Реферат по теме выпускной работы
Содержание
- Введение
- 1. Технологический процесс как объект автоматизации. Цель проектирования и требования к устройству автоматизации
- 2. Критический обзор существующих решений и выбор базовой аппаратуры автоматизации
- 3. Обоснование направления автоматизации технологической установки
- 4. Алгоритмизация блока контроля линейности забоя
- 5. Разработка структурной схемы блока контроля линейности забоя
- Выводы
- Список источников
Введение
Вопросы проведения своевременной механизации технологических установок, модернизации или замене устаревшего оборудования, внедрения комплексной автоматизации на предприятии н данный момент чрезвычайно актуальны. Данный подход позволит повысить эффективность и интенсификацию технологических процессов, а следовательно улучшить производительность шахты в целом.
В настоящее время большое количество аварий на очистных участках шахт происходит из–за значительных искривления линии забоя, что в свою очередь приводит к значительным искажениям става призабойного конвейера, порыву его цепей и, к многодневным простоям лавы, а, значит, и значительным материальным потерям.
Решить этот вопрос можно путем оперативного контроля за расстоянием передвижки каждой секции крепи и соответственно става конвейера с определенным шагов и выдачи соответствующих сигналов управления на начало и конец передвижки механизированной крепи. Разрабатываемый блок должен работать в составе базовой аппаратуры автоматизации механизированного комплекса и дополнять его функционально.
Таким образом, вопрос разработки устройства автоматического контроля линейности забоя очень актуален в настоящее время.
1.Технологический процесс как объект автоматизации. Цель проектирования и требования к устройству автоматизации
Эксплуатация забойных машин, комплексов и агрегатов связана со значительными трудностями, обусловленными их непрерывным перемещением, разнообразными горно–геологическими условиями, пылегазовым режимом шахты, ее микроклиматом и другими факторами. Решение задачи автоматизации забойных машин позволит:
- повысить производительность машин путем более полного использования мощности их электродвигателей;
- освободить машиниста от функций управления машиной с последующим выводом его из забоя;
- повысить качество добытого угля и снизить его себестоимость;
- улучшить динамические качества машин, их надежность и продлить срок службы;
- включить забойные машины в подсистему АСУ
Очистные забои
.
Системы автоматизации горных машин должны удовлетворять ряду требований, связанных со спецификой шахтных условий работы, и общих требований, предъявляемых к системам управления. Они должны удовлетворять правилам безопасности, быть надежными в работе, обеспечивать автоматическое регулирование скорости подачи комбайна и положения исполнительных органов в профиле слоя с целью исключения обработки резцами боковых вмещающих пород. Системы автоматизации выемочных машин должны обеспечивать автоматическое отключение комбайна: при останове забойного конвейера, уходе комбайна от передвинутых секции крепи на расстояние более заданного, наличии препятствий на машинной дороге, превышении допустимой концентрации метана на исходящей струе и в месте работы комбайна, прекращать подачу воды в оросительное устройство комбайна по достижении им исходного положения по концам лавы.
Система автоматизации выемочного комбайна должна также обеспечивать: мгновенный останов комбайна при установке скорости подачи в нулевое значение; разгрузку тягового органа при останове комбайна с последующим стопорения приводной звездочки механизма подачи; снижение скорости подачи до нуля при пуске комбайна и длительных перегрузок электродвигателей, а также фиксацию нулевой скорости подачи; двустороннюю громкоговорящую связь и сигнализацию в лаве.
Система автоматизации рабочего цикла забойной машины содержит систему автоматического регулирования (САР) нагрузки электродвигателей; систему автоматического управления перемещением машины в профиле пласта; средства автоматического контроля местонахождения горной машины и наличия препятствий на ее пути. Работа выемочной машины в автоматическом режиме, кроме того, должна согласовываться с работой гидрофицированной крепи, скребкового конвейера и средствами его автоматической передвижки.
На рисунке 1 приведена технологическая схема очистных работ вместе со средствами механизации.
