом.
1. КОРОТКА ХАРАКТЕРИСТИКА СИРОВИНИ, ВИКОРИСТАНОЇ ПРИ БРИКЕТУВАННІ
1.1. Матеріали, використовувані при брикетуванні.
У металургійному виробництві використовують велику кількість матеріальних ресурсів, що мають загальне, термінологічно усталене назва: сировину і матеріали або сировинні (сирі) матеріали. Технологічне паливо на увазі його важливості, особливого впливу на металургійні процеси, а також високу вартість виділено в окрему групу.
За призначенням і характером споживання сирі металургійні матеріали діляться на основні та допоміжні. Основні матеріали становлять головний зміст продукту, наприклад, руди, концентрати. Допоміжні матеріали використовують в процесі виробництва як додаткові та інші матеріали, що поліпшують технологічний процес і якість продукції, зокрема, флюси, легуючі добавки та ін.
За джерелами утворення всі матеріали підрозділяють на первинні, свіжі матеріали і оборотні, вторинні матеріали або відходи. До оборотних матеріалів відносять використовувані відходи, просипу, повернення, побічні і попутні продукти.
Під відходами металургійного виробництва в широкому сенсі слова слід розуміти сировину, матеріали та енергоресурси, в силу тих чи інших причин не використані для отримання основної продукції. Відходи є неминучим елементом існуючої технології виробництва металів.
Показником, досить повно характеризує ступінь досконалості технології, рівень її безвідходності, є коефіцієнт використання матеріалів км, який для чорної металургії становить 0,4. Процес можна вважати матеріально безвідходним, якщо Км>0,9 і маловідходних – при Км=0,8–0,9.
Надалі під відходами будемо розуміти сирі матеріали або продукти їх неповного обробки, виведені з технологічного процесу (відсівання, просипу, шлами, пилу), а також продукти вторинного окислення (окалина, зварювальний шлак і т.п.).
Оскільки для огрудкування брикетуванням можна використовувати тільки подрібнені види сировини розміром менше 10 мм з певним фракційним складом, в подальшому в якості основного компонента брикетуємої суміші будемо розглядати тільки тверді подрібнені матеріали.
Найважливішими брикетуючі характеристиками такого матеріалу є міцність, щільність, аутогезіонні (адгезійні і когезійні) властивості, форма частинок і їх крупність, а також мінералогічний (хімічний) склад. Зокрема, з нетривкого і пористого крейди складно отримати досить міцні брикети.
Низькі аутогезіонні властивості піску і вугілля також не дозволяють отримати з них брикети високої міцності при нормальному тиску і без використання сполучного. Брикети з великої і дрібної руди, спресовані в однакових умовах, матимуть істотні відмінності в міцності: брикети з дрібної руди виявляться значно міцніше.
Істотна відмінність по міцності дає пресування сумішей однакового фракційного, але різного хіміко-мінералогічного складу. Так, алюмокальцієві з'єднання надають брикетам значно більш високу міцність, ніж феррокальцієві.
У брикетуванні матеріалів слід враховувати і суперечливий вплив окремих факторів. Так, питома поверхня, гранулометричний склад і вологість є такими факторами. Зокрема, гранулометричний склад двояко впливає на брикетуємість. Грубозерниста шихта пресується краще, ніж дрібнозернистий, проте в цілому міцність брикетів з крупнозернистою шихти менше, ніж з дрібнозернистої з причини малої поверхні контакту частинок. Для досягнення гарної пресованості і високої щільності брикетів необхідний відповідний підбір гранулометричного складу шихти.
Форма частинок впливає на насипну масу, спікаємість, сипкість (плинність), а отже, пресуємість і міцність брикетів. Частинки шорсткою і неправильної форми зачіпляються краще, ніж гладкою і правильної, а менша насипна маса і погана пластичність погіршують брикетуємість шихти.
Питома поверхня залежить від розміру часток і двояко впливає на брикетуємість. З одного боку, висока питома поверхня збільшує сили зчеплення, а з іншого – зростає адсорбція газів і інших речовин і збільшується робота на подолання тертя часток один про одного і стінки прес-форми.
