Abstract on the topic of graduation work
When writing this essay, the master's work has not yet been completed. Final completion: June 2021. The full text of the work and materials on the topic can be obtained from the author or his manager after that date.
Content
- 1. Introduction
- 2.Purpose and objectives of the study, planned results
- 3.Research overview
- 3.1Analysis of technological capabilities and features of the use of modern CNC machines
- 3.2 Available data and practical experience to date
- Сonclusions
- List of sources
1.Introduction
Modern advances in cybernetics, electronics, computer technology and instrumentation have led to the creation of a programmed control system for a machine tool, which are currently widely used in industry. A feature of these machines is that the movements of the executive bodies are determined by the number of pulses, recorded in a certain sequence on the storage medium. This sequence of pulses forms the control program of the CNC machine. This greatly simplifies and reduces the cost of setting up equipment for the release of parts. Therefore, the purpose of this work is to study the technological capabilities and features of the use of modern CNC machines.
2.Purpose and objectives of the study, planned results
The purpose of this work is: increasing the efficiency of processing parts on CNC machines, through the use of modern equipment, cutting tools, tooling, software and advanced processing strategies. To achieve this goal in the master's work, the following tasks were set:
- Analyze literary sources and catalogs to identify the most productive and durable cutting tools, as well as the most advanced tooling.
- Develop your own processing strategies and evaluate their performance, taking into account the possible reduction in metal waste.
- To develop a methodology for choosing strategies for processing and cutting tools.
- Carry out experimental research on the implementation of increasing the efficiency of processing on CNC machines
- Savings in the implementation of these techniques.
3. Research overview
3.1 Analysis of technological capabilities and features of the use of modern CNC machines
All machines with an automated cycle, according to the type of control, are subdivided into machines and cycle control systems and machines with numerical control systems. The first – are simpler, since only the machine cycle is programmed in them, and the values of the working displacements are set in a simplified way, for example, using stops. In CNC machines, control is carried out from the program, in which both geometric and technological information is entered in numerical form.
In CNC systems, the program is specified as an array of information. Control information for CNC systems is discrete and its processing in the control process is carried out by digital methods. Control of technological cycles is almost everywhere carried out using programmable logic controllers, implemented on the basis of the principles of digital electronic computing devices
The block diagram of the CNC system is shown in Fig. 1, a. The drawing of the part (BH) to be processed simultaneously enters the program preparation system (SPP) and the technological preparation system (STP), which provides the program preparation system with data on the technological process and processing modes. Based on these data, a control program (UP) is developed. After that, the adjusters install fixtures and cutting tools on the machine. The installation of the blank and removal of the finished part is carried out by an operator or an automatic loader. The reader (SU) reads information from the program carrier. The information enters the CNC device, which issues control commands to the target mechanisms (CM) of the machine, carrying out the main and auxiliary movements of the processing cycle.
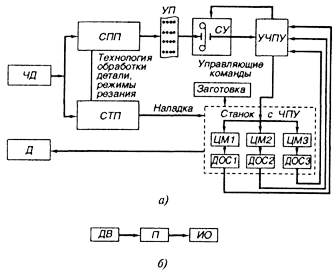
Figure 3.1 – Block diagram of the use of the CNC system and the target mechanism
The machine also contains several target mechanisms (Fig. 1, b), each of which includes: engine (DV); transfer (P), serving to convert energy and transfer it from the engine and the actual executive body (IO) (table, slide, support, spindle, etc.), performing coordinate movements.
The level of modern technology makes it possible to create three-dimensional computer models of parts of complex shaping tooling of dies and molds and manufacture them on CNC machines even in a single production. In this case, the preparation of the control program is carried out automatically based on the three-dimensional model of the product. This does not require the creation of prototypes, which significantly reduces the cost of production preparation.

Figure 3.1 – Machining the die part on a CNC machine
Recently, the development of CNC systems has undergone some changes. If earlier the only tendency in the development of such machines was the tendency to transform them into machining centers with tool magazines and manual compilation of control programs, then with the advent of powerful computers, it became possible to create control programs automatically, reducing to a minimum the amount of manual labor. This made it possible to develop control programs for processing complex three-dimensional surfaces without the need to describe them, used most often in the shaping parts of tooling dies and molds. However, the requirements for numerically controlled machine tools have changed. This happened mainly due to the increase in size and structural changes of the control program, and also a significant increase in the proportion of the main processing time with a corresponding decrease in the proportion of auxiliary time.
In this case, processing is carried out mainly with one tool for many hours in a row, and the machine loses its already familiar equipment: magazines, satellite tables, etc. At the same time, the number of controlled coordinates increased to five. But along with this, the requirements for the CNC system have grown significantly.
