Реферат по теме выпускной работы
Содержание
- Введение
- 1. КРАТКАЯ ХАРАКТЕРИСТИКА СЫРЬЯ, ИСПОЛЬЗУЕМОГО ПРИ БРИКЕТИРОВАНИИ
- 1.1. Материалы, используемые при брикетировании
- 1.2. Традиционные связующие, используемые при брикетировании
- 2. ПЕРСПЕКТИВЫ ИСПОЛЬЗОВАНИЯ БРИКЕТИРОВАНИЯ ПРИ ПЕРЕРАБОТКЕ ПРОМЫШЛЕННЫХ ОТХОДОВ В УСЛОВИЯХ МИКРО-ЗАВОДОВ
- 2.1. Целесообразность применения микро-заводов по переработке металлосодержащих отходов
- 2.2. Брикетирование как основной способ подготовки вторичного сырья к переработке на мини-предприятии.
- 2.3. Экономическая эффективность использования брикетного пресса в условиях микро-заводов при переработке побочных продуктов промышленного производства.
- ЗАКЛЮЧЕНИЕ
- СПИСОК ИСПОЛЬЗОВАННЫХ ИСТОЧНИКОВ
Введение
Проблемы, связанные с увеличением доли амортизационного лома с повышенным содержанием нежелательных примесей и накоплением в отвалах металлсодержащих побочных промышленных продуктов, наносящих вред окружающей среде, потребовали принятия действенных мер по их решению. В связи с этим свое время были основаны Европейская ассоциация по шлаку и Институт промышленной циркуляции вторичного сырья. По данным, опубликованным этими организациями, суммарный объем утилизации металлургических шлаков в развитых странах уже превысил 93 %, а переработка промышленных отходов позволяет ежегодно получать полезные товары на сумму, превышающую 70 млрд. долларов[1].
Совершенно иная картина, отражающая состояние дел в данной области человеческой деятельности, наблюдается в странах СНГ. Например, в Украине площадь, занимаемая свалками промышленных отходов, превышает 160 тыс. гектаров, а их ежегодный прирост уже достиг 1 млрд. тонн.
В Российской Федерации только в зоне расположения Магнитогорского металлургического комбината за полувековой промежуток времени его работы в шламохранилищах накопилось более 11 млн. тонн побочных продуктов с содержанием в них железа до 30 %.
Постоянно растущие темпы накопления вторичных сырьевых материалов с достаточно высокой концентрацией в них ценных компонентов вызывают насущную необходимость их рециклинга. Зарубежный опыт позволяет сделать вывод о том, что переработку и утилизацию отходов черной металлургии целесообразно выполнять в условиях специального технологического комплекса, являющегося микро-заводом с неполным металлургическим циклом.
1. КРАТКАЯ ХАРАКТЕРИСТИКА СЫРЬЯ, ИСПОЛЬЗУЕМОГО ПРИ БРИКЕТИРОВАНИИ
1.1. Материалы, используемые при брикетировании
В металлургическом производстве используют большое количество материальных ресурсов, имеющих общее, терминологически установившееся название: сырьё, сырьё и материалы или сырьевые (сырые) материалы. Технологическое топливо в виду его важности, особого влияния на металлургические процессы, а также высокой стоимости выделено в отдельную группу.
По назначению и характеру потребления сырые металлургические материалы делятся на основные и вспомогательные. Основные материалы составляют главное содержание продукта, например, руды, концентраты. Вспомогательные материалы используют в процессе производства как добавочные и прочие материалы, улучшающие технологический процесс и качество продукции, в частности, флюсы, легирующие добавки и др.
По источникам образования все материалы подразделяют на первичные, свежие материалы и оборотные, вторичные материалы или отходы. К оборотным материалам относят используемые отходы, просыпи, возвраты, побочные и попутные продукты.
Под отходами металлургического производства в широком смысле слова следует понимать сырьё, материалы и энергоресурсы, в силу тех или иных причин не использованные для получения основной продукции. Отходы являются неизбежным элементом существующей технологии производства металлов.
Показателем, достаточно полно характеризующим степень совершенства технологии, уровень её безотходности, является коэффициент использования материалов Км, который для чёрной металлургии составляет 0,4. Процесс можно считать материально безотходным, если Км > 0,9 и малоотходным – при Км = 0,8–0,9.