Аутогезіонние властивості є важливою характеристикою подрібнених матеріалів і пилу. Вони багато в чому визначають міцність брикетів і залежать від розміру, форми, питомої поверхні і матеріалу частинок. За своїми розмірами і формою частинки надзвичайно різноманітні (мал. 1).
Залежно від завдань, поставлених перед утилізацією відходів, речового складу чи інших критеріїв можуть застосовуватися різні системи їх класифікації [2].
У разі огрудкування відходів брикетуванням первинне сировину, матеріали та відходи класифікують:
– за місцем виробництва, виникнення або джерелами утворення;
– за характером утворення та видалення;
– за способом видобутку, вилучення або уловлювання;
– за хімічним (речовинним) складом;
– за фізичними властивостями;
– по іншим (в т.ч. технологічним) критеріям.
За місцем виробництва первинне сировину і матеріали поділяють на поставляєму з боку і власну. Якість матеріалів, що поставляються регламентовано відповідними стандартами та договірними технічними умовами [3].
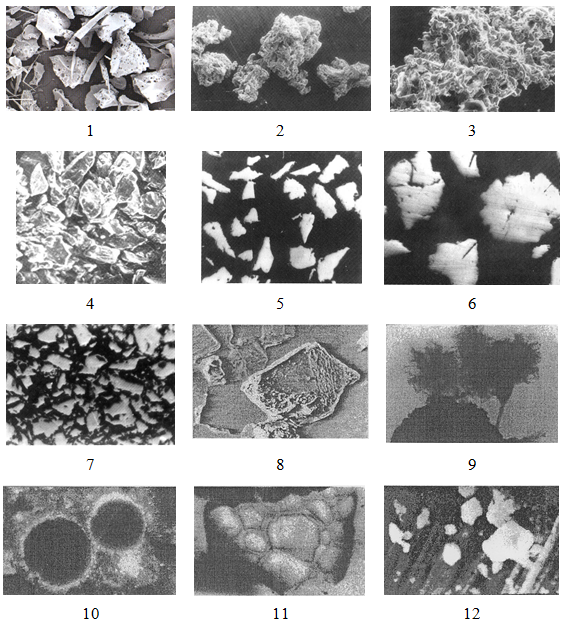
Малюнок 1 – Зовнішній вигляд і структура частинок деяких матеріалів, які використовуються для брикетування.
Якість власних матеріалів регламентують внутрішніми технічними умовами, а для відходів встановлюють знижені вимоги, що стимулюють їх використання всередині підприємства.
Як класифікації відходів за місцем виникнення може служити номенклатура шламів, представлена в роботах.
За характером утворення та видалення всі відходи поділяють на несеться з газами, що відходять (пилу); просипи, осипи, змиви (шлами); сливи, натікання, залишки (шлаки, зварювальний шлак, скардовини). У металургії найбільші проблеми пов'язані з утилізацією першої і до частини відходів другої групи.
Способи уловлювання поділяють на сухі і мокрі. Пилу хімічно активніші, ніж вилежатися вологі шлами.
За хімічним (речового) складом відходи групують за двома рівнями – виду (наявності) і змістом основного компонента. По виду основного компонента відходи класифікують на залізовмісні, Марганцевмісні і ін., А також відходи, детерміноване по шкідливого компоненту.
За змістом основного компонента відходи класифікують на багаті, щодо-багаті і бідні. Рівень багатства визначають зіставленням з аналогічним первинним сировиною. За речовинним (компонентного) складу шлами представляють собою суміші залишків сировини і матеріалів, частково зазнали обробці, забирає, возгони і вторинні оксиди.
До фізичних властивостей, що визначає придатність шламів до огрудкування, гранулювання, відносять щільність, дисперсність, адгезіонну здатність та інші властивості.
