Abstract on the topic of graduation work
Content
- Introduction
- 1. Technological process as an object of automation. The purpose of the design and requirements to the automation device
- 2. Critical review of existing solutions and selection of basic automation equipment
- 3.Justification of the direction of automation of the technological installation
- 4 Algorithmization of the face linearity control unit
- 5. Development of the block diagram of the block for monitoring the linearity of the face
- Conclusions
- List of sources
Introduction
The issues of timely mechanization of technological installations, modernization or replacement of outdated equipment, and the introduction of integrated automation at the enterprise are extremely relevant at the moment. This approach will increase the efficiency and intensification of technological processes, and therefore improve the productivity of the mine as a whole. Currently, a large number of accidents at the treatment sites of mines occur due to significant curvature of the bottom line, which in turn leads to significant distortions of the bottom–hole conveyor, a break in its chains and, to many days of lava downtime, and, consequently, significant material losses.
This problem can be solved by quickly monitoring the distance of movement of each section of the support and, accordingly, setting the conveyor with a certain number of steps and issuing appropriate control signals to the beginning and end of the movement of the mechanized support. The developed unit should work as part of the basic automation equipment of the mechanized complex and complement it functionally. Thus, the issue of developing a device for automatic control of the linearity of the face is very relevant at the present time.
1. Technological process as an object of automation. The purpose of the design and requirements to the automation device
The operation of downhole machines, complexes and aggregates is associated with significant difficulties due to their continuous movement, various mining and geological conditions, the dust and gas regime of the mine, its microclimate and other factors. Solving the problem of automation of downhole machines will allow:
- increase the productivity of machines by making fuller use of the power of their electric motors;
- release the driver from the functions of controlling the machine and then remove it from the face;
- improve the quality of the extracted coal and reduce its cost;
- improve the dynamic quality of machines, their reliability and extend their service life;
- include downhole machines in the automated control system subsystem
Cleaning faces
.
Mining machine automation systems must meet a number of requirements related to the specifics of the mine working conditions, and the general requirements for control systems. They must meet the safety rules, be reliable in operation, provide automatic control of the feed speed of the combine and the position of the executive bodies in the profile of the layer in order to exclude the processing of the lateral enclosing rocks by the cutters. Automation systems mining machine needs to provide automatic shutdown of the processor: while stopping the AFC, the care of combine pridvinutyh from sections of support in distance than specified, the presence of obstacles on the machine the road, exceeding the permissible concentration of methane for outgoing the jet and in the place of work of the processor, to stop the flow of water in irrigation device processor reaches the initial position at the end of the lava.
System of automation of the extraction of the combine must also provide: immediate stop of the harvester when installing the feed rate to a value of zero; unloading traction on when you stop the processor, followed locking the drive sprocket feed; reduced feed rate to zero at the start of the combine and prolonged overloads of electric motors, and commit a zero feed rate; two way voice communication and signaling in the lava.
The automation system cycle downhole machine contains a system of automatic control (SAC) load electric motors; automatic control system, move the machine to the profile of the reservoir; means for automatic control of the location of the mining machines and obstacles in her way. Work mining machines are in the automatic mode, moreover, should be consistent with the work of the hydraulic roof supports, scraper conveyor and means of automatic shifting.
Figure 1 shows the technological scheme of cleaning operations together with the means of mechanization.
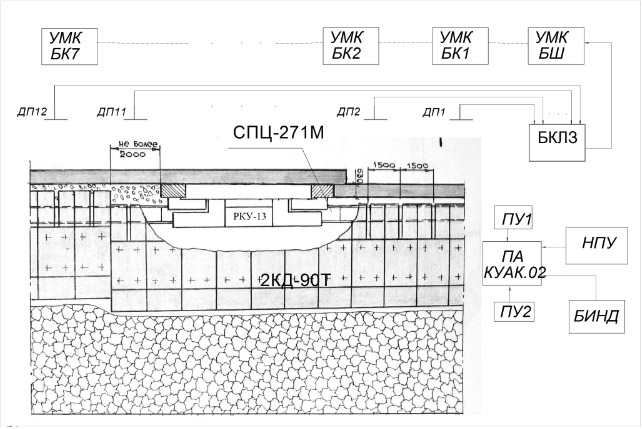
Figure 1 – Technological scheme of the treatment face
2. Critical review of existing solutions and selection of basic automation equipment
For the cleaning combine of the unified RKU–13 series with a hydraulic feed mechanism, an automation complex of the KUAK type is used.02. The complex provides the following main functions:
а) on management:
- start – up and shutdown of the combine and conveyor;
- the task of the direction and speed of the combine movement;
- changing the position of the executive bodies of the combine;
- disabling of the slaughterhouse mechanisms;
- prohibition of starting the combine and conveyor during repair work;
- And control over the operation of electric hydraulic distributors;
- selecting the control mode;
b) on protection:
- from overturning the electric motor during a delayed start-up;
- from reducing the water pressure in the irrigation and cooling system;
- overheating of the motor windings;
c) on diagnostics:
- memorizing the reasons for turning off the combine and decoding it on the scoreboard;
- fixing breakdowns of individual components and issuing recommendations for their elimination;
- monitoring of the technical condition of individual components and blocks with the help of LED indicators.