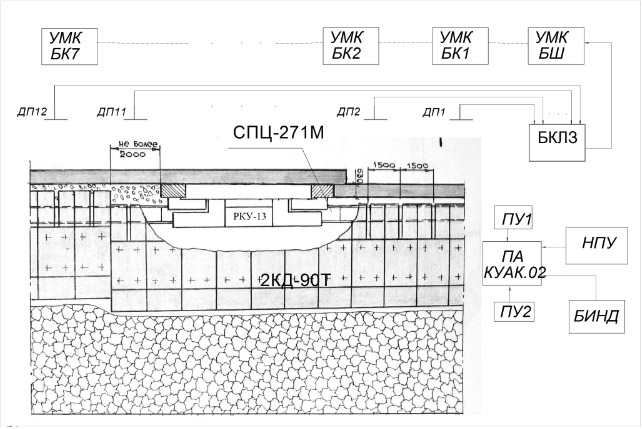
Рисунок 1 – Технологическая схема очистного забоя.
На данный момент большинство аппаратур автоматизации забойных машин и комплексов рассчитано на регулирование нагрузки на очистной комбайн, осуществление верного алгоритма пуска/останова механизмов очистного забоя, обеспечения необходимых защит и блокировок для безопасности труда рабочих забоя и создание локальной системы автоматизации АСУ ТП Очистные забои
.
Однако одной из проблем, которые фигурируют на данный момент при эксплуатации очистных комплексов является неравномерная передвижка секций крепи, а вслед за ними и призабойного конвейера, к которому секции пристыкованы, после прохода комбайна. Это приводит к изгибу конвейера, разрыву цепей и его заклиниванию, что негативно сказывается на производительности работы всего забоя в целом, приводит к остановке работы лавы на несколько дней и значительным материальным потерях.
Следовательно, целью исследований является повышения безопасности и эффективности работы механизированного комплекса шахты путем совершенствования его системы автоматизации.
Поскольку совершенствование системы автоматизации пойдет по принципу разработки нового блока контроля передвижки секций крепи, то последний предназначен для работы в составе базовой аппаратуры управления и должен значительно расширять ее функциональные и защитные возможности, а также иметь достаточно высокие эксплуатационные показатели (надежность, простота обслуживания, и т . д.).
Сформулируем основные требования к разрабатываемому устройству:
- Обеспечивать управления перемещением секций крепи;
- Оперативно контролировать местоположение каждой секции крепи; -
- Обеспечивать легкость и удобство эксплуатации;
- Обеспечивать возможность эксплуатации в экстремальных условиях (чрезвычайная загазованность, 90% влажности, запыленность и т.п.);
- Обеспечивать возможность работы в составе базовой аппаратуры автоматизации очистных комбайнов;
- Иметь минимальные массогабаритные показатели и себестоимость;
- Удовлетворять требованиям взрывозащиты и искробезопасности.
2. Критический обзор существующих решений и выбор базовой аппаратуры автоматизации
Для очистного комбайна унифицированного ряда РКУ–13 с гидравлическим механизмом подачи применяется комплекс автоматизации типа КУАК.02. Комплекс обеспечивает следующие основные функции:
а) по управлению:
- пуск и отключение комбайна и конвейера;
- задача направления и скорости движения комбайна;
- изменение положения исполнительных органов комбайна;
- отключение механизмов забоя;
- запрет пуска комбайна и конвейера при ремонтных работах;
- Иконтроль за работой элеетрогидрораспределеителей;
- выбор режима управления;
б) по защите:
- от опрокидывание электродвигателя при затянутом пуске;
- от снижения давления воды в системе орошения и охлаждения;
- от перегрева обмоток электродвигателя;
б)по диагностике:
- запоминания причин отключения комбайна и расшифровка на табло;
- фиксирование поломок отдельных узлов и выдача рекомендации по их устранению;
- контроль технического состояния отдельных узлов и блоков с помощью светодиодных индикаторов.
Структурная схема комплекса КУАК.02 приведена на рисунке 2.
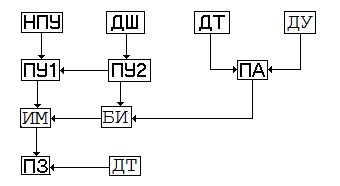
Рисунок 2 – Структурная схема КУАК.02.
Состав аппаратуры КУАК.02: два пульта управления ПУ1 и ПУ2, носимый пульт управления НПУ, коробка распределительная КР, блок индикации БИ, панель защиты ПЗ, панель аппаратов ПА, датчики скорости ДС, уровня ДУ, датчик тока ДТ и термодатчик ДТм, ИМ – исполнительные механизмы.