Щільність є важливою властивістю матеріалів, від якого залежить ефективність того чи іншого способу огрудкування. Так, при агломерації бажано, щоб об'ємна щільність шихти приймала максимальне значення при деякому оптимальному значенні насипної щільності, що забезпечує потрібну газопроникність. При брикетуванні, навпаки, слід прагнути до збільшення насипної щільності, що зменшує усадку матеріалу і дозволяє отримувати більш міцні брикети.
Розрізняють справжню (питому), що здається, об'ємну і насипну, в т.ч. При струшуванні, щільності сипучих матеріалів [4][5].
Справжня щільність – щільність матеріалу, з якого складаються частинки.
Удавана щільність – це маса частинок одиниці об'єму матеріалу з урахуванням закритих в частинках пір.
Об'ємна щільність – це маса одиниці об'єму матеріалу з урахуванням закритих і відкритих пір.
Насипна щільність – це маса одиниці вільно насипаного обсягу дисперсного матеріалу. У насипний об'єм, крім обсягу матеріалу, входить обсяг простору між частинками і пір. Струшування або вплив вібрацією на ємність забезпечує насипний щільності найбільш щільну упаковку частинок, в якій обсяг простору між частинками практично мінімальний. Таку щільність називають щільністю при струшуванні.
1.2. Традиційні сполучні, використовувані при брикетуванні.
При брикетуванні багатьох видів подрібненої сировини, що володіє недостатніми аутогезіоннимі властивостями, навіть при високому тиску (180 МПа і більше) звичайним холодним пресуванням отримувати міцні брикети без їх спікання не представляється можливим. У таких випадках використовують сполучні – допоміжні матеріали, що поліпшують злипання частинок і підвищують міцність брикетів до заданого рівня.
Оскільки добавки таких матеріалів можуть становити від декількох до 10% і більше, вони повинні відповідати наступним вимогам [6].
• Володіти високими аутогезіоннимі властивостями, тобто забезпечувати високу холодну і гарячу міцність при мінімальній витраті сполучного.
• Забезпечувати швидку зхвачуюмість.
• Вносити мінімальну кількість шкідливих, баластних та інших домішок, небезпечних для обслуговуючого персоналу і знижують якість кінцевого продукту.
• Не погіршувати умов плавки брикетів.
• Бути поширеними і мати невисоку вартість.
• Не вимагати складних прийомів і операцій по їх використанню.
• Забезпечувати мінімальну вологостійкість.
Сполучна речовина є визначальною умовою міцності і в значній мірі – восстановимости брикетів. Збільшення витрат сполучного, підвищуючи міцність, призводить не тільки до зниження корисних компонентів в брикетах, а й до значного їх подорожчання.
До поширених неорганічним сполучною слід віднести гашене вапно, рідке скло, глиноземистий і портландский цементи. Однак багато хто з них мають істотні недоліки. Так, гашене вапно і портландцемент при нагріванні віддають гідрадну вологу і втрачають міцність, рідке скло містить значну кількість лугів і двоокис кремнію, а глиноземний цемент до того ж надзвичайно доріг. При цьому кращі в'яжучі характеристики виявляє рідке скло і глиноземний цемент.
До поширених органічним сполучним відносять кам'яновугільні і нафтові смоли, меляса, відходи гідролізної і целюлозної промисловості тощо Загальним недоліком органічних сполучних є їх піроліз або вигоряння при високих температурах з втратою міцності, а також внесок в брикети значної кількості сірки.
Більшість органічних сполучних можуть використовуватися для отримання брикетів з високими показниками холодної міцності. При нагріванні таких брикетів зв'язка руйнується або згорає, в результаті чого вони втрачають більшу частину міцності, розсипаються під тиском верхніх шарів матеріалу і виносяться потоком газів з агрегату. Більш стійкі сполучні при згорянні утворюють спечений шлак, який скріплює частки брикетів, перешкоджаючи їх руйнування.