The block diagram of the complex AS. 02 is shown in Figure 2.
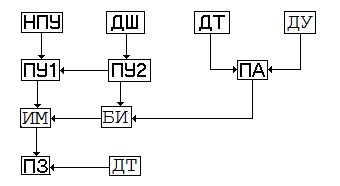
Figure 2 – Block diagram AS.02
Block diagram of the CUAC. 02specificity of the CUAC complex.The advantage is that the load regulator is built on the basis of microprocessor elements, as well as the ability to control the combine using infrared radiation. The equipment is located on the cleaning combine. As a result of the automation of the treatment combine, the efficiency of coal mining increases due to the contracture of downtime in case of failures of the downhole equipment. The principle of operation is as follows. The speed of movement of the combine, its direction, switching on and off of the combine and the conveyor is carried out from the main control panel PU1. After turning on the combine, the feed rate decreases to zero, and then gradually increases from the set point (m / min). When the combine is moving, the equipment monitors the current strength of the drive motor using the DT current sensor. When the load on the electric motor increases above the setpoint, the equipment reduces the feed speed of the combine. With a sharp increase in the load, the CORD device, which is located on the PZ protection panel, is triggered,and the harvester stops. The cutting elements of the combine are controlled from the remote control PU1.
The indication of the operating modes of the combine is illuminated in the BI display unit. The equipment also monitors the level, pressure and temperature of the oil in the hydraulic feed system of the combine. As a result of the automation of the treatment combine, the efficiency of coal mining increases due to the contracture of downtime in case of failures of the downhole equipment. Also, to automate the mechanisms of the treatment complex in the RKU combine, a device for controlling the mechanisms of the treatment complex of the UMK is used. It is designed to control the mechanisms of the longwall equipment at the auxiliary pumping power cable or combine with additional cable laid across the face, from Shearer on the roadway. It works together with the electrical equipment of the site – magnetic starters, control stations, as well as with alarm and communication equipment. The equipment performs 25 functions for control, protection, and blocking.
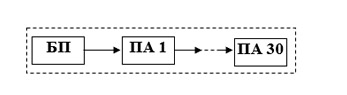
Figure 3 – Structure of the KUZ.03 complex
The structure of the complex KUZ. 03PA-post subscriber equipment KUZ. 03 contains only a communication unit with a switch of the operating mode. KUZ. 03 is used for loudspeaker communication with a length of up to 2 km. It does not have a battery. Since one of the functions of the device under development is to maintain the uniformity of movement of the support sections, and after them, the conveyor, it is necessary to determine the type of the corresponding movement sensors as a source of technological information. The most widespread in domestic and foreign practice are the GP position sensors, based on the principle of counting the number of revolutions of the drum installed at the control point, with a coil of flexible material. The free end of this material is fixed in the soil of the developed space and when the conveyor is moved (in our case, the support section), the drum makes two rotations, the number of which is proportional to the path traveled by this point of the conveyor. As a flexible material, perforated tape (France), nylon cord (England) or steel thread (Poland, Germany, Ukraine) are used.