Принцип действия аппаратуры. Скорость перемещения комбайна, направление его передвижения, включение и отключение комбайна и конвейера задается с основного пульта ПУ1 (см. Рис. 2.1). После включения комбайна скорость подачи уменьшается до нуля, а затем плавно растет с установленной уставки (Vпуст=1,9м/мин). При движении комбайна аппаратура осуществляет контроль силы тока приводного электродвигателя с помощью датчика тока ДС. При увеличении нагрузки на электродвигатель выше заданной уставки аппаратура уменьшает скорость подачи комбайна. При резком увеличении нагрузки срабатывает аппарат КОРД, который располагается на панели защиты ПО, и комбайн останавливается. Управление режущими органами комбайна осуществляется с пульта ПУ1.
Особенностью комплекса КУАК.02 является то, что регулятор нагрузки построен на базе микропроцессорных элементов, а также возможность управления комбайном с помощью инфракрасного излучения. Аппаратура располагается на очистном комбайне. В результате автоматизации очистного комбайна повышается эффективность добычи угля за счет контрактура времени простоя при отказах забойного оборудования. Принцип действия заключается в следующем. Скорость перемещения комбайна, его направление, включение и отключение комбайна и конвейера осуществляется с основного пульта ПУ1. После включения комбайна скорость подачи уменьшается до нуля, а затем плавно растет с установленной уставки (м / мин). При движении комбайна аппаратура осуществляет контроль силы тока приводного электродвигателя с помощью датчика тока ДТ. При увеличении нагрузки на электродвигатель выше заданной уставки аппаратура уменьшает скорость подачи комбайна. При резком увеличении нагрузки срабатывает аппарат КОРД, который располагается на панели защиты ПЗ, и комбайн останавливается. Управление режущими органами комбайна осуществляется с пульта ПУ1.
Индикация о режимах работы комбайна освещается в блоке индикации БИ. Аппаратура также контролирует уровень, давление и температуру масла в гидросистеме подачи комбайна. В результате автоматизации очистного комбайна повышается эффективность добычи угля за счет контрактура времени простоя при отказах забойного оборудования. Также для автоматизации механизмов очистного комплекса в составе комбайна РКУ применяется устройство управления механизмами очистного комплекса УМК. Оно предназначено для управления механизмами очистного комплекса по вспомогательным жилам силового кабеля или комбайна с помощью дополнительного кабеля, проложенного по лаве, от очистного комбайна на штрек. Работает вместе с электрооборудованием участка – магнитными пускателями, станциями управления, а также вместе с аппаратурой сигнализации и связи. Аппаратура выполняет 25 функций по управлению, защиты, блокировки.
Основные:
- дистанционное управление с ПУ комбайна пускателем комбайна;
- автоматическое включение пускателя комбайна насоса орошения;
- дистанционное управление с ПУ предохранительной лебедкой;
- раздельное включение пускателей конвейера: только верхнего привода(только нижнего привода);
- реверс пускателей конвейера с аппаратуры управления;
- контроль технического состояния отдельных узлов и блоков с помощью светодиодных индикаторов;
- реверс пускателей конвейера с аппаратуры управления;
- дистанционное управление пускателем с аппаратуры управления;
- аварийное дистанционное отключение пускателя с аппаратуры управления;
- автоматическое включение предупредительного сигнала по скамье перед включением пускателя лебедки, конвейера и органа комбайна режущего (при наличии соответствующего оборудования);
- блокировки, обеспечивает не включения механизмов лавы без предупредительного сигнала;
- блокировки, возвращает схемы управления в выходной отключенном состоянии при любом откл/вкл комбайна, конвейера, предохранительной лебедки, при отсутствии предупредительного сигнала;
- нулевую защиту;
- защита от потери управляемости;
- контроль допускаемой не больше 10 Ом сопротивления цепи заземления;
- контроль цепей управления;
- светоиндикация о включении пускателей, аварийном отключении АВ и неисправности цепей управления.
На аппаратуре управления имеется лицевая панель, кнопки Пуск
, Стоп
и индикация, разделяется на пять групп: питание, комбайн, конвейер, лебедка, насосные станции.