В дальнейшем под отходами будем понимать сырые материалы или продукты их неполной обработки, выведенные из технологического процесса (отсевы, просыпи, шламы, пыли), а также продукты вторичного окисления (окалина, сварочный шлак и т.п.).
Поскольку для окускования брикетированием можно использовать только измельчённые виды сырья крупностью менее 10 мм с определённым фракционным составом, в дальнейшем в качестве основного компонента брикетируемой смеси будем рассматривать только твёрдые измельчённые материалы.
Важнейшими брикетирующими характеристиками такого материала являются прочность, плотность, аутогезионные (адгезионные и когезионные) свойства, форма частиц и их крупность, а также минералогический (химический) состав. В частности, из непрочного и пористого мела сложно получить достаточно прочные брикеты.
Низкие аутогезионные свойства песка и угля также не позволяют получить из них брикеты высокой прочности при обычном давлении и без использования связующего. Брикеты из крупной и мелкой руды, спрессованные в одинаковых условиях, будут иметь существенные отличия в прочности: брикеты из мелкой руды окажутся значительно прочнее.
Существенное различие по прочности даёт прессование смесей одинакового фракционного, но различного химико-минералогического состава. Так, алюмокальциевые соединения придают брикетам значительно более высокую прочность, чем феррокальциевые.
В брикетировании материалов следует учитывать и противоречивое влияние отдельных факторов. Так, удельная поверхность, гранулометрический состав и влажность являются такими факторами. В частности, гранулометрический состав оказывает двоякое влияние на брикетируемость. Крупнозернистая шихта прессуется лучше, чем мелкозернистая, однако в целом прочность брикетов из крупнозернистой шихты меньше, чем из мелкозернистой по причине малой поверхности контакта частиц. Для достижения хорошей прессуемости и высокой плотности брикетов необходим соответствующий подбор гранулометрического состава шихты.
Форма частиц оказывает сильное влияние на насыпную массу, спекаемость, сыпучесть (текучесть), а следовательно, прессуемость и прочность брикетов. Частицы шероховатой и неправильной формы зацепляются лучше, чем гладкой и правильной, а меньшая насыпная масса и плохая пластичность ухудшают брикетируемость шихты.
Удельная поверхность зависит от размера частиц и оказывает двоякое влияние на брикетируемость. С одной стороны, высокая удельная поверхность увеличивает силы сцепления, а с другой – возрастает адсорбированность газов и других веществ и увеличивается работа на преодоление трения частиц друг о друга и стенки пресс-формы.
Аутогезионные свойства являются важной характеристикой измельчённых материалов и пылей. Они во многом определяют прочность брикетов и зависят от размера, формы, удельной поверхности и материала частиц. По своим размерам и форме частицы чрезвычайно разнообразны (рис. 1) .
В зависимости от задач, поставленных перед утилизацией отходов, вещественного состава или иных критериев могут применяться различные системы их классификации [2].
В случае окускования отходов брикетированием первичное сырьё, материалы и отходы классифицируют:
– по месту производства, возникновения или источникам образования;
– по характеру образования и удаления;
– по способу добычи, извлечения или улавливания;
– по химическому (вещественному) составу;
– по физическим свойствам;
– по другим (в т.ч. технологическим) критериям.
По месту производства первичное сырьё и материалы подразделяют на поставляемые со стороны и собственные. Качество поставляемых материалов регламентировано соответствующими стандартами и договорными техническими условиями [3].