As an element that converts the number of revolutions of the drum into movement, a digital counter is used, the binary code at the output of which is proportional to this movement, which is very convenient because it does not require additional conversion of the signal from the sensor. This counter is subject to requirements for storing information in case of possible power interruptions. For this purpose, each sensor is provided with an additional electrical unit, with a battery located inside it, the disadvantages of which were discussed earlier. In addition, to control the movement of the conveyor, meters are used, the capacity of which should ensure that the value of the movement of the conveyor is maintained throughout the entire life of the system. Thus, it is advisable to adopt the CUAC as the basic automation equipment.02, and as a sensor of the technological parameter – the position of the sections in the bottom – a coil GP with a steel wire.
3. Justification of the direction of automation of the technological installation
As the experience of operating treatment facilities in mines shows, at the moment, one problem has not yet been solved: the problem of bending the line of movement of the mechanized complex, which occurs due to the lack of operational control over the movement of the support sections and leads to significant distortions of the conveyor stave and chain breaks. Solutions to this problem are very relevant, and at the moment almost has no analogues in the industry. In this paper, the mathematical model of the treatment face line and the automatic system for ensuring its straightness are widely studied, therefore, it is advisable to take these studies as the basic ones. According to the article, as a criterion for the effectiveness of the control system, it is proposed to use the absolute deviation of the actual line from the specified face line, which must be minimized at the interval specified by the near and far limits of the face. The mathematical expression of the criterion is written as:
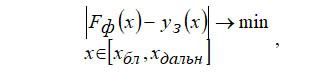
Formula – 1
Criterion (1) is subject to limitations due to operational requirements:
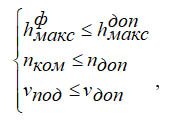
Formula – 2
Criterion (1) is subject to limitations due to operational requirements:The mathematical description of the treatment face line is carried out by feeding it in the form of an interpolation spline, set on a grid of its individual values obtained from the results of surveying measurements or from the readings of the conveyor movement sensors. With this description, the treatment face line can be represented as a continuous function:

Formula – 3
The desired position of the treatment face line is described by the setting ruler-a straight line lying at a given angle with respect to the axis:

Formula – 4
Mismatch of the specified and actual conditions of the face lines:
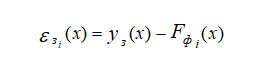
Formula – 5
The value of the function is calculated from the condition for achieving the goal (1), taking into account the capabilities of the conveyor feed system to the bottom:
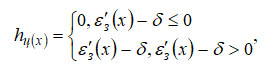
Formula – 6
The deflection boom is modeled using the iterative method. The simulation was the fact that when you change the preset parameters of straightness, it is possible accumulation of the boom deflection and its limits, in contravention of the restriction (2). Thus, the developed control system for the straightness of the bottom helps secure the necessary curvature lines stope, eliminate downtime slaughter due to exceeding the permissible degree of curvature, and, therefore, it is rational to introduce in industrial use. The following requirements should be applied to the developed device for automatic control of the curvature of the treatment face line:
1. operational control of the movement of the support sections and the bottom–hole conveyor with the appropriate step throughout the entire length of the lava;
2. control of the degree of deviation of the bottom line from the established norm;
3. ability to manually change the trigger settings;
4. user-friendly operator interface;
5. modern element base;
6. as small as possible dimensions;
7. level and type of explosion protection of the executive device RV–ZV Ia,;
8. the degree of protection against moisture and dust of the actuator is IP54, DSB–IP32.
4. Algorithmization of the face linearity control unit
In this section, you need to develop an automation algorithm and provide its flowchart. The algorithm of operation of the device for monitoring the linearity of the face is shown in Fig. 4. Operation of the device are as follows: First, there is the supply voltage for the circuit block 2, followed by enter initial setting work unit – N is the number of sensors, shifting depending on the length of the lava (because under it is advisable to install the sensors every 20 m, the maximum number of sensors adopted 12 PCs), number of pulses from the sensor in a normal pendulum, – maximum permissible error of relocation (block 3).
In block 4, a polling cycle is implemented for each movement sensor.
In this loop, the following happens:
block 5 – a permit is issued to start moving the conveyor with a support – this means that the hydraulic jack of the movement is turned on and – and;
block 6 –the control unit receives a signal from the i –th movement sensor;
block 7 counts the number of pulses from the sensor until their number is greater than or equal to the one caused;
block 8 at this time, a permit is issued for the movement of the support;
block 9 if the conveyor is sufficiently moved, a signal is issued to prohibit movement;
block 10 of disconnecting the i–th hydraulic jack of the movement.