Сполучні неорганічного походження, поміщаючись між частинками оксидів заліза і відновника, погіршують восстановимость. Органічні сполучні, частково замінюючи відновник, зазвичай вносять небажані домішки, в т.ч. сірку. Поряд з цим деякі види сполучних при нагріванні можуть сприяти утворенню легкорухомих фаз, наприклад, фаяліта, що бажано для усадки відновлюються брикетів.
До комбінованих сполучною відносять суміші різних сполучних. Ці суміші дозволяють поліпшити позитивні і знизити негативні властивості. Наприклад, суміш, яка містить рідке скло і лігносульфонат, вносить знижена кількість лугів, кремнезему або сірки, ніж кожне сполучна окремо, при одночасному забезпеченні високої механічної міцності брикетів.
В якості сполучних краще використовувати найбільш поширені і добре досліджені матеріали:
– вапно гашене (портландіт);
– рідке скло;
– портландцемент;
– глиноземний цемент;
– магнезійний цемент;
– бішофіт;
– бентоніт;
– лігносульфонат порошковий;
– сульфітно-спиртова барда (порошкова і в розчині);
– лігнін;
– меляса.
2. ПЕРСПЕКТИВИ ВИКОРИСТАННЯ БРИКЕТУВАННЯ ПРИ ПЕРЕРОБЦІ ПРОМИСЛОВИХ ВІДХОДІВ В УМОВАХ МІКРО-ЗАВОДІВ
2.1. Доцільність застосування мікро-заводів з переробки металовмісних відходів.
Перспектива появи малих підприємств, що спеціалізуються на переробці вторинних ресурсів, обумовлена значно меншими інвестиціями, необхідними при їх запуску, а також можливістю більш гнучкого вирішення питання поставок в невеликих обсягах металопродукції машинобудівним заводам, орієнтованих на випуск і ремонт допоміжного технологічного обладнання для ряду галузей вітчизняної економіки. Крім того, для забезпечення ритмічної роботи мікро-заводу немає необхідності вдаватися до послуг залізничного транспорту, так як логістика і обсяги вантажоперевезень в даному випадку з меншими витратами можуть бути забезпечені автомобільними перевезеннями [7].
У світовій практиці вже відомі позитивні приклади застосування різних технологій отримання чавуну на підприємствах з річним виробництвом в кілька десятків тисяч тонн. Так консорціумом, очолюваним фірмою ThyssenKrupp Steel, сконструйована киснева вагранка, що дозволила виплавляти з відходів 15 т/год передільного чавуну.
Ангольська металургійна компанія Companhia Siderurgica do Cuchi (CSC) в 2016 році запустила завод з випуску чавуну продуктивністю 96 тис. т/рік з доменною піччю об'ємом 119 м3, в якій для відновлення залізної руди передбачено використання деревного вугілля [8].
На експериментальному заводі ТОВ Енергокапітал, м.Макіївка Донецької області, впроваджена придбана в Китаї технологія, що забезпечує переробку в міні-доменної печі об'ємом 128 м3 окатишів з вугільного і металевого шламів в якісний чавун. При цьому одержувані попутні продукти – гранульований шлак і доменний газ – в подальшому використовують відповідно в якості будівельного матеріалу і палива в установках, що генерують електроенергію.
Досягнуті показники техніко-економічної ефективності застосування кисневих міні-конвертерів і доменних печей для отримання переробного та товарного чавуну з промислових відходів свідчить про доцільність пошуку варіантів використання малих плавильних агрегатів, що дозволяють переробляти рідкий чавун і тверді металоємкі відходи з підвищеним вмістом шкідливих домішок в сталь прийнятної якості і тим самим збільшувати додану вартість кінцевого продукту підприємства.
У структуру такого мікро-заводу повинні входити підготовче, плавильне і розливний відділення.
2.2. Брикетування як основний спосіб підготовки вторинної сировини до переробки на міні-підприємстві.