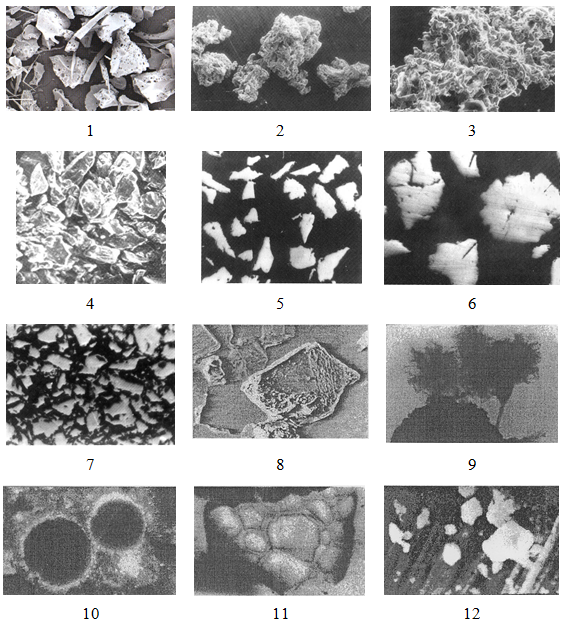
Рисунок 1 – Внешний вид и структура частиц некоторых материалов, используемых для брикетирования
Качество собственных материалов регламентируют внутренними техническими условиями, а для отходов устанавливают пониженные требования, стимулирующие их использование внутри предприятия.
В качестве классификации отходов по месту возникновения может служить номенклатура шламов, представленная в работах.
По характеру образования и удаления все отходы подразделяют на уносы с отходящими газами (пыли); просыпи, осыпи, смывы (шламы); сливы, натёки, остатки (шлаки, сварочный шлак, скардовины). В металлургии наибольшие проблемы связаны с утилизацией первой и с частью отходов второй группы.
Способы улавливания подразделяют на сухие и мокрые. Пыли химически более активны, чем вылежанные влажные шламы.
По химическому (вещественному) составу отходы группируют по двум уровням – виду (наличию) и содержанию основного компонента. По виду основного компонента отходы классифицируют на железосодержащие, марганецсодержащие и др., а также отходы, детерминируемые по вредному компоненту.
По содержанию основного компонента отходы классифицируют на богатые, относительно-богатые и бедные. Уровень богатства определяют сопоставлением с аналогичным первичным сырьем. По вещественному (компонентному) составу шламы представляют собой смеси остатков сырья и материалов, частично подвергшихся обработке, уносы, возгоны и вторичные оксиды.
К физическим свойствам, определяющим пригодность шламов к окускованию гранулированием, относят плотность, дисперсность, адгезионную способность и другие свойства.
Плотность является важным свойством материалов, от которого зависит эффективность того или иного способа окускования. Так, при агломерации желательно, чтобы объёмная плотность шихты принимала максимальное значение при некотором оптимальном значении насыпной плотности, обеспечивающей нужную газопроницаемость. При брикетировании, наоборот, следует стремиться к увеличению насыпной плотности, что уменьшает усадку материала и позволяет получать более прочные брикеты.
Различают истинную (удельную), кажущуюся, объёмную и насыпную, в т. ч. при встряхивании, плотности сыпучих материалов [4][5].
Истинная плотность – плотность материала, из которого состоят частицы.
Кажущаяся плотность – это масса частиц единицы объёма материала с учётом закрытых в частицах пор.
Объёмная плотность – это масса единицы объёма материала с учётом закрытых и открытых пор.
Насыпная плотность – это масса единицы свободно насыпанного объёма дисперсного материала. В насыпной объём, кроме объёма материала, входит объём пространства между частицами и пор. Встряхивание или воздействие вибрацией на ёмкость обеспечивает насыпной плотности наиболее плотную упаковку частиц, в которой объём пространства между частицами практически минимален. Такую плотность называют плотностью при встряхивании.
1.2. Традиционные связующие, используемые при брикетировании
При брикетировании многих видов измельчённого сырья, обладающего недостаточными аутогезионными свойствами, даже при высоких давлениях (180 МПа и более) обычным холодным прессованием получать прочные брикеты без их спекания не представляется возможным. В таких случаях используют связующие – вспомогательные материалы, улучшающие слипаемость частиц и повышающие прочность брикетов до заданного уровня.
Поскольку добавки таких материалов могут составлять от нескольких до 10 % и более, они должны соответствовать следующим требованиям [6].
• Обладать высокими аутогезионными свойствами, т.е. обеспечивать высокую холодную и горячую прочность при минимальном расходе связующего.
• Обеспечивать быструю схватываемость.
• Вносить минимальное количество вредных, балластных и других примесей, небезопасных для обслуживающего персонала и снижающих качество конечного продукта.
• Не ухудшать условий плавки брикетов.
• Быть распространёнными и обладать невысокой стоимостью.