Для обсечения громкоговорящей связи по лаве предлагается применить комплекс устройств управления забойными машинами КУЗ.03.
Аппаратура КУЗ предназначена для пуска и остановки комбайнов, конвейеров, маслостанций с абонентским постом связи, подачи и контроля прохождения предупредительного сигнала перед включением и началом перемещения, акустического контроля работы комбайна и двухсторонней полудуплексной громкоговорящей связи между абонентами очистного забоя и штрека.
Область применения: очистные забои, опасные по газу и пыли, совместно с аппаратурой УМК, КД–А, ЦПУ, САУК. Изготавливается в 3–х модификациях: КУЗ.01, КУЗ.02, КУЗ.03.
КУЗ.03 обеспечивает двухстороннюю полудуплексную связь абонентов очистного забоя. Может применяться для организации связи на конвейерных линиях или в других протяжённых горных выработках.
КУЗ заменяет аппаратуру связи АС–3СМ.
В КУЗ отсутствует усилитель мощности СГС, что повышает надёжность применения более современной динамической головки с более широкой полосой пропускания сигналов. Рабочие имеют одинаковую возможность пользоваться связью независимо от местонахождения абонентского поста громкоговорящей связи. Состав: блок питания (БП) и 30 абонентских постов (ПА).
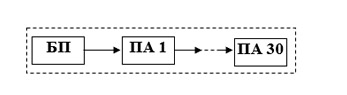
Рисунок 3 – Структура комплекса КУЗ.03.
ПА – пост абонентский аппаратуры КУЗ.03 содержит только блок связи с переключателем режима работы. КУЗ.03 используется для громкоговорящей связи протяжённостью до 2 км. Не имеет аккумулятора. Поскольку одной из функций разрабатываемого устройства является поддержание равномерности передвижения секций крепи, а вслед за ними и конвейера, то необходимо определить тип соответствующих датчиков передвижки как источника технологической информации. Наибольшее распространение в отечественной и зарубежной практике получили датчики положения ГП, основанные на принципе подсчета количества оборотов барабана, установленного в точке контроля, с катушкой из гибкого материала. Свободный конец этого материала закрепляется в почве выработанного пространства и при подвиганием конвейера (в нашем случае секции крепи) барабан делает вынуждены вращения, количество которых пропорционально пути, пройденном данной точкой конвейера. Как гибкий материал используется перфорированная лента (Франция), нейлоновый шнур (Англия) или стальная нить (Польша, Германия, Украина).
Как элемент, преобразующий количество оборотов барабана в движение, используется цифровой счетчик, двоичный код на выходе которого пропорционален этому перемещению, что очень удобно ведь не требует дополнительного преобразования сигнала с датчика. К данному счетчика предъявляются требования по сохранению информации при возможных перерывах питания. В этих целях каждый датчик обеспечивается дополнительным электроблоком, с расположенным внутри него аккумуляторную батарею, о недостатках применения которой говорилось ранее. Кроме того, для контроля подвигания конвейера используются счетчики, емкость которых должна обеспечивать сохранение величины подвигания конвейера в течение всего срока эксплуатации системы. Таким образом, целесообразно в качестве базовой аппаратуры автоматизации принять КУАК.02, а в качестве датчика технологического параметра – положения секций в забое – катушечный ГП со стальным проводом.