Необхідність в попередній підготовці вихідних сировинних матеріалів обумовлена тим, що цінні для сталеплавильного переділу компоненти містяться в шламах, шлаках, прокатної окалини і стружці, тобто в дрібнофракційних матеріалах, які не можна застосовувати в існуючому стані в якості твердої частини шихти електродугової печі або кисневого конвертера. Тому вихідна сировина підлягає обов'язковому огрудкуванню. Для цієї мети пріоритетним є процес брикетування, вигідно відрізняється за низкою показників від способів агломерації і виробництва окатишів. При цьому з метою збереження незмінності складу і властивостей інгредієнтів, що утворюють структуру брикетів, для їх отримання переважно використовувати спосіб холодного брикетування, що відрізняється простотою реалізації і малої енергоємністю. Однак така технологія брикетування вимагає ретельного підбору складу і процентного вмісту пресованих матеріалів, а також застосовуваних сполучних добавок органічного або мінерального походження [9][10].
В даний час для огрудкування дрібнодисперсних матеріалів використовують штемпельні і двохвалкові преси. Для успішної реалізації процесу формоутворення брикетів достатньої міцності, з мінімальними енергетичними затратами і високою продуктивністю рекомендується застосовувати двохвалкові преси, забезпечені пристроями попереднього ущільнення пресованого матеріалу. Вони в порівнянні з штемпельними пресами циклічної дії при інших рівних умовах забезпечують більшу продуктивність з меншим в 1,5 рази енергоспоживанням.
На кафедрі Механічного Обладнання Заводів Чорної Металургії Донецького Національного Технічного Університету на підставі результатів досліджень, які проводилися розроблений малогабаритний двовалковий прес продуктивністю до 3 т/год для отримання брикетів, що використовуються в якості шихти при виплавці чавуну в доменних печах обсягом до 130 м3, а також для часткової заміни металобрухту в процесі виробництва сталі в електродугових печах або кисневих конвертерах тоннажністю від 3 до 10 т. Даний прес призначений для роботи в умовах мікро-заводу з переробки металлоємких відходів. На малюнку 2 показаний його експериментальний зразок. На малюнку 3 анімований принцип його роботи. З використанням даного зразка провели комплексні лабораторні дослідження з метою отримання інформації про процес формоутворення брикетів з відходів прокатного виробництва. Суміш для їх отримання в своєму складі містила в різних пропорціях прокатну окалину і технологічну зв'язку із заданою вологістю. Як комплексного сполучного матеріалу використовували слабовипалений доломіт, змішаний з церезитом.
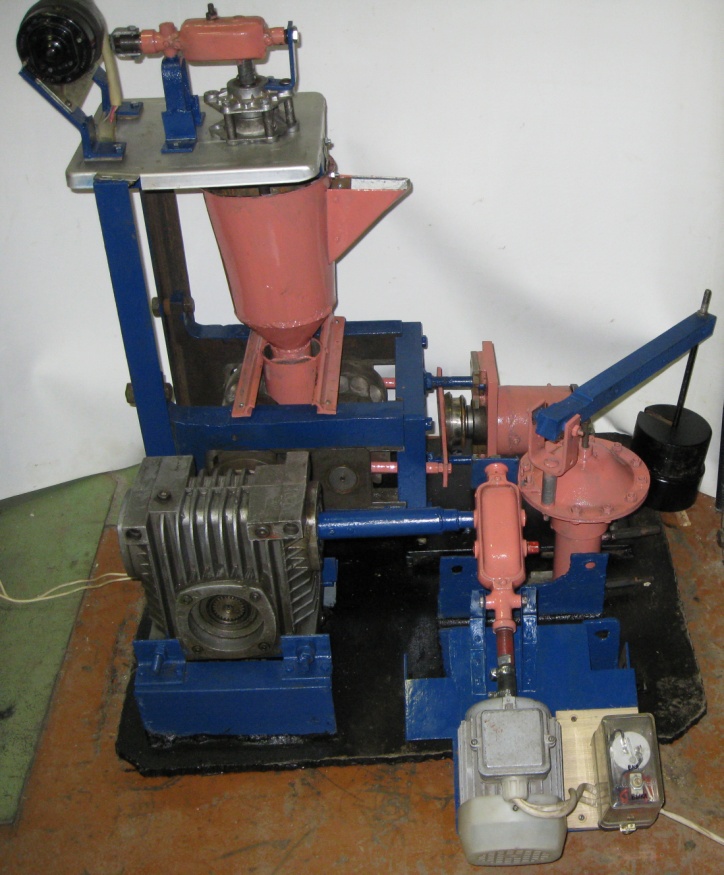
Малюнок 2 – Експериментальний зразок двовалкового брикетного преса.