3.2 Available data and practical experience to date
Taking into account the current practical experience, the following requirements for modern CNC systems can be distinguished:
- The ability to enter (receive from an external medium or via a network) control programs of unlimited size, edit them and execute them as a whole.
- In order to reduce the main processing time, an advanced (for execution) decoding of the control program frames should be provided: –working out the movement without reducing the speed to zero at the end of the movement; –determination of limiting accelerations along controlled axes, taking into account the dynamic characteristics of the machine; –the ability to switch from one machining path to another at a working feed without braking and accelerating along a three-dimensional loop, calculated by the CAM system; –the ability to work at increased speeds of working feeds (up to 60 m / min).
- In order to reduce changeover time, access to the files and resources of the design and technological bureau should be provided through a standard network, including support for standard (including distributed) databases: –built-in function of three-dimensional correction of the tool path by the value of its radius; –the ability to integrate with a CAM server to perform a full correction of the NC based on the results of previous operations; –binding a set of control programs, subroutines, correctors, system parameters and service information to a specific product (project); –possibility of automated control of part and tool dimensions.
- In order to increase the utilization factor of equipment in the conditions of single and small-scale production – the ability to work together with a top-level control system based on standard network technologies, the ability to provide information support for planning and dispatching systems at the workshop or site level.
- In order to increase maintainability and reduce the time for troubleshooting – a visual representation of electrical signals in accordance with the electrical circuit of the machine and the operating algorithms given in the technical description.
- In order to ensure the flexibility of the system – the possibility of continuous improvement of the CNC system in accordance with the continuously growing requirements of modern production, in particular: quick adaptation to any technological equipment (including non-metal cutting equipment), integration with complex autonomous systems (for example, with vision systems), etc.
For the effective use of CNC machines, it is necessary to create a system of organized support as a complex of interacting activities subordinate to the main task – the production of high quality parts on time with minimal labor and cost. The work organization system should include a feasibility study for the use of CNC machines, a nomenclature of parts for processing on machines, a special structure of the system, proper maintenance of machines, automated development of control programs. The experience of domestic and foreign enterprises testifies to the advisability of installing CNC machines in one production room, creation of specialized workshops and sections. The location of the machines in one room creates conditions for better service, multi-station service, better planning and control over equipment operation, etc.
Сonclusions
Thus, the use of CNC machines in comparison with conventional equipment creates a number of technical and economic advantages. The productivity of these machines is higher with less space required. Labor productivity of workers is growing significantly.
A great effect is given by CNC machines when performing particularly complex operations, therefore, with their use, highly qualified workers are freed, and the costs of technological preparation of production, tool operation are sharply reduced, the content of the inspectors of the technical control department.
The main effect of using software equipment is to increase the equipment utilization up to 80-90% due to a sharp reduction in auxiliary time and time for equipment changeover.
List of sources
- "Электроник" , Системы ЧПУ // Загл. с титул. экрана.– Режим доступа – http://elektronik-chel.ru/literature/sistemyi-chpu.html. – (25.09.2020).
- StudFiles // Загл. с титул. экрана.– Режим доступа – https://studfile.net/preview/6021773/page:6/ – (26.09.2020).
- Николай Панышев, Дмитрий Ялымов: Система числового программного управления технологическим оборудованием // Загл. с титул. экрана.– Режим доступа – https://www.fastwel.ru/solutions/sistema-chislovogo-programmnogo-upravleniya-tekhnologicheskim-oborudovaniem-nc-2000/ – (26.09.2020).
- Гжиров Р.И., Серебреницкий П.П. Программирование обработки на станках с ЧПУ. Справочник. – Л:., Машиностроение, 1990. –592с.
- Гузеев В.И., Батуев В.А., Сурков И.В. Режимы обработки для токарных и сверлильно-фрезерно-расточных станков с числовым программным управлением. Справочник.– Санкт-Петербург: Машиностроение, 2007. –368с.
- Баранчиков В.И. . Программное обеспечение режимов резания / В.И. Баранчиков // Вестник машиностроения.–1993. – №3. – С. 45–46.
- Беллман Р. Прикладные задачи . динамического программирования / Р. Беллман. – Рипол Классик, 2013. – 464 с. .
- Бесекерский В.А. . Теория систем автоматического управления / В.А. Бесекерский, Е.П. Попов. – СПб. : Профессия, 2003. –752 с. .
- Вермель В. Геометрические модели . для программирования обработки на станках с ЧПУ / В. Вермель, П. Николаев // САПР и графика. –2001. – №1. – С. 38–40..
- Климов А.В. . Создание математической модели технологического оборудования с ЧПУ в концепции «интеграционной индустрии» [Электронный ресурс] / А.В. Климов, Н.С. Васильев // Сборник тезисов докладов конгресса молодых ученых. Электронное издание. – СПб: Университет ИТМО, 2015. – Режим доступа : http://kmu.ifmo.ru/collections_ar.