3. Обоснование направления автоматизации технологической установки
Как показывает опыт эксплуатации очистных комплексов в шахтах, на данный момент еще не решена одна проблема – проблема искривления линии подвигания механизированного комплекса, что происходит из–за отсутствия оперативного контроля за подвигания секций крепи и приводит к значительным перекосам става конвейера и порывам цепей. Решения этой задачи очень актуально, и на данный момент почти не имеет аналогов в промышленности. В работе достаточно широко исследуется математическая модель линии очистного забоя и системы автоматического обеспечения ее прямолинейности, следовательно в качестве базовых целесообразно принять именно эти исследования. Согласно в качестве критерия эффективности функционирования системы управления предложено использовать абсолютное отклонение фактической от заданной линии забоя, что необходимо минимизировать на интервале, заданном ближними и дальними пределами забоя. Математическое выражение критерия записывается в виде:
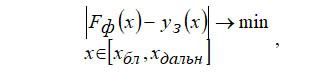
Формула – 1
На критерий (1) налагаются ограничения, вызванные требованиями эксплуатации:
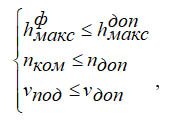
Формула – 2
Математическое описание линии очистного забоя осуществлено путем его подачи в виде интерполяционного сплайна, заданного на сетке ее отдельных значений, полученных по результатам маркшейдерских замеров или по показаниям датчиков величины подвижки конвейера. При таком описании, линия очистного забоя может быть представлена как непрерывная функция:

Формула – 3
Желаемое положение линии очистного забоя описывается задающей линейкой – прямой, лежащей под заданным углом по отношению к оси:

Формула – 4
Рассогласование заданного и фактического состояний линий забоя:
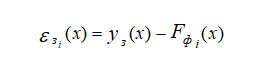
Формула – 5
Значение функции вычисляются из условия достижения цели (1) с учетом возможностей системы подачи конвейера на забой:
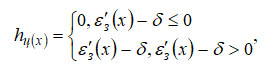
Формула – 6
Моделирование стрелы прогиба осуществляется методом итераций. В результате моделирования был установлен факт, что при изменении заданных параметров прямолинейности, возможно накопление стрелы прогиба и ее превышение допустимых пределов, что противоречит ограничению (2). Таким образом, разработанная система контроля за прямолинейностью забоя позволяет обеспечить необходимую кривизну линии очистного забоя, устранить простои забоя из–за превышения допустимой степени кривизны, а, значит, ее рационально внедрить в промышленное использование. К разрабатываемому устройства автоматического контроля кривизны линии очистного забоя следует поставить следующие требования:
1. оперативный контроль передвижки секций крепи и призабойного конвейера с соответствующим шагом на протяжении всей длины лавы;
2. контроль степени отклонения линии забоя от установленной нормы;
3. возможность ручного изменение уставок срабатывания;
4. удобный интерфейс оператора;
5. современная элементная база;
6. как можно меньшие габариты;
7. уровень и вид взрывозащиты исполнительного устройства РВ ІВ Иа, ДСВ–РО Иа;
8. степень защиты от влаги и пыли исполнительного устройства IP–54, ДСВ–IP–32.
4. Алгоритмизация блока контроля линейности забоя
В данном разделе необходимо разработать алгоритм автоматизации и предоставить его блок–схему. Алгоритм функционирования работы устройства контроля линейности забоя представлен на рис. 4. Работа устройства следующая: Сначала происходит подача напряжения питания на схему – блок 2, после чего осуществляется ввод начальных уставок работы блока – N –количество датчиков передвижки в зависимости от длине лавы (поскольку согласно целесообразно устанавливать датчики через каждые 20 м, то максимальное количество датчиков принимаем 12 шт), – количество импульсов от датчика за одну нормальную передвижку, ?d – максимально допустимая погрешность передвижки (блок 3).
В блоке 4 реализован цикл опроса каждого датчика передвижки.
В этом цикле происходит следующее:
блок 5 – выдается разрешение на начало передвижки конвейера с крепью – значит включается и–и гидродомкрат передвижки;
блок 6 – на блок управления поступает сигнал с i–го датчика передвижки;
блок 7 считается количество импульсов с датчика до тех пор, пока их количество не станет больше или равна причиненного;
блок 8 в это время выдается разрешение на передвижки крепи;
блок 9 при достаточном перемещении конвейера выдается сигнал на запрет перемещения;
блок 10 отключения i–го гидродомкрата передвижки.
Далее в блоке 11 происходит проверка или в допустимых пределах лежит искривление линии забоя при перемещении i–го участка конвейера, и в случае недопустимо большого искривления выдается аварийный сигнал блок 13).