Further, in block 11, a check is made or the curvature of the bottom line lies within the permissible limits when moving the i–o section of the conveyor, and in the case of an unacceptably large curvature, an alarm signal is issued block 13
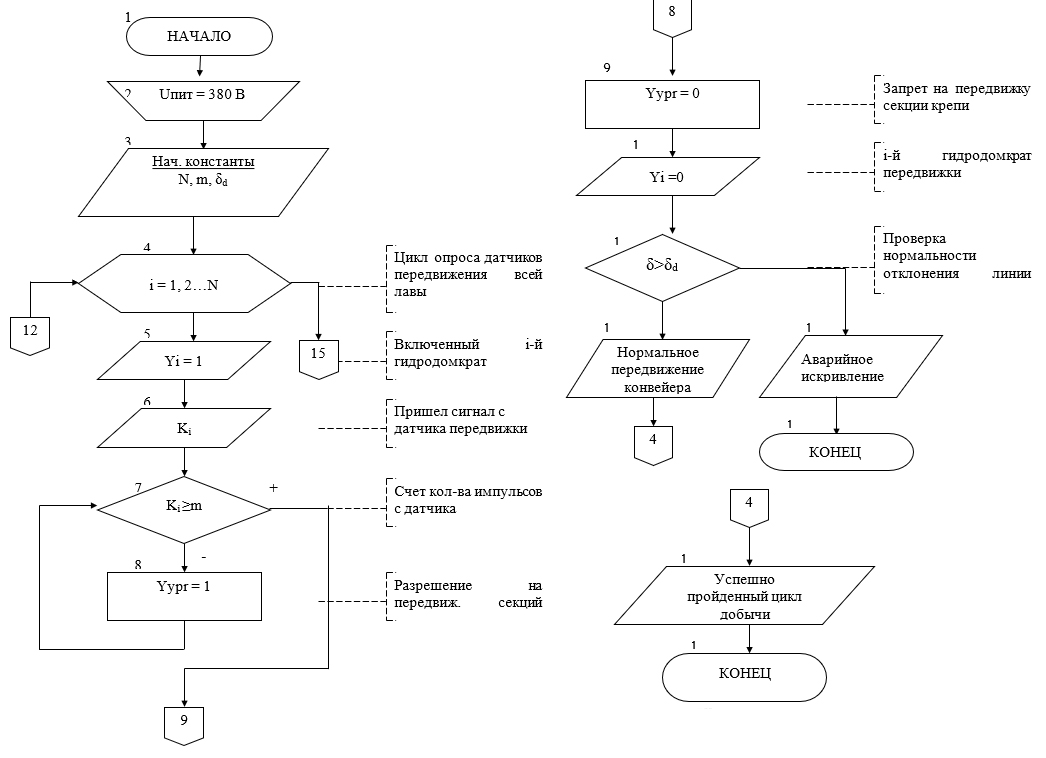
Figure 5 – Block diagram of the operation of the face linearity control unit
In the case of normal movement, the normal movement of the conveyor is indicated (block 12). In block 15, the end of the cycle occurs, block 16 – the end of the block operation.
5. Development of a block diagram of the block for monitoring the linearity of the face
Let's consider the construction of a block diagram of the automatic control of the linearity of the bottom, which is shown in Fig. 5.
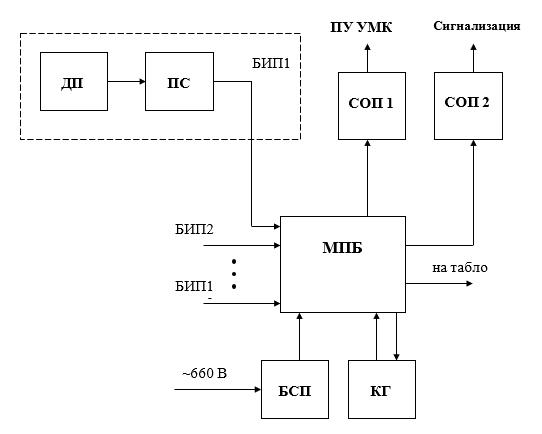
Figure 6 – Block diagram of the face linearity control unit
The linearity control unit consists of 12 units for measuring the movement of the BIP, a power supply unit with a stabilized voltage BSP, a quartz generator KG, 2 blocks of triac optocouplers SOP and a microprocessor unit BCH. One displacement measurement unit provides information about the movement of the support and the conveyor, it includes a DP-displacement sensor and a PS-signal conversion unit (signal amplification). The microprocessor control unit can receive information from a maximum of twelve data processing units, that is, about the distance of movement of the support and the conveyor at twelve points.