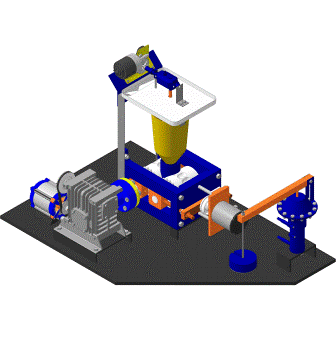
Малюнок 3 – Тривимірна модель установки преса.
(Анімація: обсяг 223 кб, кадрів 11, кількість циклів повторень 14, затримка між кадрами 100 мс)
Результати випробувань отриманих брикетів на ударну міцність, проведені за стандартною методикою шляхом їх багаторазового скидання з висоти 2 м на металеву плиту і подальшим визначенням виходу фракції менш 5 мм, наведені в таблиці, дані якої свідчать про те, що зміст окалини і сполучних у вихідному матеріалі брикетуємої маси має становити 60–70 і 30–40% відповідно.
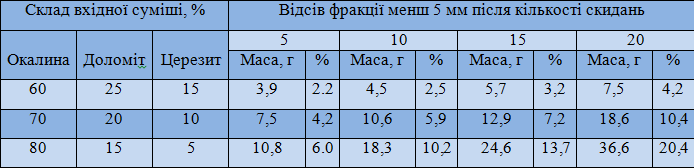
Таблиця 1 – Результати випробувань отриманих брикетів з прокатної окалини на ударну міцність.
Отримані після брикетування промислові відходи можна використовувати в якості замінників металевої шихти, паливних і відновлювальних добавок, регуляторів шлакового режиму, розкислювачів і легуючих.
2.3. Економічна ефективність використання брикетного преса в умовах мікро-заводів при переробці побічних продуктів промислового виробництва.
Зниження рівня витратних показників при спорудженні мікро-заводу і організації на ньому виробництва металопродукції з використанням в якості шихти пройшли попередню підготовку відходів підприємств гірничо-металургійного комплексу, дозволяє прогнозувати скорочення терміну окупності таких підприємств в порівнянні з міні-заводами, для яких він в даний час становить від 5 до 7 років. Поряд з інвестиційною привабливістю важливим спонукальним мотивом до початку розвитку мікро-заводів в країнах, що входять до складу СНД, є назріла необхідність в дієвих заходи щодо поліпшення екологічної обстановки в їх промислово розвинених регіонах. Цьому буде сприяти скорочення обсягів накопичуваних в відвалах і шламосховищах відходів завдяки їх переробці в чавун і сталь[11][12][13].
Результати аналізу статистичних даних про розмір капітальних вкладень, необхідних для будівництва металургійних підприємств, свідчать про те, що пуск заводу повного циклу передбачає витрати не менше 1 тис. Доларів на тонну запланованого річного виробництва металопродукції, у міні-заводу даний показник знижується в два рази і становить 500–600 дол./т. Тому при введенні в експлуатацію мікро-заводу слід очікувати подальшого зниження необхідних інвестицій. Даний прогноз заснований на тому, що мікро-завод може функціонувати як допоміжний ділянку ливарного цеху великого машинобудівного підприємства або базуватися на території раніше припинили виробництво місцевих заводів різного профілю, включаючи ремонтні і домобудівні. У цьому випадку за рахунок часткового або повного використання наявної інфраструктури значно знизяться капітальні витрати на фундаментні та будівельні роботи. Варто окремо зупинитися на зниженні виробничих витрат в умовах випуску металопродукції на мікро-заводах, обумовленому зменшенням її собівартості. Орієнтовні розрахунки витрат на отримання тонни продукції в умовах переробки промислових металлоємких відходів з використанням кисневого конвертера з обертовим корпусом, з урахуванням підвищеної витрати вогнетривів на його футерування через інтенсивне механічного перемішування розплаву, показали, що собівартість стали знижується приблизно на 10 % і це пов'язано з дешевизною вихідної шихти.