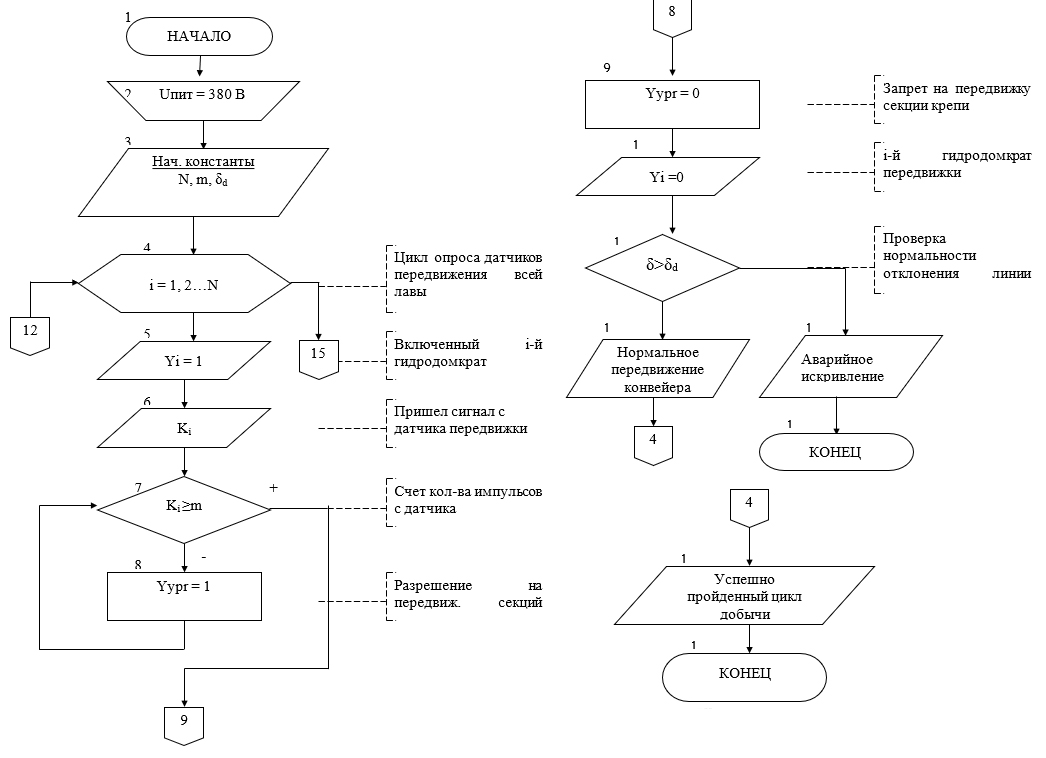
Рисунок 5 – Блок–схема работы блока контроля линейности забоя
В случае нормального передвижки происходит индикация нормального передвижки конвейера (блок 12). В блоке 15 происходит завершение цикла, блок 16 – конец работы блока.
5. Разработка структурной схемы блока контроля линейности забоя
Рассмотрим построение структурной схемы блока автоматического контроля линейности забоя, которая приведена на рис.5.
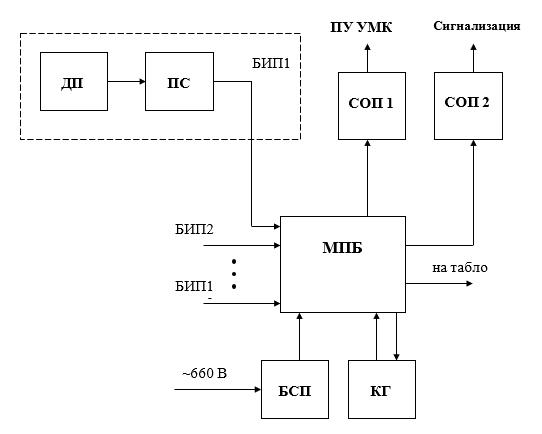
Рисунок 6 – Структурная схема блока контроля линейности забоя
Блок контроля линейности состоит из 12 блоков измерений передвижки БИП, блока питания стабилизированным напряжением БСП, кварцевого генератора КГ, 2–х блоков симисторных оптопар СОП и микропроцессорного блока МПБ. Один блок измерения перемещения выдает информацию о передвижки крепи и конвейера, в его состав входит ДП–датчик перемещения и ПС – блок преобразования сигнала (усиление сигнала). Микропроцессорный блок управления может принимать информацию максимально от двенадцати блоков обработки данных, то есть о расстоянии передвижки крепи и конвейера в двенадцати точках.