The microprocessor control unit processes the received data from the motion sensors. The received data is analyzed and the processing result is displayed on the display unit, implemented as a scoreboard. In emergency modes, when the amount of movement at the controlled point significantly deviates from the established norms in accordance with the algorithm, the microprocessor sends a signal to the control panel of the control center about the need to stop the operation of the treatment complex, since further movement can lead to a break in the conveyor chain. Also, in the event of a significant deviation of the movement of the norm, an appropriate alarm is issued. According to the developed block diagram of the movement control unit, a functional diagram of the device under development is developed, shown in Fig. 5.
According to Fig.5, the functional device for monitoring the bottom line consists of twelve units for measuring movement, a microprocessor unit that processes information on technological sensors and issues guidance signals to the UMK and signaling via triac optocouplers VU1, VU2 in accordance with the program embedded in it and is implemented on the DD2 chip, a block for converting the exchange protocol for feeding information to a digital scoreboard and is implemented on the DD1 chip. BIP1 consists of a pulse motion sensor DP1 and an amplifier A1, which serves to amplify the signal over a long distance of transmitting the information signal, and an amplitude limiter ZL1 and a zener diode STU1, which bring the information signal to the form necessary for use in BCH and protect the input circuits of the microcontroller from sudden voltage drops from the sensors.
Conclusions
The main object of the study of this work is the mechanized treatment complex of the mine. Was considered the features of the technological modes of operation, the sequence of actions when you move the complex following the advancing lava determined the point at which you want to monitor movement of the conveyor, and identified metrological requirements for measuring means of advancing.
The equipment for automated control of the work of the treatment complex on the basis of the RKU combine harvester of the UMK type was considered, which was chosen as the basic equipment, and which, however, does not have the function of monitoring and protecting against bends of the bottom-hole conveyor. The project has developed an automatic block for monitoring the linearity of the face, developed structural, functional, and basic electrical circuits. The developed device can be used in the system of automatic control of the work of the treatment complex, as a source of measuring information about the state of the curvature of the bottom line and for preventive actions in this direction. Solving this issue is very important for the mine and leads to significant financial savings.
When writing this abstract, the master's work has not yet been completed. Final completion: June 2021. Full text of the work and materials on the topic can be obtained from the author or his supervisor after the specified date.
References
- Топорков А. А. Машинист горных выемочных машин: Учёб. для учащихся профтехобразования и рабочих на производстве.– М.: Недра, 1991. – 334 с.: ил.
- Комплекс автоматизированного управления АУК–3.
- Правила технической эксплуатации электроустановок потребителей и Правила техники безопасности при эксплуатации электроустановок потребителей / Глав. Упр. Гос. Энергетического надзора Минэнерго СССР.–4–е изд.–М.: Энергоатомиздат, 1989.–432с.
- Правила устройства электроустановок / Минэнерго СССР. – 6–е изд. перер. и доп. – М: Энергоатомиздат, 1985. – 640 с.
- Правила безопасности в угольных шахтах.–К.: Основа, 1996.–421 с. исслед.
- МИНПИ – ЮНЕСКО, ОАО «Автоматгормаш им. В. А. Антипова». –Донецк: Вебер, Донец. отд–ние, 2009.
- Автоматизация производства на угольных шахтах / Г.И. Бедняк, В.А., Ульшин, В.П. Довженко и др. – К.: Техника, 1989. – 272 с.
- Батицкий В.А., Куроедов В.И., Рыжков А.А., Автоматизация производственных процессов и АСУ ТП в горной промышленности: Учеб. Для техникумов. – 2–е изд., перераб. и доп. –М.: Недра, 1991.
- Электрослесарю добычного и проходческого оборудования: Справочник /Под.ред. В.А. Антипова. – Донецк: Донбасс, 1989. – 159 с.
- Груба В.И., Староверов К.С. Математическая модель фактического состояния линии забоя струговой лавы// Труды Донецкого государственного технического университета. Выпуск 7, серия горно–электромеханическая. – Донецк: ДонГТУ, 1999.– С. 69–74.