ВИСНОВОК
В результаті даної роботи виконано аналіз перспектив застосування брикетного преса в умовах мікро-заводів з переробки шихти з підвищеним вмістом шкідливих домішок, а також побічних продуктів металургійного виробництва, що включають цінні компоненти. Відповідно до зазначеної концепцією мікро-завод повинен включати підготовчу ділянку для огрудкування методом брикетування дрібнофракційних відходів вуглевидобувної, коксохімічної та металургійної промисловості в якості основного на підприємстві; плавильні відділення з печами або агрегатами, що дозволяють виплавляти чавун і сталь; ливарний і (або) розливний проліт, в якому можна одержувати виливки, а також заготовки для заключного прокатного переділу. Економічна ефективність виробництва продукції на мікро-заводі обумовлена порівняно низькою вартістю переробляються шихтових матеріалів.
СПИСОК ВИКОРИСТАНИХ ДЖЕРЕЛ
- Робин Виннер. Переработка вторичного сырья // Металлолом. – 2011 – №2 – С.9
- Иванченко В.В. Нерудные материалы в металлургических шламах ОАО КГМК
Криворожсталь
/ В.В. Иванченко, А.В. Кекух, П.И. Оторвин и др. // Металлург. и горноруд. пром-сть. – 2004. – № 3. – С. 17–21. - Классен П.В. Гранулирование / П.В. Классен, И.Г. Гришаев, И.П. Шомин. – М.: Химия, 1991. – 320 с.
- Коузов П.А. Основы анализа дисперсного состава промышленных пылей и измельченных материалов / П.А. Коузов. – Л.: Химия, 1987. – 264 с.
- Производство конвертерной извести во вращающихся печах с шахтным подогревателем: Технологическая инструкция ТИ 232–163–98. – ОАО Металлургический комбинат
Азовсталь
. – 1998. – 30 с. - Монастырёв А.В. Печи для производства извести: Справочник / А.В. Монастырёв, А.В. Александров. – М.: Металлургия, 1979. – 232 с.
- Смирнов А.Н., Сафонов В.М., Дорохова Л.В. Металлургические мини-заводы.- Донецк: ООО
Норд-Пресс
, 2005.– 465 с. - Овчинников А.М. Модернизация оборудования и реконструкция заводов черной металлургии за рубежом // Черная металлургия: Бюл. ин-та
Черметинформация
. 2016. № 2. С. 96 – 100. - Кокорин В.Н., Григорьев А.Н., Кокорин М.В. и др. Промышленный рециклинг техногенных отходов.- Ульяновск: УлГТУ, 2005.– 42 с.
- Далмиа И.К. Производство и применение в доменной печи брикетов нового поколения // Металлург. 2012. № 3. С. 39 – 41.
- Еронько С.П., Климович Н.А. Перспективы использования и проблематика создания мини-агрегата для переработки некачественной шихты и металлсодержащих отходов // Черная металлургия: Бюл. ин-та
Черметинформация
. 2016. № 5. С. 26 – 31. - Сафонов В. М., Смирнов А.Н. Ядро мини-металлургии. Современная электродуговая печь: основные параметры и концептуальные решения // Металл. 2004. № 10 (58). С. 28 – 36.
- Бойченко Б.М., Охотский В.Б., Харлашин П.С. Конвертерное производство стали: теория, технология, качество стали, конструкция агрегатов, рециркуляция материалов и экология.– Днепропетровск: РВА
Днепро-ВАЛ
, 2006.– 452 с..