• Не требовать сложных приёмов и операций по их использованию.
• Обеспечивать минимальную влагостойкость.
Связующее является определяющим условием прочности и в значительной мере – восстановимости брикетов. Увеличение расхода связующего, повышая прочность, приводит не только к снижению полезных компонентов в брикетах, но и к значительному их удорожанию.
К распространённым неорганическим связующим следует отнести гашёную известь, жидкое стекло, глинозёмистый и портландский цементы. Однако многие из них обладают существенными недостатками. Так, гашёная известь и портландцемент при нагревании отдают гидратную влагу и теряют прочность, жидкое стекло содержит значительное количество щелочей и двуокись кремния, а глинозёмистый цемент к тому же чрезвычайно дорог. При этом лучшие вяжущие характеристики обнаруживает жидкое стекло и глинозёмистый цемент.
К распространённым органическим связующим относят каменноугольные и нефтяные смолы, меласса, отходы гидролизной и целлюлозной промышленности и т.п. Общим недостатком органических связующих является их пиролиз или выгорание при высоких температурах с потерей прочности, а также внос в брикеты значительного количества серы.
Большинство органических связующих могут использоваться для получения брикетов с высокими показателями холодной прочности. При нагреве таких брикетов связка разрушается или сгорает, в результате чего они теряют бoльшую часть прочности, рассыпаются под давлением верхних слоёв материала и выносятся потоком газов из агрегата. Более стойкие связующие при сгорании образуют спёкшийся шлак, который скрепляет частицы брикетов, препятствуя их разрушению.
Связующие неорганического происхождения, помещаясь между частицами оксидов железа и восстановителя, ухудшают восстановимость. Органические связующие, частично заменяя восстановитель, обычно вносят нежелательные примеси, в т.ч. серу. Наряду с этим некоторые виды связующих при нагреве могут способствовать образованию легкоподвижных фаз, например, фаялита, что желательно для усадки восстанавливающихся брикетов.
К комбинированным связующим относят смеси различных связующих. Эти смеси позволяют улучшить положительные и снизить негативные свойства. Например, смесь, содержащая жидкое стекло и лигносульфонат, вносит пониженное количество щелочей, кремнезёма или серы, чем каждое связующее в отдельности, при одновременном обеспечении высокой механической прочности брикетов.
В качестве связующих предпочтительнее использовать наиболее распространённые и хорошо исследованные материалы:
– известь гашёная (портландит);
– жидкое стекло;
– портландцемент;
– глинозёмистый цемент;
– магнезиальный цемент;
– бишофит;
– бентонит;
– лигносульфонат порошковый;
– сульфитно-спиртовая барда (порошковая и в растворе);
– лигнин;
– меласса.
2. ПЕРСПЕКТИВЫ ИСПОЛЬЗОВАНИЯ БРИКЕТИРОВАНИЯ ПРИ ПЕРЕРАБОТКЕ ПРОМЫШЛЕННЫХ ОТХОДОВ В УСЛОВИЯХ МИКРО-ЗАВОДОВ
2.1. Целесообразность применения микро-заводов по переработке металлосодержащих отходов
Перспектива появления малых предприятий, специализирующихся на переработке вторичных ресурсов, обусловлена значительно меньшими инвестициями, требующимися при их запуске, а также возможностью более гибкого решения вопроса поставок в небольших объемах металлопродукции машиностроительным заводам, ориентированных на выпуск и ремонт вспомогательного технологического оборудования для ряда отраслей отечественной экономики. Кроме того, для обеспечения ритмичной работы микро-завода нет необходимости прибегать к услугам железнодорожного транспорта, так как логистика и объемы грузоперевозок в данном случае с меньшими издержками могут быть обеспечены автомобильными перевозками[7].
В мировой практике уже известны положительные примеры применения различных технологий получения чугуна на предприятиях с годовым производством в несколько десятков тысяч тонн. Так консорциумом, возглавляемым фирмой ThyssenKrupp Steel, сконструирована кислородная вагранка, позволившая выплавлять из отходов 15 т/ч передельного чугуна.
Ангольская металлургическая компания Companhia Siderurgica do Cuchi (CSC) в 2016 году запустила завод по выпуску передельного чугуна производительностью 96 тыс. т/год с доменной печью объёмом 119 м3, в которой для восстановления железной руды предусмотрено использование древесного угля [8].