Микропроцессорный блок управления обрабатывает полученные данные от датчиков перемещения. Полученные данные анализируются и результат обработки выводится на блок индикации, реализовано в качестве табло. При аварийных режимах, когда величина передвижки в контролируемой точке значительно отклоняется от установленных норм в соответствии с алгоритмом, то микропроцессор выдает сигнал на пульт управления УМК о необходимости остановки работы очистного комплекса, поскольку дальнейшее передвижки может привести к порыву цепи конвейера. Также в случае значительного отклонения передвижки нормы выдается соответствующая сигнализация Согласно разработанной структурной схемы блока контроля передвижки разработана функциональная схема разрабатываемого устройства, приведенной на рис.5.
Согласно рис.5 функционально устройство контроля линии забоя состоит из двенадцати блоков измерения передвижки, микропроцессорного блока, который осуществляет обработку информации по технологическим датчиков и выдает руководящие сигналы на УМК и сигнализацию через симисторные оптопары VU1, VU2 в соответствии с заложенной в него программы и реализован на микросхеме DD2, блока преобразования протокола обмена для подачи информации на цифровое табло и реализован на микросхеме DD1. БИП1 состоит из импульсного датчика передвижения DP1 и усилителя А1, который служит для усиления сигнала через большое расстояние передачи информационного сигнала, и ограничителя амплитуды ZL1 и стабилитрона STU1, которые приводят информационный сигнал к виду, необходимому для использования в МПБ и осуществляют защиту входных цепей микроконтроллера от резких перепадов напряжения с датчиков.
Выводы
Главным объектом исследования данной работы является очистной механизированный комплекс шахты. Были рассмотрены особенности технологических режимов его работы, последовательность действий при перемещении комплекса вслед за продвижением лавы, определены точки, в которых необходимо контролировать передвижки конвейера, и определены метрологические требования к средству измерения передвижки.
Была рассмотрена аппаратура автоматизированного управления работой очистного комплекса на базе комбайна РКУ типа УМК, которая выбрана в качестве базовой аппаратуры, и которая, однако, не обладает функцией контроля и защиты от изгибов призабойного конвейера. В проекте разработан автоматический блок контроля линейности забоя, разработаны структурная, функциональная, принципиальная электрическая схемы. Разработанное устройство можно применять в системе автоматического управления работой очистного комплекса, как источник измерительной информации о состоянии искривление линии забоя и для предупредительных действий в этом направлении. Решение этого вопроса очень актуально для шахты и приводит к значительной финансовой экономии.
При написании данного реферата магистерская работа еще не завершена. Окончательное завершение: июнь 2021 года. Полный текст работы и материалы по теме могут быть получены у автора или его руководителя после указанной даты.
Список источников
- Топорков А. А. Машинист горных выемочных машин: Учёб. для учащихся профтехобразования и рабочих на производстве.– М.: Недра, 1991. – 334 с.: ил.
- Комплекс автоматизированного управления АУК–3.
- Правила технической эксплуатации электроустановок потребителей и Правила техники безопасности при эксплуатации электроустановок потребителей / Глав. Упр. Гос. Энергетического надзора Минэнерго СССР.–4–е изд.–М.: Энергоатомиздат, 1989.–432с.
- Правила устройства электроустановок / Минэнерго СССР. – 6–е изд. перер. и доп. – М: Энергоатомиздат, 1985. – 640 с.
- Правила безопасности в угольных шахтах.–К.: Основа, 1996.–421 с. исслед.
- МИНПИ – ЮНЕСКО, ОАО «Автоматгормаш им. В. А. Антипова». –Донецк: Вебер, Донец. отд–ние, 2009.
- Автоматизация производства на угольных шахтах / Г.И. Бедняк, В.А., Ульшин, В.П. Довженко и др. – К.: Техника, 1989. – 272 с.
- Батицкий В.А., Куроедов В.И., Рыжков А.А., Автоматизация производственных процессов и АСУ ТП в горной промышленности: Учеб. Для техникумов. – 2–е изд., перераб. и доп. –М.: Недра, 1991.
- Электрослесарю добычного и проходческого оборудования: Справочник /Под.ред. В.А. Антипова. – Донецк: Донбасс, 1989. – 159 с.
- Груба В.И., Староверов К.С. Математическая модель фактического состояния линии забоя струговой лавы// Труды Донецкого государственного технического университета. Выпуск 7, серия горно–электромеханическая. – Донецк: ДонГТУ, 1999.– С. 69–74.