На экспериментальном заводе ООО Энергокапитал
, г. Макеевка Донецкой области, внедрена приобретённая в Китае технология, обеспечивающая переработку в мини-доменной печи объёмом 128 м3 окатышей из угольного и металлического шламов в качественный чугун. При этом получаемые попутные продукты – гранулированный шлак и доменный газ – в дальнейшем используют соответственно в качестве строительного материала и топлива в установках, генерирующих электроэнергию.
Достигнутые показатели технико-экономической эффективности применения кислородных мини-вагранок и доменных печей для получения передельного и товарного чугуна из промышленных отходов свидетельствует о целесообразности поиска вариантов использования малых плавильных агрегатов, позволяющих перерабатывать жидкий чугун и твердые металлсодержащие отходы с повышенным содержанием вредных примесей в сталь приемлемого качества и тем самым увеличивать добавленную стоимость конечного продукта предприятия.
В структуру такого микро-завода должны входить подготовительное, плавильное и разливочное отделения.
2.2. Брикетирование как основной способ подготовки вторичного сырья к переработке на мини-предприятии
Необходимость в предварительной подготовке исходных сырьевых материалов обусловлена тем, что ценные для сталеплавильного передела компоненты содержатся в шламах, шлаках, прокатной окалине и стружке, т.е. в мелкофракционных материалах, которые нельзя применять в существующем состоянии в качестве твердой части шихты электродуговой печи или кислородного конвертера. Поэтому исходное сырье подлежит обязательному окускованию. Для этой цели приоритетным является процесс брикетирования, выгодно отличающийся по ряду показателей от способов агломерации и производства окатышей. При этом с целью сохранения неизменности состава и свойств ингредиентов, образующих структуру брикетов, для их получения предпочтительно использовать способ холодного брикетирования, отличающийся простотой реализации и малой энергоемкостью. Однако такая технология брикетирования требует тщательного подбора состава и процентного содержания прессуемых материалов, а также применяемых связующих добавок органического или минерального происхождения [9][10].
В настоящее время для окомкования мелкодисперсных материалов используют штемпельные и двухвалковые прессы. Для успешной реализации процесса формообразования брикетов достаточной прочности, с минимальными энергетическими затратами и высокой производительностью рекомендуется применять двухвалковые прессы, снабженные устройствами предварительного уплотнения прессуемого материала. Они в сравнении со штемпельными прессами цикличного действия при прочих равных условиях обеспечивают большую производительность с меньшим в 1,5 раза энергопотреблением.
На кафедре механического оборудования заводов черной металлургии Донецкого национального технического университета на основании результатов проводившихся исследований разработан малогабаритный двухвалковый пресс производительностью до 3 т/час для получения брикетов, используемых в качестве шихты при выплавке чугуна в доменных печах объемом до 130 м3, а также для частичной замены металлолома в процессе производства стали в электродуговых печах или кислородных конвертерах тоннажностью от 3 до 10 т. Данный пресс предназначен для работы в условиях микро-завода по переработке металлсодержащих отходов. На рисунке 2 показан его экспериментальный образец. На рисунке 3 анимирован принцип его работы. С использованием данного образца провели комплексные лабораторные исследования с целью получения информации о процессе формообразования брикетов из отходов прокатного производства. Смесь для их получения в своем составе содержала в различных пропорциях прокатную окалину и технологическую связку с заданной влажностью. В качестве комплексного связующего материала использовали слабообожженный доломит, смешенный с церезитом.
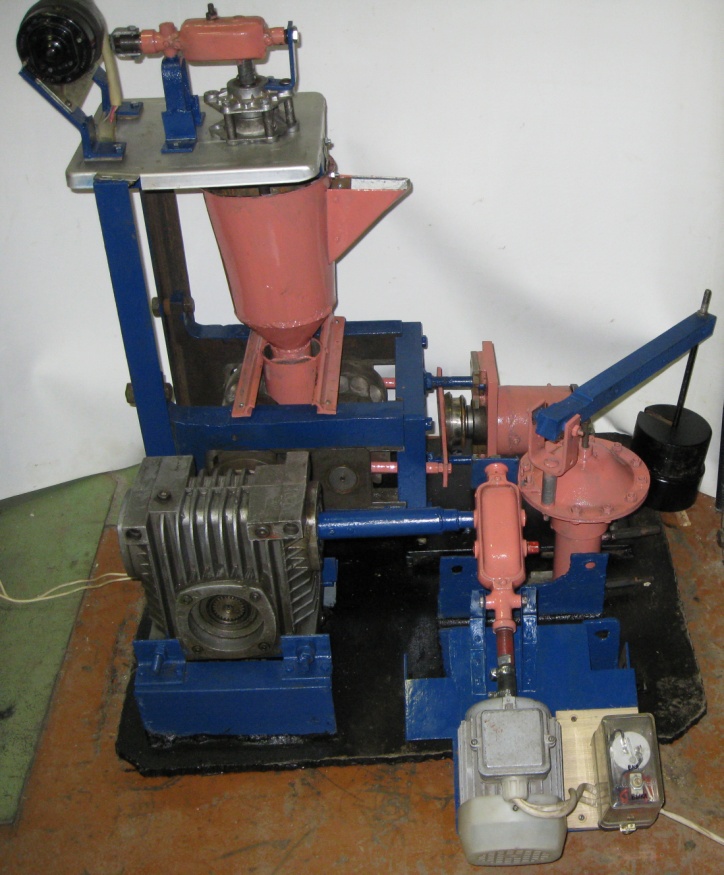
Рисунок 2 – Экспериментальный образец двухвалкового брикетного пресса
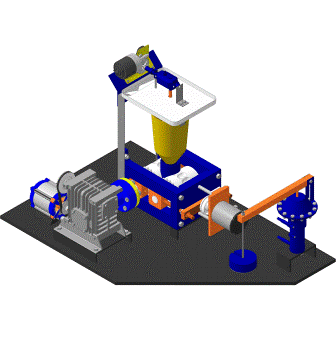
Рисунок 3 – Трёхмерная модель установки пресса
(анимация: объём 223 кб, кадров 11 , количество циклов повторений 14, задержка между кадрами 100 мс)
Результаты испытаний полученных брикетов на ударную прочность, проведенные по стандартной методике путем их многократного сбрасывания с высоты 2 м на металлическую плиту и последующим определением выхода фракции менее 5 мм, приведены в таблице, данные которой свидетельствуют о том, что содержание окалины и связующих в исходном материале брикетируемой массы должно составлять 60 – 70 и 30 – 40 % соответственно.

Таблица 1 – Результаты испытаний полученных брикетов из прокатной окалины на ударную прочность
Полученные после брикетирования промышленные отходы можно использовать в качестве заменителей металлической шихты, топливных и восстановительных добавок, регуляторов шлакового режима, раскислителей и легирующих.
2.3. Экономическая эффективность использования брикетного пресса в условиях микро-заводов при переработке побочных продуктов промышленного производства.
Снижение уровня затратных показателей при сооружении микро-завода и организации на нем производства металлопродукции с использованием в качестве шихты прошедших предварительную подготовку отходов предприятий горно-металлургического комплекса, позволяет прогнозировать сокращение срока окупаемости таких предприятий в сравнении с мини-заводами, для которых он в настоящее время составляет от 5 до 7 лет. Наряду с инвестиционной привлекательностью важным побудительным мотивом к началу развития микро-заводов в странах, входящих в состав СНГ, является назревшая необходимость в действенных мерах по улучшению экологической обстановки в их промышленно развитых регионах. Этому будет способствовать сокращение объемов накапливаемых в отвалах и шламохранилищах отходов благодаря их переработке в чугун и сталь.[11][12][13]
Результаты анализа статистических данных о размере капитальных вложений, требуемых для строительства металлургических предприятий, свидетельствуют о том, что пуск завода полного цикла предполагает затраты не менее 1 тыс. долларов на тонну запланированного годового производства металлопродукции, у мини-завода данный показатель снижается в два раза и составляет 500 – 600 дол./т. Поэтому при вводе в эксплуатацию микро-завода следует ожидать дальнейшего снижения необходимых инвестиций. Данный прогноз основан на том, что микро-завод может функционировать как вспомогательный участок литейного цеха крупного машиностроительного предприятия или базироваться на территории ранее прекративших производство местных заводов разного профиля, включая ремонтные и домостроительные. В этом случае за счет частичного или полного использования имеющейся инфраструктуры значительно снизятся капитальные затраты на фундаментные и строительные работы. Особо следует остановиться на снижении производственных расходов в условиях выпуска металлопродукции на микро-заводах, обусловленном уменьшением ее себестоимости. Ориентировочные расчеты затрат на получение тонны продукции в условиях переработки промышленных металлсодержащих отходов с использованием кислородного конвертера с вращающимся корпусом, с учетом повышенного расхода огнеупоров на его футеровку из-за интенсивного механического перемешивания расплава (данные таблицы), показали, что себестоимость стали снижается примерно на 10 % и это связано с дешевизной исходной шихты.
ЗАКЛЮЧЕНИЕ
В результате данной работы выполнен анализ перспектив применения брикетного пресса в условиях микро-заводов по переработке шихты с повышенным содержанием вредных примесей, а также побочных продуктов металлургического производства, включающих ценные компоненты. В соответствии с обозначенной концепцией микро-завод должен включать подготовительный участок для окускования методом брикетирования мелкофракционных отходов угледобывающей, коксохимической и металлургической промышленности в качестве основного на предприятии; плавильные отделения с печами или агрегатами, позволяющими выплавлять чугун и сталь; литейный и (или) разливочный пролет, в котором можно получать отливки, а также заготовки для заключительного прокатного передела. Экономическая эффективность производства продукции на микро-заводе обусловлена сравнительно низкой стоимостью перерабатываемых шихтовых материалов.
Список источников
- Робин Виннер. Переработка вторичного сырья // Металлолом. – 2011 – №2 – С.9
- Иванченко В.В. Нерудные материалы в металлургических шламах ОАО КГМК
Криворожсталь
/ В.В. Иванченко, А.В. Кекух, П.И. Оторвин и др. // Металлург. и горноруд. пром-сть. – 2004. – № 3. – С. 17–21. - Классен П.В. Гранулирование / П.В. Классен, И.Г. Гришаев, И.П. Шомин. – М.: Химия, 1991. – 320 с.
- Коузов П.А. Основы анализа дисперсного состава промышленных пылей и измельченных материалов / П.А. Коузов. – Л.: Химия, 1987. – 264 с.
- Производство конвертерной извести во вращающихся печах с шахтным подогревателем: Технологическая инструкция ТИ 232–163–98. – ОАО Металлургический комбинат
Азовсталь
. – 1998. – 30 с. - Монастырёв А.В. Печи для производства извести: Справочник / А.В. Монастырёв, А.В. Александров. – М.: Металлургия, 1979. – 232 с.
- Смирнов А.Н., Сафонов В.М., Дорохова Л.В. Металлургические мини-заводы.- Донецк: ООО
Норд-Пресс
, 2005.– 465 с. - Овчинников А.М. Модернизация оборудования и реконструкция заводов черной металлургии за рубежом // Черная металлургия: Бюл. ин-та
Черметинформация
. 2016. № 2. С. 96 – 100. - Кокорин В.Н., Григорьев А.Н., Кокорин М.В. и др. Промышленный рециклинг техногенных отходов.- Ульяновск: УлГТУ, 2005.– 42 с.
- Далмиа И.К. Производство и применение в доменной печи брикетов нового поколения // Металлург. 2012. № 3. С. 39 – 41.
- Еронько С.П., Климович Н.А. Перспективы использования и проблематика создания мини-агрегата для переработки некачественной шихты и металлсодержащих отходов // Черная металлургия: Бюл. ин-та
Черметинформация
. 2016. № 5. С. 26 – 31. - Сафонов В. М., Смирнов А.Н. Ядро мини-металлургии. Современная электродуговая печь: основные параметры и концептуальные решения // Металл. 2004. № 10 (58). С. 28 – 36.
- Бойченко Б.М., Охотский В.Б., Харлашин П.С. Конвертерное производство стали: теория, технология, качество стали, конструкция агрегатов, рециркуляция материалов и экология.– Днепропетровск: РВА
Днепро-ВАЛ
, 2006.– 452 с..